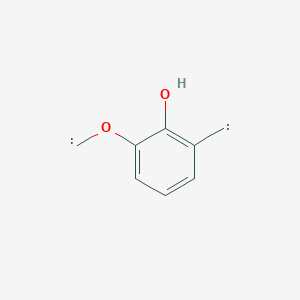
Phenol-formaldehyde resin
描述
Phenol-formaldehyde (PF) resins, first synthesized by Leo Baekeland in 1909, are thermosetting polymers renowned for their exceptional mechanical strength, chemical resistance, and thermal stability . These resins are widely used in wood composites, adhesives, coatings, and electrical insulation due to their robust bonding performance and environmental durability . However, PF resins face challenges such as high production costs, formaldehyde emissions, and reliance on petrochemical-derived phenol . Recent research focuses on modifying PF resins with bio-based materials (e.g., lignin, tannin, bio-oil) and comparing their performance with alternative resins like urea-formaldehyde (UF), melamine-formaldehyde (MF), and epoxy resins . This article provides a detailed comparison of PF resins with similar compounds, supported by experimental data and authoritative references.
准备方法
Traditional Preparation Methods
The foundational synthesis of PF resins involves step-growth polymerization, typically conducted in batch reactors with precise temperature and pH control. A seminal patent (US4656239A) outlines a multi-stage process beginning with charging phenol into a reactor equipped with a Dean-Stark trap for azeotropic water removal . Formaldehyde (35–60% aqueous solution) is gradually introduced under alkaline catalysis, with sodium hydroxide (NaOH) or potassium hydroxide (KOH) concentrations ranging from 0.2 to 0.36 moles per mole of phenol . For instance, Example I details the addition of 1955 g of 51.4% formaldehyde to 1504 g phenol over 4 hours at 85°C under vacuum, achieving a bubble viscosity of 60 seconds before acid quenching with formic acid .
Key steps include:
-
Azeotropic Dehydration : Xylene co-solvents facilitate continuous water removal via reflux, maintaining reaction temperatures between 80–90°C .
-
Vacuum Distillation : Post-formaldehyde addition, vacuum dehydration (26–28" Hg) elevates resin solids content to >90%, yielding brittle, grindable resins with melt points of 70–79°C .
-
Catalyst Neutralization : Acidic quenchers like formic acid terminate polymerization, stabilizing resin viscosity.
Catalytic Systems and Reaction Mechanisms
Catalysts profoundly influence resin architecture, distinguishing resole (alkaline-catalyzed) and novolac (acid-catalyzed) resins. Alkaline conditions (pH 10–12) favor methylolation, where formaldehyde reacts with phenol’s aromatic ring to form methylol intermediates . Sulfuric acid, in contrast, accelerates condensation, producing linear novolacs requiring hexamethylenetetramine (hexa) curing .
Recent studies demonstrate optimized NaOH-to-phenol molar ratios (1.0–1.4) for lignin-modified resins, where hydroxymethylated alkaline rice straw lignin substitutes 20–50% of petroleum-based phenol . FTIR analyses confirm structural parity between lignin-PF and conventional resins, with lignin’s aliphatic hydroxyls participating in crosslinking .
Reaction Parameter Optimization
Molar Ratios
Stoichiometric control is critical: a phenol/formaldehyde molar ratio of 1:1.5 balances cost and performance, yielding resins with 44.02% solids content and infinite water dilutability . Excess phenol (1:1.2) enhances thermal stability but raises production costs by 15–20% .
Temperature and Time
Reaction temperatures between 70–100°C inversely affect bulk density (1.18–1.05 g/cm³) but improve Shore D hardness (75–92) due to accelerated crosslinking . Prolonged formaldehyde addition (3–4.5 hours) reduces gelation risks, as evidenced by a 6-hour kettle cycle producing 2125 g resin with 18–19 sec gel time at 166°C .
Advanced Modifications and Composite Integration
Lignin Substitution
Hydroxymethylated lignin incorporation (20–50 wt%) reduces free formaldehyde emissions by 30–40% while maintaining adhesive strength (>2.5 MPa) . Optimal formulations use 1.8–2.6 formaldehyde-to-lignin molar ratios, achieving viscosities of 300–500 cP suitable for plywood bonding .
Nanocomposite Reinforcement
Nanofillers like reactive rubber nanoparticles (RRNP) and Cloisite 30B clay enhance PF matrices, increasing tensile strength by 40% (248 MPa) and thermal stability by 10–20% . Nanoindentation tests reveal interfacial adhesion improvements, with lignin nanoparticles (LNP) dispersing uniformly versus microparticles (LMP) .
