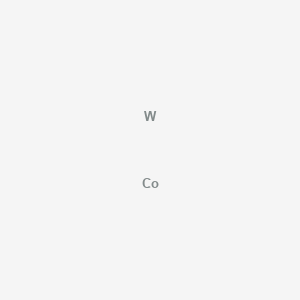
cobalt;tungsten
- Click on QUICK INQUIRY to receive a quote from our team of experts.
- With the quality product at a COMPETITIVE price, you can focus more on your research.
Overview
Description
Cobalt (Co) and tungsten (W) are transition metals with distinct chemical and physical properties, enabling their use in diverse industrial applications. Cobalt is renowned for its role in lithium-ion batteries, magnetic alloys, and catalysts . Tungsten, the metal with the highest melting point (3,422°C), is critical for high-temperature applications, cemented carbides, and radiation shielding . Their compounds, particularly cobalt-tungsten systems like tungsten carbide-cobalt (WC-Co), are pivotal in materials science due to their exceptional hardness, wear resistance, and catalytic properties .
Preparation Methods
Synthetic Routes and Reaction Conditions
The preparation of cobalt tungsten involves several steps:
Powder Preparation: Tungsten carbide powder is mixed with cobalt powder in precise ratios.
Compaction: The mixed powders are pressed into a desired shape using high pressure.
Sintering: The compacted material is heated to a temperature just below the melting point of cobalt.
Industrial Production Methods
Industrial production of cobalt tungsten often involves molten salt electrolysis, where tungsten carbide scrap is used as the sacrificial anode and NaCl–KCl salt as the electrolyte . This method allows for the efficient extraction of cobalt and tungsten from cemented carbide scraps, making it a sustainable approach to producing this compound .
Chemical Reactions Analysis
Catalytic Water Splitting with Cobalt-Tungsten Polyoxometalates
A cobalt-tungsten polyoxometalate (Co-W-POM) demonstrates superior catalytic activity for acidic water splitting compared to iridium-based catalysts . The reaction occurs via:
2H2O→2H2+O2
Key Findings :
-
Acid Stability : Co-W-POMs operate efficiently in acidic media (pH < 1), avoiding catalyst degradation common in other systems .
-
Low-Voltage Advantage : Optimal performance at reduced voltages (e.g., <1.5 V) enables integration with renewable energy sources like solar panels .
-
Hydrophobic Enhancement : Supporting Co-W-POMs on hydrophobic scaffolds increases efficiency by 30–40% and extends catalyst lifetime by minimizing acid corrosion .
Parameter | Value/Outcome | Source |
---|---|---|
Overpotential (Oxygen Evolution) | 280 mV at 10 mA/cm² | |
Stability in 0.5 M H₂SO₄ | >100 hours without decay |
Reactive Oxygen Species (ROS) Generation in Cobalt-Tungsten Carbide Composites
Cobalt-tungsten carbide (WC-Co) composites exhibit synergistic toxicity due to ROS generation via interfacial reactions :
\text{Co}+\text{WC}+\text{O}_2\rightarrow \text{Co}^{2+}+\text{OH}^-\(\text{via Fenton like reactions})
Mechanistic Insights :
-
Electron Transfer : Tungsten carbide acts as a conductor, facilitating electron transfer from cobalt to oxygen, accelerating oxygen reduction .
-
Hydroxyl Radical Production : WC-Co mixtures generate 5× more hydroxyl radicals (⋅OH
) than cobalt alone .
Toxicity Comparison :
Material | ROS Generation (Relative) | Cellular Toxicity (IC₅₀) |
---|---|---|
Cobalt alone | 1.0× | 50 µM |
WC-Co composite | 5.2× | 12 µM |
Recovery of Tungsten and Cobalt from WC-Co Waste
Recycling WC-Co involves thermochemical oxidation followed by hydrogen reduction :
Oxidation Step (900°C, air) :
2WC+5O2→2WO3+2CO2
Co+WO3→CoWO4
Reduction Step (H₂ atmosphere) :
WO3+3H2→W+3H2O
CoWO4+4H2→Co+W+4H2O
Thermodynamic Data :
Reaction | ΔH (kJ/mol) | ΔG (kJ/mol) |
---|---|---|
WC oxidation to WO₃ | -395.2 | -380.1 |
CoWO₄ reduction to Co | -128.7 | -112.4 |
Electrocatalytic Oxygen Evolution with Cobalt-Tungsten Oxides
Self-optimizing cobalt-tungsten oxide (Co-W-Oₓ) nanostructures enhance oxygen evolution reaction (OER) efficiency :
4OH−→2H2O+O2+4e−
Performance Metrics :
-
Overpotential : 290 mV at 10 mA/cm² (vs. 340 mV for pure Co₃O₄).
