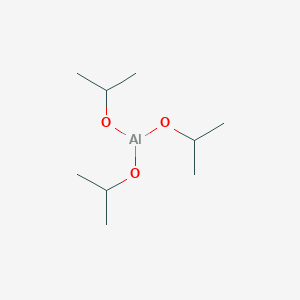
Aluminium isopropoxide
Overview
Description
Aluminium isopropoxide is a chemical compound with the formula Al(O-i-Pr)₃, where i-Pr represents the isopropyl group (–CH(CH₃)₂). This colourless solid is widely used as a reagent in organic synthesis. It is known for its utility in various chemical reactions, particularly in the reduction of ketones and aldehydes .
Mechanism of Action
Target of Action
Aluminium isopropoxide primarily targets ketones and aldehydes . It acts as a catalyst in the Meerwein-Ponndorf-Verley (MPV) reduction, where it facilitates the reduction of these compounds to their corresponding alcohols .
Mode of Action
The mode of action of this compound involves a catalytic cycle with a six-member ring transition state . Starting with the aluminium alkoxide, a carbonyl oxygen is coordinated to achieve a tetra-coordinated aluminium intermediate. The hydride is then transferred to the carbonyl from the alkoxy ligand via a pericyclic mechanism . At this point, the new carbonyl dissociates and gives a tri-coordinated aluminium species. Finally, an alcohol from the solution displaces the newly reduced carbonyl to regenerate the catalyst .
Biochemical Pathways
The primary biochemical pathway affected by this compound is the reduction of ketones and aldehydes to alcohols . This process, known as the MPV reduction, is highly chemoselective and uses a cheap, environmentally friendly metal catalyst .
Result of Action
The result of this compound’s action is the conversion of ketones and aldehydes to their corresponding alcohols . This transformation is highly selective, making this compound a valuable tool in organic synthesis .
Action Environment
The action of this compound can be influenced by environmental factors such as the presence of other reactants and the reaction conditions. For example, the presence of a sacrificial alcohol is necessary for the MPV reduction . Additionally, the reaction is reversible and driven by the thermodynamic properties of the intermediates and products .
Biochemical Analysis
Biochemical Properties
Aluminium isopropoxide is a versatile and inexpensive Lewis acid catalyst and dehydrating agent widely used in the field of organic transformations . It is assumed that the tetrameric cluster disaggregates in these reactions .
Molecular Mechanism
The molecular mechanism of this compound primarily involves its role as a Lewis acid catalyst in organic transformations. It can catalyze various reactions such as Meerwein–Ponndorf–Verley–Oppenauer (MPVO) reactions and ring-opening polymerization of lactides and lactones .
Metabolic Pathways
Preparation Methods
Synthetic Routes and Reaction Conditions: Aluminium isopropoxide can be synthesized by reacting aluminium metal with isopropyl alcohol in the presence of a catalyst such as mercuric chloride. The reaction is typically carried out under anhydrous conditions to prevent hydrolysis . The reaction can be represented as: [ 2 \text{Al} + 6 \text{i-PrOH} \rightarrow 2 \text{Al(O-i-Pr)}_3 + 3 \text{H}_2 ]
Industrial Production Methods: Industrially, this compound is prepared by reacting aluminium trichloride with isopropyl alcohol. This method avoids the use of mercury, making it more environmentally friendly . The reaction is as follows: [ \text{AlCl}_3 + 3 \text{i-PrOH} \rightarrow \text{Al(O-i-Pr)}_3 + 3 \text{HCl} ]
Types of Reactions:
Oxidation: It is also used in the Oppenauer oxidation of secondary alcohols to ketones.
Substitution: In the Tishchenko reaction, this compound catalyzes the formation of esters from aldehydes.
Common Reagents and Conditions:
Meerwein–Ponndorf–Verley Reduction: Typically involves this compound and a secondary alcohol such as isopropanol.
Oppenauer Oxidation: Utilizes this compound and an oxidizing agent.
Major Products:
Reduction: Alcohols from ketones and aldehydes.
Oxidation: Ketones from secondary alcohols.
Substitution: Esters from aldehydes.
Scientific Research Applications
Aluminium isopropoxide has a wide range of applications in scientific research:
Biology: Employed in the synthesis of various biologically active compounds.
Industry: Utilized in sol-gel processing to produce alumina nanoparticles and multimetallic oxides.
Comparison with Similar Compounds
Titanium isopropoxide: Similar in structure but used in different catalytic applications.
Aluminium tert-butoxide: A dimeric compound used in similar reactions but with different reactivity.
Uniqueness: Aluminium isopropoxide is unique due to its high chemoselectivity in the Meerwein–Ponndorf–Verley reduction and its ability to catalyze a wide range of organic transformations. Its versatility and effectiveness as a catalyst make it a valuable reagent in both academic and industrial settings .
