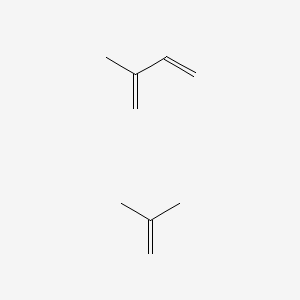
Butyl rubber
Overview
Description
Butyl rubber (IIR) is a synthetic elastomer synthesized via copolymerization of isobutylene (97–99%) with a small proportion of isoprene (1–3%) . This unique structure, characterized by high saturation and densely packed methyl groups, imparts exceptional properties such as:
- Low gas and moisture permeability (superior to natural rubber (NR) and styrene-butadiene rubber (SBR)) .
- Broad operational temperature range (−50°C to 120°C) .
Applications span automotive tires (inner liners), pharmaceutical stoppers, seals, and vibration-damping components . Halogenated derivatives, bromobutyl (BIIR) and chlorobutyl (CIIR), enhance curing versatility and adhesion while retaining IIR’s impermeability .
Preparation Methods
Synthetic Routes and Reaction Conditions
The polymerization of 2-methylpropene with 2-methyl-1,3-butadiene is typically carried out in the presence of a catalyst. One common method involves the use of azobisisobutyronitrile as a radical initiator. The reaction is conducted in a solvent mixture, such as 2,2,4-trimethylpentane and carbon tetrachloride, under an inert nitrogen atmosphere. The reaction mixture is heated to around 75°C, and the polymerization process is allowed to proceed for several hours.
Industrial Production Methods
In industrial settings, the production of butyl rubber involves the copolymerization of isobutylene with isoprene in large reactors. The process is typically carried out at low temperatures to control the polymerization rate and achieve the desired molecular weight distribution. The resulting polymer is then purified and processed into various forms, such as sheets, granules, or coatings .
Chemical Reactions Analysis
Types of Reactions
Butyl rubber undergoes several types of chemical reactions, including:
Oxidation: The polymer can be oxidized to form various oxidation products.
Substitution: The polymer can undergo substitution reactions, where hydrogen atoms are replaced by other functional groups.
Cross-linking: The polymer chains can be cross-linked through vulcanization, which involves the formation of sulfur bridges between polymer chains.
Common Reagents and Conditions
Oxidation: Common oxidizing agents include hydrogen peroxide and ozone.
Substitution: Reagents such as halogens (e.g., chlorine, bromine) are used for substitution reactions.
Cross-linking: Sulfur or sulfur-containing compounds are used in the vulcanization process.
Major Products Formed
Oxidation: Oxidized derivatives of the polymer.
Substitution: Halogenated polymers.
Cross-linking: Vulcanized rubber with enhanced mechanical properties.
Scientific Research Applications
Key Properties of Butyl Rubber
- Low Permeability : Exceptional barrier properties against gases and moisture make this compound ideal for applications requiring retention of these elements.
- Chemical Resistance : this compound exhibits strong resistance to chemical degradation, particularly in contact with polar and non-polar solvents.
- Vibration Damping : Its high energy absorption capability allows for effective vibration damping in automotive and industrial applications.
Major Applications
-
Tire Industry
- Approximately 86% of this compound is utilized in tires and inner tubes due to its low gas permeability, which enhances fuel efficiency and reduces CO2 emissions .
- Case Study : The use of halothis compound in tire innerliners significantly improves air retention, contributing to better tire performance and longevity .
-
Pharmaceuticals
- This compound is essential in creating closures for infusion containers, injection vials, and blood-collection tubes due to its biological inertness and low extractables .
- Case Study : A study demonstrated that this compound stoppers used for drug delivery systems maintained integrity under various conditions, ensuring safe medication delivery .
- Sealants and Adhesives
Sealant Type | Permeability Rate (g/m²/day) | Application Area |
---|---|---|
This compound Sealant | 0.1 | Automotive |
Silicone Sealant | 0.5 | Construction |
Polyurethane Sealant | 0.3 | General Purpose |
- Protective Clothing
-
Automotive Applications
- Used in engine mounts and body mounts to absorb vibrations effectively.
- Data Table : Mechanical properties of this compound compared to other elastomers.
Property | This compound | Natural Rubber | Synthetic Rubber |
---|---|---|---|
Tensile Strength (MPa) | 15 | 20 | 18 |
Elongation at Break (%) | 300 | 500 | 400 |
Hardness (Shore A) | 60 | 50 | 55 |
- Electronics
Recent Developments
Recent research has focused on enhancing the properties of this compound through various modifications:
- Halogenation Techniques : New methods have been developed to improve thermal stability and resistance to aggressive media through halogenation processes .
- Composite Materials : Studies have shown that incorporating fillers such as silica can enhance mechanical strength and hydrophobicity while maintaining low permeability .
Mechanism of Action
The mechanism by which Butyl rubber exerts its effects involves the formation of a highly stable polymer network. The polymer chains are cross-linked through vulcanization, which enhances the mechanical strength and chemical resistance of the material. The molecular targets and pathways involved in this process include the formation of sulfur bridges between polymer chains, which create a three-dimensional network structure .
