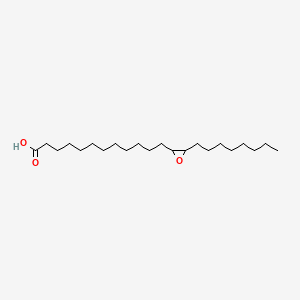
Ppolypropylene(melt flow rate)
Overview
Description
Melt Flow Rate (MFR), also termed Melt Flow Index (MFI), is a critical metric for assessing the flow properties of polypropylene (PP) under standardized conditions (230°C, 2.16 kg load per ASTM D1238) . It quantifies the mass of molten PP extruded through a capillary die over 10 minutes (g/10 min) and inversely correlates with molecular weight: higher MFR indicates lower molecular weight and reduced melt viscosity . This property is pivotal in determining PP's processability—higher MFR grades (e.g., 1,550 g/10 min) are optimized for high-speed processes like melt-blown nonwovens, while lower MFR grades (e.g., 20 g/10 min) suit conventional extrusion or injection molding . However, increased MFR often compromises mechanical properties, such as impact strength, due to shorter polymer chains .
Preparation Methods
Synthetic Routes and Reaction Conditions
Polypropylene is synthesized through the polymerization of propylene monomers. The most common method is the Ziegler-Natta polymerization, which involves the use of titanium chloride catalysts and aluminum alkyl co-catalysts. The reaction typically occurs at low temperatures and pressures, resulting in high molecular weight polymers .
Industrial Production Methods
In industrial settings, polypropylene is produced using either gas-phase polymerization or bulk polymerization processes. These methods involve the polymerization of propylene in the presence of a catalyst system, followed by the removal of unreacted monomers and the stabilization of the polymer. The melt flow rate of the resulting polypropylene can be controlled by adjusting the polymerization conditions and the molecular weight distribution .
Chemical Reactions Analysis
Types of Reactions
Polypropylene undergoes various chemical reactions, including oxidation, reduction, and substitution. Oxidation reactions can occur during processing or exposure to environmental conditions, leading to the formation of hydroperoxides and carbonyl compounds. Reduction reactions are less common but can be induced using specific reducing agents .
Common Reagents and Conditions
Common reagents used in the chemical reactions of polypropylene include oxygen, hydrogen, and various catalysts. Oxidation reactions typically occur at elevated temperatures and in the presence of oxygen, while reduction reactions require specific reducing agents and controlled conditions .
Major Products Formed
The major products formed from the oxidation of polypropylene include hydroperoxides, alcohols, ketones, and carboxylic acids. These oxidation products can affect the mechanical properties and stability of the polymer .
Scientific Research Applications
Understanding Melt Flow Rate (MFR)
Melt flow rate is defined as the mass of polymer that flows through a specific capillary under a given load and temperature, typically measured in grams per 10 minutes. It serves as an indicator of the polymer's viscosity when melted. Higher MFR values indicate lower viscosity, allowing for easier processing, while lower MFR values suggest higher viscosity, suitable for more robust applications .
Applications Based on MFR
The applications of polypropylene can be categorized based on their melt flow rates:
-
High Melt Flow Rate Polypropylene (MFR > 20 g/10 min)
- Packaging : Ideal for thin-walled containers such as yogurt cups and food packaging due to its ability to fill molds quickly.
- Disposable Products : Used in manufacturing disposable cutlery and plates where rapid production is essential.
- Textiles : Employed in non-woven fabrics and geotextiles that require high processing speeds .
- Medium Melt Flow Rate Polypropylene (MFR 5-20 g/10 min)
- Low Melt Flow Rate Polypropylene (MFR < 5 g/10 min)
Case Study 1: Predictive Modeling of MFR
A study conducted on the predictive modeling of melt flow rates for different polypropylene blends demonstrated that understanding MFR can significantly enhance recycling processes. The research involved characterizing various grades of polypropylene, including virgin homopolymers and post-consumer recyclates, achieving high accuracy in predicting MFR using models like Arrhenius and Cragoe . This predictive capability supports the development of recycling technologies by optimizing processing conditions.