Properties
CAS No. |
555-31-7 |
---|---|
Molecular Formula |
C3H8AlO |
Molecular Weight |
87.08 g/mol |
IUPAC Name |
aluminum;propan-2-olate |
InChI |
InChI=1S/C3H8O.Al/c1-3(2)4;/h3-4H,1-2H3; |
InChI Key |
XHODMTAOVMFHQJ-UHFFFAOYSA-N |
SMILES |
CC(C)[O-].CC(C)[O-].CC(C)[O-].[Al+3] |
Canonical SMILES |
CC(C)O.[Al] |
boiling_point |
135 °C @ 10 mm Hg; 131 °C @ 7.5 mm Hg; 125.5 °C @ 5.5 mm Hg; 113 °C @ 2.5 mm Hg; 106 °C @ 1.5 mm Hg; 94 °C @ 0.5 mm Hg |
Color/Form |
White solid WHITE CRYSTALS |
density |
1.025 @ 20 °C |
melting_point |
119 °C |
Key on ui other cas no. |
555-31-7 |
physical_description |
Liquid; OtherSolid |
Pictograms |
Flammable |
shelf_life |
Low melting solids or colorless, volatile liquids. /Alkylaluminum halides/ Less sensitive than trialkylaminums to oxidation upon exposure to air. /Alkylaluminum halides/ |
solubility |
Soluble in ethanol, isopropanol, benzene, toluene, chloroform, carbon tetrachloride, petroleum hydrocarbons. |
Synonyms |
2-Propanol Aluminum Salt; Isopropyl Alcohol Aluminum Salt; AIPD; Aliso; Aluminum 2-Propoxide; Aluminum Isopropanolate; Aluminum Isopropioate; Aluminum Isopropylate; Aluminum sec-Propanolate; Aluminum Triisopropoxide; Aluminum Triisopropylate; Aluminu |
Origin of Product |
United States |
Synthesis routes and methods I
Procedure details
Synthesis routes and methods II
Procedure details
Synthesis routes and methods III
Procedure details
Synthesis routes and methods IV
Procedure details
Synthesis routes and methods V
Procedure details
Retrosynthesis Analysis
AI-Powered Synthesis Planning: Our tool employs the Template_relevance Pistachio, Template_relevance Bkms_metabolic, Template_relevance Pistachio_ringbreaker, Template_relevance Reaxys, Template_relevance Reaxys_biocatalysis model, leveraging a vast database of chemical reactions to predict feasible synthetic routes.
One-Step Synthesis Focus: Specifically designed for one-step synthesis, it provides concise and direct routes for your target compounds, streamlining the synthesis process.
Accurate Predictions: Utilizing the extensive PISTACHIO, BKMS_METABOLIC, PISTACHIO_RINGBREAKER, REAXYS, REAXYS_BIOCATALYSIS database, our tool offers high-accuracy predictions, reflecting the latest in chemical research and data.
Strategy Settings
Precursor scoring | Relevance Heuristic |
---|---|
Min. plausibility | 0.01 |
Model | Template_relevance |
Template Set | Pistachio/Bkms_metabolic/Pistachio_ringbreaker/Reaxys/Reaxys_biocatalysis |
Top-N result to add to graph | 6 |
Feasible Synthetic Routes
Q1: What is the molecular formula of aluminium isopropoxide?
A1: The molecular formula of this compound is Al(OC3H7)3.
Q2: What is the molecular weight of this compound?
A2: The molecular weight of this compound is 204.25 g/mol.
Q3: What spectroscopic techniques are useful for characterizing this compound?
A3: Several spectroscopic techniques are valuable for characterizing this compound:
- FTIR (Fourier-Transform Infrared Spectroscopy): Provides information about the functional groups present in the molecule, particularly the Al-O bonds and the isopropoxide groups [, , , ].
- NMR (Nuclear Magnetic Resonance Spectroscopy): Offers insights into the structure and dynamics of the molecule, including the coordination environment of the aluminium atom [, , , ]. Both ¹H and ¹³C NMR are commonly used.
- Mass Spectrometry: Useful for determining the molecular weight and fragmentation patterns of the compound, providing evidence for the presence of dimeric, trimeric, and tetrameric species [, ].
- XRD (X-Ray Diffraction): Primarily used to analyze the crystalline structure of this compound in its solid forms [, , , , ].
Q4: How do the physical properties of liquid this compound change over time?
A4: During storage, liquid this compound undergoes a slow molecular rearrangement []. This is evidenced by gradual changes in its physical properties, including density, refractive index, dielectric constant, and viscosity [].
Q5: What are some common applications of this compound as a catalyst?
A5: this compound is widely used as a catalyst in various organic reactions, including:
- Meerwein-Ponndorf-Verley (MPV) Reduction: This reaction involves the reduction of aldehydes and ketones to their corresponding alcohols using a secondary alcohol, typically isopropanol, as the hydrogen source [, , ].