Comparison with Similar Compounds
Natural Rubber (NR)
- Gas Permeability : Butyl rubber exhibits 8–10 times lower air permeability than NR due to its densely packed structure .
- Thermal Stability : NR degrades above 80°C, whereas IIR maintains stability up to 120°C . However, NR surpasses IIR in tensile strength (25–30 MPa vs. 10–20 MPa) and elasticity .
- Chemical Resistance : IIR resists acids, alkalis, and polar solvents better than NR, which swells in hydrocarbons .
Styrene-Butadiene Rubber (SBR)
- Impermeability : IIR’s gas retention is 5–7 times superior to SBR, making it ideal for tire inner liners .
- Ozone Resistance : SBR requires stabilizers to resist ozone, while IIR inherently resists degradation .
- Mechanical Properties : SBR outperforms IIR in abrasion resistance and load-bearing capacity .
Ethylene Propylene Diene Monomer (EPDM)
- Thermal Stability : Both EPDM and IIR operate up to 120°C, but EPDM exhibits better resistance to thermal aging .
- Mechanical Performance : EPDM has higher tensile strength (15–25 MPa) and elongation at break compared to IIR . Blending IIR with EPDM improves thermal stability but reduces tensile strength due to crosslinking limitations .
- Chemical Compatibility: EPDM resists polar fluids (e.g., glycols), while IIR is better for non-polar hydrocarbons .
Halobutyl Rubbers (BIIR/CIIR)
- Curing Flexibility: Halogenation enables covalent bonding with other rubbers (e.g., NR) and metals, unlike non-halogenated IIR .
- Enhanced Resistance : BIIR/CIIR offer superior UV, ozone, and chemical resistance compared to standard IIR .
- Applications : Widely used in pharmaceutical closures and tire inner liners for improved adhesion .
Nitrile Rubber (NBR)
- Polarity: NBR’s polar nitrile groups provide excellent oil resistance, whereas non-polar IIR fails in oil-rich environments .
- Temperature Range : NBR operates up to 100°C, underperforming IIR in high-temperature applications .
Neoprene (CR)
- Flame Resistance : CR inherently resists flames, while IIR requires additives .
- Chemical Compatibility : CR degrades in oxidizing acids, whereas IIR remains stable .
Data Tables
Table 1: Key Properties of this compound and Comparable Elastomers
Property | Butyl (IIR) | NR | SBR | EPDM | BIIR/CIIR | NBR |
---|---|---|---|---|---|---|
Gas Permeability | Very Low | High | High | Medium | Very Low | Medium |
Max. Temp. (°C) | 120 | 80 | 100 | 120 | 130 | 100 |
Tensile Strength (MPa) | 10–20 | 25–30 | 20–25 | 15–25 | 12–22 | 20–25 |
Ozone Resistance | Excellent | Poor | Poor | Good | Excellent | Good |
Chemical Resistance* | A/B | C | C | A | A | B |
*Chemical resistance ratings for non-polar solvents (e.g., hydrocarbons). A = Excellent, B = Good, C = Poor .
Table 2: Chemical Compatibility Ratings (Selected Chemicals)
Chemical | IIR | EPDM | NBR | CR |
---|---|---|---|---|
Butyl Alcohol | B | B | A | A |
Ethylene Glycol | A | A | A | A |
Trichloroethylene | U | U | U | A |
Fatty Acids | C | C | B | B |
Key: A = Resistant, B = Moderate, C = Poor, U = Unsuitable .
Research Findings
- Blending with EPDM : IIR/EPDM composites show 15–20% higher thermal stability than pure EPDM but suffer reduced tensile strength at irradiation doses >100 kGy .
- Halogenation Effects : Bromination increases IIR’s cure rate by 30% compared to chlorination, enhancing adhesion in tire manufacturing .
- Dynamic Properties: Non-polar IIR exhibits lower hysteresis loss than polar NBR, critical for vibration damping .
Q & A
Basic Research Questions
Q. What are the key physicochemical properties of butyl rubber that influence its gas barrier performance, and how are they experimentally measured?
this compound’s gas impermeability stems from its low polyisoprene content and dense molecular structure. To quantify this, researchers use gas permeability tests (e.g., ASTM D1434) under controlled temperature and pressure. Parameters like permeability coefficient (Barrer units) and diffusion activation energy are derived using time-lag methods or sorption experiments .
Q. How do researchers assess the thermal stability of this compound, and what are the standard experimental protocols?
Thermogravimetric analysis (TGA) and differential scanning calorimetry (DSC) are primary methods. TGA measures mass loss under programmed heating (e.g., 10°C/min in nitrogen), identifying decomposition temperatures. DSC detects glass transition (Tg) and exothermic/endothermic events. ASTM E2550 and E1131 provide guidelines for data interpretation .
Q. What methodologies are used to evaluate the cross-linking efficiency of this compound during vulcanization?
Cross-linking is quantified via swelling tests (ASTM D471) in solvents like toluene, calculating the Flory-Rehner equation to determine cross-link density. Dynamic mechanical analysis (DMA) measures storage/loss moduli to assess network formation. Comparative studies often contrast sulfur vulcanization with peroxide-initiated systems .
