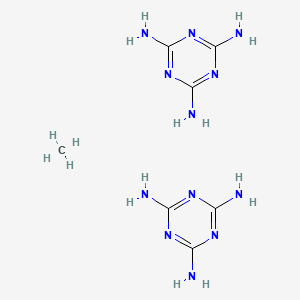
Melamine molybdate
Overview
Description
Melamine molybdate is an inorganic salt synthesized by combining melamine (C₃H₆N₆) with molybdate ions (MoO₄²⁻). It is primarily employed as a flame retardant and smoke suppressant in polymer composites, particularly flexible polyvinyl chloride (PVC) . Its flame-retardant mechanism involves:
- Char formation: Catalyzing the dehydrochlorination of PVC, promoting cross-linking reactions, and forming a stable, intumescent char layer that insulates the underlying material .
- Gas-phase action: Melamine releases non-flammable gases (e.g., NH₃) that dilute combustible gases, while molybdate acts as a Lewis acid to accelerate charring .
- Synergistic effects: The combination of nitrogen-rich melamine and molybdate’s catalytic properties enhances both flame retardancy and smoke suppression .
Scientific Research Applications
Flame Retardant Properties
Melamine molybdate is primarily recognized for its effectiveness as a smoke retardant additive in polymer compositions, especially those based on vinyl chloride and vinylidene chloride. Its smoke-retarding properties are attributed to its unique chemical structure which allows it to act effectively even at lower concentrations compared to traditional flame retardants.
Case Studies and Experimental Findings
- Smoke Chamber Tests : Experimental results from the NBS Smoke Chamber Test demonstrated that this compound exhibited superior smoke retarding effects compared to other molybdenum compounds like molybdenum trioxide. In tests where this compound was incorporated at 5% and 10% weight parts, it significantly reduced smoke emissions while maintaining a visually appealing white color in the final product, unlike the discoloration observed with molybdenum trioxide .
- Applications in Various Products : The compound's incorporation into various materials, such as carpets, house siding, and plastic components for airplane interiors, illustrates its versatility. The ability to blend well without altering the aesthetic properties of the polymers makes it an attractive option for manufacturers seeking to enhance fire safety without compromising product quality .
Electrochemical Sensors
This compound has also been utilized in the development of electrochemical sensors , particularly for detecting melamine residues in food products such as milk powder.
Research Highlights
- Detection Methods : A study developed a solid-phase electrochemiluminescent electrode using molybdenum disulfide quantum dots immobilized with melamine. This innovative approach allowed for sensitive detection of melamine at concentrations as low as mol L, showcasing the potential of this compound in food safety applications .
- Performance Metrics : The sensor demonstrated excellent linearity and recovery rates (97-98%) when applied to real samples, indicating its practical applicability in monitoring food safety standards .
Industrial Applications
This compound finds extensive use in various industrial applications due to its chemical stability and functional properties.
Usage Statistics
According to recent studies, melamine is predominantly used in:
- Surface decorative panels (approximately 40.6%)
- Molding compounds (18.3%)
- Adhesives and coatings (each around 13.1%)
- Other minor applications include textiles and cement products .
These statistics highlight the compound's significant role in enhancing product performance across multiple sectors.
Summary Table of Applications
Application Area | Description | Benefits |
---|---|---|
Flame Retardants | Used in vinyl chloride polymers | Reduces smoke emissions; maintains color |
Electrochemical Sensors | Detection of melamine residues in food products | High sensitivity; good recovery rates |
Industrial Products | Used in decorative panels, adhesives, coatings | Enhances durability and performance |
Chemical Reactions Analysis
Molar Ratios and Composition
The molybdenum-to-nitrogen (Mo:N) ratio is a critical determinant of product composition.
The stoichiometric ratio of 1:3 (Mo:N) aligns with the formula (C₃H₇N₆)₄Mo₈O₂₆, indicating a coordination complex where melamine ligands bind to molybdenum centers .
pH and Reaction Conditions
The acidic environment (pH 1–4) is essential for product formation. Lower pH values favor stable melamine octamolybdate complexes.
pH Range | Key Observations |
---|---|
≤4 | Optimal for synthesis |
1–2 | Higher stability in decomposition tests |
3–4 | Moderate stability, lower decomposition temperatures |
In Example 12 , a pH of 2 during synthesis correlated with a decomposition onset temperature of 375.1°C, demonstrating the pH’s influence on thermal stability .
Thermal Stability Analysis
Thermogravimetric analysis (TGA) data highlights significant variations in thermal stability across synthesis methods.
