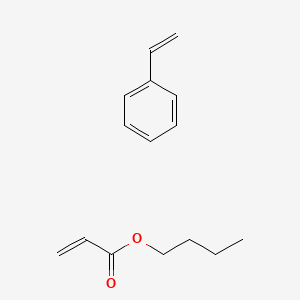
Butyl prop-2-enoate;styrene
Overview
Description
Butyl prop-2-enoate (Butyl acrylate): Butyl acrylate (CAS 141-32-2, C₇H₁₂O₂) is an acrylic ester formed by the condensation of acrylic acid and 1-butanol. It is a clear, colorless liquid with a sharp odor, low water solubility, and applications in coatings, adhesives, sealants, and impact modifiers for plastics . Its polymerization behavior is notable in controlled radical polymerization techniques, such as nitroxide-mediated polymerization (NMP), where additives like α-hydroxy carbonyl compounds enhance conversion rates and reduce polydispersity .
Styrene: Styrene (C₈H₈, CAS 100-42-5) is a vinyl aromatic monomer widely used to produce polystyrene, rubber, and copolymers. It is a volatile, flammable liquid with a sweet odor. Styrene’s copolymerization with acrylates (e.g., butyl acrylate) improves mechanical properties and thermal stability in materials like adhesives and coatings .
Preparation Methods
Monomer Preparation
Butyl prop-2-enoate (Butyl Acrylate) Synthesis
Butyl prop-2-enoate is industrially synthesized by several methods, mainly:
β-Propiolactone Method : Acetic acid or acetone is used as raw materials, with triethyl phosphate as a catalyst. Ketene is generated by pyrolysis at high temperatures (625–730 °C) and then reacted with anhydrous acetic acid derivatives in the presence of catalysts like aluminum chloride or boron trifluoride to form β-propiolactone. This intermediate is then reacted with butanol and sulfuric acid to produce butyl acrylate without purification.
Acrylonitrile Hydrolysis Method : Acrylonitrile is hydrolyzed with sulfuric acid at around 90 °C to form acrylamide sulfate, which is then esterified to produce acrylate esters including butyl acrylate.
Repee Method (Acetylene Carbonylation) : Acetylene and carbon monoxide react with alcohols in the presence of nickel carbonyl catalysts under controlled temperature and pressure to produce acrylic esters such as butyl acrylate.
Propylene Direct Oxidation : Propylene is oxidized catalytically in the gas phase with air and butanol to produce butyl acrylate, a newer industrial method with optimized raw material consumption.
Styrene Preparation
Styrene is commercially produced mainly by the catalytic dehydrogenation of ethylbenzene. It is purified by distillation to remove impurities that could inhibit polymerization.
Copolymerization: Butyl prop-2-enoate and Styrene
Emulsion Polymerization
The most common method for preparing butyl prop-2-enoate;styrene copolymers is emulsion polymerization , which offers control over molecular weight, particle size, and polymer properties.
Monomer Purification : Both butyl acrylate and styrene monomers are purified to remove inhibitors and impurities that affect polymerization.
Initiation : Radical initiators such as benzoyl peroxide or potassium persulfate are used to start the polymerization reaction.
Reaction Conditions : The monomers are emulsified in water with surfactants (emulsifiers). The reaction is typically conducted under nitrogen atmosphere to prevent unwanted oxidation, at temperatures ranging from 50 to 90 °C.
Monomer Ratio and Feed : The ratio of butyl acrylate to styrene is adjusted to tailor the copolymer properties. Styrene imparts rigidity and impact resistance, while butyl acrylate provides flexibility.
Polymerization Time : The reaction is maintained for 6–8 hours to ensure complete conversion.
Post-Polymerization Treatment : The latex is demulsified using calcium chloride solution, followed by filtration and washing to neutral pH, and drying to obtain the final copolymer.
Graft Copolymer Preparation (Butyl acrylate-styrene-acrylonitrile)
A more complex preparation involves graft copolymers with acrylonitrile, where:
Core monomers (e.g., butyl acrylate) and shell monomers (styrene, acrylonitrile) are polymerized sequentially in a reactor under stirring with emulsifiers and initiators.
Crosslinking agents like butanediol diacrylate or divinylbenzene are added to control polymer network.