Case Study 2: Effect of Composition on MFR
Research examining the effects of kaolin geo-filler on the melt flow index of polypropylene composites revealed significant insights into material behavior. The study found that incorporating specific percentages of kaolin improved the melt flow index, enhancing processability while maintaining mechanical properties. This highlights the importance of material composition in tailoring polypropylene for specific applications .
Table 1: Comparison of Polypropylene Types Based on MFR
Type | MFR Range (g/10 min) | Typical Applications |
---|---|---|
High Melt Flow Rate | > 20 | Packaging, disposable products, textiles |
Medium Melt Flow Rate | 5 - 20 | Automotive components, household goods |
Low Melt Flow Rate | < 5 | Industrial applications, medical devices |
Table 2: Impact of Filler Composition on MFR
Filler Type | Filler Percentage (wt%) | MFR (g/10 min) |
---|---|---|
Kaolin | 0 | 5 |
Kaolin | 6 | 8 |
Kaolin | 8 | 7 |
Kaolin Geo-filler | 0 | 5 |
Kaolin Geo-filler | 6 | 9 |
Mechanism of Action
The mechanism of action of polypropylene involves its ability to form strong intermolecular bonds, resulting in high tensile strength and durability. The polymer’s molecular structure, consisting of repeating propylene units, contributes to its crystallinity and resistance to chemical degradation. The melt flow rate of polypropylene is influenced by the polymer’s molecular weight and the degree of branching, which affect its flow behavior during processing .
Comparison with Similar Compounds
Polypropylene vs. Polyethylene (PE)
- MFR Range : PP typically exhibits MFR values spanning 1.5–1,550 g/10 min , while low-density polyethylene (LDPE) and high-density polyethylene (HDPE) are measured at 190°C (per ASTM D1238) with distinct MFR ranges (e.g., LDPE: 0.3–50 g/10 min) .
- Blending Effects: PP/LDPE blends show non-linear MFR behavior. For high-MFR PP (e.g., 30 g/10 min), blending with LDPE at a 50/50 ratio maximizes MFR due to interfacial slip between polymers . In contrast, HDPE additions to PP reduce MFR by increasing viscosity .
Table 1: MFR of PP vs. PE Blends
Polymer/Blend | MFR (g/10 min) | Conditions | Source |
---|---|---|---|
PP Homopolymer | 1.5 | 230°C, 2.16 kg | |
PP/LDPE (50/50) | 30 (peak) | 230°C, 2.16 kg | |
HDPE | 0.8–1.2 | 190°C, 2.16 kg |
Polypropylene vs. Polyethylene Terephthalate (PET)
- Blend Performance : Adding PET waste to PP reduces MFR by 10–15% due to PET’s higher melt viscosity and incompatibility, which disrupts flow . For example, a PET/PP composite showed an MFR reduction from 25 g/10 min (pure PP) to 22 g/10 min .
- Thermal Stability : PP/PET blends exhibit lower Vicat softening temperatures (a measure of heat resistance) compared to pure PP, further limiting high-temperature applications .
Linear vs. Long-Chain Branched Polypropylene (LCB-PP)
- MFR and Melt Strength : Linear PP (L-PP) with high MFR (e.g., 1,550 g/10 min) is ideal for melt-blown fibers but suffers from low melt strength. LCB-PP, synthesized via reactive extrusion, has lower MFR (e.g., 60 g/10 min) but superior melt strength, enabling stable foaming and thermoforming .
- Rheological Behavior: LCB-PP demonstrates higher extensional viscosity at low strain rates, reducing fiber diameter variability in nonwovens (coefficient of variation: 40% for L-PP vs. 30% for LCB-PP) .
