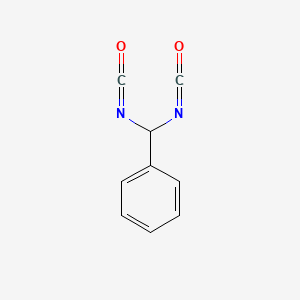
Diisocyanatotoluene
Overview
Description
Diisocyanatotoluene, commonly referred to as toluene diisocyanate (TDI), is an aromatic diisocyanate with two primary isomers: 2,4-diisocyanatotoluene and 2,6-diisocyanatotoluene. Its chemical formula is C₉H₆N₂O₂ (molecular weight: 174.16 g/mol), featuring a toluene backbone substituted with two isocyanate (-NCO) groups at positions 2,4 or 2,6 . TDI is a key precursor in polyurethane production, widely used in flexible foams, adhesives, and coatings due to its high reactivity with polyols . Commercial TDI is often an 80:20 mixture of 2,4- and 2,6-isomers, balancing reactivity and stability .
The compound is highly reactive with water, alcohols, and amines, forming carbamates or urea linkages . However, its volatility and toxicity (e.g., respiratory sensitization) necessitate stringent handling protocols .
Scientific Research Applications
Industrial Applications
1. Polyurethane Production
- Foams : TDI is primarily utilized in the manufacture of flexible and rigid polyurethane foams. These foams are essential in furniture, automotive seats, insulation materials, and packaging.
- Coatings and Adhesives : TDI-based formulations are employed in protective coatings and adhesives due to their excellent adhesion properties and durability. They are used in automotive finishes and construction materials.
2. Medical Applications
- Biocompatible Materials : TDI is being explored for use in medical devices and implants due to its ability to form biocompatible polyurethane elastomers. These materials can be tailored for specific applications such as catheters and wound dressings.
3. Research Applications
- Toxicology Studies : TDI is often used in toxicological research to study its effects on human health, particularly concerning respiratory conditions like asthma. Research has shown that exposure to TDI can lead to airway inflammation and asthma-like symptoms due to its reactivity with biological molecules such as glutathione .
Case Study 1: Occupational Health Impact
A comprehensive study investigated the incidence of asthma among workers exposed to TDI. It was found that long-term exposure led to a significant increase in respiratory symptoms and a higher prevalence of asthma among exposed individuals compared to non-exposed groups . The study highlighted the need for stringent safety measures in workplaces where TDI is used.
Case Study 2: Biocompatibility Testing
Research focusing on TDI-based polyurethanes for medical applications demonstrated their biocompatibility through various in vitro tests. The results indicated that these materials did not elicit significant cytotoxic effects on human cell lines, making them suitable candidates for further development in medical devices .
Summary Table of Applications
Application Area | Specific Use Cases | Key Benefits |
---|---|---|
Polyurethane Production | Flexible foams, rigid foams | Excellent insulation properties |
Coatings and Adhesives | Automotive finishes, construction materials | High durability and adhesion |
Medical Applications | Biocompatible implants, catheters | Tailored properties for specific medical uses |
Toxicology Research | Studies on respiratory effects | Understanding health impacts of exposure |
Q & A
Basic Research Questions
Q. What established methods ensure accurate synthesis and characterization of Diisocyanatotoluene (2,4- and 2,6-TDI) in laboratory settings?
- Methodological Answer : Synthesis typically involves phosgenation of toluene diamines. Characterization requires spectroscopic techniques (e.g., FT-IR for NCO group identification at ~2270 cm⁻¹) and chromatographic methods (HPLC/GC-MS) to confirm purity and isomer ratios. Ensure documentation of reaction conditions (temperature, catalyst) and validation against reference spectra from peer-reviewed studies. Reproducibility hinges on detailed procedural logs, including solvent choices and quenching protocols to prevent side reactions .
Q. What safety protocols are critical when handling this compound in experimental workflows?
- Methodological Answer : Use fume hoods with adequate ventilation, as TDI is a volatile respiratory sensitizer. Personal protective equipment (PPE) must include nitrile gloves, goggles, and vapor-resistant suits. In vivo studies require institutional ethics approvals and protocols to minimize exposure risks, referencing models like the 1997 study on bis(S-glutathionyl) adduct formation in circulatory systems . Storage should adhere to NFPA guidelines, with inert gas purging to prevent moisture-induced polymerization .
