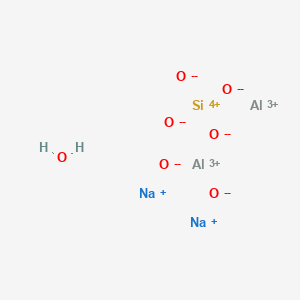
Alusil ET
Overview
Description
Alusil is a hypereutectic aluminum-silicon (Al-Si) alloy, historically developed to address challenges in automotive engineering, particularly for engine components requiring low thermal expansion, high wear resistance, and lightweight properties. It typically contains 23% silicon, aluminum, and minor additions of copper to enhance mechanical strength . Initially commercialized in Germany and France (under the trade name Alsia), Alusil replaced nickel-based coatings like Nikasil due to environmental concerns and superior material performance in engine bores .
In industrial applications, Alusil is also referenced as an aluminosilicate matrix (e.g., ALUSIL®) for radioactive waste conditioning, demonstrating its versatility . However, this article focuses on its metallurgical applications, where it competes with similar alloys and coatings.
Scientific Research Applications
Automotive Applications
Engine Components:
Alusil ET is widely used in the production of engine blocks and cylinder liners due to its excellent wear resistance and thermal stability. The alloy's hypereutectic composition, which includes approximately 17% silicon, enhances its hardness and reduces wear rates compared to traditional cast iron components. For instance, Porsche's extensive testing demonstrated that Alusil cylinders exhibited significantly lower deformation and scoring compared to earlier materials .
Performance Enhancements:
The use of this compound allows manufacturers to produce lighter engines without compromising strength or performance. For example, Toyota reported a 26.17% increase in horsepower when using Alusil in their engines, highlighting the material's efficiency in enhancing power output while maintaining lower weight .
Data Table: Performance Comparison of Engine Components
Material Type | Weight Reduction (%) | Horsepower Increase (%) | Wear Resistance (Relative) |
---|---|---|---|
Cast Iron | 0 | 0 | 1 |
This compound | 20 | 26.17 | 2 |
Thermal Management
Heat Storage Applications:
this compound is also utilized in thermal management systems, specifically as a metallic phase change material (mPCM). Its ability to store thermal energy during phase changes at around 577 °C makes it valuable for applications requiring efficient heat transfer and storage . This property is particularly beneficial in automotive applications where managing engine heat is crucial for performance and longevity.
Industrial Uses
Manufacturing Components:
Beyond automotive applications, this compound is employed in various industrial components that require high wear resistance and thermal stability. The alloy's unique microstructure allows for enhanced performance in high-stress environments such as pumps and compressors.
Case Study: Cylinder Liners
A case study analyzed the performance of Alusil-coated cylinder liners in heavy-duty diesel engines. The results indicated that engines equipped with these liners experienced reduced friction and improved fuel efficiency compared to those with conventional liners. The study highlighted a significant decrease in maintenance costs due to the extended lifespan of the Alusil components .
Summary of Properties
The key properties that make this compound a preferred choice for various applications include:
- High Wear Resistance: Due to its silicon content, which creates a hard surface that withstands abrasion.
- Thermal Stability: Maintains performance under high-temperature conditions.
- Lightweight: Contributes to overall vehicle weight reduction, enhancing fuel efficiency.
- Corrosion Resistance: Offers durability against environmental factors.
Q & A
Basic Research Questions
Q. What standardized characterization techniques are recommended for verifying the microstructure and phase composition of Alusil ET in experimental settings?
- Methodological Answer : Employ scanning electron microscopy (SEM) with energy-dispersive X-ray spectroscopy (EDS) to map elemental distribution and identify intermetallic phases. Pair this with X-ray diffraction (XRD) to confirm crystallographic structure . For reproducibility, document instrument parameters (e.g., acceleration voltage, scan rate) and adhere to ASTM standards for sample preparation .
Q. How should researchers design controlled experiments to assess the mechanical properties of this compound under varying thermal conditions?
- Methodological Answer : Use a split-plot experimental design to test tensile strength and hardness across temperature gradients (e.g., 25°C to 300°C). Standardize strain rates (e.g., 0.5 mm/min) per ISO 6892-1 and incorporate control groups with pure aluminum or silicon analogs for baseline comparison. Statistical tools like ANOVA should validate significance (p < 0.05) .
Q. What protocols ensure reproducibility in synthesizing this compound at the laboratory scale?
- Methodological Answer : Publish detailed synthesis steps, including precursor purity (≥99.9%), melting temperatures (±5°C tolerance), and cooling rates (e.g., 10°C/min for eutectic solidification). Cross-reference with peer-reviewed protocols and validate via inter-laboratory comparisons .
