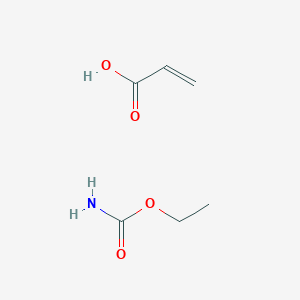
Urethane acrylate
Overview
Description
Urethane acrylate, also known as this compound, is a useful research compound. Its molecular formula is C6H11NO4 and its molecular weight is 161.16 g/mol. The purity is usually 95%.
BenchChem offers high-quality this compound suitable for many research applications. Different packaging options are available to accommodate customers' requirements. Please inquire for more information about this compound including the price, delivery time, and more detailed information at info@benchchem.com.
Scientific Research Applications
Coatings
Overview : Urethane acrylates are primarily utilized in the coatings industry due to their ability to form durable and protective films upon curing. They are commonly employed in both aliphatic and aromatic forms.
- Photocurable Coatings : Urethane acrylate oligomers can be photopolymerized using ultraviolet (UV) radiation, leading to rapid curing processes that enhance production efficiency. These coatings are applied on various substrates like wood, plastics, and metals to improve their mechanical properties and resistance to environmental factors .
- Mechanical Property Enhancement : Research has demonstrated that formulations incorporating urethane acrylates significantly improve the mechanical properties of coated surfaces. For example, studies have shown enhanced hardness and flexibility when using aliphatic urethane acrylates compared to traditional coatings .
Type of Coating | Properties Enhanced | Applications |
---|---|---|
Aliphatic Urethane | UV stability, flexibility | Wood finishes, automotive |
Aromatic Urethane | Toughness, chemical resistance | Industrial machinery, electronics |
Adhesives
Overview : Urethane acrylates are integral in formulating UV-curable adhesives, which are widely used in the electronics and healthcare sectors.
- UV-Curable Adhesives : These adhesives combine the benefits of urethane acrylates with modified acrylic esters to provide strong bonding capabilities while allowing for quick curing times. The composition can be tailored to achieve specific adhesive properties based on application needs .
- Performance Studies : Research indicates that varying the ratios of prepolymers and diluents can optimize adhesive performance. For instance, studies have shown that modifying the composition can enhance adhesion strength and reduce curing time without compromising mechanical integrity .
Composites
Overview : The integration of urethane acrylates into composite materials has gained traction due to their ability to improve mechanical properties when reinforced with fibers such as aramid or graphene.
- Graphene-Reinforced Composites : Recent studies have highlighted the potential of urethane-acrylate thermoset resins (UATR) when combined with graphenic materials. These composites exhibit superior mechanical properties compared to traditional epoxy systems, making them suitable for high-performance applications .
- Case Studies : A comparative study demonstrated that adding graphene significantly improved tensile strength and modulus in UATR composites. This advancement positions urethane acrylates as a promising alternative in the composite materials sector .
Composite Type | Reinforcement Material | Mechanical Properties Enhanced |
---|---|---|
UATR with Graphene | Graphene | Increased tensile strength |
UATR with Aramid | Aramid fibers | Enhanced impact resistance |
3D Printing
Overview : Urethane acrylates are increasingly used in additive manufacturing, particularly in digital light processing (DLP) 3D printing technologies.
- Photopolymer Resins : Various formulations of urethane acrylates have been developed for use as photopolymer resins in DLP printing. These resins exhibit tunable mechanical properties that can be adjusted based on the application requirements .
- Research Findings : A study involving five different urethane acrylates formulated for DLP printing revealed significant differences in mechanical performance based on exposure times and material compositions. The results indicated that certain formulations achieved higher flexural strength and hardness compared to conventional acrylic resins .
Resin Type | Exposure Time | Mechanical Properties Achieved |
---|---|---|
Aliphatic Urethane | 15 minutes | High flexural strength |
Aromatic Urethane | 30 minutes | Enhanced hardness |
Properties
Molecular Formula |
C6H11NO4 |
---|---|
Molecular Weight |
161.16 g/mol |
IUPAC Name |
ethyl carbamate;prop-2-enoic acid |
InChI |
InChI=1S/C3H7NO2.C3H4O2/c1-2-6-3(4)5;1-2-3(4)5/h2H2,1H3,(H2,4,5);2H,1H2,(H,4,5) |
InChI Key |
UHESRSKEBRADOO-UHFFFAOYSA-N |
Canonical SMILES |
CCOC(=O)N.C=CC(=O)O |
Synonyms |
urethane acrylate |
Origin of Product |
United States |
Synthesis routes and methods I
Procedure details
Synthesis routes and methods II
Procedure details
Synthesis routes and methods III
Procedure details
Synthesis routes and methods IV
Procedure details
Synthesis routes and methods V
Procedure details
Disclaimer and Information on In-Vitro Research Products
Please be aware that all articles and product information presented on BenchChem are intended solely for informational purposes. The products available for purchase on BenchChem are specifically designed for in-vitro studies, which are conducted outside of living organisms. In-vitro studies, derived from the Latin term "in glass," involve experiments performed in controlled laboratory settings using cells or tissues. It is important to note that these products are not categorized as medicines or drugs, and they have not received approval from the FDA for the prevention, treatment, or cure of any medical condition, ailment, or disease. We must emphasize that any form of bodily introduction of these products into humans or animals is strictly prohibited by law. It is essential to adhere to these guidelines to ensure compliance with legal and ethical standards in research and experimentation.