-
Stability : <5% activity loss after 50 hours.
Mechanism : In situ oxidation forms active CoOOH/CoO₂ species, while tungsten stabilizes the structure against corrosion .
Structural Interactions in WC-Co Alloys
The reactivity of WC-Co systems depends on:
-
Cobalt Content : Higher Co (5–20 wt%) improves ductility but reduces hardness .
-
Grain Size : Smaller WC grains (<1 µm) enhance hardness but increase susceptibility to oxidation .
Property | WC-5%Co | WC-20%Co |
---|---|---|
Hardness (HV) | 1,800 | 1,200 |
Fracture Toughness | 8 MPa·m¹/² | 14 MPa·m¹/² |
This synthesis highlights cobalt-tungsten systems’ versatility in catalysis, environmental chemistry, and materials engineering, underpinned by tailored electronic and structural interactions.
Scientific Research Applications
Cobalt tungsten powder is a composite material created by mixing tungsten carbide (WC) particles with cobalt as a binder . It is also known as cemented tungsten carbide cobalt (WC-Co) . Cobalt tungsten powder's applications span across diverse industries because of its unique properties, which include extreme hardness, high strength, excellent wear resistance, good thermal conductivity, and high-temperature strength .
Applications and Uses of Cobalt Tungsten Powder
Cobalt tungsten powder and its composites are utilized across a diverse range of industries and applications :
Scientific Research Applications
- Catalysis: Tungsten oxide cobalt composites can be used in heterogeneous catalysis to promote chemical reactions . Cobalt oxide combined with tungsten oxide shows catalytic activity for hydrogenation processes, which is useful in synthetic fuel production and petrochemical refining .
- Energy Storage and Conversion: Tungsten oxide cobalt composites are being researched for use in supercapacitors and lithium-ion batteries because their high surface area and conductivity enhance charge and discharge rates . These composites can also act as electrocatalysts in fuel cells, which improves the efficiency of reactions like hydrogen oxidation and oxygen reduction. Cobalt oxide increases the material’s catalytic activity, and tungsten oxide improves stability in high-temperature conditions .
- Electronics and Sensors: Composites are used to produce gas sensors for detecting toxic gases or VOCs. The high catalytic activity and surface reactivity of the materials make them suitable for sensors used in environmental monitoring or industrial safety . Tungsten oxide is known for changing color when subjected to an electrical charge, a property that can be improved with cobalt oxide for smart window applications and displays .
- Hydrogen Production: Tungsten oxide-cobalt composites are used in photoelectrochemical cells for hydrogen production via water splitting . The combination of tungsten and cobalt enhances the efficiency of photoelectrodes, improving the conversion of solar energy into chemical energy (hydrogen) . These composites can be used in solar hydrogen generation, as tungsten oxide absorbs solar energy, and cobalt oxide enhances the electrochemical reactions that split water into hydrogen and oxygen .
Case Studies
- Childhood Leukemia: Research has suggested a temporal correlation between the onset of childhood leukemia and elevated levels of tungsten and cobalt in Fallon, Nevada .
- Toxicity: Studies have explored the potential role of tungsten carbide cobalt (WC-Co) particle size and internalization on toxicity using lung epithelial cells . Tungsten carbide nanoparticles alone are not acutely toxic, but when combined with cobalt, they can have toxic effects at high particle concentrations . The toxicity of the WC-Co mixture was higher than that of similar concentrations of cobalt ions .
- Carcinogenicity: Cobalt metal (without tungsten carbide) and soluble cobalt(II) salts have been classified as probably carcinogenic to humans based on sufficient evidence from animal studies and strong mechanistic evidence . Cobalt(II) oxide and weapons-grade tungsten alloy were classified as possibly carcinogenic to humans based on sufficient evidence in experimental animals .
