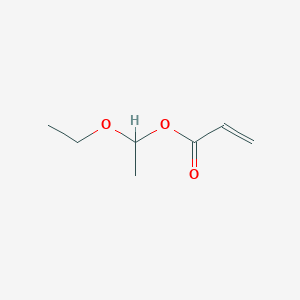
1-Ethoxyethyl acrylate
- Click on QUICK INQUIRY to receive a quote from our team of experts.
- With the quality product at a COMPETITIVE price, you can focus more on your research.
Overview
Description
1-Ethoxyethyl acrylate (EEA) is an acetal-protected derivative of acrylic acid, synthesized via controlled radical polymerization (CRP) techniques such as atom transfer radical polymerization (ATRP) and reversible addition-fragmentation chain transfer (RAFT). Its structure features an ethoxyethyl group that protects the carboxylic acid functionality, enabling polymerization under mild conditions . Deprotection, achieved by heating (80–160°C) or treatment with trifluoroacetic acid (TFA), releases poly(acrylic acid) (PAA) and volatile ethyl vinyl ether, making EEA a critical precursor for well-defined PAA-based materials . This strategy overcomes challenges in directly polymerizing acrylic acid, which is prone to side reactions and poor control .
Scientific Research Applications
Applications in Polymer Chemistry
1-Ethoxyethyl acrylate serves as a crucial monomer in the synthesis of various polymers, including:
- Copolymers : It is frequently copolymerized with other acrylates to enhance material properties such as flexibility, adhesion, and thermal stability. For instance, it has been used to create amphiphilic block copolymers that exhibit improved solubility and functionality in aqueous environments .
- Pressure-Sensitive Adhesives : The incorporation of this compound into adhesive formulations enhances tackiness and adhesion properties, making it suitable for applications in tapes and labels .
- Coatings and Paints : Its use in coatings improves durability and resistance to environmental factors. The compound contributes to the formulation of water-based paints and coatings that require high clarity and gloss .
A study on the propagation rate coefficients of various acrylates indicated that this compound exhibits a relatively high propagation rate compared to other monomers, making it advantageous for rapid polymerization processes. The activation energy for its polymerization was found to be lower than that of isobornyl acrylate, indicating its efficiency in forming polymers at lower temperatures .
Case Study 1: Block Copolymer Synthesis
In a study focused on synthesizing block copolymers for drug delivery systems, researchers utilized this compound as a precursor monomer. The resulting copolymers demonstrated enhanced biocompatibility and controlled drug release characteristics, making them suitable for biomedical applications .
Case Study 2: Adhesive Formulation
A formulation study highlighted the effectiveness of this compound in pressure-sensitive adhesives. The resulting adhesives exhibited superior peel strength and tackiness compared to traditional formulations without this monomer. This enhancement is attributed to the unique chemical structure of this compound, which allows for better interaction with substrates .
Chemical Reactions Analysis
RAFT Polymerization
1-Ethoxyethyl acrylate (EEA) undergoes reversible addition-fragmentation chain-transfer (RAFT) polymerization using 2-cyano-2-butyl dithiobenzoate (CBDB) as the chain-transfer agent and AIBN as the initiator. Key findings include:
ATRP Limitations
Atom transfer radical polymerization (ATRP) of EEA faces challenges:
-
Side reactions : Acrylic acid impurities (from EEA deprotection) coordinate with Cu(I), reducing catalytic activity (PDI >1.5 at 50% conversion)
-
Temperature sensitivity : Requires strict temperature control (<60°C) to prevent deprotection
Deprotection Reactions
The 1-ethoxyethyl group undergoes cleavage under specific conditions to yield poly(acrylic acid) (PAA):
Thermal Deprotection
Acid-Catalyzed Deprotection
EEA synthesis involves acid-catalyzed esterification:
textAcrylic acid + ethyl vinyl ether → EEA (H₂SO₄, 0°C, 90% yield) [3]
Kinetic Analysis
Propagation rate coefficients (kp) for EEA vs. related acrylates:
Monomer | log(kp at 60°C) | Ea (kJ/mol) |
---|---|---|
This compound | 6.80 | 13.8 |
tert-Butyl acrylate | 7.28 | 17.5 |
Isobornyl acrylate | 7.05 | 17.0 |
EEA’s lower activation energy (13.8 kJ/mol) enables faster polymerization compared to sterically hindered acrylates .
