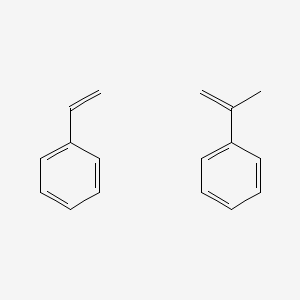
Prop-1-en-2-ylbenzene; styrene
Overview
Description
Prop-1-en-2-ylbenzene (α-methylstyrene, C₉H₁₀, CAS 98-83-9) is a styrene derivative featuring a methyl group at the α-position of the vinyl group. Its structure is characterized by a benzene ring attached to a propene chain with a methyl substituent at the double bond (CC(=C)C₆H₅) . It is widely used in polymer chemistry and organic synthesis due to its steric and electronic effects .
Styrene (vinylbenzene, C₈H₈, CAS 100-42-5) consists of a benzene ring bonded to an ethylene group (C₆H₅CH=CH₂). It is a fundamental monomer for polystyrene production and participates in diverse catalytic reactions, including hydroformylation and polymerization .
Scientific Research Applications
Industrial Applications
1. Production of Polymers and Plastics
Styrene is primarily utilized in the synthesis of various polymers, with approximately 60% of global styrene production converted into polystyrene. This versatile plastic is available in several forms, including solid, foam, and film. Key applications include:
Type of Polymer | Applications |
---|---|
Polystyrene (PS) | Packaging materials, food containers, medical devices, electronics, toys |
Expandable Polystyrene (EPS) | Insulation materials, lightweight protective packaging |
Acrylonitrile Butadiene Styrene (ABS) | Refrigerator liners, automotive parts, toys |
Styrene Acrylonitrile (SAN) | Food containers, optical fibers |
Styrene's ability to be copolymerized with other monomers enhances its utility in creating engineering plastics with tailored properties for specific applications .
2. Synthetic Rubber
Styrene is a key component in the production of synthetic rubber, specifically Styrene Butadiene Rubber (SBR). SBR is widely used in tire manufacturing due to its excellent durability and performance characteristics. It also finds applications in conveyor belts and gaskets .
3. Composite Materials
Styrene is integral in producing fiber-reinforced polymer composites, which are utilized in various sectors such as automotive manufacturing and aerospace. These composites offer high strength-to-weight ratios and corrosion resistance .
Case Studies
Case Study 1: Styrene in Automotive Components
In the automotive industry, styrene-based composites are increasingly used for lightweight components that improve fuel efficiency. For instance, manufacturers have adopted polystyrene for interior parts and structural components due to its strength and cost-effectiveness. A study demonstrated that vehicles utilizing styrenic composites achieved up to a 20% reduction in weight compared to traditional materials .
Case Study 2: Styrene in Medical Devices
Styrene's biocompatibility has led to its application in medical devices such as syringes and IV bags. The clarity and strength of polystyrene make it suitable for these uses. Research indicates that styrenic materials can withstand sterilization processes without compromising their integrity or safety .
Environmental Impact and Safety
While styrene offers numerous benefits, it is essential to consider its environmental impact and potential health risks. Styrene has been classified as a possible human carcinogen based on limited evidence from studies involving occupational exposure. Research indicates an association between styrene exposure and increased risks of certain cancers among workers in the styrene-butadiene rubber industry .
Chemical Reactions Analysis
Polymerization Reactions
Both compounds undergo free-radical polymerization, but their kinetics and outcomes differ due to structural variations.
Styrene Polymerization
-
Mechanism : Free-radical polymerization initiated thermally or via initiators like benzoyl peroxide (BPO) .
-
Kinetics : Follows first-order dependence on monomer concentration and ~0.5-order dependence on initiator .
-
Shear Rate Effects : In spinning disc reactors (SDRs), polymerization rates increase with shear rate (e.g., 76% conversion at 90°C and 6 cm³/s flow rate) .
Parameter | Styrene (100% mass) | Styrene + Ethylbenzene (55% mass) |
---|---|---|
Peak Exotherm (°C) | 205 | 210 |
Heat Release (kJ/mol) | 690 | 520 |
Molecular Weight (Mn) | 120,000–150,000 | 85,000–110,000 |
Data from DSC and GPC analyses .
Prop-1-en-2-ylbenzene Polymerization
-
Limited chain growth due to steric hindrance from the methyl group. Primarily forms dimers or short oligomers under radical conditions .
Thermal Decomposition
High-temperature stability and decomposition pathways differ significantly.
Styrene
-
Products : Generates styryl radicals (50% α-styryl), phenyl + vinyl radicals (25%), and benzene + vinylidene (5%) above 1,660 K .