Mechanism of Action
The mechanism by which cobalt tungsten exerts its effects involves the interaction of cobalt and tungsten ions with their molecular targets. Cobalt ions can interact with cellular components, leading to various biological effects, including antimicrobial activity . Tungsten ions can enhance the catalytic properties of the compound, making it effective in industrial applications .
Comparison with Similar Compounds
Structural and Mechanical Properties
Table 1: Mechanical Properties of WC-Co Composites
Property | Fine-Grain WC-Co (S105/KFS64) | Coarse-Grain WC-Co | Binderless WC |
---|---|---|---|
Cobalt Content (wt%) | 6.0 | 6.0 | 0.0 |
Hardness (HV) | 1,550 | 1,400 | 2,200 |
Flexural Strength (MPa) | 3,800 | 3,200 | 1,500 |
Fracture Toughness (MPa√m) | 12.0 | 14.5 | 4.0 |
- WC-Co Composites : The addition of cobalt as a binder in WC-Co significantly enhances toughness compared to pure tungsten carbide, albeit with a trade-off in hardness. Fine-grained WC-Co exhibits superior hardness (1,550 HV) due to grain boundary strengthening, while coarse-grained variants prioritize fracture resistance (14.5 MPa√m) .
- CoWO₄ vs. MnWO₄ : In multiferroic materials, cobalt doping in Mn₀.₇Co₀.₃WO₄ stabilizes the local structure by reducing octahedral distortion around Mn²⁺ ions, unlike pure MnWO₄. CoWO₄ itself adopts a wolframite structure with minimal lattice distortions, making it more thermally stable .
Chemical Reactivity and Dissolution
Table 2: Dissolution Behavior in Acidic Media
Material | Dissolution Rate (Cobalt) | Dissolution Rate (Tungsten) |
---|---|---|
WC-Co Hardmetal | High (Selective etching) | Low (Inert matrix) |
Pure Cobalt | Very High | N/A |
Binderless WC | N/A | Very Low |
- Selective Etching : Cobalt in WC-Co dissolves readily in nitric acid, while tungsten remains inert. This property is exploited in industrial processes to purify WC surfaces for coatings .
- This phase separation is critical in designing corrosion-resistant composites .
Catalytic and Electrochemical Performance
- Hydrogen Evolution Reaction (HER): Cobalt sulfide (CoS) and tungsten disulfide (WS₂) are both HER catalysts. CoS nanoparticles show higher activity (overpotential = 180 mV) compared to WS₂ (overpotential = 240 mV) due to favorable electron transfer kinetics .
- Co-W Coatings: Electrodeposited cobalt-tungsten alloys demonstrate enhanced microhardness (600–800 HV) and current efficiency (85–90%) when using soluble tungsten anodes, outperforming graphite anode-based coatings .
Toxicity and Environmental Impact
- Carcinogenicity: Cobalt metal with tungsten carbide (WC-Co) is classified as Group 2A (probably carcinogenic) by the IARC due to synergistic effects, whereas pure cobalt is Group 2B (possibly carcinogenic) .
- Industrial Exposure : Cemented carbide production generates cobalt-containing dust, linked to respiratory toxicity. Regulatory limits for airborne cobalt are typically <0.1 mg/m³ .
Q & A
Basic Research Questions
Q. What experimental methodologies are recommended for synthesizing and characterizing cobalt-tungsten (Co-W) alloys?
- Answer: Co-W alloys are typically synthesized via electrodeposition or thermal spraying (e.g., high-velocity oxygen-fuel, HVOF). For characterization, use scanning electron microscopy (SEM) to analyze microstructure and X-ray diffraction (XRD) for phase identification. Residual stress behavior can be quantified using profilometry or neutron diffraction. Ensure synthesis parameters (e.g., temperature, current density) are documented for reproducibility .
Q. How can researchers address inconsistencies in reported corrosion resistance properties of Co-W coatings?
- Answer: Discrepancies often arise from variations in alloy composition or testing environments. Standardize electrochemical testing (e.g., potentiodynamic polarization in 3.5% NaCl solution) and control variables such as coating thickness and substrate pretreatment. Cross-validate results with energy-dispersive X-ray spectroscopy (EDS) to confirm elemental homogeneity .