Advanced Research Questions
Q. How can researchers resolve contradictions between in vitro and in vivo reactivity data for this compound?
- Methodological Answer : Cross-validate findings using hybrid approaches. For instance, in vitro hydrolysis rates may conflict with in vivo detoxification pathways due to protein binding. Employ isotopic labeling (e.g., ¹⁴C-TDI) to track metabolite distribution in animal models. Pair LC-MS/MS data with computational models (QSAR) to reconcile kinetic discrepancies. Critical analysis of solvent systems (aqueous vs. lipid matrices) in vitro is essential to mimic physiological conditions .
Q. What frameworks optimize hypothesis-driven studies on this compound’s toxicological mechanisms?
- Methodological Answer : Apply the PICOT framework to structure questions:
- P (Population): Human bronchial epithelial cells or murine models.
- I (Intervention): Subchronic TDI exposure at 0.1–10 ppm.
- C (Comparison): Controls with urea derivatives or non-isocyanate analogs.
- O (Outcome): Biomarkers (e.g., glutathione depletion, IL-6 elevation).
- T (Time): Acute (24–72 hr) vs. chronic (4-week) exposure.
The FINER criteria (Feasible, Interesting, Novel, Ethical, Relevant) ensure alignment with toxicology research gaps, such as long-term immunotoxicity .
Q. How should experimental procedures be documented to ensure reproducibility in this compound studies?
- Methodological Answer : Follow guidelines from the Beilstein Journal of Organic Chemistry:
- Data Tables : Include isomer-specific reactivity data (e.g., % conversion, byproduct profiles) with error margins (±SEM). Use Word tables with footnotes explaining outliers .
- Supporting Information : Provide raw NMR spectra, HPLC chromatograms, and kinetic plots in public repositories (e.g., Zenodo). For animal studies, detail euthanasia protocols and histopathology scoring systems .
Methodological and Analytical Questions
Q. What statistical approaches are recommended for analyzing dose-response relationships in this compound exposure studies?
- Methodological Answer : Use nonlinear regression (e.g., Hill equation) to model EC₅₀ values for airway inflammation. For skewed datasets (common in low-dose studies), apply non-parametric tests (Mann-Whitney U) and bootstrap resampling. Report confidence intervals (95% CI) and adjust for multiple comparisons (Bonferroni correction) in omics datasets .
Q. How can researchers design robust controls to distinguish this compound-specific effects from background noise in cellular assays?
- Methodological Answer : Include three control tiers:
- Negative Controls : Solvent-only (e.g., DMSO ≤0.1%).
- Isomer Controls : 2,4-TDI vs. 2,6-TDI to isolate isomer-specific effects.
- Competitive Inhibitors : Co-treatment with N-acetylcysteine to confirm thiol-mediated adduction pathways. Normalize data to housekeeping genes (e.g., GAPDH) in qPCR assays .
Q. Data Interpretation and Reporting
Q. What strategies mitigate bias when interpreting conflicting data on this compound’s environmental persistence?
- Methodological Answer : Conduct systematic reviews using PRISMA guidelines to aggregate hydrolysis half-life data across pH levels (4–9). Perform meta-regression to identify confounding variables (e.g., humic acid presence). Transparently report funding sources and analytical instrument calibration logs to address potential conflicts .
Q. How should researchers structure discussions on Diisocyanatoluene’s dual role as an industrial reagent and immunogen?
- Methodological Answer : Use a Dual-Perspective Framework :
Comparison with Similar Compounds
Comparison with Structurally Similar Compounds
Hexamethylene Diisocyanate (HDI)
Chemical Structure : HDI (1,6-diisocyanatohexane) is an aliphatic diisocyanate with the formula C₈H₁₂N₂O₂ (molecular weight: 168.19 g/mol). Its linear hexane chain contrasts with TDI’s aromatic ring .
Reactivity :
- HDI reacts slower with polyols than TDI due to its aliphatic nature, making it suitable for UV-stable coatings.
- Applications: Primarily used in automotive coatings, weather-resistant paints, and elastomers . Safety: Lower volatility than TDI but still classified as a respiratory irritant .
Methylenediphenyl Diisocyanate (MDI)
Chemical Structure : MDI (4,4’-diisocyanatodicyclohexylmethane) is a larger aromatic diisocyanate with the formula C₁₅H₁₀N₂O₂ (molecular weight: 250.27 g/mol). It features two benzene rings linked by a methylene group .
