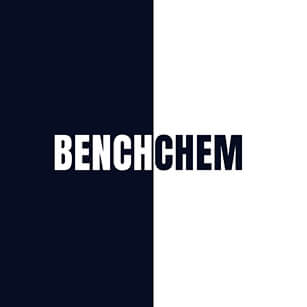
Ethynylbenzene-13C2
Overview
Description
Ethynylbenzene-13C2 is a labeled analogue of ethynylbenzene, an aromatic hydrocarbon. This compound is significant in the petrochemical industry as an intermediate in the production of styrene, which is used to make polystyrene, a common plastic material .
Mechanism of Action
Target of Action
Ethynylbenzene-13C2, also known as Phenylacetylene-1,2-13C2 , is a labeled analogue of Ethynylbenzene It’s known that ethynylbenzene and its analogues are important in the petrochemical industry as intermediates in the production of styrene .
Mode of Action
The general mechanism of electrophilic aromatic substitution, a common reaction type for aromatic compounds like ethynylbenzene, involves the attack of the pi electrons in the aromatic ring on the electrophile . In the next step, a base attacks the hydrogen, causing the electrons in the C-H bond to form a C-C double bond, and aromaticity is reformed .
Biochemical Pathways
It’s known that ethynylbenzene is used as an intermediate in the production of styrene , which is used for making polystyrene, a common plastic material .
Pharmacokinetics
The compound’s physical properties such as boiling point (142-144 °c) and density (0948 g/mL at 25 °C) are known , which could potentially influence its pharmacokinetic behavior.
Result of Action
As an intermediate in the production of styrene , it contributes to the synthesis of polystyrene, a common plastic material .
Preparation Methods
Synthetic Routes and Reaction Conditions: Ethynylbenzene-13C2 can be synthesized through various methods. One common approach involves the reaction of benzene with acetylene in the presence of a catalyst. The reaction conditions typically include high temperatures and pressures to facilitate the formation of the ethynyl group on the benzene ring .
Industrial Production Methods: In industrial settings, the production of this compound often involves the use of labeled carbon sources to incorporate the 13C2 isotopes into the ethynyl group. This process ensures the compound’s isotopic labeling, which is crucial for its applications in scientific research .
Chemical Reactions Analysis
Types of Reactions: Ethynylbenzene-13C2 undergoes various chemical reactions, including:
Common Reagents and Conditions:
Oxidation: Potassium permanganate (KMnO4), chromium trioxide (CrO3)
Reduction: Hydrogen gas (H2), palladium catalyst (Pd/C)
Substitution: Bromine (Br2), nitric acid (HNO3)
Major Products Formed:
Oxidation: Benzoic acid
Reduction: Ethylbenzene
Substitution: Brominated or nitrated ethynylbenzene derivatives
Scientific Research Applications
Ethynylbenzene-13C2 has a wide range of applications in scientific research, including:
Chemistry: Used as a tracer in reaction mechanisms and kinetic studies due to its isotopic labeling.
Biology: Employed in metabolic studies to trace the incorporation of carbon atoms into biological molecules.
Medicine: Utilized in the development of radiolabeled compounds for imaging and diagnostic purposes.
Industry: Serves as an intermediate in the synthesis of various polymers and materials.
Comparison with Similar Compounds
Ethynylbenzene-13C2 is unique due to its isotopic labeling, which distinguishes it from other similar compounds. Some similar compounds include:
Ethynylbenzene: The non-labeled analogue, used in similar applications but without the isotopic tracking capability.
Phenylacetylene: Another aromatic compound with an ethynyl group, used in organic synthesis and polymer production.
1-Bromo-2-ethynylbenzene: A brominated derivative used in substitution reactions.
This compound’s uniqueness lies in its isotopic labeling, making it invaluable for research applications that require precise tracking and analysis of reaction mechanisms .
Properties
CAS No. |
263012-32-4 |
---|---|
Molecular Formula |
C8H6 |
Molecular Weight |
104.121 |
IUPAC Name |
ethynylbenzene |
InChI |
InChI=1S/C8H6/c1-2-8-6-4-3-5-7-8/h1,3-7H/i1+1,2+1 |
InChI Key |
UEXCJVNBTNXOEH-ZDOIIHCHSA-N |
SMILES |
C#CC1=CC=CC=C1 |
Synonyms |
1-Phenylethyne-13C2; Ethynylbenzene-13C2; NSC 4957-13C2; Phenylacetylene-13C2; Phenylethyne-13C2; Ethynyl-1-13C2-benzene; Phenyl[1-13C2]acetylene; |
Origin of Product |
United States |
Synthesis routes and methods I
Procedure details
Synthesis routes and methods II
Procedure details
Synthesis routes and methods III
Procedure details
Disclaimer and Information on In-Vitro Research Products
Please be aware that all articles and product information presented on BenchChem are intended solely for informational purposes. The products available for purchase on BenchChem are specifically designed for in-vitro studies, which are conducted outside of living organisms. In-vitro studies, derived from the Latin term "in glass," involve experiments performed in controlled laboratory settings using cells or tissues. It is important to note that these products are not categorized as medicines or drugs, and they have not received approval from the FDA for the prevention, treatment, or cure of any medical condition, ailment, or disease. We must emphasize that any form of bodily introduction of these products into humans or animals is strictly prohibited by law. It is essential to adhere to these guidelines to ensure compliance with legal and ethical standards in research and experimentation.