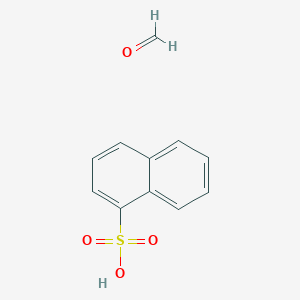
Napthalene sulfonic acid formaldehyde
概述
描述
Naphthalene sulfonic acid formaldehyde condensate (NSAF) is an anionic surfactant synthesized via sulfonation of naphthalene with concentrated sulfuric acid, followed by condensation with formaldehyde under acidic conditions . The optimal molar ratio of naphthalene to sulfuric acid is 1:2, with condensation temperatures of 110–120°C and reaction times of ~5.5 hours . NSAF’s molecular structure consists of linearly polymerized β-naphthalene sulfonic acid units linked by methylene bridges (–CH₂–), resulting in a high degree of sulfonation (–SO₃H groups) and molecular weights ranging from 1,500–3,000 Da .
科学研究应用
Construction Industry
Naphthalene sulfonic acid formaldehyde is primarily used as a superplasticizer in concrete formulations. Its applications include:
- Water Reduction : It effectively reduces the water-cement ratio without compromising workability, leading to higher strength concrete.
- Durability Enhancement : The compound improves the density and durability of concrete, making it ideal for construction projects requiring long-lasting materials, such as bridges and high-rise buildings.
Application | Benefits |
---|---|
Superplasticizer | Reduces water content while maintaining workability |
Durability | Enhances strength and reduces cracking risk |
Textile Industry
In textile processing, naphthalene sulfonic acid formaldehyde serves as a dye dispersant . Its roles include:
- Improving Dye Uptake : It facilitates even dye distribution on fabrics, ensuring vibrant colors.
- Stabilizing Dye Solutions : The compound prevents dye precipitation during storage and application.
Pharmaceutical Applications
Naphthalene sulfonic acid formaldehyde is also utilized in pharmaceuticals:
- Drug Formulation : It acts as a stabilizer and dispersant for active pharmaceutical ingredients, enhancing bioavailability.
- Oral Hygiene Products : Its derivatives are effective in reducing dental plaque formation due to their ability to impart a negative charge to surfaces, repelling plaque-forming bacteria .
Concrete Performance Enhancement
A study demonstrated that incorporating naphthalene sulfonic acid formaldehyde into concrete mixtures resulted in a 20% increase in compressive strength compared to control samples without the additive. This improvement was attributed to reduced porosity and enhanced particle packing within the concrete matrix.
Textile Dyeing Efficiency
Research indicated that textiles treated with naphthalene sulfonic acid formaldehyde showed a 30% improvement in dye uptake efficiency compared to untreated fabrics. This efficiency leads to reduced dye consumption and lower environmental impact from dye effluents.
Environmental Considerations
While naphthalene sulfonic acid formaldehyde has numerous benefits, its production and application must be managed carefully due to potential environmental impacts associated with unreacted formaldehyde. Advances in synthesis methods aim to minimize these residues, ensuring safer applications across industries .
常见问题
Basic Research Questions
Q. What analytical methods are recommended for quantifying naphthalene sulfonic acid formaldehyde in environmental or biological matrices?
- Methodology : Use modified spectrophotometric techniques, such as the mercury-free pararosaniline method with sequential reagent addition for enhanced sensitivity and reproducibility . For chromatographic separation, employ high-performance liquid chromatography (HPLC) coupled with UV detection, validated against standardized formaldehyde quantification protocols (e.g., NIOSH Method 2016) .
- Key considerations : Calibrate instruments using certified reference materials, account for matrix interferences (e.g., sulfites or phenols), and validate recovery rates in spiked samples.
Q. What synthetic pathways are effective for producing naphthalene sulfonic acid formaldehyde copolymers?
- Methodology : Optimize condensation reactions between naphthalene sulfonic acid derivatives and formaldehyde under controlled pH (3.5–5.0) and temperature (70–90°C) . Monitor polymerization kinetics using gel permeation chromatography (GPC) to determine molecular weight distribution.
