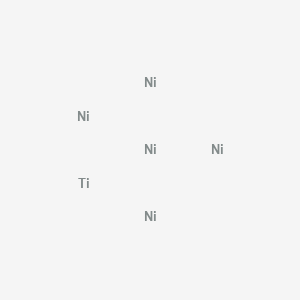
nickel;titanium
- Click on QUICK INQUIRY to receive a quote from our team of experts.
- With the quality product at a COMPETITIVE price, you can focus more on your research.
Overview
Description
Nickel-titanium (NiTi) alloys, also known as nitinol, are intermetallic compounds exhibiting unique shape memory effects (SME) and superelasticity, enabling recovery of up to 8% strain . These properties arise from a reversible martensitic-austenitic phase transition triggered by temperature or stress. NiTi alloys are widely used in aerospace, biomedical implants (e.g., orthodontic archwires, endodontic instruments), and actuators due to their biocompatibility, corrosion resistance, and fatigue durability .
Preparation Methods
Nickel titanium alloys are typically produced through vacuum melting techniques. Common methods include electron beam melting, arc melting, high-frequency vacuum melting in a graphite crucible, and plasma melting . These methods ensure the precise compositional control required to achieve the desired properties of the alloy .
Chemical Reactions Analysis
Formation of Intermetallic Phases in Ni-Ti Systems
Nickel and titanium form intermetallic compounds under controlled thermal conditions.
Phase Sequences at 1173 K
Initial Alloy Composition | Reaction Layer Sequence (Phases) |
---|---|
Ni₈₀Fe₂₀ | Ni₃Ti → NiTi → NiTi₂ → Ti |
Ni₄₈Fe₅₂ | Ni₃Ti → TiFe₂ → TiFe → NiTi₂ |
-
Diffusion Coefficients :
Electrochemical Oxidation in Alkaline Media
Ni-Ti electrodes exhibit dual oxidation behavior in 0.1 M NaOH:
Reactions:
Ti→TiO2+4e−(E=+0.4V vs Ag AgCl)Ni→NiO→NiOOH(E>+0.5V)
-
Surface Analysis (XPS) :
Stability : Ni-Ti electrodes show smoother oxide layers and reduced degradation compared to pure Ni .
Corrosion in Chloride Environments
NiTi alloys undergo localized corrosion in acidic, chloride-rich solutions:
Reaction Pathway :
-
Chloride adsorption on TiO₂ surface.
-
Formation of soluble titanium oxychloride:
TiO2+2Cl−+2H+→TiOCl2+H2O
-
Hydrolysis of TiOCl₂:
TiOCl2+H2O→TiO2+2HCl
Intermetallic Layer Formation in Joining Processes
Explosive bonding of Ni to Ti alloys produces brittle intermetallic layers:
Phases Observed :
Mechanical Impact :
Scientific Research Applications
Nickel-titanium (NiTi), also known as nitinol, is a metal alloy of nickel and titanium, with the two elements present in roughly equal atomic percentages . Nitinol alloys possess unique properties, including superelasticity and the shape memory effect . The word "nitinol" is derived from its composition and its place of discovery, Nickel Titanium - Naval Ordnance Laboratory . William J. Buehler, along with Frederick E. Wang, discovered its properties during research at the Naval Ordnance Laboratory in 1959 .
Shape Memory and Superelasticity
Nitinol alloys exhibit two closely related and unique properties: the shape memory effect and superelasticity (also called pseudoelasticity) .
- Shape memory is the ability of nitinol to undergo deformation at one temperature, stay in its deformed shape when the external force is removed, then recover its original, undeformed shape upon heating above its "transformation temperature" .
- Superelasticity is the ability for the metal to undergo large deformations and immediately return to its undeformed shape upon removal of the external load . Nitinol can undergo elastic deformations 10 to 30 times larger than alternative metals .
Whether nitinol behaves with shape memory effect or superelasticity depends on whether it is above its transformation temperature during the action . Nitinol behaves with the shape memory effect when it is colder than its transformation temperature, and superelastically when it is warmer than it .
Applications
Because of its properties, nickel-titanium alloys have various applications in a variety of fields.
Biomedical Field
Due to its shape-memory effect, corrosion resistance, super-elasticity, and favorable biocompatibility, nitinol has been used for internal fixation since the 1990s .
- Wires for orthodontic tooth alignment and osteosynthesis staples .
- Stents, implants, and surgical devices .
- Nickel–titanium and chromium–cobalt wires supported better cell viability and healthier cell morphology .
Aerospace
- Aircraft pipe joints
- Spacecraft antennas
- Fasteners, connecting components, electrical connections, and electromechanical actuators .
- Engineers successfully flight-tested SMA-actuated morphing chevrons on the Boeing 777-300ER Quiet Technology Demonstrator 2 .
Civil Engineering
- Superelastic nitinol finds a variety of applications in civil structures such as bridges and buildings .
- Intelligent Reinforced Concrete (IRC), which incorporates NiTi wires embedded within the concrete . These wires can sense cracks and contract to heal macro-sized cracks .
