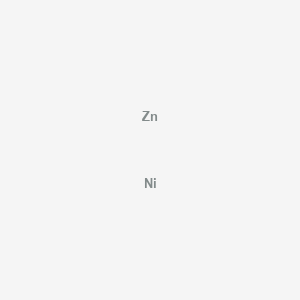
Nickel-ZINC
- Click on QUICK INQUIRY to receive a quote from our team of experts.
- With the quality product at a COMPETITIVE price, you can focus more on your research.
Overview
Description
Nickel-zinc (Ni-Zn) compounds encompass a diverse range of materials and systems, including batteries, ferrites, and alloys. These compounds are distinguished by their unique electrochemical, magnetic, and structural properties, which enable applications in energy storage, electronics, and catalysis. This article provides a detailed comparison of Ni-Zn compounds with analogous systems, supported by data tables and research findings.
Scientific Research Applications
Nickel-Zinc Batteries
This compound batteries are rechargeable batteries that utilize nickel oxide as the positive electrode and zinc as the negative electrode. They have several advantages over traditional battery technologies:
- High Power Density : this compound batteries exhibit the highest power density among mainstream rechargeable battery chemistries, making them suitable for applications requiring quick bursts of energy .
- Environmental Safety : Unlike lithium-ion batteries, this compound batteries do not contain toxic metals such as cobalt or lead, making them more environmentally friendly .
- Long Cycle Life : These batteries can endure hundreds of charge-discharge cycles without significant degradation, which is beneficial for applications in electric vehicles and portable electronics .
Applications in Electric Mobility
This compound batteries are increasingly used in electric mobility applications such as:
- Electric Bikes and Scooters : Their lightweight and high power output make them ideal for e-bikes and e-scooters.
- Electric Vehicles : Companies like ZincFive are developing this compound batteries for trams and electric vehicle charging stations, targeting short-range electric vehicles and hybrid electric vehicles .
Zinc-Nickel Alloys
Zinc-nickel alloys are primarily used for their excellent corrosion resistance properties. They are often employed in various industries where durability is crucial.
Industrial Applications
- Automotive Industry : Zinc-nickel plating is widely used for automotive components such as bolts, fasteners, and brake parts due to its superior corrosion resistance compared to traditional zinc coatings . The typical composition includes 12-15% nickel.
- Aerospace Industry : The aerospace sector utilizes zinc-nickel coatings to meet stringent safety and reliability standards under harsh environmental conditions .
- Oil and Gas Sector : These alloys provide protection against corrosion in pipelines and equipment exposed to aggressive environments.
Case Study 1: Electric Vehicle Applications
A study conducted by ZincFive highlighted the successful integration of this compound batteries in electric bikes and trams. The implementation resulted in a significant reduction in operational costs while maintaining performance standards comparable to lithium-ion systems. This case demonstrates the potential for broader adoption of this compound technology in urban transportation systems.
Case Study 2: Automotive Coatings
In an automotive manufacturing facility, the transition from cadmium plating to zinc-nickel plating resulted in improved environmental compliance and product longevity. The switch not only met regulatory standards but also extended the lifecycle of critical components by up to 50%, showcasing the effectiveness of zinc-nickel coatings under rigorous conditions .
Comparative Data Table
Property/Feature | This compound Batteries | Zinc-Nickel Alloys |
---|---|---|
Power Density | High | N/A |
Environmental Impact | Low (non-toxic) | Moderate (recyclable) |
Cycle Life | Hundreds of cycles | N/A |
Corrosion Resistance | Moderate | Excellent |
Typical Applications | E-mobility, electronics | Automotive, aerospace |
Q & A
Basic Research Questions
Q. What are the standard electrochemical characterization techniques for evaluating Nickel-Zinc (Ni-Zn) battery performance, and how should they be applied?
Methodological Answer: Key techniques include:
- Cyclic Voltammetry (CV): To assess redox behavior and reversibility of NiOOH/Ni(OH)₂ and Zn/ZnO reactions .
- Galvanostatic Charge-Discharge (GCD): Measures capacity retention and cycle life under controlled current densities .
- Electrochemical Impedance Spectroscopy (EIS): Identifies interfacial resistance and charge-transfer limitations .
- X-ray Diffraction (XRD): Monitors phase transitions (e.g., β-NiOOH formation) and structural stability .
