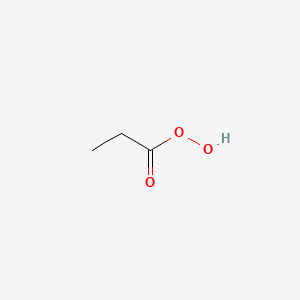
Peroxypropionic acid
Overview
Description
Peroxypropionic acid (PPA, C₂H₅COOOH) is a peroxycarboxylic acid (PCA) characterized by its strong oxidizing properties. It is synthesized via the acid-catalyzed perhydrolysis of propionic acid (PA) with hydrogen peroxide (H₂O₂), typically using homogeneous catalysts like sulfuric acid or heterogeneous catalysts such as cation-exchange resins (e.g., Dowex 50Wx2, Amberlite IR-120) . PPA is widely utilized in industrial applications, including chemical synthesis, pulp delignification, and heavy oil oxidation, due to its ability to generate hydroxyl radicals (•OH) under specific conditions . Its decomposition in the liquid phase produces carbon dioxide and oxygen, with kinetics influenced by temperature, catalyst type, and mass transfer effects .
Q & A
Basic Research Questions
Q. What are the validated laboratory protocols for synthesizing high-purity Peroxypropionic acid, and how can contamination risks be minimized?
- Methodological Answer : Synthesis typically involves controlled oxidation of propionic acid using hydrogen peroxide under acidic catalysis. Key steps include:
- Temperature regulation (5–10°C) to prevent runaway reactions .
- Purification via vacuum distillation or recrystallization, with purity verified by HPLC (>98%) .
- Contamination mitigation: Use stabilizers (e.g., chelating agents) to inhibit peroxide decomposition and store in amber glassware under inert gas .
Q. What analytical techniques are most reliable for quantifying this compound in complex matrices?
- Methodological Answer :
- Chromatography : Reverse-phase HPLC with UV detection (λ = 210 nm) offers sensitivity for trace analysis .
- Spectroscopy : FT-IR (C-O-O stretching at 880 cm⁻¹) confirms functional group integrity .
- Titration : Iodometric titration quantifies active oxygen content but requires calibration against standardized solutions .
Q. How can researchers assess the thermal stability of this compound under varying experimental conditions?
- Methodological Answer :
- Use differential scanning calorimetry (DSC) to measure decomposition onset temperatures.
- Variables to control: concentration (neat vs. diluted), solvent polarity, and presence of metal contaminants .
- Safety note: Conduct tests in small batches with blast shields due to explosive risks .
Advanced Research Questions
Q. What computational models are validated for predicting the reaction kinetics of this compound in oxidative environments?
- Methodological Answer :
- Density Functional Theory (DFT) : Models electron transfer mechanisms during oxidation, validated against experimental kinetic data (e.g., Arrhenius parameters) .
- Molecular Dynamics (MD) : Simulates solvent effects on degradation pathways; cross-validate with NMR or mass spectrometry data .
- Limitations: Computational models may underestimate steric effects in concentrated solutions, necessitating experimental corroboration .
Q. How should researchers resolve contradictions in literature regarding catalytic decomposition mechanisms of this compound?
- Methodological Answer :
- Systematic Review : Apply PICOT framework to compare studies by population (e.g., catalyst type), intervention (pH, temperature), and outcomes (decomposition rate) .
- Experimental Replication : Standardize conditions (e.g., 25°C, 0.1M substrate) to isolate variables causing discrepancies .
- Meta-Analysis : Use statistical tools (e.g., random-effects models) to aggregate data and identify outlier studies .
Q. What experimental designs are optimal for studying the environmental degradation pathways of this compound?
- Methodological Answer :
- Field Studies : Spike soil/water samples with isotopically labeled compound (¹³C-Peroxypropionic acid) to track degradation via LC-MS .
- Lab Simulations : Use photoreactors with UV-C light to mimic sunlight-driven decomposition; monitor intermediates via GC-MS .
- Controls : Include abiotic (e.g., sterile samples) and biotic (microbe-inoculated) conditions to distinguish pathways .
Q. Data Contradiction and Reproducibility
Q. How can researchers address variability in reported half-lives of this compound across studies?
- Methodological Answer :
- Sensitivity Analysis : Identify critical parameters (e.g., pH, ionic strength) using Plackett-Burman experimental design .