Virgin vs. Recycled Polypropylene
- MFR Variance : Recycled PP (RPP) often shows a 5–10% higher MFR than virgin PP (VPP) due to chain scission during recycling. For instance, RPP exhibited an MFR of 25 g/10 min vs. 23 g/10 min for VPP .
- Thermal Properties : RPP may display dual melting peaks (163°C for PP, 110–120°C for polyethylene contaminants), unlike VPP’s single peak .
Key Research Findings
Additives and Fillers : Incorporating 20–40 wt% post-consumer recyclates into PP compounds alters MFR within ±10% of calculated values (via Arrhenius mixing rule), except for highly contaminated blends (error up to 20%) .
Processing Conditions : Foaming PP with gas content >5 wt% reduces MFR by increasing melt viscosity, necessitating adjusted pressure parameters .
Molecular Weight Distribution : Broadening PP’s molecular weight distribution (e.g., via controlled rheology) enhances MFR stability during multiple reprocessing cycles, mitigating property degradation .
Biological Activity
Polypropylene (PP) is a widely used thermoplastic polymer known for its versatility and favorable properties in various applications, including packaging, textiles, automotive parts, and medical devices. The biological activity of polypropylene, particularly concerning its melt flow rate (MFR), is an important factor influencing its processing characteristics and end-use performance. This article explores the biological activity of polypropylene with a focus on MFR, incorporating data tables, case studies, and detailed research findings.
Understanding Melt Flow Rate (MFR)
The melt flow rate is a measure of the viscosity of a polymer melt and is defined as the weight of polymer that can be extruded through a specific die under controlled conditions over a set period. It is typically measured in grams per 10 minutes (g/10 min). A higher MFR indicates lower viscosity, which can enhance processability during manufacturing.
Measurement Methodology
The MFR is measured according to ASTM D1238 standards, where a sample of polypropylene is heated to a specified temperature (usually around 230°C) and subjected to a defined load (commonly 2.16 kg). The resulting MFR values provide insights into the molecular weight and flow characteristics of the polymer.
Case Studies
- Polypropylene in Medical Applications
-
Environmental Impact
- The degradation behavior of polypropylene during reprocessing has been studied extensively. Reprocessing cycles lead to an increase in MFR due to molecular weight reduction caused by mechanical shear forces. This degradation can influence the biological activity of PP when used in environmental applications, such as biodegradable composites .
Table 1: Melt Flow Rate Variations with Filler Composition
Sample Composition | Polypropylene (wt%) | Filler Type | Melt Flow Rate (g/10 min) |
---|---|---|---|
PP | 100 | None | 5.0 |
PP/Kaolin | 98 | Kaolin | 6.5 |
PP/Kaolin | 94 | Kaolin | 8.0 |
PP/Geo-filler | 94 | Kaolin Geo | 9.5 |
This table illustrates how the incorporation of fillers affects the MFR of polypropylene composites, indicating that certain fillers can enhance flow characteristics .
Table 2: Biological Activity Assessment of Polypropylene
Research Findings
Recent studies have focused on predictive modeling for MFR based on various blends of polypropylene. The research demonstrated that different grades of PP, including virgin homopolymers and post-consumer recyclates, exhibit distinct rheological properties that can be optimized for specific applications . These findings are crucial for improving recycling technologies and enhancing the sustainability of polypropylene use.
Furthermore, investigations into the crystallization behavior of polypropylene reveal that variations in processing conditions significantly affect its physical properties and biological activity. For instance, controlling the crystallization temperature can lead to different morphologies that impact both mechanical performance and biocompatibility .
Q & A
Basic Research Questions
Q. How is melt flow rate (MFR) experimentally measured for polypropylene, and what standards ensure reproducibility?
MFR is measured using an extrusion plastometer under standardized conditions (ASTM D1238-04c or ISO 1133). The polymer is melted at 230°C and extruded through a capillary die under a 2.16 kg load. The extrudate mass over 10 minutes (g/10 min) is recorded. Key steps include:
- Pre-drying samples to remove moisture.