Analytical Characterization Techniques
FTIR spectra of lignin-PF resins show retained phenolic C-O-C (1240 cm⁻¹) and methylene bridges (1470 cm⁻¹), confirming successful co-polymerization .
Industrial Scalability and Economic Considerations
Batch processes dominate due to easier parameter control, with cycle times of 5.5–6 hours yielding 1965–2125 g resin per 4L reactor . Xylene recycling from distillates reduces solvent costs by 25%, while lignin substitution lowers phenol consumption by 20–50% . Economic models suggest a 15% cost reduction for lignin-PF adhesives without sacrificing bond strength .
化学反应分析
Phenol-formaldehyde resins undergo various chemical reactions, including:
Condensation Reactions: Phenol reacts with formaldehyde at the ortho and para sites, forming hydroxymethyl phenol.
Oxidation and Reduction: These reactions are less common but can occur under specific conditions, altering the resin’s properties.
Substitution Reactions: Phenolic hydroxyl groups can undergo substitution reactions, introducing new functional groups to modify the resin’s properties.
Common reagents include sulfuric acid, oxalic acid, hydrochloric acid, and various base catalysts. Major products include bisphenol F and higher phenol oligomers .
科学研究应用
Wood Industry
PF resin is predominantly used as an adhesive in the production of wood-based panels such as plywood, particleboard, and medium-density fiberboard (MDF). It provides strong bonding that is resistant to moisture and insects, making it ideal for furniture, cabinetry, and flooring products.
Application | Material Type | Properties Enhanced |
---|---|---|
Plywood | Laminated wood panels | Water resistance, durability |
Particleboard | Engineered wood products | Strength, moisture resistance |
Medium-Density Fiberboard | Furniture components | Stability, durability |
Automotive Industry
In the automotive sector, PF resin is utilized in manufacturing components such as brake pads, fuel pumps, and transmission parts. Its high thermal stability and strength make it suitable for high-performance applications.
Application | Component Type | Properties Enhanced |
---|---|---|
Brake Pads | Friction materials | Heat resistance, durability |
Fuel Pumps | Engine components | Chemical resistance |
Transmission Parts | Mechanical components | Structural integrity |
Electrical Insulation
PF resin is extensively used in the production of electrical insulation materials due to its excellent dielectric properties and thermal stability. It is commonly found in circuit boards and electrical equipment.
Application | Product Type | Properties Enhanced |
---|---|---|
Circuit Boards | Printed circuit boards (PCBs) | Electrical insulation |
Electrical Equipment | Insulating components | Thermal stability |
Composite Materials
Recent research has highlighted the use of PF resin in composite materials reinforced with fibers such as glass or natural fibers. These composites exhibit improved mechanical properties and are used in construction and aerospace applications.
- Case Study : A study investigated glass fiber-reinforced PF composites, demonstrating enhanced mechanical properties suitable for structural applications .
Coatings and Paints
PF resin serves as a binder in coatings and paints due to its excellent adhesion properties and chemical resistance. It enhances the durability of coatings used in various environments.
Research Findings
Research has shown that modifying PF resins with additives can significantly improve their performance characteristics:
- Hybrid Composites : Incorporating organic fibers or inorganic fillers into PF resins has been shown to enhance thermal stability and mechanical strength .
- Environmental Considerations : The use of biomass waste in PF composites not only improves performance but also addresses environmental concerns related to waste management .
作用机制
The mechanism of action of phenol-formaldehyde resins involves the formation of a highly crosslinked polymer network through condensation reactions. The hydroxymethyl groups react with free ortho or para sites on the phenol ring, forming methylene or ether bridges. This results in a rigid, thermosetting polymer with high mechanical strength and chemical resistance .
相似化合物的比较
Chemical and Physical Properties of PF Resins
PF resins are synthesized via polycondensation of phenol and formaldehyde under alkaline (resols) or acidic (novolacs) conditions. Key properties include:
- Thermal Stability : Decomposition begins at 300–350°C, with char yields exceeding 50% at 800°C .
- Mechanical Strength : Tensile strength ranges from 40–60 MPa, outperforming many bio-based alternatives .
- Formaldehyde Emissions : Free formaldehyde content in cured PF resins is typically 0.1–0.3%, lower than UF resins but still regulated .