- Ring-Opening Polymerization: this compound can initiate the polymerization of cyclic esters, such as lactides and caprolactones, to form biodegradable polyesters [, , ].
- Claisen Rearrangement: This reaction involves the rearrangement of allyl vinyl ethers to give γ,δ-unsaturated aldehydes or ketones [].
Q6: What factors influence the catalytic activity of this compound?
A6: Several factors can impact the catalytic activity of this compound:
- Presence of Lewis Bases: Adding Lewis bases, such as triphenylphosphine or 4-picoline, to this compound significantly enhances the polymerization rate of lactides [].
- Solvent Effects: The solvent used in the reaction can considerably affect the catalytic activity. For instance, in the MPV reduction, solvents with high hydrogen-bond accepting ability, like ethers, tend to reduce catalytic activity due to the formation of larger aggregates that hinder the access of reactants to the catalytic sites [].
- Deactivation: Water and heavy by-products can deactivate the catalyst. Water can hydrolyze the this compound, while heavy by-products might block the active sites [].
Q7: How does this compound interact with supports when used as a heterogeneous catalyst?
A7: When immobilized on mesoporous supports like SiO2, TiO2, and γ-Al2O3, this compound binds covalently to the surface []. This heterogenization allows for easy catalyst recovery and reuse without significant loss of activity [].
Q8: What are the advantages of using this compound as a heterogeneous catalyst compared to its homogeneous counterpart?
A8: Heterogenized this compound offers several benefits over its homogeneous form:
Q9: How can the amount of aluminium residue in polymers produced using this compound be reduced?
A9: Adding a secondary alcohol, like isopropanol, as a transfer agent during the polymerization process helps to reduce the amount of aluminium remaining in the final polymer product [].
Q10: How is this compound used in preparing alumina materials?
A10: this compound is a common precursor for synthesizing various alumina materials, including:
- Nano Aluminium Hydroxide: Prepared through a hydrolysis-hydrothermal process, where this compound is first hydrolyzed to form pseudoboehmite, which is then transformed into boehmite under hydrothermal conditions [].
- B-Alumina: Synthesized by thermal decomposition of a mixture containing excess sodium isopropoxide and this compound, followed by heating to 1000°C [].
- Mesoporous γ-Alumina: Produced through a sol-gel method using glucose as a template, followed by calcination. The textural properties, crucial for applications like molybdenum-99 adsorption, are influenced by the water to this compound ratio used during synthesis [].
- Al2O3 Thin Films: Prepared by spin-coating a solution of this compound, followed by calcination. These films can be doped with luminescent materials like (Ca,Sr)S:Eu²⁺ for various applications [].
Q11: How does the choice of aluminium source affect the synthesis of zeolite A?
A11: The choice of aluminium source significantly affects the synthesis kinetics, morphology, and properties of zeolite A []:
- This compound: Leads to the formation of zeolite A with spherical morphology and a size of approximately 100 nm [].
- Freshly Prepared Aluminium Hydroxide: When combined with Ludox colloidal silica, it produces well-defined cubic zeolite A crystals ranging from 300 nm to 1 µm in size [].
Q12: Can this compound be used to modify the properties of cotton fabrics?
A12: Yes, combining this compound with hydrolyzed organotrialkoxysilanes can functionalize cotton fabrics []. This treatment enhances crease recovery but may reduce tensile and tear strength. The modified fabrics also exhibit improved hydrophobicity and can be used for mordant dyeing [].
Q13: How does this compound contribute to flame retardancy in ethylene-vinyl acetate (EVA) nanocomposites?
A13: When incorporated into EVA via a sol-gel process, this compound forms nanoparticles within the polymer matrix []. These nanoparticles act as flame retardants, improving the material's fire resistance and allowing it to meet specific safety standards [].
Q14: What are some other applications of this compound?
A14: Besides its uses in catalysis and materials science, this compound finds application in:
- Organic Synthesis: It acts as a reagent in various organic reactions, such as the preparation of farnesylacetone from nerolidol [].
- Surface Treatment: this compound sols are being explored as environmentally friendly alternatives to chromium-based sealants for aluminium alloy anodized films. These sols enhance the corrosion resistance and dyeing properties of the treated surfaces [].
Disclaimer and Information on In-Vitro Research Products
Please be aware that all articles and product information presented on BenchChem are intended solely for informational purposes. The products available for purchase on BenchChem are specifically designed for in-vitro studies, which are conducted outside of living organisms. In-vitro studies, derived from the Latin term "in glass," involve experiments performed in controlled laboratory settings using cells or tissues. It is important to note that these products are not categorized as medicines or drugs, and they have not received approval from the FDA for the prevention, treatment, or cure of any medical condition, ailment, or disease. We must emphasize that any form of bodily introduction of these products into humans or animals is strictly prohibited by law. It is essential to adhere to these guidelines to ensure compliance with legal and ethical standards in research and experimentation.