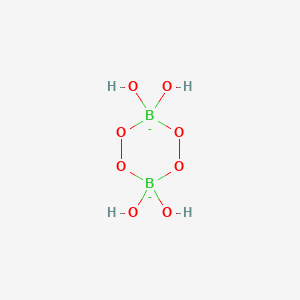
Perborate
描述
Perborate(2-) is a boron oxoanion.
科学研究应用
Applications in Cleaning Products
Detergents and Laundry Products
- Sodium perborate is widely used in laundry detergents as a bleaching agent due to its ability to release active oxygen at elevated temperatures (above 60°C) and even at lower temperatures when combined with activators like tetraacetylethylenediamine (TAED) .
- It is less aggressive than chlorine-based bleaches, making it suitable for colored fabrics .
Household Cleaners
- Beyond laundry, sodium this compound is incorporated into various household cleaning products, including automatic dishwasher detergents and stain removers. Its effectiveness as a bleach booster enhances the overall cleaning performance of these products .
Dental Applications
Tooth Bleaching
- Sodium this compound is commonly used in tooth bleaching techniques for non-vital teeth. It acts as an internal bleaching agent, releasing hydrogen peroxide that penetrates the tooth structure to remove stains .
- Research indicates that sodium this compound can effectively reduce the colonization of anaerobic bacteria in oral wounds, supporting its use in dental care .
Safety Assessments
- Recent studies have evaluated the cytotoxicity of sodium this compound in oral care products, demonstrating that at commercial concentrations (around 0.06 mg/mL), it exhibits minimal toxicity . This finding emphasizes the need for rigorous safety testing protocols in product formulation.
Organic Synthesis
Sodium this compound serves as an oxidizing agent in organic chemistry:
- It can convert thioethers to sulfoxides and sulfones and is used as a milder alternative to hydrogen peroxide for various oxidation reactions .
- In specific reactions, such as the conversion of aryl halides to phenols, sodium this compound provides an efficient pathway while minimizing by-product formation .
Environmental Remediation
Advanced Oxidation Processes
- Recent studies highlight the potential of sodium this compound in environmental applications, particularly for remediating organic pollutants like phenol. When combined with iron-bearing materials, it enhances the generation of reactive oxygen species that facilitate the oxidation and degradation of contaminants .
- This application positions sodium this compound as a promising candidate for treating recalcitrant organic compounds in both natural and engineered environments.
Summary of Key Applications
Application Area | Description |
---|---|
Cleaning Products | Used as a bleaching agent in laundry detergents and household cleaners; effective stain remover. |
Dental Care | Employed in tooth bleaching; supports antibacterial action in oral care products. |
Organic Synthesis | Acts as an oxidizing agent for various chemical transformations; alternative to hydrogen peroxide. |
Environmental Remediation | Facilitates advanced oxidation processes for degrading organic pollutants like phenol. |
常见问题
Basic Research Questions
Q. How to prepare phosphate-citrate buffer systems containing sodium perborate for enzyme activity assays?
Sodium this compound is often integrated into phosphate-citrate buffers (pH 5.0) for enzymatic studies. To prepare 0.05 M buffer:
- Dissolve one phosphate-citrate buffer capsule (e.g., Sigma-Aldrich P4922) in 100 mL ultrapure water.
- Adjust pH to 5.0 and add 0.03% (w/v) sodium this compound.
- For reaction termination, add 50 µL of 2 M H₂SO₄ per 200 µL reaction mixture to acidify the medium and halt enzymatic activity .
Q. What factors determine the selection of sodium this compound monohydrate versus tetrahydrate in oxidation experiments?
Sodium this compound monohydrate (NaBO₃·H₂O) is preferred for its higher oxygen content (active species yield), thermal stability, and solubility in aqueous systems compared to tetrahydrate. Monohydrate is optimal for low-temperature reactions (40–60°C), while tetrahydrate may require activators like tetra-acetylethylenediamine (TAED) for decomposition .
Q. What are the best practices for stabilizing sodium this compound in laboratory settings?
Store sodium this compound in airtight containers under cool, dry conditions to prevent hydrolysis. Pre-dissolve in buffers immediately before use to minimize premature decomposition. Avoid prolonged exposure to humid air or temperatures >60°C, which accelerate oxygen release .
Advanced Research Questions
Q. How to identify radical species generated in this compound-based advanced oxidation processes (AOPs)?
Use electron paramagnetic resonance (EPR) with spin traps like DMPO (5,5-dimethyl-1-pyrroline-N-oxide) to detect hydroxyl (•OH) and superoxide (O₂•⁻) radicals. For example:
- In Fe(0)-perborate systems, EPR spectra show dominant •OH signals (DMPO-OH adducts at 1:2:2:1 quartet).
- Carbonaceous material-perborate systems exhibit weaker radical signals, suggesting non-radical electron transfer pathways via graphitic structures .