Comparison with Urea-Formaldehyde (UF) Resins
Property | PF Resin | UF Resin |
---|---|---|
Bond Strength (MPa) | 10–15 (wood composites) | 8–12 |
Formaldehyde Emissions | 0.1–0.3% | 0.5–1.2% |
Water Resistance | Excellent | Poor |
Cost (USD/kg) | 1.5–2.5 | 0.8–1.2 |
Thermal Stability (°C) | 300–350 | 150–200 |
UF resins are cost-effective but suffer from high formaldehyde emissions and poor moisture resistance, limiting their use in outdoor applications . PF resins exhibit superior durability, making them ideal for structural composites .
Comparison with Melamine-Formaldehyde (MF) Resins
Property | PF Resin | MF Resin |
---|---|---|
Surface Hardness | High | Very High |
Chemical Resistance | Resists acids, alkalis | Excellent stain resistance |
Cost (USD/kg) | 1.5–2.5 | 3.0–4.0 |
Curing Temperature (°C) | 120–150 | 130–160 |
MF resins offer enhanced surface finish and stain resistance, often used in decorative laminates. However, their high cost and brittleness compared to PF resins restrict broader industrial use .
Comparison with Epoxy Resins
Property | PF Resin | Epoxy Resin |
---|---|---|
Tensile Strength (MPa) | 40–60 | 70–90 |
Curing Time | 2–4 hours | 24–72 hours |
Adhesion to Metals | Moderate | Excellent |
Flame Retardancy | Inherently flame-resistant | Requires additives |
Epoxy resins excel in adhesion and mechanical performance but require prolonged curing and lack inherent flame retardancy. PF resins are preferred in fire-resistant applications .
Bio-Based Modifications of PF Resins
Lignin-PF Resins
- Performance: Substituting 30% phenol with lignin reduces tensile strength by 15% but improves biodegradability .
- Formaldehyde Emissions: Reduced by 20–30% due to lignin’s phenolic structure .
Bio-Oil-PF Resins
- Thermal Stability : Bio-oil modification lowers decomposition onset temperature to 250°C but enhances flexibility .
- Cost : Bio-oil reduces raw material costs by 25% .
Tannin-PF Resins
- Curing Speed: Tannin accelerates curing by 30% through reactive polyphenol groups .
Data Tables and Research Findings
Table 1: Mechanical Properties of Modified PF Resins
Modifier | Tensile Strength (MPa) | Flexural Modulus (GPa) | Reference |
---|---|---|---|
Unmodified PF | 58 ± 3 | 3.2 ± 0.2 | |
20% Lignin-PF | 49 ± 2 | 2.8 ± 0.3 | |
15% Bio-Oil-PF | 45 ± 4 | 2.5 ± 0.2 | |
25% Tannin-PF | 53 ± 3 | 3.0 ± 0.1 |
Table 2: Environmental Impact Comparison
Resin Type | Formaldehyde Emission (%) | Biodegradability | Renewable Content (%) |
---|---|---|---|
PF | 0.1–0.3 | Low | 0 |
Lignin-PF | 0.08–0.2 | Moderate | 30 |
UF | 0.5–1.2 | Low | 0 |
Bio-Oil-PF | 0.2–0.4 | Moderate | 25 |
生物活性
Phenol-formaldehyde resin (PF resin) is a widely used thermosetting polymer known for its excellent adhesive properties, durability, and resistance to heat and chemicals. However, its biological activity raises concerns regarding toxicity, allergenicity, and potential health effects on humans and the environment. This article explores the biological activity of PF resin, focusing on its health impacts, mechanisms of toxicity, and recent research findings.
Overview of this compound
PF resin is created through the polymerization of phenol and formaldehyde, typically in an alkaline environment. It is extensively used in the production of wood-based panels, adhesives, and coatings due to its strong bonding capabilities and thermal stability. Despite its industrial benefits, PF resin poses several health risks that necessitate thorough investigation.
Allergic Reactions and Dermatitis
Epidemiological studies indicate that PF resins can cause contact dermatitis in a subset of individuals. Approximately 1-3% of people with skin diseases show positive reactions to PF resins, suggesting a significant allergenic potential . In a multicenter patch testing study involving 2,504 patients, 27 individuals (1.1%) reacted positively to a specific PF resin variant (PFR-2), highlighting the importance of monitoring allergic responses in occupational settings .