Advanced Research Questions
Q. How can researchers resolve contradictions in reported thermal stability data for this compound across different studies?
- Methodological Answer : Conduct a meta-analysis of existing datasets to identify confounding variables (e.g., impurity levels, annealing duration). Use sensitivity analysis to isolate factors like oxygen content or quenching methods. Pre-register hypotheses to avoid bias, as per Recommendation 8.1 in .
Q. What advanced computational models are suitable for predicting phase transitions in this compound under extreme stress conditions?
- Methodological Answer : Implement finite element analysis (FEA) with ABAQUS or COMSOL, integrating experimental stress-strain data to calibrate models. Validate predictions against synchrotron XRD results under dynamic loading. Address discrepancies via Bayesian inference to refine model parameters .
Q. How can experimental design be optimized to minimize interfacial defects in this compound composites during additive manufacturing?
- Methodological Answer : Apply a Taguchi orthogonal array to test variables (e.g., laser power, layer thickness). Characterize defects via micro-CT imaging and quantify porosity using Archimedes’ principle. Optimize parameters via response surface methodology (RSM), prioritizing defect reduction while maintaining mechanical integrity .
Q. What strategies validate the chemical homogeneity of this compound in large-scale samples without destructive testing?
- Methodological Answer : Use neutron diffraction for bulk phase analysis or laser-induced breakdown spectroscopy (LIBS) for surface mapping. Cross-validate with EBSD (electron backscatter diffraction) on subsectioned samples. Statistical process control (SPC) charts can monitor homogeneity across batches .
Q. Methodological Frameworks for Data Interpretation
Q. How should researchers document and justify deviations from pre-registered analysis plans when studying this compound’s corrosion resistance?
- Methodological Answer : Maintain an open lab notebook detailing unplanned variables (e.g., humidity fluctuations). Use the STROBE framework to report deviations transparently. Apply Bonferroni corrections to adjust p-values in multi-test scenarios .
Q. What statistical approaches are recommended for reconciling contradictory fatigue-life data in this compound across different testing environments?
- Methodological Answer : Employ Cox proportional hazards models to account for censored data in fatigue tests. Stratify results by environmental factors (e.g., saline exposure, cyclic humidity) and use Kaplan-Meier survival curves to visualize disparities. Reconcile outliers via Grubbs’ test or robust regression .
Q. How can systematic reviews be structured to evaluate the long-term durability of this compound in aerospace applications?
- Methodological Answer : Follow PRISMA guidelines to screen studies, emphasizing peer-reviewed journals and excluding industrial reports. Use GRADE criteria to assess evidence quality, focusing on sample size, follow-up duration, and environmental simulation fidelity. Highlight gaps for future research, such as microgravity effects .
Comparison with Similar Compounds
Alusil vs. Nikasil
Nikasil is an electrodeposited nickel-silicon carbide (Ni-SiC) coating applied to aluminum engine cylinders. While it improved durability in high-performance engines, Alusil emerged as a bulk-material alternative with distinct advantages:
Key Findings :
- Alusil’s hypereutectic structure minimizes piston-cylinder friction, critical for air-cooled engines (e.g., Porsche 928, 944) .
- Nikasil’s susceptibility to corrosion with modern lubricants (e.g., IF-WS2-doped oils) limits its use, whereas Alusil remains compatible .
Alusil vs. Standard Al-Si Alloys
Conventional Al-Si alloys (eutectic or hypoeutectic) lack the silicon content required for extreme wear resistance:
Research Insight :
- Laser-clad Alusil coatings with SiC particles show inhomogeneous distribution, but still outperform standard alloys in wear tests .
Alusil vs. Alsia
Alsia is the French equivalent of Alusil, sharing similar composition and applications. Minor differences lie in regional manufacturing standards and historical patenting .
Critical Analysis of Advantages and Limitations
Advantages of Alusil :
- High Silicon Content : Reduces thermal expansion and improves seizure resistance .
- Environmental Safety : Eliminates nickel, aligning with stricter regulations .
- Longevity : Maintains dimensional stability under cyclic thermal loads .
Limitations :
Preparation Methods
Compositional Design and Raw Material Selection
Hypereutectic Alusil ET alloys typically contain 12–20 wt% silicon , with precise compositional adjustments dictating final mechanical and thermal properties . The inclusion of copper (Cu) and magnesium (Mg) at 4–5 wt% enhances precipitation hardening, while trace additions of phosphorus (P) or rare earth elements (RE) refine silicon crystallites .