-
Pressure Dependence : Radical formation dominates at low pressures (0.5–12 atm) .
Prop-1-en-2-ylbenzene
-
Decomposes at higher temperatures (>250°C) via β-scission, yielding cumene and benzene derivatives .
Catalytic Addition Reactions
Both compounds participate in transition-metal-catalyzed transformations.
Anti-Markovnikov Hydroallylation
-
Substrates : Styrene reacts with 1-aryl-2-alkyl alkenes to form internal alkenes (up to 99% yield, >19:1 E/Z) .
-
Example :
Cu-Catalyzed Oxyalkylation
-
Mechanism : Radical pathway confirmed via TEMPO inhibition .
-
Substrate Scope : Prop-1-en-2-ylbenzene reacts with alkyl halides (e.g., 2-bromopropane) to form ethers (76% yield) .
Comparative Analysis
Q & A
Basic Research Questions
Q. How can researchers optimize the synthesis of styrene-derived cyclobutanone oximes for high yields?
- Methodology : Utilize nickel-catalyzed Negishi coupling reactions with aryl zinc reagents, as demonstrated in the preparation of 3-methyl-3-phenylcyclobutan-1-one oxime derivatives. Key steps include controlling reaction stoichiometry, selecting appropriate catalysts (e.g., Ni(COD)₂), and optimizing reaction time/temperature. Purification via column chromatography and validation using spectral data (¹H/¹³C NMR) are critical .
- Data Validation : Compare melting points and spectral signatures with literature values to confirm purity and structural integrity.
Q. What analytical techniques are recommended for characterizing styrene-based intermediates in organic synthesis?
- Approach : Combine NMR spectroscopy (to confirm regioselectivity and stereochemistry) with gas chromatography-mass spectrometry (GC-MS) for volatile derivatives. For crystalline intermediates, employ X-ray crystallography using SHELX software (e.g., SHELXL for refinement) to resolve bond lengths and angles .
- Safety Note : Follow GHS/CLP guidelines (e.g., avoid inhalation of styrene vapors; use fume hoods) during handling .
Advanced Research Questions
Q. How can researchers resolve contradictions in spectroscopic data for styrene-containing polymers or coordination complexes?
- Contradiction Analysis :
- Cross-Validation : Use complementary techniques (e.g., FT-IR for functional groups, XRD for crystallinity) to verify structural assignments.
- Iterative Refinement : Apply SHELXL’s least-squares refinement to adjust thermal parameters and occupancy rates in crystallographic models, addressing outliers in R-factor metrics .
Q. What strategies are effective for studying hydrogen-bonding networks in styrene-based supramolecular assemblies?
- Graph Set Analysis : Use Etter’s formalism to classify hydrogen-bonding motifs (e.g., chains, rings) in crystal structures. SHELXL’s hydrogen-bond restraint tools can model these interactions during refinement .
- Experimental Design : Co-crystallize styrene derivatives with hydrogen-bond donors (e.g., carboxylic acids) and analyze packing motifs via Mercury or Olex2 visualization software .
Q. How should researchers design experiments to probe the mechanistic role of styrene in catalytic cycles (e.g., hydrotrifluoromethylation)?
- Mechanistic Probes :
- Isotopic Labeling : Incorporate deuterated styrene (e.g., C₆D₅-CD=CH₂) to track regioselectivity in radical addition pathways.
- Kinetic Studies : Monitor reaction progress via in situ IR or UV-Vis spectroscopy to identify rate-determining steps.
- Data Interpretation : Compare turnover frequencies (TOF) and Eyring plots under varying temperatures to distinguish between concerted and stepwise mechanisms .
Q. Methodological Guidance
Q. What protocols ensure reproducibility in styrene derivative synthesis for multi-lab collaborations?
- Standardization :
- Document reaction conditions (e.g., solvent purity, inert atmosphere protocols) using IUPAC nomenclature.
- Share raw spectral data (e.g., NMR FID files) and crystallographic CIF files via repositories like Cambridge Structural Database (CSD) .
- Quality Control : Include internal standards (e.g., 1,3,5-trimethoxybenzene for GC-MS) and report yields as averages of triplicate runs ± SD .
Q. How can researchers address challenges in crystallizing styrene-containing compounds for structural studies?
- Crystallization Optimization :
- Screen solvents (e.g., benzene/methanol gradients) using high-throughput platforms.
- Apply SHELXD’s dual-space algorithms for phase problem resolution in twinned or low-resolution datasets .