- Characterization : Confirm structural integrity via Fourier-transform infrared spectroscopy (FTIR) for sulfonic acid group identification (~1030 cm⁻¹ S=O stretch) and nuclear magnetic resonance (NMR) for backbone connectivity analysis .
Q. How can researchers assess the environmental stability of naphthalene sulfonic acid formaldehyde derivatives?
- Methodology : Conduct accelerated degradation studies under varying pH (2–12), UV exposure, and microbial activity. Quantify breakdown products (e.g., free formaldehyde) using gas chromatography-mass spectrometry (GC-MS) .
Advanced Research Questions
Q. How can contradictions between in vitro and in vivo toxicological data for naphthalene sulfonic acid formaldehyde be resolved?
- Methodology : Integrate multi-model approaches:
Cross-validate in vitro cytotoxicity assays (e.g., mitochondrial dysfunction in hepatocytes) with in vivo rodent studies tracking hepatic biomarkers (e.g., ALT/AST levels) .
Apply physiologically based pharmacokinetic (PBPK) modeling to reconcile dose-response disparities, accounting for metabolic differences (e.g., sulfonation pathways) .
- Case example : If in vitro data overpredicts nephrotoxicity, assess renal clearance rates and protein-binding affinity in vivo to identify detoxification mechanisms.
Q. What mechanistic insights explain the interaction of naphthalene sulfonic acid derivatives with atmospheric SO₂?
- Methodology : Use surface-sensitive techniques (e.g., vibrational sum-frequency spectroscopy) to study interfacial reactions between aqueous formaldehyde and SO₂, identifying sulfonic acid adducts .
- Theoretical modeling : Apply density functional theory (DFT) to map reaction pathways, emphasizing nucleophilic attack by sulfonic acid groups on SO₂-derived intermediates .
Q. How can multi-omics approaches elucidate the cellular impact of naphthalene sulfonic acid formaldehyde exposure?
- Methodology : Combine transcriptomics (RNA-seq) to identify dysregulated pathways (e.g., oxidative stress response) with metabolomics (LC-MS) to quantify perturbed metabolites (e.g., glutathione depletion) .
- Data integration : Use network analysis tools (e.g., Cytoscape) to overlay omics datasets, prioritizing nodes with high centrality in toxicity pathways .
Q. Data Contradiction and Analysis
Q. What strategies address inconsistencies in reported ecotoxicity values for naphthalene sulfonic acid formaldehyde across studies?
- Root causes : Variability in test organisms (e.g., Daphnia magna vs. algae), exposure durations, or analytical detection limits.
- Resolution :
Standardize test protocols using OECD guidelines (e.g., Test No. 201 for algal growth inhibition).
Perform meta-analyses to quantify heterogeneity sources, applying random-effects models to derive consensus EC₅₀ values .
Q. Methodological Innovations
Q. What advanced techniques improve structural elucidation of naphthalene sulfonic acid formaldehyde oligomers?
相似化合物的比较
Sodium Polynaphthalenesulfonate (SPNS)
Synthesis : SPNS is derived from NSAF by neutralizing the sulfonic acid groups with sodium hydroxide, forming a polymeric structure .
Structural Differences :
- Functional Groups : SPNS retains –SO₃⁻Na⁺ groups, enhancing water solubility compared to NSAF (–SO₃H) .
- Molecular Weight : SPNS has higher molecular weights (3,000–10,000 Da) due to extended polymerization .
Performance :
- Thermal Stability : SPNS is more stable than NSAF at temperatures >200°C due to its stable polymeric backbone .
- Cost : Higher production costs due to additional neutralization steps .
Alkylnaphthalene Sulfonates
Synthesis : Alkyl chains (e.g., methyl, butyl) are introduced to naphthalene before sulfonation, followed by formaldehyde condensation .
Structural Differences :
- Hydrophobic Groups : Alkyl chains improve compatibility with organic matrices .
- Molecular Weight : Lower (1,000–2,000 Da) compared to NSAF .
Performance :
- Solubility : Better organic solubility than NSAF but reduced dispersing efficiency in aqueous systems .