Q. How does this compound compare to hydrogen peroxide in UV-driven AOPs for contaminant degradation?
this compound (NaBO₃) generates H₂O₂ in situ under acidic or UV conditions, enabling comparable •OH yields to H₂O₂. Key differences:
- This compound requires lower UV energy for activation due to its borate matrix.
- Acetic acid additives enhance this compound’s oxidative capacity by forming peracetic acid, unlike H₂O₂ systems. Validate via kinetic assays (e.g., pseudo-first-order rate constants) and TOC removal analysis .
Q. What experimental approaches distinguish radical vs. non-radical oxidation mechanisms in this compound systems?
- Radical scavengers : Add tert-butanol (•OH scavenger) or NaN₃ (singlet oxygen quencher). Inhibition of phenol degradation confirms radical dominance.
- Electron transfer probes : Use electrochemical analysis (e.g., cyclic voltammetry) to detect direct oxidation via carbonaceous materials’ graphitic layers.
- EPR-negative systems : Absence of radical signals with retained degradation efficiency indicates non-radical pathways .
Q. How do iron-bearing and carbonaceous materials synergize with this compound for pollutant degradation?
- Zero-valent iron (ZVI) : Fe⁰ donates electrons to this compound, accelerating H₂O₂ decomposition into •OH. Monitor Fe²⁺/Fe³⁺ ratios via ferrozine assays to track redox cycling.
- Biochar/graphite : π-electron-rich surfaces activate this compound, enabling electron transfer to adsorbed pollutants. Characterize material defects via Raman spectroscopy (D/G band ratios) .
Q. How to assess ecotoxicological risks of this compound byproducts in wastewater treatment studies?
Conduct acute toxicity assays using Daphnia magna (LC₅₀ = 11–30 mg/L) and algal models (Pseudokirchneriella subcapitata, EC₅₀ = 3.3–20 mg/L). Compare degradation byproduct toxicity via Microtox® or in vitro cell viability assays. Note: Residual H₂O₂ drives toxicity, not borate .
Q. Methodological Notes
准备方法
Traditional Two-Step Synthesis via Sodium Peroxide and Hydrogen Peroxide
The foundational method for sodium perborate production, patented in 1927, involves a sequential reaction of borax (Na₂B₄O₇·10H₂O) with sodium peroxide (Na₂O₂) followed by hydrogen peroxide (H₂O₂) . This two-step approach optimizes oxidation efficiency while minimizing side reactions.
Reaction Mechanism and Stoichiometry
The process begins with borax dissolution in cold water (≤15°C) to form a metastable solution. Sodium peroxide is added to convert borax into sodium metaborate (NaBO₂) and partially oxidize it to this compound:
2\text{B}4\text{O}7 + 2\text{Na}2\text{O}2 + 11\text{H}2\text{O} \rightarrow 4\text{NaBO}3·\text{H}2\text{O} + 2\text{NaOH} + 6\text{H}_2\text{O}
Excess hydrogen peroxide is then introduced at 8–12°C to complete the oxidation, yielding crystalline sodium this compound tetrahydrate (NaBO₃·4H₂O) .
Process Conditions and Yield Optimization
-
Temperature Control : Initial reaction stages require strict temperature maintenance (12–20°C) to prevent this compound decomposition. Exceeding 20°C risks oxygen loss, while temperatures below 15°C leave unreacted borax .
-
Reagent Ratios : A molar ratio of 1:1:3 (borax:sodium peroxide:hydrogen peroxide) achieves >90% conversion efficiency .
-
Mother Liquor Recycling : The spent solution from crystallization (saturated with NaBO₃ at 0°C) is reused for subsequent batches, reducing raw material costs by 15–20% .
Table 1: Traditional Two-Step Process Parameters
Parameter | Optimal Range | Impact on Yield |
---|---|---|
Borax concentration | 200–250 g/L | Higher solubility at 15°C |
Na₂O₂ addition rate | 0.5 mol/min per 100 L | Prevents thermal runaway |
H₂O₂ cooling temperature | 8–12°C | Maximizes crystal purity |
Continuous Slurry Reactor Method for Industrial-Scale Production
A 2025 patent outlines a continuous process that operates at elevated temperatures (20–50°C), significantly reducing refrigeration costs compared to traditional methods . This approach uses a slurry reactor to maintain supersaturation and control crystal growth.
Reaction Dynamics and pH Management
Sodium metaborate (NaBO₂·2H₂O) is reacted with hydrogen peroxide in a slurry containing sodium this compound seed crystals. The liquid phase maintains:
-
Free borax (Na₂B₄O₇) at 10–30 g/L to inhibit side reactions
-
pH 9.4–9.9 to stabilize this compound ions and prevent H₂O₂ decomposition
The overall reaction is:
2·2\text{H}2\text{O} + \text{H}2\text{O}2 + \text{H}2\text{O} \rightarrow \text{NaBO}3·4\text{H}_2\text{O}
Advantages Over Batch Processing
-
Throughput : Continuous feed and withdrawal enable 24/7 operation, increasing annual output by 40% .
