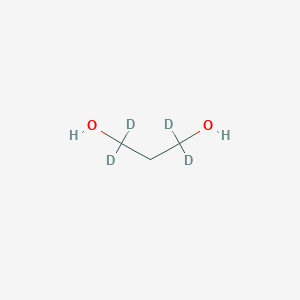
Ethylene-d4 glycol
Overview
Description
Ethylene-d4 glycol, also known as deuterated ethylene glycol, is a deuterated form of ethylene glycol. It is a colorless, odorless liquid that is commonly used as a solvent in nuclear magnetic resonance (NMR) spectroscopy due to its unique properties. The molecular formula of this compound is HOCD2CD2OH, and it has a molecular weight of 66.09 g/mol .
Mechanism of Action
Target of Action
Ethylene-d4 glycol, a deuterated variant of ethylene glycol, shares similar properties and reactivity with its non-deuterated counterpart . It acts as a diol, featuring two hydroxyl groups . These hydroxyl groups allow it to participate in various chemical reactions, making it a versatile compound in biochemical processes.
Mode of Action
The mode of action of this compound is primarily through its interaction with its targets via its hydroxyl groups . These groups enable it to participate in a wide range of chemical reactions, thereby influencing various biochemical processes.
Biochemical Pathways
This compound has been used in the preparation of perdeuterated ethylenediaminetetraacetate tetraanion (EDTA-d 124-) for use in the spectroscopic analysis of cadmium-EDTA complex . This indicates that it can participate in complex biochemical pathways involving the formation of chelating agents like EDTA.
Pharmacokinetics
It is known that stable heavy isotopes of hydrogen, carbon, and other elements have been incorporated into drug molecules, largely as tracers for quantitation during the drug development process
Result of Action
Its use in the preparation of perdeuterated EDTA suggests that it may play a role in the formation of chelating agents and the sequestration of metal ions .
Biochemical Analysis
Biochemical Properties
Ethylene-d4 glycol plays a significant role in biochemical reactions. It serves as a starting material in the preparation of perdeuterated ethylenediaminetetraacetate tetraanion (EDTA-d 124-), which is used in the spectroscopic analysis of cadmium-EDTA complex
Cellular Effects
It’s non-deuterated counterpart, ethylene glycol, is known to have significant effects on cells, particularly in cases of poisoning
Molecular Mechanism
The molecular mechanism of this compound is primarily understood in the context of its role as a solvent in NMR-based research and analyses
Dosage Effects in Animal Models
The non-deuterated ethylene glycol has a known minimum lethal dose in various animals
Metabolic Pathways
Ethylene glycol, its non-deuterated counterpart, is metabolized in the liver through successive oxidations to a variety of compounds including glycoaldehyde, glycolic acid, glyoxylic acid, and oxalic acid .
Preparation Methods
Synthetic Routes and Reaction Conditions
Ethylene-d4 glycol can be synthesized through the deuteration of ethylene glycol. This process involves the replacement of hydrogen atoms with deuterium atoms. One common method is the catalytic exchange of hydrogen with deuterium in the presence of a deuterium source such as deuterium oxide (D2O). The reaction is typically carried out under high temperature and pressure conditions to achieve a high degree of deuteration .
Industrial Production Methods
In an industrial setting, the production of this compound involves the use of deuterium gas (D2) and a suitable catalyst. The process is similar to the laboratory synthesis but is scaled up to produce larger quantities. The reaction conditions are optimized to ensure maximum yield and purity of the deuterated product .
Chemical Reactions Analysis
Types of Reactions
Ethylene-d4 glycol undergoes various chemical reactions similar to those of ethylene glycol. These reactions include:
Oxidation: this compound can be oxidized to form deuterated glycolic acid and oxalic acid.
Reduction: It can be reduced to form deuterated ethylene.
Substitution: The hydroxyl groups in this compound can be substituted with other functional groups such as halides or alkoxides.
Common Reagents and Conditions
Oxidation: Common oxidizing agents include potassium permanganate (KMnO4) and chromium trioxide (CrO3).
Reduction: Reducing agents such as lithium aluminum hydride (LiAlH4) are used.
Substitution: Reagents like thionyl chloride (SOCl2) or phosphorus tribromide (PBr3) are employed for substitution reactions.
Major Products Formed
Oxidation: Deuterated glycolic acid, deuterated oxalic acid.
Reduction: Deuterated ethylene.
Substitution: Deuterated alkyl halides or ethers.
Scientific Research Applications
Ethylene-d4 glycol is widely used in scientific research due to its deuterated nature. Some of its applications include:
NMR Spectroscopy: As a solvent in NMR spectroscopy, this compound provides a deuterium signal that does not interfere with the proton signals of the sample being analyzed.
Isotope Labeling: It is used in the synthesis of deuterated compounds for use in various spectroscopic and analytical techniques.
Biological Studies: Deuterated compounds like this compound are used in metabolic studies to trace the pathways and interactions of molecules within biological systems.
