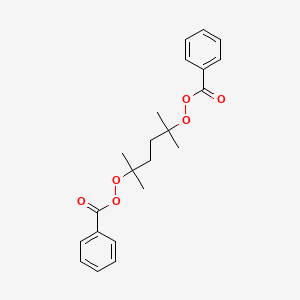
2,5-Dimethyl-2,5-di(benzoylperoxy)hexane
Overview
Description
2,5-Dimethyl-2,5-di(benzoylperoxy)hexane (CAS RN: 2618-77-1) is an organic peroxide with the molecular formula C₂₂H₂₆O₆ and a molecular weight of 386.444 g/mol . It is structurally characterized by two benzoylperoxy groups attached to a 2,5-dimethylhexane backbone. This compound is widely used as a crosslinking agent in polymer chemistry, particularly for medical rubber parts, fluororubbers, and high-temperature vulcanization systems . Its low thermal expansion hazard (rated "Low" under UN testing criteria) distinguishes it from other peroxides .
Scientific Research Applications
Polymer Curing Agent
DBPH serves as an effective curing agent for various polymers, particularly in the production of thermoset plastics and elastomers. It facilitates crosslinking reactions that enhance the mechanical properties of materials.
Applications include :
- Curing silicone rubbers
- Crosslinking polyethylene (PE), ethylene-propylene diene monomer (EPDM), and other elastomers
- Producing thermoset composites and acrylics
Polymerization Initiator
As a radical initiator, DBPH initiates free radical polymerization processes essential for producing high-performance polymers.
Key uses :
- Initiating polymerization in styrene and other vinyl monomers
- Controlling the rheology of polypropylene (PP) to achieve desired melt flow indices (MFI)
Degradation Agent
DBPH is also used to degrade polypropylene, providing flexibility in modifying polymer properties.
Benefits :
- Allows producers to control MFI by adjusting peroxide concentration and processing temperature.
Advantages of Using DBPH
- Versatility : Effective across various polymer systems.
- Efficiency : Facilitates rapid curing processes, reducing production time.
- Non-Tacky Surfaces : Cured products exhibit minimal tackiness, enhancing usability in applications requiring clean surfaces.
Case Study 1: Curing Silicone Rubbers
A study demonstrated that using DBPH as a curing agent for silicone rubbers resulted in significantly improved tensile strength and elasticity compared to traditional curing agents. The cured rubber showed enhanced resistance to heat and aging, making it suitable for automotive and aerospace applications.
Case Study 2: Polypropylene Processing
In another investigation, DBPH was utilized in the production of controlled rheology polypropylene (CR-PP). By varying the concentration of DBPH during processing, manufacturers achieved tailored MFI values that met specific processing requirements for injection molding applications.
Data Table: Comparative Analysis of Curing Agents
Property | DBPH | Traditional Agents |
---|---|---|
Curing Temperature | Moderate (185 °C) | Higher (200 °C - 250 °C) |
Surface Tackiness | Low | Moderate |
Mechanical Strength | High | Variable |
Processing Time | Short | Longer |
Safety and Handling Considerations
DBPH is sensitive to temperature increases and contamination, which can lead to violent decomposition. It should be stored under controlled conditions away from strong oxidizers and reducing agents. Proper safety protocols must be followed during handling to prevent accidents.
Q & A
Basic Questions
Q. How is 2,5-dimethyl-2,5-di(benzoylperoxy)hexane structurally characterized, and what analytical methods confirm its identity?
- Structural identifiers : Molecular formula C₂₂H₂₆O₆ , average mass 386.44 g/mol , and IUPAC name 2,5-dimethylhexane-2,5-diyl dibenzenecarboperoxoate .
- Analytical methods :
- Nuclear Magnetic Resonance (NMR) : Confirm peroxide linkage and aromatic protons from benzoyl groups.
- Fourier-Transform Infrared Spectroscopy (FTIR) : Detect O-O stretching (~800 cm⁻¹) and carbonyl (C=O) peaks (~1700 cm⁻¹).
- Gas Chromatography (GC) : Assess purity (>90%) by comparing retention times against standards .
Q. What safety protocols are critical when handling this compound in laboratory settings?
- Hazard classification : Classified under UN 3106 (Organic Peroxide, Type E) with GHS hazard statements for skin irritation and fire risk .
- Handling recommendations :
- Store at 0–30°C in inert, airtight containers to prevent decomposition .
- Avoid contact with reducing agents, acids, or heavy metals to prevent unintended radical initiation .
- Use personal protective equipment (PPE): nitrile gloves, lab coat, and eye protection .
Q. What are the solubility properties, and how do they influence reaction solvent selection?
- Solubility : Immiscible in water but soluble in organic solvents (e.g., alcohols, dichloromethane) .
- Methodological guidance : Pre-dissolve in non-polar solvents (e.g., hexane) for homogeneous radical initiation in polymer matrices. For polar systems, use co-solvents like tetrahydrofuran (THF) .