- Scanning Electron Microscopy (SEM): Evaluates electrode morphology changes, such as zinc dendrite formation . Best Practice: Cross-validate data with multiple techniques to account for experimental variability.
Q. How should researchers design experiments to ensure reproducibility in Ni-Zn battery studies?
Methodological Answer:
- Detailed Methodology: Include electrolyte composition (e.g., KOH concentration, additives), electrode fabrication (e.g., binder ratios, porosity control), and cycling protocols (voltage limits, C-rates) .
- Supplementary Data: Provide raw datasets (e.g., voltage vs. capacity curves) and material characterization (e.g., BET surface area) in supporting information .
- Reference Standards: Compare results with established benchmarks (e.g., theoretical capacity of 820 mAh g⁻¹ for Zn) .
Q. What metrics are critical for assessing Ni-Zn battery efficiency and durability?
Methodological Answer:
- Energy Density (Wh kg⁻¹): Calculate using discharge curves and active material mass .
- Coulombic Efficiency: Ratio of discharge-to-charge capacity to quantify side reactions (e.g., H₂/O₂ evolution) .
- Cycle Life: Report capacity retention (%) over ≥100 cycles, noting degradation mechanisms (e.g., shape change, dendrites) .
- Self-Discharge Rate: Measure open-circuit voltage decay over time .
Q. How can researchers validate the purity and composition of Ni-Zn electrode materials?
Methodological Answer:
- Inductively Coupled Plasma (ICP) Spectroscopy: Quantifies Ni/Zn ratios in synthesized materials .
- Thermogravimetric Analysis (TGA): Detects impurities (e.g., residual NaCl from powder metallurgy) .
- Fourier-Transform Infrared Spectroscopy (FTIR): Identifies functional groups in composite electrodes .
Q. What are the best practices for reporting conflicting data in Ni-Zn research (e.g., varying cycle life reports)?
Methodological Answer:
- Contextualize Variables: Highlight differences in testing conditions (temperature, current density) or electrode architectures (3D vs. planar designs) .
- Statistical Analysis: Use error bars and ANOVA to assess significance of discrepancies .
- Literature Comparison: Tabulate prior studies’ methodologies and outcomes to identify trends .
Advanced Research Questions
Q. How can experimental designs address the contradiction between theoretical and practical energy densities in Ni-Zn systems?
Methodological Answer:
- Material Optimization: Systematically vary Zn/Ni ratios and electrolyte additives (e.g., Bi₂O₃) to reduce parasitic reactions .
- In-Situ/Operando Techniques: Use Raman spectroscopy or synchrotron XRD to monitor real-time phase evolution during cycling .
- Multiscale Modeling: Combine density functional theory (DFT) for reaction kinetics with finite element analysis (FEA) for electrode stress modeling .
Q. What strategies mitigate zinc dendrite formation and shape change in Ni-Zn batteries?
Methodological Answer:
- Electrolyte Engineering: Optimize pH and additive concentrations (e.g., PEG-200) to suppress Zn dissolution and promote uniform deposition .
- Advanced Electrodes: Develop 3D porous Ni substrates or Zn composites with carbon nanotubes to homogenize current density .
- Pulsed Charging Protocols: Implement asymmetric charge/discharge currents to reduce dendrite growth .
Q. How should researchers resolve discrepancies in reported corrosion rates of Ni-Zn electrodes under varying operational conditions?
Methodological Answer:
- Accelerated Aging Tests: Expose electrodes to extreme temperatures (e.g., 50°C) or high humidity to simulate long-term degradation .
- Surface Passivation: Apply protective coatings (e.g., TiO₂) and quantify effectiveness via EIS and X-ray photoelectron spectroscopy (XPS) .
- Comparative Studies: Replicate prior experiments with identical parameters to isolate variable impacts .
Q. What methodological frameworks are effective for optimizing Ni-Zn battery components while balancing multiple performance metrics?
Methodological Answer:
- Design of Experiments (DoE): Use factorial designs to evaluate interactions between variables (e.g., binder type, porosity) .
- Machine Learning: Train models on published datasets to predict optimal compositions or cycling conditions .
- Multi-Criteria Decision Analysis (MCDA): Weight energy density, cost, and safety to rank candidate materials .
