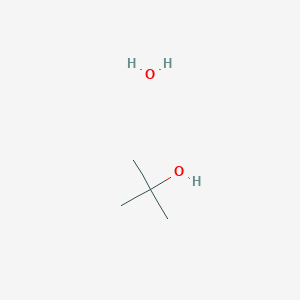
Water tert-butyl alcohol
- Click on QUICK INQUIRY to receive a quote from our team of experts.
- With the quality product at a COMPETITIVE price, you can focus more on your research.
Overview
Description
tert-Butyl alcohol (TBA), also known as 2-methyl-2-propanol (C₄H₁₀O), is a branched-chain tertiary alcohol with a hydroxyl group attached to a carbon atom bonded to three methyl groups. Its unique structure imparts distinct physical and chemical properties, such as high water solubility (miscible in all proportions) , a boiling point of 82°C , and low viscosity. In aqueous solutions, TBA interacts with water through hydrogen bonding, but its bulky tert-butyl group disrupts water’s hydrogen-bond network more significantly than smaller alcohols like ethanol .
TBA is widely used as a solvent, fuel additive, and intermediate in organic synthesis (e.g., production of tert-butyl chloride) . It is also a key degradation product of fuel oxygenates like methyl tert-butyl ether (MTBE) and ethyl tert-butyl ether (ETBE) .
Scientific Research Applications
Pharmaceutical Applications
Lyophilization Process Optimization
Tert-butyl alcohol is increasingly utilized in the pharmaceutical industry, particularly in the lyophilization (freeze-drying) of sensitive compounds. A study demonstrated that using a water-tert-butyl alcohol cosolvent system can enhance the solubility of hydrophobic drugs and improve product stability during the drying process. The phase diagram of the water-tert-butyl alcohol system reveals critical eutectic points that facilitate optimal drying conditions, thus reducing drying time and improving reconstitution characteristics of lyophilized products .
Case Study: Tobramycin Sulfate Production
In a specific case study, a formulation involving tert-butyl alcohol was used to produce freeze-dried tobramycin sulfate. The research highlighted that careful manipulation of TBA concentrations led to a desirable powder consistency that could be easily poured from vials, emphasizing the importance of maintaining low residual levels of TBA during processing .
Environmental Applications
Air Filter Components
Recent studies have explored the use of water-tert-butyl alcohol mixtures in creating high-performance air filter components. The incorporation of these mixtures into aerogel structures has shown promise in enhancing the efficiency of high-efficiency particulate air (HEPA) filters by improving their ability to capture airborne microorganisms .
Industrial Applications
Solvent and Chemical Intermediate
Tert-butyl alcohol serves as an important solvent in various industrial applications, including paint formulations and as a denaturant for ethanol. Its ability to dissolve both polar and non-polar substances makes it valuable for producing high-quality paints and coatings . Additionally, TBA is a key intermediate in synthesizing other chemicals such as methyl tert-butyl ether (MTBE) and ethyl tert-butyl ether (ETBE), which are used as fuel additives to enhance octane ratings and reduce emissions .
Toxicological Studies and Safety Considerations
Health Effects Assessment
Toxicological assessments have been conducted to evaluate the safety profile of tert-butyl alcohol. Studies indicate potential renal toxicity following prolonged exposure; however, it has not shown significant mutagenic effects in various in vitro tests . Understanding these health implications is crucial for industries utilizing TBA to ensure safe handling practices.
Data Table: Summary of Applications
Application Area | Specific Use Cases | Benefits |
---|---|---|
Pharmaceuticals | Lyophilization of drugs | Increased solubility, reduced drying time |
Environmental Science | Air filter components | Enhanced microorganism capture |
Industrial Processes | Solvent for paints, ethanol denaturant | High-quality formulations |
Chemical Manufacturing | Intermediate for MTBE and ETBE production | Improved fuel properties |
Q & A
Basic Research Questions
Q. What standardized protocols are recommended for assessing tBA toxicity in animal models?
- The U.S. EPA outlines rigorous protocols for tBA toxicity studies, including OECD Good Laboratory Practice (GLP) compliance, controlled dosing (e.g., oral, inhalation), and systematic histopathological evaluations . Key parameters include sample size calculations (to ensure statistical power), longitudinal monitoring of organ-specific effects (e.g., liver/kidney function), and inclusion of control groups to isolate confounding variables .