The process involves controlled temperature (85–90 °C) and demulsification steps similar to emulsion polymerization.
Detailed Reaction Parameters and Data
Parameter | Typical Range / Condition | Notes |
---|---|---|
Monomer Purity | >99% | Removal of inhibitors essential |
Initiator | Benzoyl peroxide, potassium persulfate | Radical initiators |
Emulsifier Concentration | 1–5 wt% relative to monomers | Controls particle size |
Temperature | 50–90 °C | Optimal for radical polymerization |
Pressure | Atmospheric to slight overpressure (N2 blanket) | To avoid oxygen inhibition |
Monomer Ratio (Butyl Acrylate:Styrene) | 30:70 to 70:30 (wt%) | Adjusted for desired mechanical properties |
Reaction Time | 6–8 hours | Ensures high conversion |
pH during Neutralization | 9–12 | To remove organic acid catalysts |
Demulsification Agent | 1–2% Calcium chloride aqueous solution | For latex breaking |
Research Findings and Optimization Insights
Monomer Ratio Effect : Increasing styrene content improves rigidity and chemical resistance, whereas higher butyl acrylate content enhances flexibility and elongation at break.
Initiator Concentration : Excessive initiator leads to lower molecular weight and broader molecular weight distribution, affecting mechanical properties.
Crosslinking : Incorporation of crosslinkers in graft copolymers improves thermal stability and solvent resistance but reduces elongation.
Reaction Control : Maintaining strict temperature and pH control during polymerization and neutralization steps is critical for polymer quality and yield.
Summary Table of Preparation Methods
Method | Description | Advantages | Limitations |
---|---|---|---|
β-Propiolactone Method (Butyl Acrylate) | Ketene pyrolysis and reaction with alcohols | High purity product | High temperature required |
Acrylonitrile Hydrolysis | Hydrolysis and esterification of acrylonitrile | Uses abundant raw materials | Multi-step process |
Repee Method (Acetylene Carbonylation) | Reaction of acetylene, CO, and alcohols | Direct synthesis route | Requires specialized catalysts |
Propylene Direct Oxidation | Catalytic oxidation of propylene with alcohol | Latest industrial method | Catalyst sensitivity |
Emulsion Polymerization (Copolymer) | Radical polymerization of purified monomers | Good control over polymer properties | Requires surfactants and initiators |
Chemical Reactions Analysis
Radical Polymerization
Butyl acrylate-styrene copolymer forms via free radical polymerization. Typical conditions involve:
Initiator | Temperature (°C) | Solvent | Reaction Time (h) | Molecular Weight (kDa) |
---|---|---|---|---|
Benzoyl peroxide | 60–80 | Bulk/Emulsion | 4–12 | 50–500 |
AIBN | 70–90 | Toluene | 6–18 | 100–600 |
The styrene moiety enhances rigidity, while butyl acrylate imparts flexibility, enabling tunable glass transition temperatures () between −45°C (pure butyl acrylate) and 100°C (pure polystyrene) .
Copolymer Composition Effects
Varying monomer ratios significantly influence polymer properties:
Butyl Acrylate (%) | Styrene (%) | (°C) | Tensile Strength (MPa) | Applications |
---|---|---|---|---|
70 | 30 | −20 | 1.5 | Pressure-sensitive adhesives |
50 | 50 | 25 | 12.0 | Coatings, films |
30 | 70 | 60 | 30.0 | Structural plastics |
Data adapted from copolymer studies .
Crosslinking Reactions
The copolymer undergoes crosslinking to enhance thermal stability:
-
Peroxide-Induced Crosslinking : Dicumyl peroxide (1–5 wt%) at 160–180°C forms covalent bonds between polymer chains, increasing decomposition temperature by 40–60°C .
-
Radiation Crosslinking : Gamma irradiation (50–200 kGy) creates free radicals that recombine into crosslinks, improving solvent resistance .
