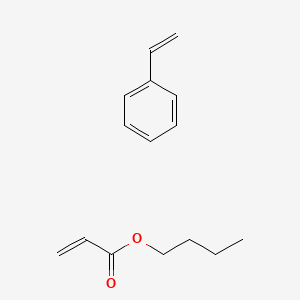
Butyl prop-2-enoate;styrene
概述
描述
Butyl prop-2-enoate;styrene is a copolymer formed from the polymerization of butyl acrylate and styrene. This compound is known for its versatility and is widely used in various industrial applications due to its excellent mechanical properties, chemical resistance, and ease of processing .
准备方法
Synthetic Routes and Reaction Conditions
The synthesis of Butyl prop-2-enoate;styrene involves the polymerization of butyl acrylate and styrene monomers. The polymerization can be carried out using different methods such as solution polymerization, suspension polymerization, or emulsion polymerization. The choice of method depends on the desired properties of the final product .
Solution Polymerization: This method involves dissolving the monomers in a suitable solvent and initiating the polymerization reaction using a free radical initiator such as benzoyl peroxide or azobisisobutyronitrile. The reaction is typically carried out at temperatures ranging from 60°C to 90°C.
Suspension Polymerization: In this method, the monomers are dispersed in water with the help of a stabilizer such as polyvinyl alcohol. The polymerization is initiated using a water-soluble initiator like potassium persulfate. The reaction temperature is usually maintained between 70°C and 90°C.
Emulsion Polymerization: This method involves emulsifying the monomers in water using surfactants. The polymerization is initiated using a water-soluble initiator, and the reaction is carried out at temperatures between 50°C and 80°C.
Industrial Production Methods
Industrial production of this compound typically employs emulsion polymerization due to its ability to produce high molecular weight polymers with excellent mechanical properties. The process involves continuous monitoring and control of reaction parameters to ensure consistent product quality .
化学反应分析
Types of Reactions
Butyl prop-2-enoate;styrene can undergo various chemical reactions, including:
Oxidation: The polymer can be oxidized using strong oxidizing agents such as potassium permanganate or hydrogen peroxide. This reaction can lead to the formation of carboxylic acid groups on the polymer chain.
Reduction: Reduction reactions can be carried out using reducing agents like lithium aluminum hydride or sodium borohydride. These reactions can convert carbonyl groups to alcohols.
Substitution: The polymer can undergo substitution reactions where functional groups on the polymer chain are replaced with other groups. For example, halogenation can be achieved using halogens like chlorine or bromine.
Common Reagents and Conditions
Oxidation: Potassium permanganate in acidic or neutral conditions, hydrogen peroxide in the presence of a catalyst.
Reduction: Lithium aluminum hydride in anhydrous conditions, sodium borohydride in protic solvents.
Substitution: Halogens (chlorine, bromine) in the presence of light or a catalyst.
Major Products Formed
Oxidation: Formation of carboxylic acid groups.
Reduction: Formation of alcohol groups.
Substitution: Formation of halogenated polymers.
科学研究应用
Butyl prop-2-enoate;styrene has a wide range of applications in scientific research and industry:
Chemistry: Used as a precursor for the synthesis of various functionalized polymers. It is also used in the development of polymer blends and composites.
Biology: Employed in the fabrication of biocompatible materials for medical devices and drug delivery systems.
Medicine: Utilized in the production of medical implants, prosthetics, and tissue engineering scaffolds.
作用机制
The mechanism of action of Butyl prop-2-enoate;styrene involves the formation of a polymer network through the polymerization of butyl acrylate and styrene monomers. The polymerization process creates a three-dimensional network of polymer chains, which imparts the material with its unique mechanical and chemical properties. The molecular targets and pathways involved in this process include the initiation, propagation, and termination steps of free radical polymerization .
相似化合物的比较
Butyl prop-2-enoate;styrene can be compared with other similar compounds such as:
2-Propenoic acid, butyl ester, polymer with 1,3-butadiene and ethenylbenzene: This compound has similar properties but includes 1,3-butadiene, which can enhance the flexibility and impact resistance of the polymer.
2-Propenoic acid, 2-methyl-, methyl ester, polymer with butyl 2-propenoate and ethenylbenzene: This compound includes methyl methacrylate, which can improve the hardness and transparency of the polymer.
The uniqueness of this compound lies in its balanced combination of mechanical strength, chemical resistance, and ease of processing, making it suitable for a wide range of applications.
属性
CAS 编号 |
25767-47-9 |
---|---|
分子式 |
C15H20O2 |
分子量 |
232.32 g/mol |
IUPAC 名称 |
butyl prop-2-enoate;styrene |
InChI |
InChI=1S/C8H8.C7H12O2/c1-2-8-6-4-3-5-7-8;1-3-5-6-9-7(8)4-2/h2-7H,1H2;4H,2-3,5-6H2,1H3 |
InChI 键 |
TUZBYYLVVXPEMA-UHFFFAOYSA-N |
SMILES |
CCCCOC(=O)C=C.C=CC1=CC=CC=C1 |
规范 SMILES |
CCCCOC(=O)C=C.C=CC1=CC=CC=C1 |
Key on ui other cas no. |
25767-47-9 |
产品来源 |
United States |
Synthesis routes and methods I
Procedure details
Synthesis routes and methods II
Procedure details
Synthesis routes and methods III
Procedure details
Synthesis routes and methods IV
Procedure details
Synthesis routes and methods V
Procedure details
体外研究产品的免责声明和信息
请注意,BenchChem 上展示的所有文章和产品信息仅供信息参考。 BenchChem 上可购买的产品专为体外研究设计,这些研究在生物体外进行。体外研究,源自拉丁语 "in glass",涉及在受控实验室环境中使用细胞或组织进行的实验。重要的是要注意,这些产品没有被归类为药物或药品,他们没有得到 FDA 的批准,用于预防、治疗或治愈任何医疗状况、疾病或疾病。我们必须强调,将这些产品以任何形式引入人类或动物的身体都是法律严格禁止的。遵守这些指南对确保研究和实验的法律和道德标准的符合性至关重要。