Industrial Applications: It is used in the production of deuterated materials for specialized industrial applications, such as in the development of advanced materials and pharmaceuticals.
Comparison with Similar Compounds
Ethylene-d4 glycol is similar to other deuterated glycols such as:
Ethylene glycol-d6: This compound has six deuterium atoms and is used in similar applications as this compound.
Propylene glycol-d8: Another deuterated glycol with eight deuterium atoms, used in NMR spectroscopy and other analytical techniques.
Uniqueness
The uniqueness of this compound lies in its specific deuteration pattern, which provides distinct advantages in NMR spectroscopy and other analytical methods. Its balanced deuteration allows for clear and precise analysis without significant interference from hydrogen signals .
Biological Activity
Ethylene-d4 glycol (C2H6O2D4), a deuterated form of ethylene glycol, is primarily utilized as a solvent in nuclear magnetic resonance (NMR) spectroscopy. This article delves into the biological activity of this compound, focusing on its pharmacokinetics, toxicity, and potential therapeutic applications based on diverse research findings.
This compound is a heavy water variant of ethylene glycol, distinguished by the presence of deuterium atoms. Its molecular structure allows for unique applications in NMR studies, providing insights into molecular dynamics and interactions. The compound is also used in various industrial applications due to its low freezing point and high boiling point.
Pharmacokinetics
Absorption and Distribution:
Ethylene glycol is absorbed rapidly through oral and dermal routes. Studies indicate that after ingestion, it distributes widely across body tissues, with significant concentrations found in the kidneys and liver . In humans, the biological half-life of ethylene glycol can vary significantly based on dose and individual metabolism.
Metabolism:
Ethylene glycol undergoes metabolic conversion primarily in the liver. It is oxidized to glyoxylic acid and subsequently to oxalic acid, which can lead to calcium oxalate crystallization in renal tissues, causing nephrotoxicity . The metabolic pathway can be influenced by factors such as dose and the presence of co-ingestants like ethanol, which competes for metabolic enzymes.
Toxicological Profile
Acute Toxicity:
Ethylene glycol is highly toxic, with lethal doses estimated between 30 to 100 mL for adults. Symptoms of toxicity include metabolic acidosis, renal failure, and central nervous system depression. A notable case study reported a patient who survived a massive ingestion (over 300 mL) with minimal sequelae after receiving prompt treatment .
Chronic Toxicity:
Long-term exposure to ethylene glycol has been associated with kidney damage and potential reproductive toxicity. Animal studies have indicated histopathological changes in renal tissues at high doses, suggesting a critical need for monitoring occupational exposure levels .
Case Studies
-
Case Report of High-Level Intoxication:
A documented case involved a patient who ingested a record-high level of ethylene glycol during a suicide attempt. Despite severe acidosis and renal impairment initially observed, the patient was treated successfully with ethanol infusion, highlighting the importance of timely intervention . -
Epidemiological Study:
An analysis of 81 cases of ethylene glycol poisoning revealed that most incidents were accidental or suicidal in nature. Concentrations of ethylene glycol in biological samples varied significantly, with blood levels ranging from 145 to 7060 μg/mL in non-fatal cases .
Research Findings
A recent study developed an analytical method for detecting ethylene glycol and its metabolites using gas chromatography coupled with mass spectrometry (GC-MS). This method enhances the ability to diagnose ethylene glycol poisoning effectively by quantifying its presence in postmortem biological materials .
Table 1: Summary of Toxicity Data
Parameter | Findings |
---|---|
Lethal Dose | 30-100 mL (adults) |
Common Symptoms | Metabolic acidosis, renal failure |
Metabolites Detected | Glyoxylic acid, oxalic acid |
Biological Half-Life | Variable; dependent on dose |
Treatment Options | Ethanol infusion; supportive care |
Properties
IUPAC Name |
1,1,2,2-tetradeuterioethane-1,2-diol | |
---|---|---|
Source | PubChem | |
URL | https://pubchem.ncbi.nlm.nih.gov | |
Description | Data deposited in or computed by PubChem | |
InChI |
InChI=1S/C2H6O2/c3-1-2-4/h3-4H,1-2H2/i1D2,2D2 | |
Source | PubChem | |
URL | https://pubchem.ncbi.nlm.nih.gov | |
Description | Data deposited in or computed by PubChem | |
InChI Key |
LYCAIKOWRPUZTN-LNLMKGTHSA-N | |
Source | PubChem | |
URL | https://pubchem.ncbi.nlm.nih.gov | |
Description | Data deposited in or computed by PubChem | |
Canonical SMILES |
C(CO)O | |
Source | PubChem | |
URL | https://pubchem.ncbi.nlm.nih.gov | |
Description | Data deposited in or computed by PubChem | |
Isomeric SMILES |
[2H]C([2H])(C([2H])([2H])O)O | |
Source | PubChem | |
URL | https://pubchem.ncbi.nlm.nih.gov | |
Description | Data deposited in or computed by PubChem | |
Molecular Formula |
C2H6O2 | |
Source | PubChem | |
URL | https://pubchem.ncbi.nlm.nih.gov | |
Description | Data deposited in or computed by PubChem | |
Molecular Weight |
66.09 g/mol | |
Source | PubChem | |