Example | Decomposition Onset Temp (°C) | 1% Weight Loss Temp (°C) | 2% Weight Loss Temp (°C) |
---|---|---|---|
Example 1 | <160 | <160 | <160 |
Example 2 | >350 | >350 | >350 |
Example 3 | <250 | <250 | <250 |
Example 12 | 375.1 | 351.4 | 366.4 |
Example 2 and Example 12 exhibit exceptional thermal stability, attributed to controlled stoichiometry and acidic conditions .
Q & A
Basic Research Questions
Q. What are the standard protocols for synthesizing melamine molybdate-based composites?
- Methodological Answer : A common approach involves mechanochemical grinding of melamine, cyanuric acid, and sodium molybdate (Na₂MoO₄) precursors, followed by calcination under an inert nitrogen atmosphere at 550°C for 4 hours. The molar ratios of precursors and heating rates (e.g., 5°C/min) critically influence crystallinity and phase purity. Post-synthesis characterization via X-ray diffraction (XRD) and Fourier-transform infrared spectroscopy (FTIR) is essential to confirm the formation of molybdenum-integrated graphitic carbon nitride (g-C₃N₄) structures .
Q. What characterization techniques are essential for confirming the structural integrity of this compound?
- Methodological Answer : Key techniques include:
- XRD : To verify crystallographic phases and detect molybdenum oxide (MoO₃) impurities.
- SEM/TEM : To analyze morphology and particle size distribution.
- FTIR : To identify functional groups (e.g., triazine rings in melamine and Mo–O bonds).
- XPS : To confirm the oxidation state of molybdenum (e.g., Mo⁶⁺ in molybdate).
- BET Surface Area Analysis : To assess porosity and active sites for catalytic applications .
Q. What are the common precursors and reaction conditions for this compound synthesis?
- Methodological Answer : Melamine (C₃H₆N₆), cyanuric acid (C₃H₃N₃O₃), and sodium molybdate (Na₂MoO₄) are typical precursors. Optimized conditions involve a 1:5 molar ratio of melamine to cyanuric acid, with molybdate content varying between 0.02–0.04 g. Calcination under nitrogen at 550°C ensures thermal stability and avoids oxidation of molybdenum species .
Advanced Research Questions
Q. How can researchers optimize the molybdenum content in this compound to enhance photocatalytic activity?
- Methodological Answer : Systematic variation of sodium molybdate (e.g., 0.02–0.04 g) during synthesis allows tuning of Mo⁶⁺ incorporation. Photocatalytic efficiency (e.g., H₂ evolution or dye degradation) should be correlated with molybdenum content using UV-vis diffuse reflectance spectroscopy (DRS) to assess bandgap narrowing. Excess molybdenum (>3 wt%) may form MoO₃ aggregates, reducing active sites, as shown in studies comparing 2Mo–CN, 3Mo–CN, and 4Mo–CN composites .
Q. How to address contradictions in reported antimicrobial efficacy of this compound coatings?
- Methodological Answer : Discrepancies often arise from differences in:
- Testing protocols : Compare JIS (Japanese Industrial Standard) methods with ISO 22196 for antimicrobial activity.
- Sample preparation : Ensure uniform dispersion of molybdate (e.g., 3% Zinc Molybdate in melamine resin) and control coating thickness.
- Microbial strains : Validate results across multiple organisms (e.g., Staphylococcus aureus, Escherichia coli) using standardized inoculum concentrations (e.g., 10⁵ CFU/mL). Replicate studies under controlled humidity and temperature to isolate environmental variables .
Q. What mechanistic studies are used to elucidate the catalytic pathways of this compound in photocatalysis?
- Methodological Answer : Advanced approaches include:
- Electron Spin Resonance (ESR) : To detect reactive oxygen species (ROS) like •OH and •O₂⁻ during photocatalysis.
- Transient Absorption Spectroscopy : To study charge carrier lifetimes and recombination rates.
- DFT Calculations : To model band structures and identify active sites for redox reactions.
- In-situ FTIR : To track intermediate species during catalytic cycles .
Q. Data Contradiction Analysis
Q. How to resolve discrepancies in the thermal stability of this compound composites reported in literature?
- Methodological Answer : Conflicting thermal degradation profiles may stem from:
- Atmospheric differences : Compare thermogravimetric analysis (TGA) under nitrogen vs. air to assess oxidative stability.
- Molybdenum dispersion : Agglomerated MoO₃ reduces thermal resistance, while atomically dispersed molybdate enhances it. Use TEM-EDS mapping to verify dispersion homogeneity.