- Calibrating temperature and piston weight to ±0.1°C and ±0.5% accuracy, respectively.
- Repeating tests to account for variability (e.g., ±5% tolerance for homogeneous samples) .
Q. Why does MFR inversely correlate with molecular weight, and how does this affect material selection for processing?
MFR is inversely proportional to molecular weight (MW) due to chain entanglement: higher MW increases viscosity, reducing flow. For example, polypropylene with MFR < 2 g/10 min (high MW) is used for pipes (toughness), while MFR > 8 g/10 min (low MW) suits injection molding (ease of flow). Direct MW-MFR correlations require polymers with identical catalyst systems and processing histories to avoid skewed results .
Q. What are the limitations of MFR as a rheological parameter for polypropylene?
MFR is a single-shear-rate measurement (low shear, ~0.1–1 s⁻¹), making it inadequate for predicting behavior under high-shear processing (e.g., injection molding at 10³–10⁴ s⁻¹). Capillary rheometry or dynamic mechanical analysis (DMA) is recommended for full viscosity-shear rate profiles. Additionally, MFR does not account for molecular weight distribution (MWD), which affects shear thinning .
Advanced Research Questions
Q. How can researchers resolve contradictions between MFR data and observed processing behavior in recycled polypropylene (rPP)?
Contradictions often arise from inconsistent feedstock (e.g., contaminants, mixed polymer grades). Methodological solutions include:
- Pre-sorting and purification : Remove polar polymers (e.g., EVOH) via solvent extraction.
- Additive blending : Incorporate 2–10 wt% maleic anhydride-grafted styrene-ethylene/butylene (g-MAH) to lower MFR by 15–30% via crosslinking .
- Statistical analysis : Use ANOVA to compare batch variability (e.g., Table 7 in ).
Q. What experimental designs are effective for analyzing MFR dependence on polymerization conditions?
Controlled studies should vary chain-transfer agents (e.g., hydrogen concentration) during polymerization. For example:
- DOE setup : Hydrogen concentration (0.1–1.0 mol%) vs. MFR (measured at 230°C/2.16 kg).
- Characterization : Pair MFR with gel permeation chromatography (GPC) for MW and MWD validation. Correlations are valid only within the same catalyst family (e.g., Ziegler-Natta) .
Q. How does molecular weight distribution (MWD) influence MFR interpretation in copolymer polypropylene?
Broad MWD (e.g., block copolymers) enhances shear thinning, causing higher flow rates under processing conditions despite similar MFR values. The Flow Rate Ratio (FRR = MFR@10 kg / MFR@2.16 kg) quantifies this: FRR > 30 indicates broad MWD, impacting mold-filling behavior .
Q. What methodologies address MFR instability in polypropylene composites with fillers or regranulates?
For composites (e.g., glass fiber-filled PP):
- Pre-drying : Minimize moisture-induced degradation.
- MFR adjustment : Add 5–15 wt% ethylene-α-olefin copolymers to stabilize flow.
- In-line monitoring : Use rheometers during extrusion to detect real-time MFR shifts .
Q. Methodological Considerations
Q. How should researchers statistically validate MFR data from heterogeneous samples (e.g., recycled PP)?
Apply 95% confidence intervals and t-tests to compare means against supplier data. For example, undergraduate experiments using four PP grades showed ±8% MFR variability, requiring n ≥ 5 replicates for significance .
Q. Why do MFR and viscosity measurements sometimes conflict, and how can this be resolved?
MFR-viscosity inversions occur in pseudoplastic materials (e.g., high-MW PP) due to shear-rate mismatches. Address this by:
- Conducting capillary rheometry at shear rates matching processing conditions.
- Calculating the power-law index (n) from viscosity curves .
Q. What advanced techniques complement MFR for comprehensive polymer characterization?
Pair MFR with:
- Thermogravimetric analysis (TGA) : Assess thermal stability (e.g., degradation during recycling).
