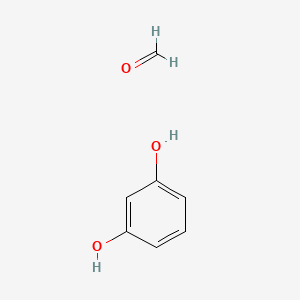
Resorcinol formaldehyde
Overview
Description
Resorcinol formaldehyde (RF) is a thermosetting polymer synthesized via polycondensation of resorcinol (C₆H₄(OH)₂) and formaldehyde (CH₂O). It is widely used as an ion-exchange resin for removing Cs-137 from alkaline liquid radioactive waste (LRW), owing to its high adsorption efficiency (>98%) and chemical stability under extreme conditions (pH 13, 210°C) . Key properties, such as mechanical strength and Cs selectivity, depend on the resorcinol/formaldehyde (R/F) molar ratio and curing temperature. For example, RF samples synthesized at an R/F ratio of 1.8/2.2 and cured at 210°C exhibit optimal performance, withstanding six adsorption cycles without degradation .
Preparation Methods
Overview of Resorcinol Formaldehyde Synthesis
The preparation of this compound involves the polymerization of resorcinol with formaldehyde under controlled conditions, typically catalyzed by acidic or basic catalysts. The process generally proceeds through a polycondensation reaction forming hydroxymethyl derivatives of resorcinol, which subsequently crosslink to form a three-dimensional polymer network.
Acid-Catalyzed Preparation Method
One documented method involves an acid-catalyzed polymerization process using a combination of acidic catalysts such as oxalic acid and p-toluenesulfonic acid. The procedure includes:
- Initial Fusion: Resorcinol is combined with a catalytic amount of acidic catalyst and heated to 110–120 °C to achieve fusion.
- Preliminary Polymerization: Under reflux at 110–130 °C, a portion of formaldehyde and a properties-correcting agent (such as vinylbenzene) are added dropwise over 20–30 minutes to initiate polymerization.
- Main Polymerization: The remaining formaldehyde and correcting agent are added at 100–120 °C under reflux to continue polymerization.
- Alkaline Treatment: After polymerization, an alkaline compound (e.g., sodium hydroxide) is added to adjust the pH and promote further crosslinking.
- Separation and Purification: The reaction mixture is allowed to stand for phase separation, followed by removal of the aqueous layer.
- Distillation: Under reduced pressure, the mixture is distilled at 125–150 °C to reduce water and residual monomers to low levels, yielding the final resin.
This method yields this compound resin with controlled softening temperatures (around 97.5–106.5 °C) and low moisture content (<0.5%).
Step | Conditions | Notes |
---|---|---|
Fusion | 110–120 °C | Resorcinol + acidic catalyst |
Preliminary polymerization | 110–130 °C, 20–30 min reflux | Partial formaldehyde and correcting agent |
Main polymerization | 100–120 °C, reflux | Remaining formaldehyde and correcting agent |
Alkaline addition | Ambient to reflux | Sodium hydroxide or other alkaline agent |
Phase separation | Standstill | Organic and aqueous layers separate |
Vacuum distillation | 125–150 °C, reduced pressure | Removes water and residual monomers |
Base-Catalyzed Preparation and Gelation
Another prevalent approach uses alkaline catalysts such as sodium carbonate or sodium hydroxide to catalyze the polycondensation of resorcinol and formaldehyde, often leading to gel formation:
- The reaction is typically carried out at moderate temperatures (40–80 °C).
- Sodium carbonate concentration and pH are critical parameters controlling reaction kinetics.
- The reaction proceeds in two stages: initial formation of small RF clusters (~7–10 nm) within the first 3 hours, followed by slower gelation through cluster crosslinking.
- The pH influences the formation of phenolate ions, which are more reactive toward formaldehyde, accelerating the polycondensation.
- The molar ratio of resorcinol to formaldehyde and catalyst concentration directly affect the gelation time, polymer structure, and final resin properties.
Effect of Resorcinol/Formaldehyde Ratio and Heat Treatment
The molar ratio of resorcinol to formaldehyde and the subsequent thermal solidification significantly impact the resin's chemical stability and sorption properties:
- A molar ratio close to 1.8:2.2 (resorcinol:formaldehyde) with solidification at around 210 °C produces resins with optimal sorption and chemical stability.