Q. How can advanced computational tools enhance the understanding of Ni-Zn reaction mechanisms?
Methodological Answer:
Comparison with Similar Compounds
Nickel-Zinc Batteries vs. Other Battery Chemistries
Ni-Zn batteries employ a nickel oxyhydroxide cathode, zinc anode, and alkaline electrolyte, delivering a voltage of 1.6 V/cell—higher than Ni-Cd (1.2 V/cell) and comparable to silver-zinc batteries (1.8 V/cell) . Key comparisons are summarized below:
Table 1: Comparison of Rechargeable Battery Chemistries
Key Findings :
- Ni-Zn batteries excel in high-power applications due to their C/4 discharge rate and superior temperature tolerance compared to lead-acid and Li-ion systems .
- They avoid the toxicity of cadmium (Ni-Cd) and lithium’s environmental challenges (e.g., water pollution and resource scarcity) .
This compound Ferrites vs. Other Ferrite Materials
Ni-Zn ferrites (NixZn1–xFe2O4) are soft magnetic ceramics with high resistivity (~10⁵ Ω·m) and applications in high-frequency electronics (50–1000 MHz) .
Table 2: Magnetic and Structural Properties of Ferrites
Key Findings :
- Ni-Zn ferrites exhibit low ferromagnetic resonance (FMR) fields and optimal microwave absorption at nickel concentrations of x = 0.15–0.30 .
- Mn-Zn ferrites outperform Ni-Zn in low-frequency applications (<1 MHz) due to higher saturation magnetization but suffer from lower resistivity .
- Synthesis methods (e.g., sol-gel, co-precipitation) critically influence crystallinity and magnetic properties .
This compound Alloys vs. Other Metal Alloys
Ni-Zn alloys are studied for their thermodynamic stability and electrochemical behavior. For example, Mg-Ni-Zn alloys exhibit phase equilibria distinct from Mg-Zn or Ni-Cd systems .
Table 3: Thermodynamic and Mechanical Properties of Alloys
Property | Ni-Zn Alloy | Ni-Cd Alloy | Zn-Mg Alloy |
---|---|---|---|
Enthalpy of Formation (kJ/mol) | -12.5 | -10.2 | -9.8 |
Electrodeposition Efficiency | 85% | 75% | 70% |
Corrosion Resistance | Moderate | High | Low |
Key Findings :
- Ni-Zn alloys demonstrate enhanced hydrogen adsorption during electrodeposition, influencing nucleation kinetics and alloy composition .
- Compared to Ni-Cd, Ni-Zn alloys are less corrosion-resistant but more cost-effective due to zinc’s abundance .
Environmental and Economic Impact
- Ni-Zn batteries use 96% less water than lithium-ion systems and avoid toxic heavy metals (e.g., lead, cadmium) .
- Recycling Ni-Zn ferrites is simpler than Mn-Zn or Mg-Zn due to their chemical stability .
- The global Ni-Zn battery market is projected to grow at 6.5% CAGR (2023–2030), driven by demand for sustainable energy storage .
Preparation Methods
Solid-State Synthesis Using Industrial By-Products
The utilization of industrial waste materials, such as electric arc furnace dust (EAFD) and waste pickle liquor (WPL), presents an eco-friendly approach to synthesizing Ni-Zn ferrites. In this method, EAFD—a zinc-rich by-product of steelmaking—is treated with 0.5 M HCl to reduce calcium content by 70.6%, minimizing impurity interference . The treated EAFD is then combined with WPL, which provides iron and nickel ions, and calcined at elevated temperatures to form Niₓ(Zn)₁₋ₓFe₂O₄ nanoparticles.
Key Findings:
-
Phase Formation : X-ray diffraction (XRD) confirmed the formation of single-phase spinel structures at Ni content ≤0.5, with average crystallite sizes of 35–45 nm .
-
Magnetic Properties : Optimal saturation magnetization (Ms) of 73.89 emu/g and coercivity (Hc) of 2.55 Oe were achieved at Ni:Zn ratios of 0.5:0.5 and 0.25:0.75, respectively .
-
Environmental Impact : This method repurposes hazardous waste, reducing landfill reliance and raw material costs by ~40% compared to conventional reagents .
Coprecipitation and Thermal Decomposition
A low-density porous Ni-Zn ferrite (NZF) was synthesized via oxalate precursor decomposition . Metal sulfates (NiSO₄·6H₂O, ZnSO₄·7H₂O, FeSO₄·7H₂O) were coprecipitated with oxalic acid under controlled pH (3–4) and temperature (60–80°C), forming a layered oxalate precursor. Subsequent calcination in oxygen at 500–800°C yielded NZF with a wood-splitting morphology and internal cavities.
