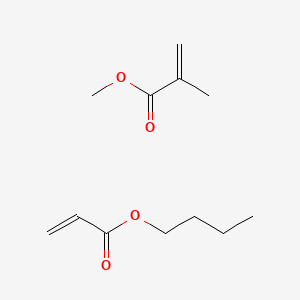
butyl prop-2-enoate; methyl 2-methylprop-2-enoate
概述
描述
Butyl prop-2-enoate: and methyl 2-methylprop-2-enoate are organic compounds that belong to the ester family. These compounds are commonly used in the production of polymers and copolymers, which are essential in various industrial applications. They are known for their ability to undergo polymerization reactions, making them valuable in the manufacturing of plastics, resins, and coatings.
准备方法
Synthetic Routes and Reaction Conditions
-
Butyl prop-2-enoate
Esterification: This compound can be synthesized through the esterification of prop-2-enoic acid with butanol in the presence of an acid catalyst such as sulfuric acid. The reaction is typically carried out under reflux conditions to ensure complete conversion.
Transesterification: Another method involves the transesterification of methyl prop-2-enoate with butanol, using a base catalyst like sodium methoxide.
-
Methyl 2-methylprop-2-enoate
Esterification: This compound is commonly prepared by esterifying 2-methylprop-2-enoic acid with methanol in the presence of an acid catalyst. The reaction is conducted under reflux to achieve high yields.
Transesterification: Similar to butyl prop-2-enoate, methyl 2-methylprop-2-enoate can also be synthesized via transesterification of ethyl 2-methylprop-2-enoate with methanol.
Industrial Production Methods
Continuous Process: In industrial settings, these esters are often produced using continuous esterification processes. This involves the continuous feeding of reactants and removal of products, which enhances efficiency and yield.
Catalytic Distillation: This method combines reaction and separation in a single unit, allowing for the efficient production of high-purity esters.
化学反应分析
Types of Reactions
-
Polymerization
- Both butyl prop-2-enoate and methyl 2-methylprop-2-enoate undergo free radical polymerization to form homopolymers and copolymers. This reaction is initiated by free radical initiators such as benzoyl peroxide or azobisisobutyronitrile.
Conditions: The polymerization is typically carried out at elevated temperatures (60-80°C) in the presence of a solvent like toluene or ethyl acetate.
-
Hydrolysis
- These esters can be hydrolyzed under acidic or basic conditions to yield the corresponding carboxylic acids and alcohols.
Conditions: Acidic hydrolysis is performed using dilute hydrochloric acid, while basic hydrolysis employs sodium hydroxide.
Major Products
Polymerization: The major products are polymers and copolymers used in coatings, adhesives, and plastics.
Hydrolysis: The products are prop-2-enoic acid and butanol for butyl prop-2-enoate, and 2-methylprop-2-enoic acid and methanol for methyl 2-methylprop-2-enoate.
科学研究应用
-
Chemistry
- These esters are used as monomers in the synthesis of various polymers and copolymers. They are also employed as intermediates in organic synthesis.
-
Biology
- In biological research, these compounds are used to study the effects of esters on cellular processes and enzyme activities.
-
Medicine
- Methyl 2-methylprop-2-enoate is used in the formulation of certain pharmaceutical products due to its ability to form biocompatible polymers.
-
Industry
- Butyl prop-2-enoate is widely used in the production of coatings, adhesives, and sealants. Methyl 2-methylprop-2-enoate is utilized in the manufacture of resins and plastics.
作用机制
Polymerization: The polymerization of these esters involves the formation of free radicals, which initiate the chain reaction leading to the formation of polymers. The double bonds in the esters react with the free radicals, resulting in the propagation of the polymer chain.
Hydrolysis: The hydrolysis mechanism involves the nucleophilic attack of water (or hydroxide ions) on the carbonyl carbon of the ester, leading to the formation of the corresponding carboxylic acid and alcohol.
相似化合物的比较
-
Similar Compounds
Ethyl prop-2-enoate: Similar to butyl prop-2-enoate but with an ethyl group instead of a butyl group.
Methyl prop-2-enoate: Similar to methyl 2-methylprop-2-enoate but without the methyl substitution on the double bond.
Butyl methacrylate: Similar to butyl prop-2-enoate but with a methyl group on the alpha carbon.
-
Uniqueness
Butyl prop-2-enoate: Offers better flexibility and adhesion properties in coatings compared to ethyl prop-2-enoate.
Methyl 2-methylprop-2-enoate: Provides higher thermal stability and resistance to UV degradation compared to methyl prop-2-enoate.
属性
CAS 编号 |
25852-37-3 |
---|---|
分子式 |
C12H20O4 |
分子量 |
228.28 g/mol |
IUPAC 名称 |
butyl prop-2-enoate;methyl 2-methylprop-2-enoate |
InChI |
InChI=1S/C7H12O2.C5H8O2/c1-3-5-6-9-7(8)4-2;1-4(2)5(6)7-3/h4H,2-3,5-6H2,1H3;1H2,2-3H3 |
InChI 键 |
AHVOFPQVUVXHNL-UHFFFAOYSA-N |
SMILES |
CCCCOC(=O)C=C.CC(=C)C(=O)OC |
规范 SMILES |
CCCCOC(=O)C=C.CC(=C)C(=O)OC |
同义词 |
utyl acrylate-methyl methacrylate copolymer Dakril 4B Dakril-4B methyl methacrylate-butyl acrylate copolyme |
产品来源 |
United States |
Synthesis routes and methods I
Procedure details
Synthesis routes and methods II
Procedure details
Synthesis routes and methods III
Procedure details
Synthesis routes and methods IV
Procedure details
Synthesis routes and methods V
Procedure details
体外研究产品的免责声明和信息
请注意,BenchChem 上展示的所有文章和产品信息仅供信息参考。 BenchChem 上可购买的产品专为体外研究设计,这些研究在生物体外进行。体外研究,源自拉丁语 "in glass",涉及在受控实验室环境中使用细胞或组织进行的实验。重要的是要注意,这些产品没有被归类为药物或药品,他们没有得到 FDA 的批准,用于预防、治疗或治愈任何医疗状况、疾病或疾病。我们必须强调,将这些产品以任何形式引入人类或动物的身体都是法律严格禁止的。遵守这些指南对确保研究和实验的法律和道德标准的符合性至关重要。