Reactivity :
- MDI’s lower volatility and slower reaction kinetics compared to TDI make it ideal for rigid foams and thermoset plastics.
- Forms stronger cross-linking networks due to its symmetrical structure .
Applications : Dominates insulation materials, automotive parts, and construction foams .
Safety : Less volatile than TDI but poses similar long-term health risks, including asthma .
Isophorone Diisocyanate (IPDI)
Chemical Structure : IPDI (3-isocyanatomethyl-3,5,5-trimethylcyclohexyl isocyanate) is a cycloaliphatic diisocyanate with the formula C₁₂H₁₈N₂O₂ (molecular weight: 222.29 g/mol). Its bicyclic structure enhances steric hindrance .
Reactivity :
- Combines aliphatic stability with moderate reactivity, suitable for light-stable coatings.
- Less reactive than TDI but more so than HDI .
Applications : Used in high-performance coatings, adhesives, and elastomers .
Safety : Lower toxicity profile compared to aromatic diisocyanates .
Comparison with Functionally Similar Compounds
TDI Isomers (2,4- vs. 2,6-Diisocyanatotoluene)
Structural Differences :
- 2,4-TDI : Asymmetric structure increases reactivity; dominant isomer in commercial mixtures (80%) .
- 2,6-TDI : Symmetric structure reduces steric hindrance, leading to slower polymerization .
Reactivity : - 2,4-TDI reacts 3–4 times faster with nucleophiles (e.g., glutathione) than 2,6-TDI, influencing toxicity profiles .
Applications : Blended to optimize foam flexibility and curing times .
Data Table: Key Properties of Diisocyanatotoluene and Comparable Compounds
Property | 2,4-TDI | HDI | MDI | IPDI |
---|---|---|---|---|
Molecular Weight | 174.16 g/mol | 168.19 g/mol | 250.27 g/mol | 222.29 g/mol |
Structure | Aromatic | Aliphatic | Aromatic | Cycloaliphatic |
Volatility | High | Moderate | Low | Low |
Reactivity | Very High | Moderate | High | Moderate-High |
Primary Applications | Flexible Foams | Coatings | Rigid Foams | Elastomers |
Toxicity | Respiratory | Irritant | Carcinogen Risk | Low Irritancy |
References |
Preparation Methods
Traditional Three-Step Synthesis of Toluene Diisocyanate
The conventional production of TDI involves three sequential stages: nitration of toluene to dinitrotoluene (DNT), hydrogenation of DNT to toluenediamine (TDA), and phosgenation of TDA to TDI. Each step requires precise control of reaction conditions to optimize yield and purity.
Nitration of Toluene to Dinitrotoluene
Toluene undergoes nitration using a mixed acid (HNO₃ and H₂SO₄) to produce mononitrotoluene (MNT) isomers, followed by a second nitration to yield dinitrotoluene (DNT). The methyl group in toluene activates the aromatic ring, enabling nitration under milder conditions compared to benzene. A typical nitrating acid contains 23% water, achieving a mixture of 63% ortho-, 33–34% para-, and 4% meta-nitrotoluene isomers . Subsequent nitration of the o- and p-MNT isomers produces 2,4-DNT and 2,6-DNT in an approximate 80:20 ratio, which serves as the feedstock for TDA synthesis .
Hydrogenation of Dinitrotoluene to Toluenenediamine
Catalytic hydrogenation of DNT to TDA employs palladium or nickel catalysts in a solvent such as methanol or ethanol. The reaction occurs at 50–150°C under hydrogen pressures of 10–30 bar, achieving near-quantitative conversion . The resulting TDA mixture, predominantly 2,4-TDA and 2,6-TDA, is purified via vacuum distillation to remove residual solvents and byproducts. This step is critical, as impurities can deactivate catalysts in subsequent phosgenation .
Phosgenation of Toluenenediamine to TDI
Phosgenation, the final and most hazardous step, involves reacting TDA with phosgene (COCl₂) in an inert solvent like o-dichlorobenzene. The process occurs in two stages:
-
Cold phosgenation : TDA reacts with phosgene at 0–40°C to form intermediate carbamoyl chlorides.
-
Thermal phosgenation : Heating to 170–185°C cleaves carbamoyl chlorides into TDI and hydrogen chloride (HCl) .
Excess phosgene and HCl are separated via fractional distillation, with phosgene recycled to minimize waste. The crude TDI is further purified to achieve commercial grades (80:20 or 65:35 2,4-:2,6-TDI ratios) .