Q. How can researchers validate analytical methods for tBA quantification in aqueous environments?
- Method validation should follow ISO/IEC 17025 guidelines, incorporating:
- Linearity tests (e.g., calibration curves across 0.1–100 µg/L).
- Recovery studies using deuterated internal standards (e.g., d9-tBA) to correct for matrix effects .
- Cross-validation with gas chromatography (GC) paired with mass spectrometry (MS) or infrared spectroscopy (IR) to confirm specificity .
Q. What environmental partitioning models predict tBA distribution in water systems?
- Level I fugacity models (e.g., EQC Model) estimate tBA partitioning, with ~72.5% in water and 27.4% in air due to its polarity (log Kow = 0.37) and volatility (vapor pressure = 44 mmHg at 26°C) . These models require input parameters like Henry’s law constant (3.2 × 10⁻⁶ atm·m³/mol) and biodegradation half-life (aerobic: 10–28 days) .
Advanced Research Questions
Q. How can competing reaction pathways in tBA-mediated catalytic processes be resolved?
- In glycerol etherification, tBA dehydration generates isobutene and di-isobutene byproducts, competing with desired glycerol-tBA adducts . To mitigate this:
- Optimize acid site density (via NH₃-TPD) on zeolite catalysts to favor glycerol adsorption.
- Adjust molar ratios (tBA:glycerol ≥ 4:1) to suppress tBA self-dehydration .
- Use kinetic modeling (e.g., Langmuir-Hinshelwood) to identify rate-limiting steps .
Q. What advanced spectroscopic techniques quantify tBA hydration dynamics in aqueous solutions?
- Terahertz time-domain spectroscopy (THz-TDS) measures absorption coefficients (0.3–1.0 THz) to calculate hydration numbers via the packing density model. For tBA, hydration numbers correlate with concentration-dependent dielectric relaxation, validated against MD simulations .
Q. How do solvent-protein interactions in tBA affect biocatalytic activity?
- tBA’s high viscosity (3.3 cP at 20°C) prolongs enzyme (e.g., CALB lipase) residence times by 30–50% compared to acetone. Water activity (aw) modulates these interactions: at aw < 0.3, tBA forms nonpolar clusters that destabilize protein helices, reducing activity by ~40% .
Q. What strategies address contradictions in tBA’s neurotoxicological data across studies?
- Discrepancies in neurobehavioral outcomes (e.g., memory deficits vs. no effect) may arise from:
- Dose-response variability : Threshold effects observed at ≥400 mg/kg/day in rats .
- Exposure duration : Subchronic vs. chronic (2-year) studies show divergent blood-brain barrier permeability .
- Systematic reviews should apply Hill’s criteria (e.g., consistency, biological plausibility) and meta-regression to isolate confounding factors .
Q. Methodological Guidance
Designing reproducible tBA oxidation experiments for peroxide synthesis
- Catalyst optimization : 12-phosphotungstic acid (0.5 wt%) at 83°C achieves >95% tBA conversion. Key factors:
- Molar ratio : tBA:H₂O₂ = 0.7:1 to minimize H₂O₂ excess.
- Orthogonal testing : Use Taguchi arrays to rank factors (temperature > catalyst mass > time) .
Evaluating tBA’s role in MTBE biodegradation pathways
- Isotopic fractionation : Compound-specific isotope analysis (CSIA) of δ¹³C in MTBE and tBA tracks anaerobic degradation. Enrichment factors (ε) of −2.05‰ for MTBE → tBA indicate rate-limiting C-O bond cleavage .
Best practices for synthesizing tBA derivatives (e.g., t-butyl chloride)
- SN1 mechanism : Concentrated HCl (12M) reacts with tBA at 0–5°C to minimize carbocation rearrangement. Yield optimization (53–58%) requires stoichiometric excess (5:1 HCl:tBA) and rapid quenching to prevent hydrolysis .