Para-Toluene Sulfonic Acid (PTSA) Derivatives
Synthesis : Toluene is sulfonated and condensed with formaldehyde, yielding shorter-chain polymers .
Structural Differences :
- Aromatic Core : Toluene instead of naphthalene reduces π-π interactions, lowering adsorption capacity .
- Functional Groups : –SO₃H and –CH₃ groups .
Performance :
- Thermal Stability : Degrades above 150°C, limiting high-temperature applications .
- Catalytic Efficiency : Inferior to fluoro-substituted sulfonic acids in carbonylation reactions .
Polycarboxylate Ethers (PCEs)
Synthesis: Carboxylic acid monomers copolymerized with polyethylene glycol (PEG) . Structural Differences:
- Functional Groups : –COOH and –O–(CH₂CH₂O)ₙ– side chains .
- Molecular Weight : 20,000–50,000 Da, significantly higher than NSAF .
Performance :
- Dispersing Efficiency : Superior to NSAF due to comb-like structure providing steric hindrance .
- Cost : 3–5× more expensive than NSAF .
Data Table: Comparative Analysis
Compound | Key Functional Groups | Molecular Weight (Da) | Primary Applications | Thermal Stability (°C) | Dispersing Efficiency (vs. NSAF) |
---|---|---|---|---|---|
NSAF | –SO₃H, –CH₂– | 1,500–3,000 | Cement, dyes, pesticides | 200–250 | Baseline |
SPNS | –SO₃⁻Na⁺ | 3,000–10,000 | High-range concrete | >250 | +20% (aqueous systems) |
Alkylnaphthalene Sulfonates | –SO₃H, alkyl chains | 1,000–2,000 | Rubber, coatings | 150–200 | -30% (aqueous), +50% (organic) |
PTSA Derivatives | –SO₃H, –CH₃ | 800–1,500 | Composites, catalysis | <150 | -50% |
Polycarboxylate Ethers | –COOH, –O–PEG | 20,000–50,000 | High-performance concrete | >300 | +100% |
Research Findings and Contradictions
- NSAF vs. SPNS : While SPNS offers better thermal stability, NSAF is preferred in cost-sensitive applications like dye dispersion .
- NSAF vs. PCEs : PCEs outperform NSAF in concrete but require precise dosing due to sensitivity to cement composition .
- Contradiction : Dodecyl benzene sulfonic acid (similar to alkylnaphthalene sulfonates) shows poor catalytic performance in carbonylation , contrasting its efficacy in dispersant applications .
属性
CAS 编号 |
577773-56-9 |
---|---|
分子式 |
C11H10O4S |
分子量 |
238.26 g/mol |
IUPAC 名称 |
formaldehyde;naphthalene-1-sulfonic acid |
InChI |
InChI=1S/C10H8O3S.CH2O/c11-14(12,13)10-7-3-5-8-4-1-2-6-9(8)10;1-2/h1-7H,(H,11,12,13);1H2 |
InChI 键 |
NVVZQXQBYZPMLJ-UHFFFAOYSA-N |
规范 SMILES |
C=O.C1=CC=C2C(=C1)C=CC=C2S(=O)(=O)O |
产品来源 |
United States |
Synthesis routes and methods I
Procedure details
Synthesis routes and methods II
Procedure details
Synthesis routes and methods III
Procedure details
Synthesis routes and methods IV
Procedure details
体外研究产品的免责声明和信息
请注意,BenchChem 上展示的所有文章和产品信息仅供信息参考。 BenchChem 上可购买的产品专为体外研究设计,这些研究在生物体外进行。体外研究,源自拉丁语 "in glass",涉及在受控实验室环境中使用细胞或组织进行的实验。重要的是要注意,这些产品没有被归类为药物或药品,他们没有得到 FDA 的批准,用于预防、治疗或治愈任何医疗状况、疾病或疾病。我们必须强调,将这些产品以任何形式引入人类或动物的身体都是法律严格禁止的。遵守这些指南对确保研究和实验的法律和道德标准的符合性至关重要。