Modern Process Innovations: Distillation and Residue Hydrolysis
Industrial advancements focus on optimizing yield and reducing waste, particularly in managing distillation residues.
Distillation and Residue Composition
Crude TDI from phosgenation contains 2–10% solvent and high-boiling residues, including oligomers and unreacted intermediates . Distillation under vacuum (10–50 mbar) separates purified TDI (99.5% purity) from residues, which constitute 5–15% of the total output . These residues pose disposal challenges due to their reactivity and toxicity.
Hydrolysis of Distillation Residues
The patent US8063241B2 introduces a hydrolysis process to recover TDA from residues. Key steps include:
-
Continuous mixing of residue with water at <230°C and <30 bar in tubular reactors.
-
Reaction mechanism : Hydrolysis cleaves carbamoyl chlorides and urea derivatives, regenerating TDA.
-
TDA recovery : The hydrolyzed mixture is dewatered and distilled under vacuum (≤80 mbar), yielding 70–90% pure TDA, which is recycled into phosgenation .
This method reduces waste by 40–60% and improves overall TDI yield by 5–8%, addressing economic and environmental concerns .
Process Optimization and Simulation Studies
Recent computational studies aim to enhance phosgenation efficiency. A 2023 AIChE Journal article models a thermally coupled reactive distillation column (TCRDC) for TDI synthesis. Key findings include:
Parameter | Traditional Reactor | TCRDC |
---|---|---|
Energy Consumption (kW) | 1,250 | 980 |
TDI Purity (%) | 99.5 | 99.8 |
Phosgene Utilization | 85% | 92% |
The TCRDC integrates reaction and separation, reducing energy use by 22% and improving phosgene utilization through real-time byproduct removal .
Properties
Molecular Formula |
C9H6N2O2 |
---|---|
Molecular Weight |
174.16 g/mol |
IUPAC Name |
diisocyanatomethylbenzene |
InChI |
InChI=1S/C9H6N2O2/c12-6-10-9(11-7-13)8-4-2-1-3-5-8/h1-5,9H |
InChI Key |
JXCHMDATRWUOAP-UHFFFAOYSA-N |
SMILES |
C1=CC=C(C=C1)C(N=C=O)N=C=O |
Canonical SMILES |
C1=CC=C(C=C1)C(N=C=O)N=C=O |
Origin of Product |
United States |
Synthesis routes and methods I
Procedure details
Synthesis routes and methods II
Procedure details
Synthesis routes and methods III
Procedure details
Retrosynthesis Analysis
AI-Powered Synthesis Planning: Our tool employs the Template_relevance Pistachio, Template_relevance Bkms_metabolic, Template_relevance Pistachio_ringbreaker, Template_relevance Reaxys, Template_relevance Reaxys_biocatalysis model, leveraging a vast database of chemical reactions to predict feasible synthetic routes.
One-Step Synthesis Focus: Specifically designed for one-step synthesis, it provides concise and direct routes for your target compounds, streamlining the synthesis process.
Accurate Predictions: Utilizing the extensive PISTACHIO, BKMS_METABOLIC, PISTACHIO_RINGBREAKER, REAXYS, REAXYS_BIOCATALYSIS database, our tool offers high-accuracy predictions, reflecting the latest in chemical research and data.
Strategy Settings
Precursor scoring | Relevance Heuristic |
---|---|
Min. plausibility | 0.01 |
Model | Template_relevance |
Template Set | Pistachio/Bkms_metabolic/Pistachio_ringbreaker/Reaxys/Reaxys_biocatalysis |
Top-N result to add to graph | 6 |
Feasible Synthetic Routes
Disclaimer and Information on In-Vitro Research Products
Please be aware that all articles and product information presented on BenchChem are intended solely for informational purposes. The products available for purchase on BenchChem are specifically designed for in-vitro studies, which are conducted outside of living organisms. In-vitro studies, derived from the Latin term "in glass," involve experiments performed in controlled laboratory settings using cells or tissues. It is important to note that these products are not categorized as medicines or drugs, and they have not received approval from the FDA for the prevention, treatment, or cure of any medical condition, ailment, or disease. We must emphasize that any form of bodily introduction of these products into humans or animals is strictly prohibited by law. It is essential to adhere to these guidelines to ensure compliance with legal and ethical standards in research and experimentation.