URL | https://pubchem.ncbi.nlm.nih.gov | |
Description | Data deposited in or computed by PubChem | |
CAS No. |
2219-51-4 | |
Record name | 1,2-Ethane-1,1,2,2-d4-diol | |
Source | CAS Common Chemistry | |
URL | https://commonchemistry.cas.org/detail?cas_rn=2219-51-4 | |
Description | CAS Common Chemistry is an open community resource for accessing chemical information. Nearly 500,000 chemical substances from CAS REGISTRY cover areas of community interest, including common and frequently regulated chemicals, and those relevant to high school and undergraduate chemistry classes. This chemical information, curated by our expert scientists, is provided in alignment with our mission as a division of the American Chemical Society. | |
Explanation | The data from CAS Common Chemistry is provided under a CC-BY-NC 4.0 license, unless otherwise stated. | |
Record name | 1,2-ethane-[2H4]diol | |
Source | European Chemicals Agency (ECHA) | |
URL | https://echa.europa.eu/substance-information/-/substanceinfo/100.017.028 | |
Description | The European Chemicals Agency (ECHA) is an agency of the European Union which is the driving force among regulatory authorities in implementing the EU's groundbreaking chemicals legislation for the benefit of human health and the environment as well as for innovation and competitiveness. | |
Explanation | Use of the information, documents and data from the ECHA website is subject to the terms and conditions of this Legal Notice, and subject to other binding limitations provided for under applicable law, the information, documents and data made available on the ECHA website may be reproduced, distributed and/or used, totally or in part, for non-commercial purposes provided that ECHA is acknowledged as the source: "Source: European Chemicals Agency, http://echa.europa.eu/". Such acknowledgement must be included in each copy of the material. ECHA permits and encourages organisations and individuals to create links to the ECHA website under the following cumulative conditions: Links can only be made to webpages that provide a link to the Legal Notice page. | |
Synthesis routes and methods I
Procedure details
Synthesis routes and methods II
Procedure details
Synthesis routes and methods III
Procedure details
Synthesis routes and methods IV
Procedure details
Synthesis routes and methods V
Procedure details
Retrosynthesis Analysis
AI-Powered Synthesis Planning: Our tool employs the Template_relevance Pistachio, Template_relevance Bkms_metabolic, Template_relevance Pistachio_ringbreaker, Template_relevance Reaxys, Template_relevance Reaxys_biocatalysis model, leveraging a vast database of chemical reactions to predict feasible synthetic routes.
One-Step Synthesis Focus: Specifically designed for one-step synthesis, it provides concise and direct routes for your target compounds, streamlining the synthesis process.
Accurate Predictions: Utilizing the extensive PISTACHIO, BKMS_METABOLIC, PISTACHIO_RINGBREAKER, REAXYS, REAXYS_BIOCATALYSIS database, our tool offers high-accuracy predictions, reflecting the latest in chemical research and data.
Strategy Settings
Precursor scoring | Relevance Heuristic |
---|---|
Min. plausibility | 0.01 |
Model | Template_relevance |
Template Set | Pistachio/Bkms_metabolic/Pistachio_ringbreaker/Reaxys/Reaxys_biocatalysis |
Top-N result to add to graph | 6 |
Feasible Synthetic Routes
Q1: What are the advantages of using a MnBDC-derived catalyst for the synthesis of ethylene-d4 glycol?
A1: The research article highlights several advantages of using a ruthenium catalyst supported on MnBDC, derived from Mn-MOF, for the synthesis of this compound:
- Dual Catalytic Activity: The catalyst enables both thermo- and electro-catalytic hydrogen isotope exchange (HIE) reactions. [] This allows for flexibility in reaction conditions and potential for energy efficiency.
- High Deuteration Rate: The catalyst exhibits a high deuterium incorporation rate of 97%, indicating its effectiveness in producing highly deuterated ethylene glycol. [] This is crucial for applications requiring high isotopic purity.
- Unique Structural Properties: The agglomerated sheet-type structure of the MnBDC-derived support and the specific electronic structure of the ruthenium nanoparticles contribute to the catalyst's activity. [] This highlights the importance of material design in catalyst development.
Disclaimer and Information on In-Vitro Research Products
Please be aware that all articles and product information presented on BenchChem are intended solely for informational purposes. The products available for purchase on BenchChem are specifically designed for in-vitro studies, which are conducted outside of living organisms. In-vitro studies, derived from the Latin term "in glass," involve experiments performed in controlled laboratory settings using cells or tissues. It is important to note that these products are not categorized as medicines or drugs, and they have not received approval from the FDA for the prevention, treatment, or cure of any medical condition, ailment, or disease. We must emphasize that any form of bodily introduction of these products into humans or animals is strictly prohibited by law. It is essential to adhere to these guidelines to ensure compliance with legal and ethical standards in research and experimentation.