Silicon Content Optimization
In the ALUSIL® process, the alloy AlSi-17Cu4Mg (17% Si, 4% Cu, 1% Mg) exemplifies the hypereutectic standard, where excess silicon forms primary crystals during solidification . Increasing silicon to 20 wt% improves wear resistance but risks coarse silicon platelet formation, necessitating microstructure modifiers .
Role of Additives
-
Phosphorus (P): Added at 0.005–0.02 wt%, phosphorus nucleates silicon crystals, reducing their size from 50–100 μm to 10–30 μm .
-
Rare Earth Elements (RE): Cerium (Ce) and lanthanum (La) at 0.2–0.5 wt% adsorb onto silicon growth fronts, promoting isotropic crystal growth and suppressing needle-like eutectic structures .
Conventional Casting and Microstructure Challenges
Traditional gravity casting of hypereutectic Al-Si alloys often yields detrimental microstructures:
Microstructural Feature | Impact on Properties |
---|---|
Coarse primary silicon (50–100 μm) | Stress concentration, brittle fracture |
Needle-like eutectic silicon | Reduced fatigue resistance |
Porosity (2–5% volume) | Impaired mechanical strength |
Source identifies shrinkage porosity and silicon phase inhomogeneity as primary limitations of conventional methods.
Advanced Preparation Methods
Spray Forming with Hot Pressing (Patent CN104264016B)
This industrial-scale method combines rapid solidification and thermomechanical processing:
-
Melting and Alloying
-
Spray Forming Parameters
-
Hot Pressing Densification
ALUSIL® Process with Phosphorus Modification
Developed for engine block production, this method prioritizes silicon morphology control:
-
Alloy Preparation
-
Directional Solidification
Comparative Analysis of Preparation Techniques
The spray-forming route achieves finer microstructures but requires higher capital investment. ALUSIL® balances cost and performance for mass production.
Post-Processing and Performance Enhancement
Heat Treatment
-
Solution treatment: 495–505°C for 4–6 hours dissolves Cu/Mg intermetallics .
-
Aging: 170–190°C for 8–12 hours precipitates Mg₂Si and Al₂Cu phases, increasing hardness by 15–20% .
Surface Engineering
-
Electrochemical etching: Removes aluminum matrix, exposing silicon protrusions (5–10 μm height) for improved lubricity .
-
Plasma electrolytic oxidation (PEO): Forms 20–30 μm Al₂O₃ coatings, enhancing wear resistance by 40% .
Industrial Applications and Case Studies
Automotive Pistons
This compound pistons exhibit 30% lower wear rates compared to eutectic alloys, with service lifetimes exceeding 300,000 km .
High-Performance Engine Blocks
The ALUSIL® process enables monolithic aluminum engine blocks with 0.5–1.5 μm RMS surface roughness , eliminating cast iron liners .
Properties
Molecular Formula |
Al2H2Na2O7Si |
---|---|
Molecular Weight |
242.04 g/mol |
IUPAC Name |
dialuminum;disodium;oxygen(2-);silicon(4+);hydrate |
InChI |
InChI=1S/2Al.2Na.H2O.6O.Si/h;;;;1H2;;;;;;;/q2*+3;2*+1;;6*-2;+4 |
InChI Key |
JYIMWRSJCRRYNK-UHFFFAOYSA-N |
Canonical SMILES |
O.[O-2].[O-2].[O-2].[O-2].[O-2].[O-2].[Na+].[Na+].[Al+3].[Al+3].[Si+4] |
Related CAS |
12042-41-0 (aluminum.H4-o4-si.hydrochloride) |
Origin of Product |
United States |
Synthesis routes and methods I
Procedure details
Synthesis routes and methods II
Procedure details
Synthesis routes and methods III
Procedure details
Synthesis routes and methods IV
Procedure details
Synthesis routes and methods V
Procedure details
Disclaimer and Information on In-Vitro Research Products
Please be aware that all articles and product information presented on BenchChem are intended solely for informational purposes. The products available for purchase on BenchChem are specifically designed for in-vitro studies, which are conducted outside of living organisms. In-vitro studies, derived from the Latin term "in glass," involve experiments performed in controlled laboratory settings using cells or tissues. It is important to note that these products are not categorized as medicines or drugs, and they have not received approval from the FDA for the prevention, treatment, or cure of any medical condition, ailment, or disease. We must emphasize that any form of bodily introduction of these products into humans or animals is strictly prohibited by law. It is essential to adhere to these guidelines to ensure compliance with legal and ethical standards in research and experimentation.