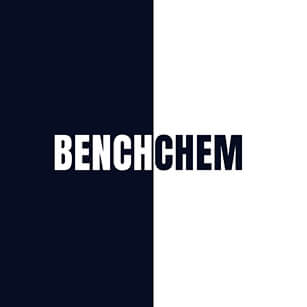
Residues, precious metal-refining
- 点击 快速询问 获取最新报价。
- 提供有竞争力价格的高质量产品,您可以更专注于研究。
描述
Residues, precious metal-refining, also known as this compound, is a useful research compound. Its molecular formula is C16H22O3Si. The purity is usually 95%.
BenchChem offers high-quality this compound suitable for many research applications. Different packaging options are available to accommodate customers' requirements. Please inquire for more information about this compound including the price, delivery time, and more detailed information at info@benchchem.com.
科学研究应用
Key Applications
-
Recovery from Electronic Waste
- Process : The oxidative refining process has been employed to recover precious metals from waste electrical and electronic equipment (WEEE). This method effectively concentrates metals like palladium and gold through controlled oxidation at elevated temperatures.
- Case Study : A study indicated that refining at 1400 °C significantly increased the concentrations of palladium and gold in the final product .
-
Spent Catalysts Recycling
- Process : Spent industrial catalysts contain significant amounts of platinum group metals (PGMs). Companies like Umicore utilize specialized processes to recover these metals efficiently.
- Case Study : Umicore's facilities recover over 90% of precious metals from spent catalysts through a combination of hydrometallurgical and pyrometallurgical techniques .
-
Platinum Group Metals Recovery
- Process : Advanced technologies such as the MRT™ (Metal Recovery Technology) allow for the selective recovery of individual PGMs from various matrices including plating baths and sludge.
- Case Study : Isondo Precious Metals employs MRT™ for recycling iridium, ruthenium, and platinum from membrane electrode assemblies used in hydrogen production .
-
Potassium Gold Cyanide Recovery
- Process : The MRT™ process also enables the recovery of potassium gold cyanide from spent gold plating solutions, streamlining the recycling process by eliminating several steps traditionally required for gold recovery.
- Efficiency : This method reduces processing time and costs while maintaining high recovery rates .
Challenges in Precious Metal Refining
The presence of base metals and impurities complicates the refining process. Techniques such as oxidative pre-treatment followed by hydrochlorination have been developed to enhance the purity of recovered precious metals. These methods allow for near-quantitative removal of unwanted elements prior to refining .
Data Tables
The following table summarizes the concentration levels of various metals before and after the oxidative refining process:
Element | Initial Concentration (wt.%) | Final Concentration (wt.%) |
---|---|---|
Copper | 89.20 | 0.05 |
Palladium | 0.28 | 0.57 |
Gold | 0.06 | 0.22 |
Nickel | 3.42 | 0.10 |
This data illustrates the effectiveness of modern refining techniques in enhancing metal recovery rates while reducing impurities.
化学反应分析
Oxidative Refining with O₂/N₂ Gas Mixtures
Oxidative refining selectively oxidizes base metals (Cu, Fe, Ni, Si) in residues, concentrating precious metals (Pd, Au) in the metal phase .
Key Reactions:
-
Copper oxidation :
2Cu+O2→2CuO -
Iron oxidation :
4Fe+3O2→2Fe2O3 -
Silicon oxidation :
Si+O2→SiO2
Process Parameters:
Parameter | Optimal Value | Precious Metal Enrichment | Impurity Removal Efficiency |
---|---|---|---|
Temperature | 1400°C | Au: 1.5×, Pd: 1.8× | Fe: 98%, Ni: 95% |
Gas Flow Rate | 4 L/min | Au: 2.1×, Pd: 2.4× | Si: 92%, P: 89% |
Time | 40 min | Au: 1.9×, Pd: 2.2× | Cu: 85% |
Slag phases (Fe₂SiO₄, CuO) sequester oxidized impurities, while precious metals remain metallic .
Nitric Acid Leaching of Silver :
3Ag+4HNO3→3AgNO3+NO+2H2O
[HNO₃] | Temp (°C) | Ag Leaching Yield (%) | Residue Mass (%) |
---|---|---|---|
4 M | 65 | 92 | 8.5 |
6 M | 80 | 95 | 7.8 |
Thiourea Precipitation :
Using H₂O₂ as an oxidizer:
Au0+2SC NH2 2→Au SC NH2 2 2++e−
Resulting in Au recovery efficiencies >90% but with sulfur co-precipitation (up to 15 wt.% S) .
Selective Sorption of PGMs :
Resin Type | Precious Metal | Sorption Efficiency (%) | Competing Ion Interference |
---|---|---|---|
Puromet MTS9200 | Pt | 98 | Cu (>5 g/L reduces to 72%) |
Lewatit MonoPlus MP600 | Rh | 91 | Requires pH > 3 |
Solution Composition :
Element | Pt (mg/L) | Pd (mg/L) | Rh (mg/L) | Au (mg/L) | Cu (g/L) | Zn (g/L) |
---|---|---|---|---|---|---|
Value | 45.2 | 32.7 | 8.4 | 12.1 | 18.9 | 9.7 |
Pyrometallurgical Hydrochlorination
Upgrading concentrates via chlorination at 800–1100°C :
PbS+2HCl→PbCl2+H2S
Cu2O+2HCl→2CuCl+H2O
Volatile chlorides (ZnCl₂, PbCl₂) are removed, leaving precious metals unreacted. Ruthenium loss is minimized by controlling HCl/H₂O ratios .
Electrolytic Recovery
Electrowinning from cyanide solutions :
Au CN 2−+e−→Au+2CN−
Cathode Material | Current Density (A/m²) | Au Recovery (%) | Energy Consumption (kWh/kg) |
---|---|---|---|
Steel Wool | 200 | 99.5 | 4.2 |
Titanium Mesh | 300 | 98.8 | 5.1 |
Case Study: Refining Catalyst Residues
Alfa Chemistry’s process for Rh recovery from octoate catalysts :
-
Acid digestion : Rh organics+HNO3→Rh3++CO2+H2O
-
Precipitation : Rh3++3OH−→Rh OH 3
-
Reduction : Rh OH 3+3H2→Rh+3H2O
Final recovery rates exceed 95% with <2% impurity carryover .
These methodologies highlight the interplay of thermodynamics, kinetics, and reagent selection in maximizing precious metal recovery while minimizing environmental impact.
属性
CAS 编号 |
124222-18-0 |
---|---|
分子式 |
C16H22O3Si |
分子量 |
0 |
同义词 |
Residues, precious metal-refining |
产品来源 |
United States |
体外研究产品的免责声明和信息
请注意,BenchChem 上展示的所有文章和产品信息仅供信息参考。 BenchChem 上可购买的产品专为体外研究设计,这些研究在生物体外进行。体外研究,源自拉丁语 "in glass",涉及在受控实验室环境中使用细胞或组织进行的实验。重要的是要注意,这些产品没有被归类为药物或药品,他们没有得到 FDA 的批准,用于预防、治疗或治愈任何医疗状况、疾病或疾病。我们必须强调,将这些产品以任何形式引入人类或动物的身体都是法律严格禁止的。遵守这些指南对确保研究和实验的法律和道德标准的符合性至关重要。