Comparison with Similar Compounds
Comparison with Structurally Similar Alcohols
2.1. Physical and Chemical Properties
Table 1 compares TBA with other butanol isomers and ethanol:
Property | tert-Butyl Alcohol (TBA) | n-Butyl Alcohol | Isobutyl Alcohol | sec-Butyl Alcohol | Ethanol |
---|---|---|---|---|---|
Boiling Point (°C) | 82 | 118 | 108 | 100 | 78 |
Water Solubility (g/100g) | Miscible | 8 | 10 | 12.5 | Miscible |
Log Kow | 0.35 | 0.88 | 0.76 | 0.61 | -0.31 |
Dipole Moment (D) | 1.5 | 1.7 | 1.6 | 1.6 | 1.7 |
Key Findings :
- TBA’s high water solubility and low boiling point stem from its steric hindrance, which limits hydrophobic interactions and reduces intermolecular forces .
- Unlike ethanol, TBA weakens adjacent water molecules’ O-H bonds (red shift in vibrational frequency) due to its bulky tert-butyl group, which disrupts hydrogen-bond networks .
2.2. Environmental Behavior
TBA shares environmental mobility with MTBE and ETBE due to high water solubility but differs in degradation pathways:
- MTBE/ETBE : Undergo microbial oxidation to TBA, which accumulates in groundwater due to slower degradation .
- TBA : Persistent in anaerobic conditions but degrades aerobically via bacteria like Aquincola tertiaricarbonis .
- Sorption : TBA has lower soil adsorption (Kd = 0.2–1.5 L/kg) compared to MTBE (Kd = 0.5–3.0 L/kg), making it more mobile in aquifers .
Environmental Impact :
- TBA contamination (>1 ppm) is linked to fuel spills and industrial waste, with cases documented in North Dakota and Ohio .
- Unlike MTBE, TBA lacks a distinct odor, complicating detection in drinking water .
Comparison with Protein-Stabilizing Compounds
3.1. Trimethylamine N-Oxide (TMAO) vs. TBA
TMAO (a protein stabilizer) and TBA (a denaturant) exhibit opposite effects on water structure:
Property | TMAO | TBA |
---|---|---|
Water Capture Lifetime | 31.2 ps (N⁺O⁻ group) | 16.5 ps (OH group) |
Dipole Moment Shift | +12% (near N⁺O⁻) | +5% (near OH) |
Hydrophobic Interaction | Enhances water polarization near CH₃ groups | Reduces polarization near CH₃ groups |
Mechanistic Insight :
- TMAO stabilizes proteins by forming strong, long-lived hydrogen bonds with water, while TBA disrupts water’s hydrogen-bond network, promoting protein denaturation .
4.1. Solvent Efficiency
- Freeze-Drying : TBA-water mixtures accelerate sublimation rates in pharmaceuticals by lowering solution viscosity and enhancing solvent mobility .
- Nanoparticle Synthesis: TBA outperforms ethanol in producing sub-100 nm zeolitic imidazolate frameworks (ZIFs) due to its lower cytotoxicity and higher miscibility with polymers .
Preparation Methods
Catalytic Hydration of Isobutylene
The direct hydration of isobutylene to TBA is a reversible reaction (C4H8+H2O⇌C4H9OH) governed by equilibrium constraints. Industrial processes optimize conversion by employing acidic catalysts and precise control over reaction conditions.
Homogeneous Acid Catalysis
Early methods utilized mineral acids like sulfuric acid (H2SO4) to protonate isobutylene, forming a carbocation intermediate that reacts with water. While effective, this approach generates corrosive waste and requires neutralization steps . Modern variants replace H2SO4 with organic acids (e.g., acetic acid) to reduce byproduct formation. For instance, a homogeneous mixture of water, TBA, and isobutylene in acetic acid achieves 70% conversion at 50°C using a sulfonic acid-type ion-exchange resin .
Heterogeneous Ion-Exchange Resin Catalysts
Solid acid catalysts, particularly sulfonated polystyrene-divinylbenzene resins, dominate industrial TBA production due to their reusability and minimal corrosion. Key advancements include:
-
Multi-Stage Reactor Systems : WO 99/33775 (cited in ) describes a series of fixed-bed reactors operating below 65°C, with intermediate product recycling to enhance conversion. A circulation rate (recycled:feed ratio) of 1.8–10 and TBA concentration of 0.5–3.5 wt% at the reactor inlet maximizes efficiency .