Respiratory Effects
Exposure to PF resin fumes has been associated with chronic airway diseases. A study involving workers in a filter-manufacturing plant revealed that those exposed for over five years exhibited decreased pulmonary function (measured by FEV1.0/FVC ratios) compared to non-exposed individuals . Symptoms such as chronic cough and sputum production were also reported among exposed workers.
Genotoxicity and Reproductive Effects
The genotoxic potential of PF resins remains equivocal. Some studies have reported chromosomal aberrations in workers exposed to PF resins, while others have shown no significant mutagenic effects . Limited data suggest potential reproductive toxicity; for instance, damage to rat spermatocytes has been noted following inhalation exposure .
Mechanisms of Toxicity
PF resin's biological activity can be attributed to several mechanisms:
- Irritation : PF resins are known to irritate the skin, eyes, and mucosal membranes upon contact or inhalation .
- Sensitization : The presence of sensitizing agents within PF resins can lead to allergic reactions upon repeated exposure.
- Volatile Organic Compounds (VOCs) : The release of formaldehyde—a known carcinogen—during the curing process poses additional health risks .
Recent Research Findings
Recent studies have focused on modifying PF resins to enhance their properties while reducing toxicity:
- Bio-Oil Modified Resins : Research indicates that incorporating bio-oil into PF resins can improve their bonding strength and aging resistance while potentially lowering costs . The bio-oil components positively affected the resin's microstructure and performance characteristics.
Modification | Effect on Bonding Strength | Aging Resistance |
---|---|---|
Bio-Oil Addition | Improved | Enhanced |
Phenol Substitution | Reduced | Variable |
- Mannich Bases Resins : A novel approach involved synthesizing PF resins using Mannich bases derived from primary amines. These resins exhibited promising biological activity profiles and could serve as safer alternatives in various applications .
Case Studies
- Plywood Manufacturing Exposure Assessment :
- Long-Term Health Monitoring :
常见问题
Basic Research Questions
Q. How can reaction conditions be optimized to synthesize phenol-formaldehyde resins with tailored thermomechanical properties?
- Methodological Answer : The synthesis of PFR (novolac or resole) depends on the molar ratio of phenol to formaldehyde, catalyst type (acidic for novolac, alkaline for resole), and curing temperature. For novolac resins, a formaldehyde-to-phenol ratio <1 and acidic catalysts (e.g., oxalic acid) yield linear prepolymers. Resoles require a formaldehyde excess (>1.2:1) and alkaline catalysts (e.g., NaOH) to form crosslinked networks. Curing at 120–160°C ensures complete crosslinking. Adjusting these parameters allows control over thermal stability (up to 300°C) and mechanical strength (e.g., flexural modulus ~3–5 GPa) .
Q. What analytical techniques are most effective for characterizing PFR curing behavior?
- Methodological Answer : Pyrolysis-gas chromatography/mass spectrometry (Py-GC/MS) quantifies residual monomers and crosslinking efficiency by analyzing volatile decomposition products. Fourier-transform infrared (FTIR) spectroscopy tracks the disappearance of methylol groups (-CH2OH) and formation of methylene bridges. Differential scanning calorimetry (DSC) measures curing exotherms (e.g., peak at 150–170°C for resoles) to optimize curing schedules .
Q. How does resin viscosity impact penetration in composite materials like wood veneers?
- Methodological Answer : Vacuum impregnation studies show that resin viscosity inversely correlates with weight percent gain (WPG) in substrates. For instance, partly polymerized PFR (WPG = 34.9%) penetrates birch veneer more effectively than industrial-grade PFR (WPG = 26.4%). Lower viscosity resins (e.g., <500 mPa·s) enhance diffusion into porous structures, critical for adhesive bonding in fiberboards .
Advanced Research Questions
Q. How can conflicting data on PFR penetration efficiency in substrates be resolved?
- Methodological Answer : Discrepancies in WPG values (e.g., 6.5–34.9% in Table 1 ) arise from resin dehydration and polymerization degree. Statistical tools like ANOVA identify variance sources (e.g., substrate porosity, resin aging). Controlled experiments with standardized viscosity (e.g., using rheometry) and substrate pretreatment (e.g., sandblasting) reduce variability. Cross-validation with microscopy (SEM) confirms resin distribution homogeneity .
Q. What strategies improve the chemical resistance of PFR-based coatings without compromising adhesion?
- Methodological Answer : Co-modification with epoxy-dianone resins introduces polar functional groups (e.g., hydroxyl, epoxy) that enhance crosslink density. For example, blending 20–30% epoxy resin with PFR increases chemical resistance by 40% (tested via immersion in 10% H2SO4). Adhesion is maintained by optimizing cure cycles (e.g., 145°C for 2 hours) and using primers to strengthen substrate-resin interfaces .