- Increasing the resorcinol/formaldehyde ratio tends to increase the degree of crosslinking, improving chemical resistance, especially in alkaline media.
- Heat treatment (solidification) at elevated temperatures enhances the polymer network's robustness and reduces degradation rates.
Alternative Preparation via Underpressure Distillation
A method described in patent literature involves:
- Mixing resorcinol, formaldehyde, and a basic compound (e.g., calcium hydroxide, sodium hydroxide) at 40–80 °C for 1–6 hours.
- Adjusting pH to 8–14 using basic fillers such as calcium oxide or magnesium oxide.
- Underpressure distillation at 30–50 °C and vacuum levels of -0.4 to -0.98 MPa to remove water and volatile impurities.
- This method allows control over resin viscosity (1500–2500 cP at 25 °C) and solid content (61–75%), yielding resins with tailored setting times and moisture contents.
Parameter | Range/Value | Effect/Outcome |
---|---|---|
Reaction temperature | 40–80 °C | Controls reaction rate and polymerization |
Reaction time | 1–6 hours | Influences degree of polymerization |
pH during distillation | 8–14 | Controls polymer stability and crosslinking |
Vacuum pressure | -0.4 to -0.98 MPa | Efficient removal of volatiles |
Viscosity (cP, 25 °C) | 1500–2500 | Indicates polymer molecular weight |
Solid content (%) | 61–75 | Higher solid content implies higher polymerization |
Formation of Hollow Nanostructures by Post-Synthesis Treatment
Recent research has demonstrated that this compound colloidal particles can undergo selective dissolution and regrowth in solvents such as ethanol or tetrahydrofuran, leading to hollow nanoshells with controllable shell thickness:
- The process exploits the structural heterogeneity of RF particles, where outer layers consist of longer chain oligomers and inner layers shorter chains.
- Selective etching removes the inner short-chain oligomers, creating hollow structures.
- Parameters such as condensation degree, etching time, temperature, and solvent composition allow precise control over morphology.
Summary Table of Key Preparation Methods
Research Findings and Analytical Insights
- The polymerization kinetics are strongly influenced by catalyst type and concentration, pH, temperature, and reactant ratios.
- Acidic catalysis typically requires higher temperatures and stepwise addition of reactants to control molecular weight and crosslinking density.
- Alkaline catalysis favors cluster formation and gelation at lower temperatures, with pH playing a critical role in polymer structure.
- Thermal solidification post-gelation enhances chemical stability and mechanical properties.
- Vacuum distillation under controlled pH conditions effectively removes residual monomers and water, improving resin purity and performance.
- Structural heterogeneity in RF polymers can be exploited for advanced nanostructure synthesis via selective etching.
This detailed analysis synthesizes diverse authoritative sources to provide a comprehensive understanding of the preparation methods of this compound, highlighting process parameters, catalyst roles, and advanced modifications for enhanced material properties.
Scientific Research Applications
Materials Science
1.1. Polymer Composites
RF resins are extensively used as adhesives and binders in composite materials. The polymer's ability to form strong cross-links makes it suitable for high-performance applications. For instance, RF resins have been incorporated into starch-based solid biopolymer electrolytes to enhance ionic conductivity and suppress crystallinity, which is critical for battery applications .
Table 1: Ionic Conductivity of Starch-Based Electrolytes with RF
Composition | Ionic Conductivity () |
---|---|
Starch:LiTf:RF (20:20:60) |
1.2. Aerogels
The polycondensation of resorcinol with formaldehyde leads to the formation of low-density organic aerogels. These aerogels exhibit unique properties such as transparency and low thermal conductivity, making them suitable for insulation and lightweight structural applications. They can also be carbonized to produce carbon foams with specific structural characteristics .
Table 2: Properties of Resorcinol-Formaldehyde Aerogels
Property | Value |
---|---|
Density | ≤ 100 mg/cc |
Cell Size | ≤ 0.1 microns |
Color | Dark red |
Dentistry
2.1. Endodontic Applications
Resorcinol formaldehyde has been historically used in endodontics, particularly in the treatment of complex root canal cases. It provides excellent sealing properties but poses challenges during retreatment due to its rigid nature once polymerized. A study evaluated the quality of retreatment using RF resin, finding that 90% of canal spaces were filled after retreatment, although some cases experienced flare-ups post-treatment .