-
Composition Optimization : US4307257A defines optimal ternary compositions (TBA-water-hydrocarbon) within a triangular diagram (Table 1), ensuring a homogeneous liquid phase and avoiding equilibrium limitations. For example, a mixture containing 55.3% TBA, 31.0% water, and 13.7% hydrocarbons achieves 90% selectivity .
Table 1: Optimal Composition Ranges for TBA Synthesis (US4307257A )
Component | Range (wt%) |
---|---|
tert-Butyl alcohol | 9.8–78.0 |
Water | 0.3–31.0 |
Hydrocarbons | 13.7–80.0 |
Continuous Production and Process Intensification
Countercurrent Flow Reactors
EP1431264A1 discloses a countercurrent reactor design where the hydrocarbon feed flows upward against a descending aqueous-catalyst phase. This configuration maintains a steady-state concentration gradient, achieving 85% conversion with a two-phase discharge (organic TBA-rich phase and aqueous catalyst phase). The catalyst phase, after water replenishment, is recycled, reducing waste .
Integrated Distillation-Hydrolysis Systems
US4011272A outlines a continuous process combining reaction, distillation, and ester hydrolysis:
-
Reaction : Isobutylene reacts with aqueous acetic acid at 50–80°C over ion-exchange resins, yielding TBA and tert-butyl acetate.
-
Distillation : Unreacted hydrocarbons are removed, and the residue is separated into TBA-ester mixtures and aqueous acid.
-
Hydrolysis : Esters are hydrolyzed back to TBA using additional resin catalysts, with the aqueous acid recycled .
Purification and Drying Techniques
Crude TBA requires rigorous purification to meet industrial standards:
-
Drying Agents : Calcium oxide (CaO), magnesium sulfate (MgSO4), and molecular sieves (type 4A) effectively remove residual water .
-
Azeotropic Distillation : Benzene forms a low-boiling azeotrope (67.3°C) with water, enabling efficient dehydration .
-
Crystallization : Partial freezing isolates high-purity TBA, though moisture exclusion is critical to prevent hydrate formation .
Thermodynamic and Kinetic Insights
The dehydration of TBA to isobutylene (ΔH=26kJ mol−1) underscores the importance of low-temperature hydration to favor the reverse reaction . Kinetic studies using ion-exchange resins reveal a Langmuir-Hinshelwood mechanism, where water and TBA adsorb competitively on acid sites. The activation energy for hydration is 18 kJ mol−1, with optimal rates observed at 60–90°C .
Industrial Case Studies
Multi-Stage Reactor Optimization
A plant employing US4307257A’s methodology operates at 60°C with a sulfonic acid resin, achieving 92% isobutylene conversion per pass. The reaction mixture is distilled to recover TBA (99.5% purity), while unreacted hydrocarbons are recycled .
Environmental and Economic Considerations
Modern processes prioritize catalyst longevity and waste minimization. For example, EP1431264A1’s catalyst recycling reduces annual resin replacement costs by 40% compared to single-use systems .
Properties
CAS No. |
75179-55-4 |
---|---|
Molecular Formula |
C4H12O2 |
Molecular Weight |
92.14 g/mol |
IUPAC Name |
2-methylpropan-2-ol;hydrate |
InChI |
InChI=1S/C4H10O.H2O/c1-4(2,3)5;/h5H,1-3H3;1H2 |
InChI Key |
ZQXSFZAMFNRZOQ-UHFFFAOYSA-N |
Canonical SMILES |
CC(C)(C)O.O |
Origin of Product |
United States |
Disclaimer and Information on In-Vitro Research Products
Please be aware that all articles and product information presented on BenchChem are intended solely for informational purposes. The products available for purchase on BenchChem are specifically designed for in-vitro studies, which are conducted outside of living organisms. In-vitro studies, derived from the Latin term "in glass," involve experiments performed in controlled laboratory settings using cells or tissues. It is important to note that these products are not categorized as medicines or drugs, and they have not received approval from the FDA for the prevention, treatment, or cure of any medical condition, ailment, or disease. We must emphasize that any form of bodily introduction of these products into humans or animals is strictly prohibited by law. It is essential to adhere to these guidelines to ensure compliance with legal and ethical standards in research and experimentation.