Advanced Research Questions
Q. How can researchers optimize crosslinking efficiency in polymer blends using this peroxide?
- Experimental design :
- Concentration gradients : Test 0.1–1.0 wt% in polymer matrices (e.g., polyethylene, silicone rubber). Higher concentrations (>0.5%) may reduce ductility due to over-crosslinking .
- Temperature control : Use a stepwise curing profile (e.g., 135°C for initiation, 175°C for crosslinking) to balance radical generation and stability .
- Post-curing analysis : Measure tensile strength, elongation at break, and dynamic mechanical analysis (DMA) to quantify crosslink density .
Q. How do thermal decomposition kinetics impact its application in controlled rheology polypropylene (CR-PP)?
- Key parameters :
- Half-life : Critical for determining processing windows (e.g., 1 min at 185°C for rapid degradation) .
- Melt Flow Index (MFI) : Adjust peroxide concentration (0.01–0.1%) to achieve target MFI values. Excessive peroxide degrades polymer chains, reducing molecular weight .
Q. What mechanisms explain conflicting data on radical scavenging effects in styrene polymerization?
- Hypothesis testing :
- Residual monomer analysis : Use HPLC to quantify styrene conversion. Higher peroxide loads (>0.2%) may prematurely terminate chains, increasing residual monomer .
- Radical trapping experiments : Introduce inhibitors (e.g., TEMPO) to differentiate between primary initiation and secondary scavenging pathways .
Comparison with Similar Compounds
Structural and Functional Group Differences
The primary structural distinction lies in the substituent groups:
- 2,5-Dimethyl-2,5-di(benzoylperoxy)hexane : Benzoylperoxy (–O–O–CO–C₆H₅) groups.
- 2,5-Dimethyl-2,5-di(tert-butylperoxy)hexane (CAS RN: 78-63-7): tert-Butylperoxy (–O–O–C(CH₃)₃) groups .
- 2,5-Dimethyl-2,5-di(tert-butylperoxy)hexyne-3 (CAS RN: 1068-27-5): tert-Butylperoxy groups with a triple bond in the hexane chain .
These structural variations significantly influence reactivity, thermal stability, and application suitability.
Thermal Stability and Reactivity
Key Findings :
- The benzoylperoxy derivative exhibits lower thermal hazard but comparable crosslinking efficiency in medical rubber applications .
- tert-Butylperoxy compounds (e.g., CAS 78-63-7) are less volatile and more stable than dicumyl peroxide (DCP), making them suitable for high-temperature vulcanization of silicones and polypropylene .
- The hexyne-3 variant’s triple bond enhances radical generation efficiency, favoring applications requiring rapid crosslinking .
Preparation Methods
Conventional Preparation Methods for Related Peroxides
A traditional method for preparing di-tert-butylperoxy derivatives involves a two-step process starting from 2,5-dimethyl-hexane-2,5-diol:
- Step 1: Conversion of 2,5-dimethyl-hexane-2,5-diol to the corresponding dihydroperoxide by reaction with hydrogen peroxide in a strongly acidic medium.
- Step 2: Further reaction of the dihydroperoxide with an alcohol (e.g., t-butanol) in a strong acid medium to form the di-tert-butylperoxy compound.
This method, however, has significant drawbacks:
- Moderate yields (60–65%)
- Long processing times
- Formation of solid dihydroperoxide intermediates posing safety risks
- Generation of large volumes of acidic wastewater and cleaning solutions
- Production of unwanted by-products requiring complex purification steps such as distillation
These limitations make the conventional process unsuitable for industrial-scale manufacture due to safety and environmental concerns.
Improved Preparation Method Using Lewis Acid Catalysis in Anhydrous Medium
Recent patented processes for related peroxides, including 2,5-dimethyl-2,5-di-tert-butylperoxyhexane, provide a more efficient and safer alternative that could be adapted for 2,5-dimethyl-2,5-di(benzoylperoxy)hexane. The key features of this method are:
- Starting Materials: 2,5-dimethyl-1,5-hexadiene and a hydroperoxide reagent (e.g., t-butyl hydroperoxide for tert-butyl derivatives, benzoyl peroxide or benzoyl hydroperoxide analogs for benzoyl derivatives).
- Catalyst: A Lewis acid acting as an electron pair acceptor, facilitating the peroxide formation.
- Reaction Medium: A completely anhydrous solvent environment to prevent side reactions and decomposition.
- Reaction Conditions: Controlled temperatures between -10 °C and +50 °C, preferably 0 °C to 30 °C.
- Molar Ratios: Hydroperoxide used in molar excess (2 to 6 moles per mole of hexadiene, typically 3 to 4 moles).
- Catalyst Loading: Lewis acid catalyst used in 0.1 to 0.5 mole per mole of hexadiene.
This method offers several advantages:
- Higher yields with good product quality
- Shorter reaction times
- Reduced formation of by-products
- Safer handling due to anhydrous conditions and controlled catalyst use
- Environmentally friendlier with less acidic waste
Although this patented method specifically describes tert-butyl peroxy derivatives, the principles are applicable to the preparation of this compound by substituting the hydroperoxide source accordingly.
Specific Considerations for this compound
- Hydroperoxide Source: For benzoyl peroxy derivatives, benzoyl peroxide or benzoyl hydroperoxide analogs are employed instead of t-butyl hydroperoxide.