Table 3: Quality Assessment After Retreatment
Outcome | Percentage (%) |
---|---|
Optimal obturation | 59 |
Improved obturation | 33 |
Unchanged | 6 |
Worse | 2 |
Environmental Remediation
3.1. Sorption Applications
RF resins have shown promise in environmental applications, particularly in the removal of heavy metals from wastewater. Research indicates that RF-derived materials can effectively sorb cesium and potassium ions from alkaline media, making them valuable for environmental cleanup efforts.
Table 4: Sorption Efficiency of RF Resins
Ion | (mL/g) | SEC (mmol/g) | Desorption Efficiency (%) |
---|---|---|---|
Cesium | 187 | 0.03 | 75 |
Potassium | 110 | 1.07 | 3.3 |
Mechanism of Action
The mechanism of action of formaldehyde, polymer with 1,3-benzenediol involves the formation of strong covalent bonds between the formaldehyde and the hydroxyl groups of 1,3-benzenediol. This results in a highly cross-linked polymer network that imparts the material with its characteristic thermal stability and chemical resistance .
Comparison with Similar Compounds
Phenol-Formaldehyde (PF) Resins
Synthesis & Structure: PF resins are synthesized from phenol and formaldehyde. Unlike RF, PF lacks the two hydroxyl groups of resorcinol, reducing its crosslinking density and ion-exchange capacity. Adsorption Performance: PF shows lower Cs-137 adsorption efficiency (70–85%) in alkaline media due to fewer active phenolic sites and weaker chemical stability . Chemical Stability: PF degrades above 200°C, whereas RF maintains stability up to 250°C before thermal oxidation occurs .
Table 1: RF vs. PF Resins
Property | RF Resin (R/F = 1.8/2.2) | PF Resin |
---|---|---|
Cs-137 Adsorption (%) | >98 | 70–85 |
Optimal Curing Temp (°C) | 210 | 150–180 |
Thermal Stability (°C) | ≤250 | ≤200 |
Alkaline Stability (pH) | 13 | ≤11 |
Polyacrylonitrile (PAN)-Based Adsorbents
Adsorption Mechanism : PAN composites rely on functional groups like sulfonic acid for ion exchange.
Performance : In high-salinity LRW (3–4.5 mol/L Na⁺), PAN’s Cs selectivity drops by 1–2 orders of magnitude compared to RF due to competitive ion interference .
Durability : PAN requires frequent regeneration, whereas RF retains >98% efficiency over six cycles .
Ferrocyanide-Based Adsorbents
Structure: Transition metal ferrocyanides (e.g., potassium cobalt hexacyanoferrate) trap Cs⁺ via lattice defects. Limitations: These materials dissolve in alkaline media (pH > 12), releasing toxic cyanide, making them unsuitable for LRW treatment .
Carbon Aerogels Derived from RF
Synthesis : RF aerogels are pyrolyzed to form carbon spheres with high surface areas (592–952 m²/g) .
Applications : Unlike RF resins, carbon aerogels excel in energy storage (specific capacitance: 17.5–33.5 F/g) but lack ion-exchange functionality for Cs removal .
Mechanistic Insights from Structural Analysis
NMR and FTIR Spectroscopy
- C-13 NMR : RF cured at 210°C shows peaks at 53.8 ppm (oxygen-containing bridges) and 153.5 ppm (aromatic carbons), confirming a crosslinked network .
- FTIR : Bands at 1440–1300 cm⁻¹ (OH bending) and 3700–3300 cm⁻¹ (hydrogen bonding) validate RF’s stability in alkaline conditions .
Adsorption Kinetics
RF follows the Sips isotherm model, with maximum Cs adsorption (Gmax) of 0.51 mmol/g in alkaline media. The high correlation coefficient (R² > 0.99) indicates monolayer adsorption on heterogeneous sites .
Table 2: Sips Isotherm Parameters for RF
Model Solution | Gmax (mmol/g) | K_SIPS |
---|---|---|
Solution 1 | 0.42 ± 0.04 | 1.8 ± 0.5 |
Solution 2 | 0.51 ± 0.01 | 2.1 ± 0.1 |
Q & A
Basic Research Questions
Q. How can resorcinol-formaldehyde resin synthesis parameters (e.g., pH, catalyst type, molar ratios) be systematically optimized for specific mechanical or structural properties?