Functionalization
The ester group in butyl acrylate allows nucleophilic substitution:
Reagent | Conditions | Product | Application |
---|---|---|---|
Ammonia | 80°C, 24 h | Acrylamide-styrene copolymer | Hydrogel matrices |
Ethylene diamine | Reflux, THF, 12 h | Amine-functionalized copolymer | Ion-exchange resins |
Thermal Degradation
Thermogravimetric analysis (TGA) reveals two-stage degradation:
-
Butyl Acrylate Segment : Degrades at 200–350°C via ester cleavage, releasing butanol and acrylic acid .
-
Styrene Segment : Degrades at 350–450°C through random scission, yielding styrene monomers and oligomers .
Hydrolytic Degradation
In alkaline conditions (pH > 10), ester hydrolysis occurs:
This reaction is accelerated at elevated temperatures (80°C), with half-life reduced from 200 h (pH 7) to 2 h (pH 12) .
Comparative Reactivity with Analogous Copolymers
Copolymer System | Key Reaction Differences | Stability (vs. Butyl Acrylate-Styrene) |
---|---|---|
Methyl Acrylate-Styrene | Faster hydrolysis due to less steric hindrance | Lower thermal stability (−10%) |
Butyl Acrylate-Acrylonitrile | Nitrile groups resist hydrolysis | Higher chemical resistance (+25%) |
Ethyl Acrylate-Styrene | Intermediate and degradation kinetics | Comparable |
Scientific Research Applications
Coatings and Paints
Butyl prop-2-enoate; styrene copolymers are extensively used in the coatings industry due to their excellent adhesion, flexibility, and weather resistance. They are ideal for:
- Architectural Coatings : Provide durability and aesthetic appeal.
- Automotive Paints : Offer protection against environmental factors.
Case Study : A study demonstrated that coatings formulated with butyl prop-2-enoate; styrene exhibited superior scratch resistance compared to traditional formulations, making them suitable for high-performance applications .
Adhesives
The adhesive properties of butyl prop-2-enoate; styrene make it a popular choice in the production of:
- Pressure-Sensitive Adhesives (PSAs) : Used in tapes and labels.
- Structural Adhesives : Employed in automotive and construction industries.
Data Table: Adhesive Performance Comparison
Type of Adhesive | Tensile Strength (MPa) | Elongation at Break (%) | Application Area |
---|---|---|---|
Butyl Acrylate | 20 | 300 | Tapes |
Styrene Copolymer | 25 | 250 | Structural Bonds |
This table illustrates the enhanced performance characteristics of adhesives based on butyl prop-2-enoate; styrene compared to traditional options.
Textiles
In textile applications, butyl prop-2-enoate; styrene is used for:
- Fabric Coatings : Improves water resistance and durability.
- Textile Finishing Agents : Enhances softness and drape.
Case Study : A textile manufacturer reported a significant increase in water repellency when using a coating based on butyl prop-2-enoate; styrene compared to standard acrylic coatings .
Plastics and Synthetic Fibers
The incorporation of butyl prop-2-enoate into plastic formulations enhances:
- Impact Resistance : Ideal for consumer goods and automotive parts.
- Thermal Stability : Suitable for high-temperature applications.
Data Table: Polymer Properties Comparison
Polymer Type | Impact Resistance (kJ/m²) | Thermal Stability (°C) |
---|---|---|
Standard Acrylic | 5 | 80 |
Butyl Prop-2-enoate/Styrene | 10 | 120 |
This comparison highlights the superior mechanical properties of polymers modified with butyl prop-2-enoate; styrene.
Environmental Considerations
While butyl prop-2-enoate; styrene offers numerous advantages, it is essential to consider its environmental impact. The compound is flammable and requires careful handling during production and application processes . Ongoing research aims to develop greener alternatives or methods to mitigate its environmental footprint.
Mechanism of Action
The mechanism of action of Butyl prop-2-enoate;styrene involves the formation of a polymer network through the polymerization of butyl acrylate and styrene monomers. The polymerization process creates a three-dimensional network of polymer chains, which imparts the material with its unique mechanical and chemical properties. The molecular targets and pathways involved in this process include the initiation, propagation, and termination steps of free radical polymerization .