Q. Data and Safety Compliance
Q. What safety protocols are critical for handling styrene in solvent-intensive reactions?
- Risk Mitigation :
- Use respiratory protection (NIOSH-approved masks) and conduct reactions in well-ventilated hoods per GHS P261/P262 guidelines .
- Monitor airborne styrene levels with real-time sensors (e.g., PID detectors) to ensure compliance with OSHA PELs (100 ppm).
Q. How should researchers archive and validate spectral data for styrene derivatives to meet journal standards?
- Data Archiving :
Comparison with Similar Compounds
Structural and Physical Properties
Property | Prop-1-en-2-ylbenzene | Styrene |
---|---|---|
Molecular Formula | C₉H₁₀ | C₈H₈ |
Molecular Weight (g/mol) | 118.18 | 104.15 |
Substituents | α-methyl | Unsubstituted |
Boiling Point (°C) | 165–167 | 145–146 |
CAS Number | 98-83-9 | 100-42-5 |
Key Synonyms | α-Methylstyrene, 2-Phenylpropene | Vinylbenzene |
The methyl group in Prop-1-en-2-ylbenzene introduces steric hindrance, reducing reactivity in certain catalytic processes compared to styrene .
Reactivity in Catalytic Reactions
Hydroformylation
In rhodium-catalyzed hydroformylation, styrene achieves 96% conversion in 4 hours under 10 bar syngas (CO/H₂ 1:1) with high regioselectivity.
Hydroboration
Lithium diisobutyl-tert-butoxyaluminum hydride (LDBBA)-catalyzed hydroboration of Prop-1-en-2-ylbenzene requires longer reaction times compared to allylbenzene (97% yield) due to steric hindrance from the α-methyl group.
Anti-Markovnikov Hydroallylation
In scandium-catalyzed reactions, Prop-1-en-2-ylbenzene reacts with styrene to yield products (D47–D50) in 63–88% yields with >19:1 E/Z selectivity. Styrene itself participates as a reactant but shows distinct regiochemical outcomes in similar systems .
Hydroamination
Prop-1-en-2-ylbenzene undergoes iodine-catalyzed hydroamination with 5-mercaptotetrazoles to yield aminated products (e.g., 3u) in 51% yield, lower than styrene derivatives due to steric constraints .
Sulfonation Reactions
Prop-1-en-2-ylbenzene reacts with 4-methylbenzenesulfinic acid to form 2-phenyl-1-tosylpropan-2-ol (3rb) in 95% yield, suggesting hydroxylated intermediates unique to α-methyl-substituted styrenes .
Comparison with Other Styrene Derivatives
trans-β-Methylstyrene (CAS 873-66-5)
- Structure: Trans-configuration of the propene chain (C₆H₅CH=CHCH₃).
- Reactivity: Higher steric bulk than styrene but less than Prop-1-en-2-ylbenzene. Used in specialty polymer synthesis .
1-Methyl-4-prop-1-en-2-ylbenzene (CAS 1195-32-0)
- Structure: Para-methyl substitution on the benzene ring (C₆H₄(CH₃)C(CH₂)=CH₂).
- Applications: Intermediate in fragrances and resins, with reactivity modulated by electronic effects .
Properties
CAS No. |
104492-15-1 |
---|---|
Molecular Formula |
C17H18 |
Molecular Weight |
222.32 g/mol |
IUPAC Name |
prop-1-en-2-ylbenzene;styrene |
InChI |
InChI=1S/C9H10.C8H8/c1-8(2)9-6-4-3-5-7-9;1-2-8-6-4-3-5-7-8/h3-7H,1H2,2H3;2-7H,1H2 |
InChI Key |
ZAKVZVDDGSFVRG-UHFFFAOYSA-N |
Canonical SMILES |
CC(=C)C1=CC=CC=C1.C=CC1=CC=CC=C1 |
physical_description |
Dry Powder |
Related CAS |
9011-11-4 68441-37-2 108080-90-6 |
Origin of Product |
United States |
Synthesis routes and methods I
Procedure details
Synthesis routes and methods II
Procedure details
Disclaimer and Information on In-Vitro Research Products
Please be aware that all articles and product information presented on BenchChem are intended solely for informational purposes. The products available for purchase on BenchChem are specifically designed for in-vitro studies, which are conducted outside of living organisms. In-vitro studies, derived from the Latin term "in glass," involve experiments performed in controlled laboratory settings using cells or tissues. It is important to note that these products are not categorized as medicines or drugs, and they have not received approval from the FDA for the prevention, treatment, or cure of any medical condition, ailment, or disease. We must emphasize that any form of bodily introduction of these products into humans or animals is strictly prohibited by law. It is essential to adhere to these guidelines to ensure compliance with legal and ethical standards in research and experimentation.