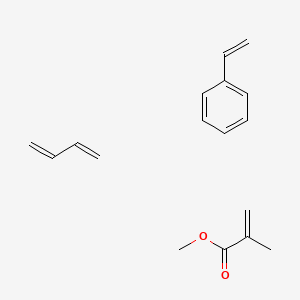
Buta-1,3-diene;methyl 2-methylprop-2-enoate;styrene
Overview
Description
Buta-1,3-diene;methyl 2-methylprop-2-enoate;styrene is a complex polymer that combines the properties of its constituent monomers. This polymer is known for its versatility and is used in various industrial applications due to its unique chemical and physical properties.
Preparation Methods
Synthetic Routes and Reaction Conditions
The polymerization of 2-Propenoic acid, 2-methyl-, methyl ester with 1,3-butadiene and ethenylbenzene typically involves free radical polymerization. The reaction is initiated by free radicals generated from initiators such as benzoyl peroxide or azobisisobutyronitrile (AIBN). The polymerization process can be carried out in bulk, solution, or emulsion, depending on the desired properties of the final product.
Industrial Production Methods
In industrial settings, the polymerization is often conducted in large reactors where the monomers are mixed with the initiator and other additives. The reaction conditions, such as temperature and pressure, are carefully controlled to ensure a consistent product. Emulsion polymerization is commonly used for large-scale production as it allows for better control over the molecular weight distribution and particle size of the polymer.
Chemical Reactions Analysis
Types of Reactions
Buta-1,3-diene;methyl 2-methylprop-2-enoate;styrene can undergo various chemical reactions, including:
Oxidation: The polymer can be oxidized using strong oxidizing agents, leading to the formation of carbonyl and carboxyl groups.
Reduction: Reduction reactions can be carried out using reducing agents like lithium aluminum hydride, which can reduce carbonyl groups to alcohols.
Substitution: The polymer can undergo substitution reactions where functional groups on the polymer chain are replaced with other groups.
Common Reagents and Conditions
Oxidation: Potassium permanganate or chromium trioxide in acidic conditions.
Reduction: Lithium aluminum hydride or sodium borohydride in anhydrous conditions.
Substitution: Halogenation using chlorine or bromine in the presence of a catalyst.
Major Products Formed
Oxidation: Formation of carbonyl and carboxyl groups.
Reduction: Formation of alcohol groups.
Substitution: Formation of halogenated polymers.
Scientific Research Applications
Buta-1,3-diene;methyl 2-methylprop-2-enoate;styrene has a wide range of applications in scientific research:
Chemistry: Used as a precursor for the synthesis of other polymers and copolymers.
Biology: Employed in the development of biocompatible materials for medical devices and drug delivery systems.
Medicine: Utilized in the formulation of dental materials and prosthetics due to its biocompatibility and mechanical properties.
Industry: Applied in the production of adhesives, coatings, and sealants due to its excellent adhesion properties and chemical resistance.
Mechanism of Action
The mechanism of action of this polymer involves the interaction of its functional groups with various molecular targets. The polymer can form hydrogen bonds, van der Waals interactions, and covalent bonds with other molecules, leading to its diverse range of applications. The pathways involved include the formation of cross-linked networks, which enhance the mechanical strength and chemical resistance of the material.
Comparison with Similar Compounds
Similar Compounds
Polymethyl methacrylate (PMMA): A polymer of 2-Propenoic acid, 2-methyl-, methyl ester without the incorporation of 1,3-butadiene and ethenylbenzene.
Styrene-butadiene rubber (SBR): A copolymer of 1,3-butadiene and ethenylbenzene without the incorporation of 2-Propenoic acid, 2-methyl-, methyl ester.
Uniqueness
Buta-1,3-diene;methyl 2-methylprop-2-enoate;styrene combines the properties of its constituent monomers, resulting in a material with enhanced mechanical strength, chemical resistance, and versatility. This makes it unique compared to other similar polymers, which may lack one or more of these properties.
Properties
CAS No. |
25053-09-2 |
---|---|
Molecular Formula |
C17H22O2 |
Molecular Weight |
258.35 g/mol |
IUPAC Name |
buta-1,3-diene;methyl 2-methylprop-2-enoate;styrene |
InChI |
InChI=1S/C8H8.C5H8O2.C4H6/c1-2-8-6-4-3-5-7-8;1-4(2)5(6)7-3;1-3-4-2/h2-7H,1H2;1H2,2-3H3;3-4H,1-2H2 |
InChI Key |
WWNGFHNQODFIEX-UHFFFAOYSA-N |
SMILES |
CC(=C)C(=O)OC.C=CC=C.C=CC1=CC=CC=C1 |
Canonical SMILES |
CC(=C)C(=O)OC.C=CC=C.C=CC1=CC=CC=C1 |
Key on ui other cas no. |
25053-09-2 |
Pictograms |
Irritant |
Origin of Product |
United States |
Synthesis routes and methods I
Procedure details
Synthesis routes and methods II
Procedure details
Synthesis routes and methods III
Procedure details
Synthesis routes and methods IV
Procedure details
Disclaimer and Information on In-Vitro Research Products
Please be aware that all articles and product information presented on BenchChem are intended solely for informational purposes. The products available for purchase on BenchChem are specifically designed for in-vitro studies, which are conducted outside of living organisms. In-vitro studies, derived from the Latin term "in glass," involve experiments performed in controlled laboratory settings using cells or tissues. It is important to note that these products are not categorized as medicines or drugs, and they have not received approval from the FDA for the prevention, treatment, or cure of any medical condition, ailment, or disease. We must emphasize that any form of bodily introduction of these products into humans or animals is strictly prohibited by law. It is essential to adhere to these guidelines to ensure compliance with legal and ethical standards in research and experimentation.