Q & A
Basic Research Questions
Q. What are the optimal conditions for controlled polymerization of 1-Ethoxyethyl Acrylate (EEA) to achieve near-monodisperse polymers?
Controlled polymerization of EEA is effectively achieved via RAFT (Reversible Addition-Fragmentation Chain Transfer) at 70°C using chain transfer agents (e.g., cumyl dithiobenzoate), yielding polymers with dispersity (Đ) < 1.2. ATRP (Atom Transfer Radical Polymerization) with copper catalysts (e.g., CuBr/PMDETA) at 60°C also produces well-defined polymers. Temperature optimization is critical to minimize side reactions like chain transfer .
Q. How is the 1-ethoxyethyl protecting group removed to synthesize poly(acrylic acid) (PAA)?
Deprotection involves heating EEA-derived polymers in 0.1 M HCl at 80°C for 4 hours , cleaving the ethoxyethyl group while preserving the acrylic acid backbone. Harsher conditions (120°C in concentrated HCl) induce cross-linking. Progress is monitored via FTIR (loss of C-O-C stretch at 1,100 cm⁻¹ and emergence of O-H stretches at 3,400 cm⁻¹) .
Q. What analytical techniques are critical for characterizing EEA-based polymers?
Essential methods include:
- GPC with triple detection (RI, viscometry, light scattering) for absolute molecular weight (Đ < 1.2 confirms controlled synthesis).
- ¹H NMR to track deprotection (disappearance of ethoxyethyl protons at δ 1.2–1.4 ppm).
- FTIR for functional group analysis (e.g., carboxylic acid formation).
- DSC to observe glass transition shifts (T_g ≈ -15°C for pEEA → 106°C for PAA) .
Q. What challenges arise in synthesizing EEA-based hydrogels for biomedical use?
Key considerations:
- Limit EEA content to <5 mol% to retain hydrophilicity post-deprotection.
- Use UV-initiated polymerization (365 nm, 10 mW/cm²) with Irgacure 2959.
- Purify via dialysis (MWCO 3.5 kDa) to remove residual monomers.
- Optimize cross-linker (PEGDA) concentration (2–5 mol%) for swelling ratios (Q = 15–25). Cytocompatibility must be validated via ISO 10993-5 assays .
Advanced Research Questions
Q. How are propagation rate coefficients (k_p) for EEA determined in free-radical polymerization?
The pulsed laser polymerization-size exclusion chromatography (PLP-SEC) method is employed. High-frequency laser pulses (500 Hz) initiate polymerization at 25°C in toluene, with SEC analyzing molecular weight distributions. For EEA, Dervaux et al. (2009) reported k_p = 2.1 × 10³ L·mol⁻¹·s⁻¹ under controlled monomer (1–3 M) and initiator (DMPA) conditions .
Q. How do EEA-containing block copolymers stabilize pigments in surface modification?
Sequential ATRP synthesizes block copolymers (e.g., poly(isobornyl acrylate)-b-pEEA). After deprotection to PAA blocks, these copolymers stabilize pigments via electrostatic/steric mechanisms. Electrokinetic Sonic Amplitude (ESA) measurements show adsorption layers (5–15 nm thick), with ultrasonic treatment increasing adsorption density by 30–40% in TiO₂ dispersions .
Q. How does solvent polarity affect RAFT polymerization kinetics of EEA?
In toluene (ε = 2.4), EEA exhibits k_p = 2.1 × 10³ L·mol⁻¹·s⁻¹ (Đ = 1.08–1.15). Polar solvents like DMF (ε = 37) reduce k_p by 15–20% due to chain stiffness, increasing activation energy from 22 kJ/mol (toluene) to 28 kJ/mol (DMF). Solvent choice balances reaction rate and end-group fidelity .