-
Product Quality : Crystals grown in slurry exhibit uniform size (50–100 μm) and reduced caking tendency due to lower surface moisture (<0.5%) .
-
Energy Efficiency : Operating at 30°C cuts refrigeration energy use by 70% compared to traditional 10°C processes .
Table 2: Comparative Analysis of Production Methods
Sodium Hydroxide-Assisted Synthesis for High-Purity Grades
A variant method incorporates sodium hydroxide (NaOH) to enhance borax dissolution and metaborate formation . This approach is preferred for pharmaceutical-grade this compound requiring >99.9% purity.
Process Modifications
-
Borax Alkalinization :
NaOH addition (1.05:1 molar ratio to borax) ensures complete conversion to metaborate .
-
Controlled Peroxidation : H₂O₂ is added at 5–10°C with ultrasonic agitation to prevent localized overheating.
Quality Control Measures
-
ICP-MS Analysis : Limits heavy metals (As <1 ppm, Pb <0.5 ppm) for medical applications .
-
Crystal Washing : Ethanol-water (70:30) solution removes residual borates, achieving <0.1% impurity levels .
Economic and Environmental Considerations
Cost Breakdown (2025 Data)
Table 3: Production Cost Analysis per Metric Ton
Component | Traditional Method | Continuous Method |
---|---|---|
Borax (40% B₂O₃) | $320 | $310 |
Sodium peroxide | $280 | – |
Hydrogen peroxide (50%) | $150 | $410 |
Energy | $85 | $30 |
Labor | $120 | $90 |
Total | $955 | $840 |
Sustainability Challenges
-
Borate Emissions : Closed-loop systems recover 95% of boron, reducing wastewater contamination .
-
Carbon Footprint : Continuous processes emit 0.8 tCO₂/ton vs. 1.5 tCO₂/ton for batch methods .
Emerging Trends and Research Directions
Catalytic Peroxidation
Pilot-scale studies show vanadium-doped catalysts accelerate H₂O₂ activation, reducing reaction time by 35% at 25°C .
Solvent-Free Synthesis
Mechanochemical methods using borax and sodium percarbonate in ball mills achieve 82% yield without aqueous solvents, though crystal morphology remains irregular .
属性
分子式 |
B2H4O8-2 |
---|---|
分子量 |
153.65 g/mol |
IUPAC 名称 |
3,3,6,6-tetrahydroxy-1,2,4,5-tetraoxa-3,6-diboranuidacyclohexane |
InChI |
InChI=1S/B2H4O8/c3-1(4)7-9-2(5,6)10-8-1/h3-6H/q-2 |
InChI 键 |
PNIJRIIGBGFYHF-UHFFFAOYSA-N |
SMILES |
[B-]1(OO[B-](OO1)(O)O)(O)O |
规范 SMILES |
[B-]1(OO[B-](OO1)(O)O)(O)O |
产品来源 |
United States |
Synthesis routes and methods I
Procedure details
Synthesis routes and methods II
Procedure details
Retrosynthesis Analysis
AI-Powered Synthesis Planning: Our tool employs the Template_relevance Pistachio, Template_relevance Bkms_metabolic, Template_relevance Pistachio_ringbreaker, Template_relevance Reaxys, Template_relevance Reaxys_biocatalysis model, leveraging a vast database of chemical reactions to predict feasible synthetic routes.
One-Step Synthesis Focus: Specifically designed for one-step synthesis, it provides concise and direct routes for your target compounds, streamlining the synthesis process.
Accurate Predictions: Utilizing the extensive PISTACHIO, BKMS_METABOLIC, PISTACHIO_RINGBREAKER, REAXYS, REAXYS_BIOCATALYSIS database, our tool offers high-accuracy predictions, reflecting the latest in chemical research and data.
Strategy Settings
Precursor scoring | Relevance Heuristic |
---|---|
Min. plausibility | 0.01 |
Model | Template_relevance |
Template Set | Pistachio/Bkms_metabolic/Pistachio_ringbreaker/Reaxys/Reaxys_biocatalysis |
Top-N result to add to graph | 6 |
Feasible Synthetic Routes
体外研究产品的免责声明和信息
请注意,BenchChem 上展示的所有文章和产品信息仅供信息参考。 BenchChem 上可购买的产品专为体外研究设计,这些研究在生物体外进行。体外研究,源自拉丁语 "in glass",涉及在受控实验室环境中使用细胞或组织进行的实验。重要的是要注意,这些产品没有被归类为药物或药品,他们没有得到 FDA 的批准,用于预防、治疗或治愈任何医疗状况、疾病或疾病。我们必须强调,将这些产品以任何形式引入人类或动物的身体都是法律严格禁止的。遵守这些指南对确保研究和实验的法律和道德标准的符合性至关重要。