Comparison with Similar Compounds
Chemical and Physical Properties
Table 1: Key Properties of Butyl Acrylate, Styrene, and Comparable Compounds
Compound | Molecular Formula | Boiling Point (°C) | Solubility in Water | Key Applications |
---|---|---|---|---|
Butyl acrylate | C₇H₁₂O₂ | 145–149 | 0.2 g/100 mL | Coatings, adhesives, plastics |
Styrene | C₈H₈ | 145–146 | 0.03 g/100 mL | Polystyrene, rubber, copolymers |
Methyl acrylate | C₄H₆O₂ | 80 | 5.2 g/100 mL | Textiles, adhesives |
Ethyl acrylate | C₅H₈O₂ | 99–101 | 1.5 g/100 mL | Paints, latexes |
Trimethylolpropane Triacrylate (TMPTA) | C₁₅H₂₀O₆ | >300 (decomposes) | Insoluble | UV-curable coatings, adhesives |
Butyl acrylate exhibits higher hydrophobicity compared to methyl and ethyl acrylates, making it suitable for water-resistant coatings. Styrene’s low water solubility and aromatic structure contribute to its rigidity in polymers. TMPTA, a trifunctional acrylate, offers superior crosslinking efficiency but requires specialized curing methods .
Polymerization Behavior
Table 2: Polymerization Characteristics
Compound | Polymerization Method | Reaction Efficiency | Polydispersity Index (PDI) |
---|---|---|---|
Butyl acrylate | NMP with BlocBuilder MA | High (90%+ conversion) | 1.2–1.4 |
Styrene | NMP with BlocBuilder MA | Moderate (70–80%) | 1.3–1.5 |
Methyl acrylate | Conventional free radical | Moderate | 1.5–2.0 |
TMPTA | UV-initiated radical | Fast curing | <1.5 |
Butyl acrylate and styrene show improved polymerization efficiency in continuous flow reactors due to rapid mixing and temperature control. Additives like acetonitrile or malononitrile accelerate butyl acrylate’s NMP while maintaining low PDI . Styrene’s slower polymerization in NMP systems is attributed to its lower radical stability compared to acrylates.
Copolymer Performance
Butyl acrylate-styrene copolymers are widely used for their balanced flexibility and strength. For example:
- Styrene-butyl acrylate-acrylic acid terpolymers exhibit enhanced adhesion and weather resistance in coatings .
- Gradient copolymers (e.g., butyl acrylate/acrylic acid) demonstrate superior self-assembly in solution compared to block copolymers, enabling tailored nanostructures .
In contrast, methyl methacrylate-styrene copolymers prioritize optical clarity and rigidity, as seen in automotive components .
Q & A
Basic Research Questions
Q. What are the optimal methods for synthesizing butyl prop-2-enoate-styrene copolymers with controlled molecular weight distributions?
- Methodological Answer : Use nitroxide-mediated polymerization (NMP) with BlocBuilder MA as an initiator in continuous flow reactors. This approach enhances conversion rates and reduces polydispersity indices (PDI) compared to batch reactors. Additives like α-hydroxy ketones or methyl-substituted compounds further accelerate polymerization while maintaining low PDIs. Monitor reaction parameters (temperature, flow rate) to optimize molecular weight control .
Q. How can spectroscopic techniques confirm copolymer composition and structural integrity?
- Methodological Answer : Employ nuclear magnetic resonance (NMR) to analyze monomer incorporation ratios and sequence distribution. Fourier-transform infrared spectroscopy (FTIR) identifies functional groups (e.g., ester linkages in butyl prop-2-enoate). Cross-validate with gel permeation chromatography (GPC) for molecular weight data. For crystalline domains, X-ray diffraction (XRD) paired with SHELX software refines crystal structure models .
Q. What experimental approaches determine the thermal stability and decomposition kinetics of butyl prop-2-enoate-styrene copolymers?
- Methodological Answer : Use thermogravimetric analysis (TGA) under nitrogen/air atmospheres to assess decomposition temperatures. Differential scanning calorimetry (DSC) measures glass transition temperatures (Tg) and phase transitions. Apply the Flynn-Wall-Ozawa method to calculate activation energies for degradation. Compare results with atomistic simulations of bond dissociation energies .
Q. How do researchers characterize self-assembly behavior in butyl prop-2-enoate-styrene copolymers?
- Methodological Answer : Utilize small-angle neutron scattering (SANS) to study micelle formation in selective solvents. Dynamic light scattering (DLS) measures hydrodynamic radii of self-assembled structures. Pair with coarse-grained molecular dynamics (CG-MD) simulations (e.g., bead-spring models) to predict aggregation patterns and compare with experimental data .