Q. What mechanistic insights explain chain transfer to polymer (CTP) in EEA homopolymerization?
MALDI-TOF analysis reveals CTP occurs via mid-chain radical formation at β-carbons (68% occurrence), increasing branching at >40% conversion. Dispersity rises from 1.15 to 1.55 at 80% conversion. The Tobita-Hamielec kinetic model incorporating penultimate unit effects predicts branching frequencies within ±5% of experimental data .
Comparison with Similar Compounds
Comparison with Similar Acrylate Compounds
Structural and Functional Differences
EEA vs. tert-Butyl Acrylate (tBA) :
- Structure : tBA has a bulky tert-butyl group, whereas EEA’s ethoxyethyl group is less sterically hindered but hydrolytically labile.
- Deprotection : tBA requires strong acidic conditions (e.g., HCl) for deprotection to PAA, while EEA deprotects thermally or with mild acid (TFA) .
- Applications : tBA is used in hydrophobic polymer segments, whereas EEA enables pH-responsive amphiphilic copolymers .
EEA vs. Isobornyl Acrylate (iBA) :
- Steric Effects : iBA’s bicyclic isobornyl group introduces significant steric hindrance, reducing propagation rate coefficients ($k_p$) compared to EEA .
- Thermal Properties : Poly(iBA) has a high glass transition temperature ($T_g = 94°C$), similar to PMMA, whereas PAA (from EEA) is hydrophilic and flexible .
EEA vs. 2-Ethylhexyl Acrylate (2-EHA) :
- Functionality : 2-EHA’s long alkyl chain imparts softness and hydrophobicity, making it ideal for adhesives and plasticizers. EEA, in contrast, is a transient precursor for hydrophilic PAA .
- Polymerization Control : 2-EHA typically forms low-$T_g$ elastomers, while EEA-derived PAA enables stimuli-responsive materials .
EEA vs. Ethyl Acrylate (EA) :
Polymerization Kinetics
Propagation rate coefficients ($k_p$) for acrylates vary with steric and electronic effects:
Key Findings :
Thermal and Deprotection Properties
Property | EEA | tBA | iBA |
---|---|---|---|
Deprotection Temp | 80–160°C (bulk/soln) | >100°C (acidic) | N/A (non-deprotecting) |
Byproduct | Ethyl vinyl ether | Isobutylene | N/A |
$T_g$ of Polymer | PAA: ~106°C | PAA: ~106°C | Poly(iBA): 94°C |
Advantages of EEA :
Properties
Molecular Formula |
C7H12O3 |
---|---|
Molecular Weight |
144.17 g/mol |
IUPAC Name |
1-ethoxyethyl prop-2-enoate |
InChI |
InChI=1S/C7H12O3/c1-4-7(8)10-6(3)9-5-2/h4,6H,1,5H2,2-3H3 |
InChI Key |
DBZKLCIHFPDWMJ-UHFFFAOYSA-N |
Canonical SMILES |
CCOC(C)OC(=O)C=C |
Origin of Product |
United States |
Disclaimer and Information on In-Vitro Research Products
Please be aware that all articles and product information presented on BenchChem are intended solely for informational purposes. The products available for purchase on BenchChem are specifically designed for in-vitro studies, which are conducted outside of living organisms. In-vitro studies, derived from the Latin term "in glass," involve experiments performed in controlled laboratory settings using cells or tissues. It is important to note that these products are not categorized as medicines or drugs, and they have not received approval from the FDA for the prevention, treatment, or cure of any medical condition, ailment, or disease. We must emphasize that any form of bodily introduction of these products into humans or animals is strictly prohibited by law. It is essential to adhere to these guidelines to ensure compliance with legal and ethical standards in research and experimentation.