- Reaction Control: Due to the higher molecular weight (386.48 g/mol) and different reactivity profile compared to tert-butyl analogs, reaction parameters such as temperature and catalyst concentration may require optimization.
- Safety: Organic peroxides like this compound have a self-accelerating decomposition temperature (SADT) around 69 °C, necessitating careful temperature control during synthesis and storage.
- Purification: Post-reaction purification typically involves washing to remove residual acids and unreacted starting materials, followed by distillation or recrystallization to isolate the pure peroxide.
Summary Table of Preparation Parameters
Parameter | Conventional Method | Lewis Acid Catalyzed Method (Improved) |
---|---|---|
Starting Material | 2,5-dimethyl-hexane-2,5-diol | 2,5-dimethyl-1,5-hexadiene |
Hydroperoxide Source | Hydrogen peroxide + alcohol (e.g., t-butanol) | Hydroperoxide (e.g., benzoyl hydroperoxide) |
Catalyst | Strong acid medium | Lewis acid (electron pair acceptor) |
Solvent | Aqueous acidic medium | Anhydrous solvent |
Temperature Range | Ambient to elevated | -10 °C to +50 °C (preferably 0 °C to 30 °C) |
Reaction Time | Long (hours) | Short (minutes to hours) |
Yield | 60–65% | Higher yields, typically >75% |
Safety | Formation of solid intermediates, acidic waste | Safer due to anhydrous conditions and less waste |
By-products | Significant, difficult to remove | Reduced by-products, easier purification |
Research Findings and Industrial Implications
- The Lewis acid catalyzed method represents a significant advancement in the preparation of sensitive organic peroxides, including this compound.
- The use of anhydrous solvents and electron pair acceptor catalysts reduces side reactions and enhances yield and purity.
- Industrial scale-up benefits from shorter reaction times and reduced environmental impact.
- Safety protocols must still be rigorously applied given the thermal sensitivity of organic peroxides.
Properties
CAS No. |
2618-77-1 |
---|---|
Molecular Formula |
C22H26O6 |
Molecular Weight |
386.4 g/mol |
IUPAC Name |
(5-benzoylperoxy-2,5-dimethylhexan-2-yl) benzenecarboperoxoate |
InChI |
InChI=1S/C22H26O6/c1-21(2,27-25-19(23)17-11-7-5-8-12-17)15-16-22(3,4)28-26-20(24)18-13-9-6-10-14-18/h5-14H,15-16H2,1-4H3 |
InChI Key |
RIPYNJLMMFGZSX-UHFFFAOYSA-N |
SMILES |
CC(C)(CCC(C)(C)OOC(=O)C1=CC=CC=C1)OOC(=O)C2=CC=CC=C2 |
Canonical SMILES |
CC(C)(CCC(C)(C)OOC(=O)C1=CC=CC=C1)OOC(=O)C2=CC=CC=C2 |
Key on ui other cas no. |
2618-77-1 |
physical_description |
This solid peroxide is particularly sensitive to temperature rises and contamination. Above a given "Control Temperature" they decompose violently. It is generally stored or transported as a mixture, with an inert solid. |
Pictograms |
Explosive; Flammable |
Origin of Product |
United States |
Retrosynthesis Analysis
AI-Powered Synthesis Planning: Our tool employs the Template_relevance Pistachio, Template_relevance Bkms_metabolic, Template_relevance Pistachio_ringbreaker, Template_relevance Reaxys, Template_relevance Reaxys_biocatalysis model, leveraging a vast database of chemical reactions to predict feasible synthetic routes.
One-Step Synthesis Focus: Specifically designed for one-step synthesis, it provides concise and direct routes for your target compounds, streamlining the synthesis process.
Accurate Predictions: Utilizing the extensive PISTACHIO, BKMS_METABOLIC, PISTACHIO_RINGBREAKER, REAXYS, REAXYS_BIOCATALYSIS database, our tool offers high-accuracy predictions, reflecting the latest in chemical research and data.
Strategy Settings
Precursor scoring | Relevance Heuristic |
---|---|
Min. plausibility | 0.01 |
Model | Template_relevance |
Template Set | Pistachio/Bkms_metabolic/Pistachio_ringbreaker/Reaxys/Reaxys_biocatalysis |
Top-N result to add to graph | 6 |
Feasible Synthetic Routes
Disclaimer and Information on In-Vitro Research Products
Please be aware that all articles and product information presented on BenchChem are intended solely for informational purposes. The products available for purchase on BenchChem are specifically designed for in-vitro studies, which are conducted outside of living organisms. In-vitro studies, derived from the Latin term "in glass," involve experiments performed in controlled laboratory settings using cells or tissues. It is important to note that these products are not categorized as medicines or drugs, and they have not received approval from the FDA for the prevention, treatment, or cure of any medical condition, ailment, or disease. We must emphasize that any form of bodily introduction of these products into humans or animals is strictly prohibited by law. It is essential to adhere to these guidelines to ensure compliance with legal and ethical standards in research and experimentation.