Methodological Answer :
-
Use a design of experiments (DOE) approach to vary synthesis parameters (e.g., formaldehyde:resorcinol molar ratios, pH adjustments using NaOH/HCl, catalyst selection such as p-toluenesulfonic acid or sodium sulfite). Monitor outcomes like gelation time, crosslinking density, and thermal stability .
-
Example Table :
Q. What characterization techniques are essential for analyzing RF resin structure-property relationships?
Methodological Answer :
- FTIR/Raman spectroscopy : Identify functional groups (e.g., methylene bridges, aromatic rings) to confirm polymerization .
- Thermogravimetric analysis (TGA) : Assess thermal degradation patterns under inert atmospheres.
- Swelling tests : Quantify crosslinking density using solvent uptake ratios (e.g., equilibrium swelling in acetone) .
- SEM/TEM : Visualize pore morphology and nanostructure (critical for applications like carbon aerogels) .
Advanced Research Questions
Q. How can contradictions in crosslinking density measurements (e.g., swelling tests vs. DSC-derived values) be resolved in RF resin studies?
Methodological Answer :
- Triangulate data : Compare results from multiple methods (swelling, differential scanning calorimetry (DSC), and rheometry). For instance, swelling tests may underestimate crosslinking in highly porous RF due to solvent diffusion limitations, whereas DSC detects glass transition temperatures (Tg) influenced by crosslink density .
- Error analysis : Quantify uncertainties in each method (e.g., solvent evaporation in swelling tests, baseline drift in DSC) and apply statistical corrections .
Q. What statistical approaches are suitable for analyzing variance in RF gelation kinetics under dynamic environmental conditions?
Methodological Answer :
- Time-series ANOVA : Evaluate the impact of temperature fluctuations or humidity on gelation rates.
- Multivariate regression : Model interactions between variables (e.g., pH × catalyst concentration) using software like R or Python’s SciPy .
- Example Workflow :
Q. How can reproducibility challenges in RF-based carbon aerogel synthesis be addressed across laboratories?
Methodological Answer :
- Standardized protocols : Publish detailed synthesis steps (e.g., solvent purity, curing time, pyrolysis ramp rates) as per IUPAC guidelines .
- Interlaboratory validation : Share raw data (e.g., TGA curves, pore size distributions) via repositories like Zenodo to enable direct comparison .
- Critical parameters : Highlight variables with the highest sensitivity (e.g., formaldehyde purity, drying method) in supplementary materials .
Q. Data Presentation and Integrity
- Tables : Use APA-style formatting for processed data (e.g., mean ± SD for triplicate experiments). Place raw datasets in appendices .
- Figures : Label error bars clearly (standard deviation vs. standard error). For pore size distributions, include histograms with bin sizes <0.5 nm .
- Reproducibility : Archive experimental logs (e.g., pH meter calibration records, batch numbers) to meet FAIR data principles .
Properties
CAS No. |
24969-11-7 |
---|---|
Molecular Formula |
C7H8O3 |
Molecular Weight |
140.14 g/mol |
IUPAC Name |
benzene-1,3-diol;formaldehyde |
InChI |
InChI=1S/C6H6O2.CH2O/c7-5-2-1-3-6(8)4-5;1-2/h1-4,7-8H;1H2 |
InChI Key |
KVBYPTUGEKVEIJ-UHFFFAOYSA-N |
SMILES |
C=O.C1=CC(=CC(=C1)O)O |
Canonical SMILES |
C=O.C1=CC(=CC(=C1)O)O |
Key on ui other cas no. |
24969-11-7 |
Origin of Product |
United States |
Synthesis routes and methods I
Procedure details
Synthesis routes and methods II
Procedure details
Synthesis routes and methods III
Procedure details
Synthesis routes and methods IV
Procedure details
Synthesis routes and methods V
Procedure details
Disclaimer and Information on In-Vitro Research Products
Please be aware that all articles and product information presented on BenchChem are intended solely for informational purposes. The products available for purchase on BenchChem are specifically designed for in-vitro studies, which are conducted outside of living organisms. In-vitro studies, derived from the Latin term "in glass," involve experiments performed in controlled laboratory settings using cells or tissues. It is important to note that these products are not categorized as medicines or drugs, and they have not received approval from the FDA for the prevention, treatment, or cure of any medical condition, ailment, or disease. We must emphasize that any form of bodily introduction of these products into humans or animals is strictly prohibited by law. It is essential to adhere to these guidelines to ensure compliance with legal and ethical standards in research and experimentation.