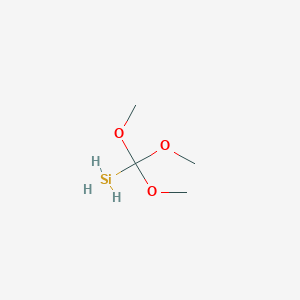
Trimethoxymethyl silane
- Click on QUICK INQUIRY to receive a quote from our team of experts.
- With the quality product at a COMPETITIVE price, you can focus more on your research.
Description
Trimethoxymethyl silane (MTMS), also known as methyltrimethoxysilane, is a silane coupling agent with the chemical formula C₄H₁₂O₃Si and molecular weight 136.22 g/mol . Its structure consists of a central silicon atom bonded to one methyl group (-CH₃) and three methoxy groups (-OCH₃), making it highly reactive in hydrolysis and condensation reactions. MTMS is widely used in sol-gel coatings, adhesion promotion, and corrosion-resistant materials due to its ability to form stable siloxane networks (Si-O-Si) upon hydrolysis .
Key applications include:
- Hybrid silica-based sol-gel coatings for metals and textiles, improving mechanical and chemical stability .
- Surface modification to enhance compatibility between organic polymers and inorganic substrates .
- Electromagnetic interference (EMI) shielding in copper-coated materials via protective silane layers .
Q & A
Basic Questions
Q. How can researchers verify the chemical identity of trimethoxymethyl silane (TMMS)?
To confirm TMMS identity, use spectroscopic techniques (e.g., NMR, FTIR) to detect characteristic functional groups (methoxy and methyl-Si bonds). Cross-reference with standard databases like NIST Chemistry WebBook (CAS 2487-90-3) for molecular weight (122.20 g/mol), IUPAC name, and InChIKey . X-ray photoelectron spectroscopy (XPS) can also validate Si-O-Si bonding in surface-modified materials, as shown by energy peaks at ~103.6–104.3 eV .
Q. What safety protocols are critical when handling TMMS in laboratory settings?
Use NIOSH/EN 166-certified eye/face shields, nitrile gloves, and full-body chemical suits to prevent skin/eye contact. Work under fume hoods with proper ventilation. Avoid incompatible materials (e.g., strong acids/bases) due to potential reactivity . Conduct pre-experiment risk assessments, including toxicity reviews and emergency response plans, as emphasized in Prudent Practices guidelines .
Q. What hydrolysis conditions optimize TMMS for silanization processes?
Adjust the pH of TMMS solutions to ~4.1 using acetic acid to activate hydrolysis. Allow 23 hours at room temperature for complete hydrolysis, as demonstrated in silane primer studies. Ethanol-water mixtures (95:5 v/v) are ideal solvents for stability . Monitor hydrolysis progress via FTIR to track Si-O-C (methoxy) reduction and Si-OH formation .
Q. How does TMMS enhance adhesion in polymer-ceramic composites?
TMMS acts as a coupling agent by forming covalent Si-O bonds with ceramic surfaces (e.g., SiO₂ in glass) and methacrylate groups in polymers. However, studies show that TMMS-containing universal adhesives (UAs) alone may not suffice for dental ceramics; additional silane layers are needed to maximize bond strength .
Advanced Research Questions
Q. How can silane ratio and concentration be optimized for hybrid film formation?
Use a factorial design approach with variables like APTES:TMMS ratio (V1), silane concentration (V2), and hydrolysis time (V3). Statistica software analysis (R² ≥ 0.87) reveals silane concentration (V2) has the strongest effect on contact angle and corrosion resistance. For galvannealed steel, a 2:1 APTES:TMMS ratio and 2% concentration yield optimal hydrophobicity (109.7° contact angle) .
Q. What advanced techniques characterize TMMS-modified surfaces?
- XPS : Identify Si-O-Si bonding at 103.6 eV and Si-C bonding at ~99.2 eV to confirm surface functionalization .
- Cyclic Voltammetry : Evaluate electrochemical stability of TMMS-functionalized materials (e.g., NiSi nanowires) by tracking lithiation/delithiation phases at 0.9–0.15 V (vs. Li/Li+) .