- Active tuning of structural natural frequency using nitinol wires to damp vibrations .
Other applications
- Demonstration model heat engines have been built which use nitinol wire to produce mechanical energy from hot and cold heat sources . A prototype commercial engine developed in the 1970s by engineer Ridgway Banks at Lawrence Berkeley National Laboratory, was named the Banks Engine .
- Extremely resilient glasses frames .
- The Ford Motor Company has registered a US patent for what it calls a "bicycle derailleur apparatus for controlling bicycle speed" . Filed on 22 April 2019, the patent depicts a front derailleur for a bicycle, devoid of cables, instead using two nitinol wires to provide the movement needed to shift gears .
- Self-bending spoons which can be used by amateur and stage magicians to demonstrate "psychic" powers or as a practical joke, as the spoon will bend itself when used to stir tea, coffee, or any other warm liquid .
- Golf club insert .
- Underwires for underwire bras .
Case Study: 3D-printed shape memory alloys
Texas A&M University researchers have developed 3D-printed nickel-titanium shape memory alloys with superior superelasticity . The researchers fabricated nickel-titanium parts that consistently exhibited a room temperature tensile superelasticity of 6% in the as-printed condition (without post-fabrication heat treatment) . This level of superelasticity is nearly double the amount previously seen in literature for 3D printing . Using 3D printing to develop these superior materials will reduce the cost and time of the manufacturing process . In the future, the researchers hope their discoveries will lead to increased use of printed nickel-titanium shape memory alloys in biomedical and aerospace applications .
Corrosion Resistance
Mechanism of Action
This transformation occurs between two different martensite crystal phases and is influenced by mechanical stress and temperature . When nickel titanium is deformed at a temperature below its transformation temperature, it exhibits the shape memory effect. When deformed above this temperature, it behaves superelastically .
Comparison with Similar Compounds
Mechanical and Thermal Properties
Table 1: Key Mechanical Properties of NiTi vs. Competing Alloys
Property | NiTi | Stainless Steel (SS) | Titanium-Molybdenum (TMA) | Nickel-Based Superalloys |
---|---|---|---|---|
Density (g/cm³) | 6.45–6.50 | 7.9–8.0 | 4.5–4.8 | 8.0–9.1 |
Elastic Modulus (GPa) | 28–75 (austenite phase) | 190–210 | 100–110 | 200–220 |
Fatigue Strength | Superior (high-cycle) | Moderate | Moderate | High (γ′-hardened) |
Thermal Conductivity | 10–18 W/m·K | 15–20 W/m·K | 7–10 W/m·K | 11–15 W/m·K |
Superelasticity | 8% recoverable strain | None | 2–3% | None |
Key Findings :
- NiTi’s lower elastic modulus (28–75 GPa) closely matches bone tissue (10–30 GPa), reducing stress shielding in orthopedic implants compared to stainless steel (190–210 GPa) .
- NiTi outperforms TMA in superelastic strain recovery (8% vs. 2–3%), critical for orthodontic archwires requiring minimal adjustments .
- Nickel-based superalloys (e.g., Inconel) exhibit superior high-temperature strength but lack shape memory and are 30–40% denser, limiting aerospace efficiency .
Table 2: Performance in Medical Devices
Key Findings :
- In orthodontics, NiTi archwires (e.g., Ormco, GAC) reduce chair time by 20–30% compared to TMA due to sustained force delivery . However, heat treatment above 400°C degrades superelasticity by 40–60% .
- Novel NiTi variants (e.g., M-Wire, R-Phase) enhance cyclic fatigue resistance by 50% compared to conventional NiTi in endodontic instruments .
- Ti-22Nb-6Zr, a nickel-free superelastic alloy, addresses NiTi’s biocompatibility concerns but exhibits 15% lower strain recovery .
Environmental and Metallurgical Stability
- Volatility in Additive Manufacturing : NiTi’s nickel component vaporizes at lower temperatures (boiling point Ni: 2,913°C vs. Ti: 3,287°C), causing compositional shifts during laser powder bed fusion (LPBF). This necessitates precise parameter control to retain stoichiometry .
- Corrosion Resistance : NiTi’s passive TiO₂ layer provides better corrosion resistance than stainless steel in saline environments but is inferior to pure titanium .
Q & A
Basic Research Questions
Q. How can researchers experimentally quantify the shape memory effect (SME) and superelasticity in NiTi alloys?
- Methodological Answer : Use differential scanning calorimetry (DSC) to measure phase transformation temperatures (austenite start/finish, martensite start/finish) and correlate them with mechanical testing. For superelasticity, perform cyclic tensile tests at temperatures above austenite finish (Af) to observe stress-induced martensite formation and recovery . Thermal cycling under controlled strain rates (e.g., 0.1–1% strain/min) can isolate hysteresis effects .
