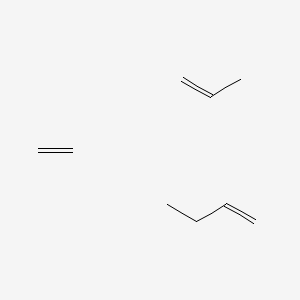
Ethene propene 1-butene
描述
Ethene propene 1-butene is a useful research compound. Its molecular formula is C9H18 and its molecular weight is 126.24 g/mol. The purity is usually 95%.
BenchChem offers high-quality this compound suitable for many research applications. Different packaging options are available to accommodate customers' requirements. Please inquire for more information about this compound including the price, delivery time, and more detailed information at info@benchchem.com.
属性
CAS 编号 |
25895-47-0 |
---|---|
分子式 |
C9H18 |
分子量 |
126.24 g/mol |
IUPAC 名称 |
but-1-ene;ethene;prop-1-ene |
InChI |
InChI=1S/C4H8.C3H6.C2H4/c1-3-4-2;1-3-2;1-2/h3H,1,4H2,2H3;3H,1H2,2H3;1-2H2 |
InChI 键 |
IYYGCUZHHGZXGJ-UHFFFAOYSA-N |
规范 SMILES |
CCC=C.CC=C.C=C |
相关CAS编号 |
827599-27-9 119008-27-4 25895-47-0 89917-24-8 |
产品来源 |
United States |
Synthesis routes and methods I
Procedure details
Synthesis routes and methods II
Procedure details
Synthesis routes and methods III
Procedure details
Synthesis routes and methods IV
Procedure details
Synthesis routes and methods V
Procedure details
体外研究产品的免责声明和信息
请注意,BenchChem 上展示的所有文章和产品信息仅供信息参考。 BenchChem 上可购买的产品专为体外研究设计,这些研究在生物体外进行。体外研究,源自拉丁语 "in glass",涉及在受控实验室环境中使用细胞或组织进行的实验。重要的是要注意,这些产品没有被归类为药物或药品,他们没有得到 FDA 的批准,用于预防、治疗或治愈任何医疗状况、疾病或疾病。我们必须强调,将这些产品以任何形式引入人类或动物的身体都是法律严格禁止的。遵守这些指南对确保研究和实验的法律和道德标准的符合性至关重要。