- Differential scanning calorimetry (DSC) : Measure melting points (Tm) affecting flow .
- FTIR : Detect oxidation or contaminants altering MFR .
Properties
IUPAC Name |
12-(3-octyloxiran-2-yl)dodecanoic acid | |
---|---|---|
Details | Computed by Lexichem TK 2.7.0 (PubChem release 2021.05.07) | |
Source | PubChem | |
URL | https://pubchem.ncbi.nlm.nih.gov | |
Description | Data deposited in or computed by PubChem | |
InChI |
InChI=1S/C22H42O3/c1-2-3-4-5-11-14-17-20-21(25-20)18-15-12-9-7-6-8-10-13-16-19-22(23)24/h20-21H,2-19H2,1H3,(H,23,24) | |
Details | Computed by InChI 1.0.6 (PubChem release 2021.05.07) | |
Source | PubChem | |
URL | https://pubchem.ncbi.nlm.nih.gov | |
Description | Data deposited in or computed by PubChem | |
InChI Key |
NSYDMBURIUSUDH-UHFFFAOYSA-N | |
Details | Computed by InChI 1.0.6 (PubChem release 2021.05.07) | |
Source | PubChem | |
URL | https://pubchem.ncbi.nlm.nih.gov | |
Description | Data deposited in or computed by PubChem | |
Canonical SMILES |
CCCCCCCCC1C(O1)CCCCCCCCCCCC(=O)O | |
Details | Computed by OEChem 2.3.0 (PubChem release 2021.05.07) | |
Source | PubChem | |
URL | https://pubchem.ncbi.nlm.nih.gov | |
Description | Data deposited in or computed by PubChem | |
Molecular Formula |
C22H42O3 | |
Details | Computed by PubChem 2.1 (PubChem release 2021.05.07) | |
Source | PubChem | |
URL | https://pubchem.ncbi.nlm.nih.gov | |
Description | Data deposited in or computed by PubChem | |
DSSTOX Substance ID |
DTXSID10337657, DTXSID20864146 | |
Record name | cis-13,14-Epoxydocosanoic acid | |
Source | EPA DSSTox | |
URL | https://comptox.epa.gov/dashboard/DTXSID10337657 | |
Description | DSSTox provides a high quality public chemistry resource for supporting improved predictive toxicology. | |
Record name | 12-(3-Octyloxiran-2-yl)dodecanoic acid | |
Source | EPA DSSTox | |
URL | https://comptox.epa.gov/dashboard/DTXSID20864146 | |
Description | DSSTox provides a high quality public chemistry resource for supporting improved predictive toxicology. | |
Molecular Weight |
354.6 g/mol | |
Details | Computed by PubChem 2.1 (PubChem release 2021.05.07) | |
Source | PubChem | |
URL | https://pubchem.ncbi.nlm.nih.gov | |
Description | Data deposited in or computed by PubChem | |
CAS No. |
28590-30-9 | |
Record name | cis-13,14-Epoxydocosanoic acid | |
Source | EPA DSSTox | |
URL | https://comptox.epa.gov/dashboard/DTXSID10337657 | |
Description | DSSTox provides a high quality public chemistry resource for supporting improved predictive toxicology. | |
Disclaimer and Information on In-Vitro Research Products
Please be aware that all articles and product information presented on BenchChem are intended solely for informational purposes. The products available for purchase on BenchChem are specifically designed for in-vitro studies, which are conducted outside of living organisms. In-vitro studies, derived from the Latin term "in glass," involve experiments performed in controlled laboratory settings using cells or tissues. It is important to note that these products are not categorized as medicines or drugs, and they have not received approval from the FDA for the prevention, treatment, or cure of any medical condition, ailment, or disease. We must emphasize that any form of bodily introduction of these products into humans or animals is strictly prohibited by law. It is essential to adhere to these guidelines to ensure compliance with legal and ethical standards in research and experimentation.