Q. What characterization techniques are critical for validating NiTi alloy microstructure and phase composition?
- Methodological Answer : Combine X-ray diffraction (XRD) for phase identification (e.g., B2 austenite vs. B19′ martensite) with scanning electron microscopy (SEM) to analyze grain morphology. Energy-dispersive X-ray spectroscopy (EDS) ensures stoichiometric consistency (e.g., Ni-rich vs. Ti-rich phases). For nanoscale precipitates, use transmission electron microscopy (TEM) with selected-area diffraction (SAD) .
Q. How should researchers design experiments to assess NiTi corrosion resistance in biomedical applications?
- Methodological Answer : Conduct electrochemical tests (potentiodynamic polarization, electrochemical impedance spectroscopy) in simulated body fluid (SBF) at 37°C. Monitor ion release (Ni<sup>2+</sup>, Ti<sup>4+</sup>) using inductively coupled plasma mass spectrometry (ICP-MS) over 30-day immersion periods. Compare with ASTM F2129 standards for pitting potential thresholds .
Advanced Research Questions
Q. How can conflicting data on β-phase stability in NiTi alloys be resolved?
- Methodological Answer : Reconcile discrepancies by applying the revised Mo equivalence equation [(Mo-Eq)Ti-Nb-Zr = 0.238Nb + 0.11Zr + 0.97] to account for Zr’s β-stabilizing effect, which existing models overlook. Validate predictions with in-situ synchrotron XRD during quenching and aging to track phase evolution . Cross-reference with d-electron theory to predict bond order and alloy stability .
Q. What experimental frameworks optimize additive manufacturing (AM) parameters for NiTi lattice structures?
- Methodological Answer : Use design of experiments (DoE) to test laser power (50–300 W), scan speed (200–1200 mm/s), and layer thickness (20–100 μm) in selective laser melting (SLM). Characterize porosity via micro-CT and mechanical anisotropy via compression testing. Post-process with heat treatment (500–700°C) to restore SME .
Q. How does torsional resistance in NiTi endodontic instruments vary with shaft length, and how should this inform clinical testing protocols?
- Methodological Answer : Conduct static torsional tests per ISO 3630-1, clamping instruments 3 mm from the tip and rotating until fracture. Measure torque-to-fracture (TtF) and fragment length. Statistically compare groups with varying lengths (e.g., 23 mm vs. 27 mm) using ANOVA. Results show longer shafts (27 mm) exhibit 2–3× higher TtF due to reduced stress concentration .
Q. What strategies mitigate data variability in DSC measurements of NiTi phase transformations?
- Methodological Answer : Standardize sample mass (5–10 mg) and heating/cooling rates (10°C/min). Use high-purity argon gas to minimize oxidation. Validate results with repeated cycles (≥3) to ensure thermal history erasure. Cross-check with resistivity measurements for abrupt phase changes .
Q. Contradiction Analysis & Future Directions
Q. Why do computational models of NiTi fatigue life often diverge from experimental results?
- Methodological Answer : Address oversimplifications in finite element analysis (FEA), such as neglecting surface defects (microcracks, inclusions) and residual stresses from machining. Incorporate microstructural data (grain size, texture) into crystal plasticity models. Validate with strain-controlled fatigue tests (R = −1) across 10<sup>3</sup>–10<sup>6</sup> cycles .
Q. How can researchers reconcile discrepancies in NiTi stent fatigue performance across in-vitro vs. in-vivo studies?
- Methodological Answer : Simulate physiological conditions (pulsatile flow, 10% radial compression) in accelerated durability testers (e.g., 400 cycles/min for 10 years equivalent). Compare with retrievable stent studies in animal models, analyzing fracture sites via SEM/EBSD to identify grain boundary sliding or twinning mechanisms .
Q. What gaps exist in understanding NiTi’s damping capacity under dynamic loading, and how can they be addressed?
- Methodological Answer : Current models underestimate damping due to incomplete martensite variant reorientation. Use dynamic mechanical analysis (DMA) with frequency sweeps (0.1–100 Hz) and strain amplitudes (0.1–5%). Correlate with acoustic emission (AE) data to map variant nucleation in real-time .
Properties
CAS No. |
61642-34-0 |
---|---|
Molecular Formula |
Ni5Ti |
Molecular Weight |
341.33 g/mol |
IUPAC Name |
nickel;titanium |
InChI |
InChI=1S/5Ni.Ti |
InChI Key |
CYVYCNHHIBOPPU-UHFFFAOYSA-N |
Canonical SMILES |
[Ti].[Ni].[Ni].[Ni].[Ni].[Ni] |
Origin of Product |
United States |
Disclaimer and Information on In-Vitro Research Products
Please be aware that all articles and product information presented on BenchChem are intended solely for informational purposes. The products available for purchase on BenchChem are specifically designed for in-vitro studies, which are conducted outside of living organisms. In-vitro studies, derived from the Latin term "in glass," involve experiments performed in controlled laboratory settings using cells or tissues. It is important to note that these products are not categorized as medicines or drugs, and they have not received approval from the FDA for the prevention, treatment, or cure of any medical condition, ailment, or disease. We must emphasize that any form of bodily introduction of these products into humans or animals is strictly prohibited by law. It is essential to adhere to these guidelines to ensure compliance with legal and ethical standards in research and experimentation.