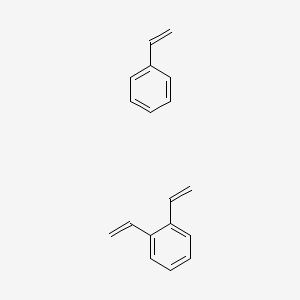
Benzene, diethenyl-, polymer with ethenylbenzene, brominated
Overview
Description
Benzene, diethenyl-, polymer with ethenylbenzene, brominated is a brominated polymer derived from the polymerization of benzene, diethenyl- and ethenylbenzene. This compound is known for its flame-retardant properties, making it valuable in various industrial applications. The bromination process enhances the polymer’s thermal stability and resistance to combustion.
Preparation Methods
Synthetic Routes and Reaction Conditions: The synthesis of benzene, diethenyl-, polymer with ethenylbenzene, brominated involves the polymerization of benzene, diethenyl- and ethenylbenzene, followed by bromination. The polymerization can be initiated using free radical initiators such as benzoyl peroxide or azobisisobutyronitrile. The reaction is typically carried out in an inert atmosphere at elevated temperatures.
Industrial Production Methods: In industrial settings, the polymerization is conducted in large reactors with precise control over temperature and pressure. The bromination step involves the addition of bromine or bromine-containing compounds to the polymer, often in the presence of a catalyst such as iron or aluminum bromide. The process is carefully monitored to ensure uniform bromination and to prevent degradation of the polymer.
Types of Reactions:
Oxidation: The brominated polymer can undergo oxidation reactions, especially at elevated temperatures, leading to the formation of brominated oxidation products.
Reduction: Reduction reactions are less common but can occur under specific conditions, leading to the removal of bromine atoms.
Substitution: The bromine atoms in the polymer can be substituted with other functional groups through nucleophilic substitution reactions.
Common Reagents and Conditions:
Oxidation: Common oxidizing agents include potassium permanganate and hydrogen peroxide.
Reduction: Reducing agents such as sodium borohydride or lithium aluminum hydride can be used.
Substitution: Nucleophiles like hydroxide ions or amines are commonly used in substitution reactions.
Major Products:
Oxidation: Brominated oxidation products.
Reduction: De-brominated polymer.
Substitution: Polymers with substituted functional groups.
Scientific Research Applications
Benzene, diethenyl-, polymer with ethenylbenzene, brominated has a wide range of applications in scientific research:
Chemistry: Used as a flame retardant in polymer chemistry and materials science.
Biology: Investigated for its potential use in biomedical applications due to its stability and biocompatibility.
Medicine: Explored for use in drug delivery systems and medical devices.
Industry: Widely used in the production of flame-retardant materials, coatings, and adhesives.
Mechanism of Action
The flame-retardant properties of benzene, diethenyl-, polymer with ethenylbenzene, brominated are primarily due to the presence of bromine atoms. Upon exposure to heat, the bromine atoms release bromine radicals, which interfere with the combustion process by capturing free radicals. This process effectively slows down or prevents the spread of flames. The polymer matrix also contributes to the overall thermal stability and mechanical strength of the material.
Comparison with Similar Compounds
Benzene, diethenyl-, polymer with ethenylbenzene, sulfonated: This compound is used in ion exchange resins and water treatment applications.
Benzene, diethenyl-, polymer with ethenylbenzene and ethenylethylbenzene: Known for its use in adsorbent resins and chromatography.
Uniqueness: Benzene, diethenyl-, polymer with ethenylbenzene, brominated stands out due to its enhanced flame-retardant properties, which are not present in the sulfonated or non-brominated versions. The bromination process significantly improves the polymer’s resistance to combustion, making it highly valuable in applications where fire safety is a critical concern.
Properties
IUPAC Name |
1,2-bis(ethenyl)benzene;styrene | |
---|---|---|
Details | Computed by Lexichem TK 2.7.0 (PubChem release 2021.05.07) | |
Source | PubChem | |
URL | https://pubchem.ncbi.nlm.nih.gov | |
Description | Data deposited in or computed by PubChem | |
InChI |
InChI=1S/C10H10.C8H8/c1-3-9-7-5-6-8-10(9)4-2;1-2-8-6-4-3-5-7-8/h3-8H,1-2H2;2-7H,1H2 | |
Details | Computed by InChI 1.0.6 (PubChem release 2021.05.07) | |
Source | PubChem | |
URL | https://pubchem.ncbi.nlm.nih.gov | |
Description | Data deposited in or computed by PubChem | |
InChI Key |
CHRJZRDFSQHIFI-UHFFFAOYSA-N | |
Details | Computed by InChI 1.0.6 (PubChem release 2021.05.07) | |
Source | PubChem | |
URL | https://pubchem.ncbi.nlm.nih.gov | |
Description | Data deposited in or computed by PubChem | |
Canonical SMILES |
C=CC1=CC=CC=C1.C=CC1=CC=CC=C1C=C | |
Details | Computed by OEChem 2.3.0 (PubChem release 2021.05.07) | |
Source | PubChem | |
URL | https://pubchem.ncbi.nlm.nih.gov | |
Description | Data deposited in or computed by PubChem | |
Molecular Formula |
C18H18 | |
Details | Computed by PubChem 2.1 (PubChem release 2021.05.07) | |
Source | PubChem | |
URL | https://pubchem.ncbi.nlm.nih.gov | |
Description | Data deposited in or computed by PubChem | |
Molecular Weight |
234.3 g/mol | |
Details | Computed by PubChem 2.1 (PubChem release 2021.05.07) | |
Source | PubChem | |
URL | https://pubchem.ncbi.nlm.nih.gov | |
Description | Data deposited in or computed by PubChem | |
CAS No. |
87924-01-4 | |
Record name | Benzene, diethenyl-, polymer with ethenylbenzene, brominated | |
Source | EPA Chemicals under the TSCA | |
URL | https://www.epa.gov/chemicals-under-tsca | |
Description | EPA Chemicals under the Toxic Substances Control Act (TSCA) collection contains information on chemicals and their regulations under TSCA, including non-confidential content from the TSCA Chemical Substance Inventory and Chemical Data Reporting. | |
Synthesis routes and methods I
Procedure details
Synthesis routes and methods II
Procedure details
Synthesis routes and methods III
Procedure details
Synthesis routes and methods IV
Procedure details
Synthesis routes and methods V
Procedure details
Disclaimer and Information on In-Vitro Research Products
Please be aware that all articles and product information presented on BenchChem are intended solely for informational purposes. The products available for purchase on BenchChem are specifically designed for in-vitro studies, which are conducted outside of living organisms. In-vitro studies, derived from the Latin term "in glass," involve experiments performed in controlled laboratory settings using cells or tissues. It is important to note that these products are not categorized as medicines or drugs, and they have not received approval from the FDA for the prevention, treatment, or cure of any medical condition, ailment, or disease. We must emphasize that any form of bodily introduction of these products into humans or animals is strictly prohibited by law. It is essential to adhere to these guidelines to ensure compliance with legal and ethical standards in research and experimentation.