- Contact Angle Goniometry : Quantify wettability changes using response surface methodology to model silane concentration effects .
Q. How does TMMS improve mechanical properties in nanocomposites?
In SiO₂/HDPE composites, TMMS enhances interfacial bonding by reducing stress concentrations. Perform nanoindentation and compression tests to measure Young’s modulus. Numerical simulations (e.g., finite element analysis) correlate treated SiO₂ with 20–30% higher modulus than untreated controls .
Q. What statistical methods resolve contradictions in silane efficacy data?
For conflicting adhesion results (e.g., insufficient silane in UAs), apply ANOVA to isolate variables like hydrolysis time or substrate roughness. Studies show silane layers must exceed 1 µm thickness to prevent bond failure in dental applications . Meta-analyses of XPS and FTIR data can also identify inconsistencies in surface coverage .
Q. How does TMMS influence solid electrolyte interphase (SEI) formation in batteries?
In silicon nanowire anodes, TMMS-functionalization reduces SEI degradation. Analyze cycling stability via electrochemical impedance spectroscopy (EIS) and observe reduced impedance growth after 37 cycles at 0.4133 mV/s .
Q. What experimental designs mitigate hazards in TMMS synthesis?
Use design of experiments (DoE) to minimize exposure risks. For example, optimize reaction scales (<100 mL) and substitute pyrophoric silanes with TMMS derivatives. Include inert gas purging and real-time FTIR monitoring to detect hazardous byproducts .
Comparison with Similar Compounds
Structural and Functional Differences
The reactivity and applications of MTMS depend on its three hydrolysable methoxy groups and methyl substituent . Below is a comparison with structurally related silanes:
Key Observations:
- Hydrolysable Groups: MTMS and PTMS both have three methoxy groups, enabling extensive crosslinking during sol-gel processes.
- Functional Groups : The methyl group in MTMS provides hydrophobicity, while methacrylate in 3-methacryloxypropyltrimethoxysilane enables polymerization with organic resins .
- Inert Compounds : Silanes like (Methoxymethyl)trimethylsilane lack hydrolysable groups, limiting their use in reactive applications .
Sol-Gel Coatings
- MTMS-based sol-gels show superior mechanical stability and corrosion resistance compared to PDMMS due to higher crosslink density .
- PTMS forms films with homogeneous coverage but requires longer curing times than MTMS .
Adhesion Promotion
- MTMS outperforms non-functionalized silanes (e.g., Trimethyl(2-phenylethoxy)silane) by forming covalent Si-O-metal bonds with substrates .
- 3-Methacryloxypropyltrimethoxysilane enhances adhesion in polymer-concrete composites through dual organic-inorganic bonding .
Thermal and Chemical Stability
- MTMS-derived coatings retain EMI shielding effectiveness (EMSE >40 dB) even after mechanical stress, unlike uncoated copper textiles .
- PDMMS films degrade faster under UV exposure due to fewer crosslinks .
Research Findings
Properties
Molecular Formula |
C4H12O3Si |
---|---|
Molecular Weight |
136.22 g/mol |
IUPAC Name |
trimethoxymethylsilane |
InChI |
InChI=1S/C4H12O3Si/c1-5-4(8,6-2)7-3/h1-3,8H3 |
InChI Key |
TUQLLQQWSNWKCF-UHFFFAOYSA-N |
Canonical SMILES |
COC(OC)(OC)[SiH3] |
Origin of Product |
United States |
Disclaimer and Information on In-Vitro Research Products
Please be aware that all articles and product information presented on BenchChem are intended solely for informational purposes. The products available for purchase on BenchChem are specifically designed for in-vitro studies, which are conducted outside of living organisms. In-vitro studies, derived from the Latin term "in glass," involve experiments performed in controlled laboratory settings using cells or tissues. It is important to note that these products are not categorized as medicines or drugs, and they have not received approval from the FDA for the prevention, treatment, or cure of any medical condition, ailment, or disease. We must emphasize that any form of bodily introduction of these products into humans or animals is strictly prohibited by law. It is essential to adhere to these guidelines to ensure compliance with legal and ethical standards in research and experimentation.