Q. What are the best practices for ensuring reproducibility in HVOF-sprayed tungsten carbide/cobalt (WC/Co) coatings?
- Answer: Employ a central composite design (CCD) to optimize process parameters (e.g., fuel-to-oxygen ratio, spray distance). Use response surface methodology (RSM) to model interactions between variables. Document particle size distribution of feedstock powders and post-spray heat treatment protocols to minimize porosity .
Advanced Research Questions
Q. How can computational modeling improve the prediction of crack propagation in WC/Co composites under thermal stress?
- Answer: Finite element analysis (FEA) coupled with fracture mechanics principles can simulate crack evolution. Input experimental data (e.g., thermal gradient maps from laser cladding) to calibrate models. Validate predictions against SEM micrographs of stress-induced microcracks .
Q. What methodologies resolve contradictions in toxicity studies of cobalt compounds used in tungsten carbide production?
- Answer: Conflicting data on pulmonary fibrosis risk (e.g., from cobalt oxide aerosols) require meta-analysis of in vivo/in vitro studies. Control for confounding variables like particle size (e.g., median diameter <0.5 µm in hamster models) and coexposure to other metals. Use intradermal testing to differentiate occupational vs. environmental sensitivities .
Q. How can laser cladding parameters be optimized to minimize residual stress in Co-W protective coatings?
- Answer: Implement a Taguchi design of experiments (DoE) to test laser power, scanning speed, and powder feed rate. Measure residual stress via X-ray diffraction sin²ψ technique. Prioritize parameter combinations that yield a metallurgical bond with the substrate, as evidenced by SEM cross-sections .
Q. What advanced techniques quantify the role of cobalt binder phase distribution in WC/Co wear resistance?
- Answer: Use nanoindentation to map hardness variations across the binder phase. Correlate results with electron backscatter diffraction (EBSD) to analyze crystallographic orientation. Tribological testing under controlled loads (e.g., 10 N, 100 rpm) can isolate the contribution of cobalt distribution to wear mechanisms .
Q. How do researchers reconcile discrepancies in reported thermal stability thresholds for Co-W alloys?
- Answer: Discrepancies often stem from differing measurement techniques (e.g., differential scanning calorimetry vs. thermogravimetric analysis). Standardize heating rates (e.g., 10°C/min in inert atmospheres) and validate phase transitions using in-situ XRD .
Methodological & Data Analysis Questions
Q. What statistical approaches are suitable for analyzing multifactorial experiments on Co-W coatings?
- Answer: Multivariate analysis of variance (MANOVA) can assess interactions between variables (e.g., composition, temperature). For non-linear relationships, apply artificial neural networks (ANNs) trained on experimental datasets. Ensure sample sizes meet power analysis requirements to avoid Type II errors .
Q. How should researchers design questionnaires for qualitative studies on cobalt exposure in academic labs?
- Answer: Structure questions around specific exposure scenarios (e.g., handling WC/Co powders, ventilation efficacy). Use Likert scales to quantify risk perception and open-ended questions for anecdotal data. Pilot-test the questionnaire with a small cohort to eliminate ambiguity and ensure IRB compliance .
Properties
CAS No. |
62431-64-5 |
---|---|
Molecular Formula |
CoW |
Molecular Weight |
242.77 g/mol |
IUPAC Name |
cobalt;tungsten |
InChI |
InChI=1S/Co.W |
InChI Key |
JPNWDVUTVSTKMV-UHFFFAOYSA-N |
Canonical SMILES |
[Co].[W] |
Origin of Product |
United States |
Disclaimer and Information on In-Vitro Research Products
Please be aware that all articles and product information presented on BenchChem are intended solely for informational purposes. The products available for purchase on BenchChem are specifically designed for in-vitro studies, which are conducted outside of living organisms. In-vitro studies, derived from the Latin term "in glass," involve experiments performed in controlled laboratory settings using cells or tissues. It is important to note that these products are not categorized as medicines or drugs, and they have not received approval from the FDA for the prevention, treatment, or cure of any medical condition, ailment, or disease. We must emphasize that any form of bodily introduction of these products into humans or animals is strictly prohibited by law. It is essential to adhere to these guidelines to ensure compliance with legal and ethical standards in research and experimentation.