- Crosslinking density : For resin-based composites, evaluate curing conditions (time/temperature) via DSC to ensure complete polymerization .
Q. Experimental Design Recommendations
Q. How to ensure reproducibility in this compound synthesis for collaborative studies?
- Methodological Answer :
- Detailed documentation : Specify precursor sources, purity (e.g., ≥99%), and grinding duration (e.g., 30 minutes).
- Calibration : Standardize furnace temperature profiles using external thermocouples.
- Supporting Information : Publish raw XRD/FE-SEM data and instrument settings (e.g., accelerating voltage, scan rates) in supplementary files. Cross-validate results with independent labs using shared protocols .
Comparison with Similar Compounds
Melamine Tungstate
- Structure : Similar to melamine molybdate but substitutes molybdate with tungstate ions (WO₄²⁻) .
- Mechanism : Delays PVC degradation and improves char stability via tungsten’s high thermal stability. However, it lacks the intumescent behavior observed in this compound systems .
- Performance :
Melamine Cyanurate
- Structure : A complex of melamine and cyanuric acid, forming a hydrogen-bonded network .
- Mechanism : Acts primarily in the gas phase by releasing nitrogen gases and cooling the combustion zone.
- Performance :
Ammonium Molybdate
- Structure : (NH₄)₂MoO₄, lacking the nitrogen-rich melamine component .
- Mechanism : Functions as a smoke suppressant by catalyzing char formation but requires blending with other flame retardants (e.g., halogenated compounds) for efficacy.
- Performance: Less thermally stable than this compound. Limited application in polymers due to solubility and compatibility issues .
Aluminum Hydroxide (Al(OH)₃)
- Mechanism : Endothermic decomposition releases water vapor, cooling the combustion zone.
- Performance: Requires high loading (50–60 wt%) to achieve flame retardancy, which compromises mechanical properties. No smoke suppression capability, unlike this compound .
Melamine Phosphate
- Structure : Combines melamine with phosphoric acid .
- Mechanism : Acts as an intumescent flame retardant, forming a phosphorus-rich char.
- Performance :
Data Table: Comparative Analysis of Flame Retardants
Compound | LOI Increase (%) | SDR Reduction (%) | Key Mechanism | Thermal Stability | Polymer Compatibility |
---|---|---|---|---|---|
This compound | 25–30 | 40–50 | Intumescent char + Lewis acid | High | Excellent (PVC) |
Melamine Tungstate | 22–28 | 30–40 | Char stabilization | Very High | Moderate |
Melamine Cyanurate | 18–22 | 10–20 | Gas-phase dilution | Moderate | Low (PVC) |
Ammonium Molybdate | 15–20 | 20–30 | Char catalysis | Low | Poor |
Aluminum Hydroxide | 5–10 | 0 | Endothermic cooling | Moderate | High (at high loading) |
Melamine Phosphate | 20–25 | 25–35 | Phosphorus-rich char | Moderate | Good (polyesters) |
Preparation Methods
Aqueous-Phase Synthesis of Melamine Molybdate
Reaction Mechanisms and Stoichiometric Control
This compound is commonly synthesized via aqueous reactions between melamine (C₃H₆N₆) and molybdenum salts such as ammonium dimolybdate [(NH₄)₂Mo₂O₇] or ammonium heptamolybdate [(NH₄)₆Mo₇O₂₄·4H₂O] . The general reaction involves deprotonation of melamine’s amine groups by molybdate anions, forming a coordination polymer. For instance, Example 1 of US4153792A describes dissolving 189.6 g of ammonium dimolybdate in 450 mL of water, followed by addition to a melamine solution (126.1 g in 1,200 mL water) under reflux . The resulting white precipitate, filtered and washed with water and ethanol, yields a 1:1 Mo/melamine molar ratio product .
Stoichiometric variations are achieved by adjusting reactant proportions. Examples 2–18 in US4153792A demonstrate that a 1:1 Mo/melamine ratio is maintained when using equimolar amounts of ammonium dimolybdate and melamine . Conversely, Examples 26–39 utilize excess molybdenum to produce a 2:1 Mo/melamine product . This stoichiometric flexibility is critical for tailoring the compound’s thermal stability and solubility.
Acid-Mediated Synthesis for Enhanced Crystallinity
Influence of Reaction Parameters on Product Properties
Temperature and Reflux Duration
Reflux temperature (80–100°C) and duration (1–24 hours) directly impact yield and crystallinity. US4153792A reports that refluxing for 1 hour in Example 2 produces a 29.25 g yield (83% efficiency), while extended refluxing (19 hours in Example 41) increases yield to 36.10 g . Prolonged heating may induce Ostwald ripening, enlarging crystal domains and improving thermal stability.