Structural and Functional Insights:
The oxygen atmosphere was critical for oxidizing Fe²⁺ to Fe³⁺, ensuring stoichiometric Fe₂O₃ formation (4FeO+O2→2Fe2O3) . The porous structure enhanced microwave absorption, with a minimum reflection loss of -23 dB at 8 GHz .
Hydrothermal Synthesis of Zn-Ni-S Nanosheets
While primarily used for sulfides, hydrothermal methods have been adapted for Ni-Zn compounds. A two-step hydrothermal process produced ZnₓNi₁₋ₓS nanosheets on nickel foam, where Zn²⁺ partially substituted Ni²⁺ in the lattice . Reaction conditions (180°C, 12 h) facilitated anisotropic growth, yielding nanosheets with high electrochemical surface area.
Electrochemical Performance:
-
Specific Capacitance : 1412 F/g at 1 A/g, retaining 68% capacity at 16 A/g .
-
Hybrid Supercapacitors : Coupled with porous carbon, the device achieved an energy density of 48 Wh/kg and power density of 800 W/kg .
Solution-Phase Synthesis for Oxide Nanoparticles
Solution-phase methods enable precise control over Ni-Zn oxide nanoparticle morphology. A study using nitrate precursors and sodium hydroxide as a precipitating agent produced homogeneous Ni₀.₅Zn₀.₅O nanoparticles with 10–20 nm diameters . Ethylene glycol acted as a capping agent, preventing agglomeration and ensuring uniform size distribution.
Catalytic Applications:
-
Oxygen Evolution Reaction (OER) : The nanoparticles exhibited a low overpotential of 320 mV at 10 mA/cm², outperforming pure NiO (380 mV) .
-
Surface Area : BET analysis revealed a surface area of 85 m²/g, enhancing active site availability .
Comparative Analysis of Synthesis Methods
Method | Precursors | Conditions | Key Advantages | Limitations |
---|---|---|---|---|
Solid-State (EAFD/WPL) | Industrial waste | 900°C, 2 h | Cost-effective, eco-friendly | Impurity management required |
Coprecipitation | Metal sulfates, oxalic acid | 600–700°C, O₂ atmosphere | Low density, high porosity | Long calcination times |
Hydrothermal | Metal sulfides | 180°C, 12 h | High electrochemical performance | Limited to sulfide derivatives |
Solution-Phase | Nitrates, NaOH | 80°C, 4 h | Uniform nanoparticles | Requires capping agents |
Advanced Characterization Techniques
-
XRD : Confirmed spinel structure in NZF (lattice parameter: 8.39–8.42 Å) .
-
FESEM/TEM : Revealed porous architectures (pore size: 10–50 nm) and nanosheet morphologies .
-
VSM : Quantified Ms and Hc, correlating with Ni/Zn ratio and crystallite size .
-
XPS : Identified Fe²⁺/Fe³⁺ ratios (e.g., 711.0 eV for Fe³⁺, 709.0 eV for Fe²⁺) .
Properties
CAS No. |
12035-62-0 |
---|---|
Molecular Formula |
NiZn |
Molecular Weight |
124.1 g/mol |
IUPAC Name |
nickel;zinc |
InChI |
InChI=1S/Ni.Zn |
InChI Key |
QELJHCBNGDEXLD-UHFFFAOYSA-N |
Canonical SMILES |
[Ni].[Zn] |
Origin of Product |
United States |
Disclaimer and Information on In-Vitro Research Products
Please be aware that all articles and product information presented on BenchChem are intended solely for informational purposes. The products available for purchase on BenchChem are specifically designed for in-vitro studies, which are conducted outside of living organisms. In-vitro studies, derived from the Latin term "in glass," involve experiments performed in controlled laboratory settings using cells or tissues. It is important to note that these products are not categorized as medicines or drugs, and they have not received approval from the FDA for the prevention, treatment, or cure of any medical condition, ailment, or disease. We must emphasize that any form of bodily introduction of these products into humans or animals is strictly prohibited by law. It is essential to adhere to these guidelines to ensure compliance with legal and ethical standards in research and experimentation.