Q. What protocols ensure reproducibility in copolymer synthesis across different laboratories?
- Methodological Answer : Standardize monomer purification (e.g., inhibitor removal via alumina columns), initiator concentrations, and reaction temperatures. Document solvent quality (e.g., n-dodecane purity) and degassing procedures. Use interlaboratory comparisons with shared reference materials to validate protocols .
Advanced Research Questions
Q. How can contradictions between simulation predictions and experimental data in copolymer studies be resolved?
- Methodological Answer : Conduct multiscale modeling: first, validate coarse-grained simulations (e.g., bead-spring models) against neutron scattering data, then refine with atomistic simulations. Adjust force fields to match experimental Tg or density values. Use Bayesian inference to quantify uncertainties in model parameters .
Q. What strategies optimize surface adsorption of butyl prop-2-enoate-styrene copolymers for coating applications?
- Methodological Answer : Simulate adsorption kinetics using CG-MD with varied surface interaction strengths and temperatures. Experimentally validate via quartz crystal microbalance (QCM-D) to measure mass uptake. Correlate adsorption efficiency with copolymer architecture (block vs gradient) and solvent selectivity .
Q. How do architectural variations (block vs gradient copolymers) impact mechanical properties?
- Methodological Answer : Synthesize gradient copolymers via controlled radical polymerization and compare with block copolymers. Test tensile strength and elasticity using dynamic mechanical analysis (DMA). Model stress-strain behavior with finite element analysis (FEA) informed by monomer sequence data .
Q. What advanced techniques accelerate polymerization while maintaining low PDIs?
- Methodological Answer : Combine flow chemistry with microwave-assisted polymerization. Use in-line FTIR or Raman spectroscopy for real-time monitoring. Optimize initiator/accelerator ratios (e.g., BlocBuilder MA with cyano compounds) to reduce reaction times without broadening molecular weight distributions .
Q. How can biocompatibility of butyl prop-2-enoate-styrene hydrogels be systematically evaluated?
- Methodological Answer : Perform cytotoxicity assays (e.g., MTT) with fibroblast cell lines. Assess degradation profiles in simulated physiological conditions (pH 7.4, 37°C). Use confocal microscopy to study cell adhesion on copolymer surfaces. Validate with in vivo models for inflammation response .
Properties
CAS No. |
25767-47-9 |
---|---|
Molecular Formula |
C15H20O2 |
Molecular Weight |
232.32 g/mol |
IUPAC Name |
butyl prop-2-enoate;styrene |
InChI |
InChI=1S/C8H8.C7H12O2/c1-2-8-6-4-3-5-7-8;1-3-5-6-9-7(8)4-2/h2-7H,1H2;4H,2-3,5-6H2,1H3 |
InChI Key |
TUZBYYLVVXPEMA-UHFFFAOYSA-N |
SMILES |
CCCCOC(=O)C=C.C=CC1=CC=CC=C1 |
Canonical SMILES |
CCCCOC(=O)C=C.C=CC1=CC=CC=C1 |
Key on ui other cas no. |
25767-47-9 |
Origin of Product |
United States |
Synthesis routes and methods I
Procedure details
Synthesis routes and methods II
Procedure details
Synthesis routes and methods III
Procedure details
Synthesis routes and methods IV
Procedure details
Synthesis routes and methods V
Procedure details
Disclaimer and Information on In-Vitro Research Products
Please be aware that all articles and product information presented on BenchChem are intended solely for informational purposes. The products available for purchase on BenchChem are specifically designed for in-vitro studies, which are conducted outside of living organisms. In-vitro studies, derived from the Latin term "in glass," involve experiments performed in controlled laboratory settings using cells or tissues. It is important to note that these products are not categorized as medicines or drugs, and they have not received approval from the FDA for the prevention, treatment, or cure of any medical condition, ailment, or disease. We must emphasize that any form of bodily introduction of these products into humans or animals is strictly prohibited by law. It is essential to adhere to these guidelines to ensure compliance with legal and ethical standards in research and experimentation.