Advanced Research Questions
Q. How can contradictory data on this compound’s aging behavior under UV exposure be resolved in experimental studies?
Discrepancies arise from variations in UV intensity, sample thickness, and stabilizer additives. Advanced approaches combine accelerated weathering tests (e.g., ASTM G154) with FTIR spectroscopy to track carbonyl index changes. Statistical models (e.g., Weibull analysis) correlate degradation kinetics with experimental parameters, while controlled replicate studies minimize noise .
Q. What experimental designs optimize the mechanical properties of this compound-nanocomposite blends?
Researchers use a factorial design to test variables like nanofiller type (e.g., clay, silica), loading (1–5 wt%), and dispersion methods (melt mixing vs. solution casting). Mechanical properties (tensile strength, elongation) are measured via ASTM D412. Transmission electron microscopy (TEM) validates nanofiller dispersion, and rheometry assesses processability .
Q. How do molecular dynamics (MD) simulations enhance the understanding of gas diffusion mechanisms in this compound?
MD simulations model gas molecules (e.g., O₂, N₂) traversing the polymer matrix. Parameters like free volume distribution and chain mobility are analyzed using software (e.g., LAMMPS). Experimental validation involves correlating simulated diffusion coefficients with gravimetric sorption data. This hybrid approach resolves atomic-scale mechanisms inaccessible to traditional methods .
Q. Methodological Challenges & Data Interpretation
Q. What statistical methods are appropriate for analyzing variability in this compound’s compression set data?
Compression set (ASTM D395) variability often stems from curing inconsistencies. Researchers employ ANOVA to identify significant factors (e.g., curing time, temperature). Non-parametric tests (e.g., Kruskal-Wallis) handle non-normal distributions. Bootstrapping improves confidence intervals for small datasets .
Q. How do researchers address ethical and safety concerns in this compound studies involving hazardous additives (e.g., halogenated compounds)?
Safety protocols include fume hood use for volatile additives and toxicity screenings (e.g., LC50 assays). Ethical review boards require risk assessments for human/animal studies. Alternatives like brominated this compound are tested under ISO 10993 for biocompatibility .
Properties
CAS No. |
68081-82-3 |
---|---|
Molecular Formula |
C9H16 |
Molecular Weight |
124.22 g/mol |
IUPAC Name |
2-methylbuta-1,3-diene;2-methylprop-1-ene |
InChI |
InChI=1S/C5H8.C4H8/c1-4-5(2)3;1-4(2)3/h4H,1-2H2,3H3;1H2,2-3H3 |
InChI Key |
VHOQXEIFYTTXJU-UHFFFAOYSA-N |
SMILES |
CC(=C)C.CC(=C)C=C |
Canonical SMILES |
CC(=C)C.CC(=C)C=C |
Key on ui other cas no. |
68441-14-5 9010-85-9 68081-82-3 |
Synonyms |
butyl rubber |
Origin of Product |
United States |
Synthesis routes and methods I
Procedure details
Synthesis routes and methods II
Procedure details
Synthesis routes and methods III
Procedure details
Synthesis routes and methods IV
Procedure details
Retrosynthesis Analysis
AI-Powered Synthesis Planning: Our tool employs the Template_relevance Pistachio, Template_relevance Bkms_metabolic, Template_relevance Pistachio_ringbreaker, Template_relevance Reaxys, Template_relevance Reaxys_biocatalysis model, leveraging a vast database of chemical reactions to predict feasible synthetic routes.
One-Step Synthesis Focus: Specifically designed for one-step synthesis, it provides concise and direct routes for your target compounds, streamlining the synthesis process.
Accurate Predictions: Utilizing the extensive PISTACHIO, BKMS_METABOLIC, PISTACHIO_RINGBREAKER, REAXYS, REAXYS_BIOCATALYSIS database, our tool offers high-accuracy predictions, reflecting the latest in chemical research and data.
Strategy Settings
Precursor scoring | Relevance Heuristic |
---|---|
Min. plausibility | 0.01 |
Model | Template_relevance |
Template Set | Pistachio/Bkms_metabolic/Pistachio_ringbreaker/Reaxys/Reaxys_biocatalysis |
Top-N result to add to graph | 6 |
Feasible Synthetic Routes
Disclaimer and Information on In-Vitro Research Products
Please be aware that all articles and product information presented on BenchChem are intended solely for informational purposes. The products available for purchase on BenchChem are specifically designed for in-vitro studies, which are conducted outside of living organisms. In-vitro studies, derived from the Latin term "in glass," involve experiments performed in controlled laboratory settings using cells or tissues. It is important to note that these products are not categorized as medicines or drugs, and they have not received approval from the FDA for the prevention, treatment, or cure of any medical condition, ailment, or disease. We must emphasize that any form of bodily introduction of these products into humans or animals is strictly prohibited by law. It is essential to adhere to these guidelines to ensure compliance with legal and ethical standards in research and experimentation.