Q. How do microadditives of PFR influence the crystallization kinetics of polymers like low-density polyethylene (LDPE)?
- Methodological Answer : Adding 1–5 wt% PFR to LDPE accelerates crystallization by acting as nucleation sites. X-ray diffraction (XRD) reveals a shift from spherulitic to lamellar structures, increasing tensile strength by 15–20%. Rheological analysis (e.g., oscillation mode tests) shows reduced melt flow index (MFI), indicating enhanced interchain interactions .
Q. What methodologies address the trade-off between thermal stability and processability in PFR composites?
- Methodological Answer : Incorporating vinylpyrrolidone (VP) latex (10–15% by weight) reduces curing temperature to 120°C while maintaining thermal stability (>250°C). Dynamic mechanical analysis (DMA) confirms a 10–15% increase in storage modulus. Processability is further improved using rheological additives (e.g., fumed silica) to control viscosity during application .
属性
InChI |
InChI=1S/C8H6O2/c1-6-4-3-5-7(10-2)8(6)9/h1-5,9H | |
---|---|---|
Source | PubChem | |
URL | https://pubchem.ncbi.nlm.nih.gov | |
Description | Data deposited in or computed by PubChem | |
InChI Key |
KXGFMDJXCMQABM-UHFFFAOYSA-N | |
Source | PubChem | |
URL | https://pubchem.ncbi.nlm.nih.gov | |
Description | Data deposited in or computed by PubChem | |
Canonical SMILES |
[CH]C1=C(C(=CC=C1)O[CH])O | |
Source | PubChem | |
URL | https://pubchem.ncbi.nlm.nih.gov | |
Description | Data deposited in or computed by PubChem | |
Molecular Formula |
C8H6O2 | |
Source | PubChem | |
URL | https://pubchem.ncbi.nlm.nih.gov | |
Description | Data deposited in or computed by PubChem | |
Molecular Weight |
134.13 g/mol | |
Source | PubChem | |
URL | https://pubchem.ncbi.nlm.nih.gov | |
Description | Data deposited in or computed by PubChem | |
CAS No. |
9003-35-4 | |
Record name | Phenol-formaldehyde resin | |
Source | ChemIDplus | |
URL | https://pubchem.ncbi.nlm.nih.gov/substance/?source=chemidplus&sourceid=0009003354 | |
Description | ChemIDplus is a free, web search system that provides access to the structure and nomenclature authority files used for the identification of chemical substances cited in National Library of Medicine (NLM) databases, including the TOXNET system. | |
Retrosynthesis Analysis
AI-Powered Synthesis Planning: Our tool employs the Template_relevance Pistachio, Template_relevance Bkms_metabolic, Template_relevance Pistachio_ringbreaker, Template_relevance Reaxys, Template_relevance Reaxys_biocatalysis model, leveraging a vast database of chemical reactions to predict feasible synthetic routes.
One-Step Synthesis Focus: Specifically designed for one-step synthesis, it provides concise and direct routes for your target compounds, streamlining the synthesis process.
Accurate Predictions: Utilizing the extensive PISTACHIO, BKMS_METABOLIC, PISTACHIO_RINGBREAKER, REAXYS, REAXYS_BIOCATALYSIS database, our tool offers high-accuracy predictions, reflecting the latest in chemical research and data.
Strategy Settings
Precursor scoring | Relevance Heuristic |
---|---|
Min. plausibility | 0.01 |
Model | Template_relevance |
Template Set | Pistachio/Bkms_metabolic/Pistachio_ringbreaker/Reaxys/Reaxys_biocatalysis |
Top-N result to add to graph | 6 |
Feasible Synthetic Routes
体外研究产品的免责声明和信息
请注意,BenchChem 上展示的所有文章和产品信息仅供信息参考。 BenchChem 上可购买的产品专为体外研究设计,这些研究在生物体外进行。体外研究,源自拉丁语 "in glass",涉及在受控实验室环境中使用细胞或组织进行的实验。重要的是要注意,这些产品没有被归类为药物或药品,他们没有得到 FDA 的批准,用于预防、治疗或治愈任何医疗状况、疾病或疾病。我们必须强调,将这些产品以任何形式引入人类或动物的身体都是法律严格禁止的。遵守这些指南对确保研究和实验的法律和道德标准的符合性至关重要。