WO2018118444A1 emphasizes maintaining reaction temperatures above 85°C to ensure complete dissolution of MoO₃ and prevent intermediate phase formation . For instance, Example 12’s 4-hour reflux at 90°C yields a product with a 1% weight loss temperature of 351.4°C, compared to 160°C for shorter-duration syntheses .
Drying Protocols and Particle Size Control
Post-synthesis drying methods significantly affect moisture content and particle morphology. Vacuum drying at 120°C (Example 2, US4153792A) reduces residual solvent content to <0.5 wt%, whereas air drying at 57°C (Example 1) retains ~2 wt% water . WO2018118444A1 reports that melamine octamolybdate dried at 110°C exhibits a median particle size (d₅₀) of 2–4 μm, ideal for polymer composite applications .
Structural and Thermal Characterization
X-ray Diffraction and Infrared Spectroscopy
XRD patterns of 1:1 Mo/melamine complexes (US4153792A) show characteristic peaks at 2θ = 10.2°, 20.5°, and 27.8°, corresponding to layered structures with intercalated molybdate anions . IR spectra reveal N–H stretching vibrations at 3,400 cm⁻¹ and Mo–O–Mo bridging modes at 850 cm⁻¹ . Acid-mediated products (e.g., Example 25) display broadened peaks due to mixed 1:1 and 2:1 stoichiometries .
Thermogravimetric Analysis (TGA)
TGA data from WO2018118444A1 highlight the superior thermal stability of acid-synthesized melamine octamolybdates. Example 2’s product exhibits a 2% weight loss at 366.4°C, compared to 250°C for commercial analogs . This enhancement is attributed to stronger Mo–N coordination bonds in acidic media .
Comparative Analysis of Synthesis Routes
Parameter | Aqueous Synthesis (US4153792A) | Acid-Mediated Synthesis (WO2018118444A1) |
---|---|---|
Mo Source | Ammonium dimolybdate | Molybdenum trioxide (MoO₃) |
Solvent | Water | Acidic aqueous (pH ≤ 4) |
Molar Ratio (Mo:N) | 1:1 or 2:1 | 1:2 to 1:4 |
Drying Temp. | 57–120°C | 110°C |
Decomposition Onset | 200–250°C | 300–500°C |
Challenges and Optimization Strategies
Byproduct Formation in Acidic Media
HCl-mediated reactions (US4153792A) occasionally yield ammonium chloride byproducts, necessitating thorough washing with ethanol . WO2018118444A1 addresses this by using organic acids (e.g., formic acid), which volatilize during drying, minimizing impurities .
Scale-Up Considerations
Industrial-scale production requires optimizing mixing efficiency and temperature uniformity. Example 12 of WO2018118444A1 demonstrates successful scale-up to 644.3 g batches using peristaltic pump-controlled reactant addition .
Properties
CAS No. |
65235-34-9 |
---|---|
Molecular Formula |
C7H16N12 |
Molecular Weight |
268.28 g/mol |
IUPAC Name |
methane;1,3,5-triazine-2,4,6-triamine |
InChI |
InChI=1S/2C3H6N6.CH4/c2*4-1-7-2(5)9-3(6)8-1;/h2*(H6,4,5,6,7,8,9);1H4 |
InChI Key |
FMXPXIONARXTLI-UHFFFAOYSA-N |
Canonical SMILES |
C.C1(=NC(=NC(=N1)N)N)N.C1(=NC(=NC(=N1)N)N)N |
Origin of Product |
United States |
Synthesis routes and methods I
Procedure details
Synthesis routes and methods II
Procedure details
Synthesis routes and methods III
Procedure details
Disclaimer and Information on In-Vitro Research Products
Please be aware that all articles and product information presented on BenchChem are intended solely for informational purposes. The products available for purchase on BenchChem are specifically designed for in-vitro studies, which are conducted outside of living organisms. In-vitro studies, derived from the Latin term "in glass," involve experiments performed in controlled laboratory settings using cells or tissues. It is important to note that these products are not categorized as medicines or drugs, and they have not received approval from the FDA for the prevention, treatment, or cure of any medical condition, ailment, or disease. We must emphasize that any form of bodily introduction of these products into humans or animals is strictly prohibited by law. It is essential to adhere to these guidelines to ensure compliance with legal and ethical standards in research and experimentation.