- Interlaboratory Trials : Collaborate to standardize protocols (e.g., OECD guidelines) and validate reproducibility .
- Transparency : Publish raw datasets and instrument calibration logs to enable cross-checking .
Q. Ethical and Safety Considerations
Q. What safety protocols are critical when handling this compound in high-throughput screening?
- Methodological Answer :
- Engineering Controls : Use fume hoods with blast-resistant glass and automated dispensing systems to minimize exposure .
- Personal Protective Equipment (PPE) : Acid-resistant gloves, face shields, and flame-retardant lab coats are mandatory .
- Waste Management : Neutralize waste with sodium bicarbonate before disposal; avoid mixing with organic solvents .
Comparison with Similar Compounds
Peroxypropionic acid belongs to the broader class of peroxycarboxylic acids, which share the functional group -C(=O)-OOH. Below is a detailed comparison with structurally and functionally related compounds:
Peroxyacetic Acid (PAA, CH₃COOOH)
- Synthesis : Similar to PPA, PAA is synthesized from acetic acid and H₂O₂, often using sulfuric acid. However, PAA formation is faster due to the lower molecular weight of acetic acid .
- Stability : PAA is less thermally stable than PPA, decomposing exothermically at lower temperatures (starting at ~25°C). In contrast, PPA’s decomposition initiates at higher temperatures (~40–60°C) .
- Reactivity : Both acids are effective in pulp bleaching, but PAA exhibits higher delignification efficiency at neutral pH, whereas PPA requires acidic conditions (pH ~3–4.5) for optimal performance .
- Applications : PAA is predominantly used in disinfection and wastewater treatment, while PPA is favored in organic synthesis and heavy oil oxidation .
Peroxyformic Acid (PFA, HCOOOH)
- Synthesis : PFA forms spontaneously from formic acid and H₂O₂ without requiring strong acid catalysts, but its synthesis is highly exothermic (ΔH = −116 kJ/mol for epoxidation), posing greater safety risks .
- Decomposition : PFA decomposes more rapidly than PPA, with a higher propensity for autocatalytic runaway reactions. Its decomposition kinetics are influenced by iron ions, which accelerate H₂O₂ breakdown .
- Industrial Use : PFA is employed in epoxidation reactions but is less stable in storage compared to PPA .
Methyl Ethyl Ketone Peroxide (MEKPO)
- Structure and Stability : Unlike PPA, MEKPO is a cyclic peroxide with lower thermal stability, decomposing at 30–32°C in multiple exothermic steps (total heat: 1.26 kJ/g). This makes MEKPO significantly more hazardous .
- Applications : MEKPO is used as a polymerization initiator, whereas PPA is avoided in such contexts due to its carboxylic acid functionality .
Peroxynitrous Acid (HOONO)
- Reactivity: HOONO decomposes to produce nitroxyl (HNO) and singlet oxygen (¹O₂), whereas PPA generates •OH and CO₂. HOONO’s isomerization to nitric acid (HNO₃) is a key distinction in decomposition pathways .
- Environmental Role: HOONO is a transient atmospheric species, while PPA is primarily an industrial oxidizer .
Comparative Data Tables
Key Research Findings
Catalyst Efficiency : Heterogeneous catalysts like Dowex 50Wx2 enhance PPA synthesis safety by reducing H₂SO₄ usage, whereas PAA production relies more on homogeneous catalysts .
Microreactor Advantages : Continuous-flow microreactors reduce PPA synthesis time from hours to 10 minutes, improving yield (72.36% at 50°C) and minimizing decomposition risks .
pH Sensitivity : PPA’s delignification efficiency drops above pH 4.5, unlike PAA, which remains effective up to pH 7 .
Preparation Methods
Continuous Reactive Distillation with Catalyst Recycling
Reactor Configuration and Process Flow
The method disclosed in CN108863883B employs a series of 4–5 reaction rectification towers connected to a distillation rectification tower . Propionic acid and hydrogen peroxide are premixed with a catalyst (e.g., boric acid) and phosphate ester (e.g., tributyl phosphate) before entering the first tower. Reactive distillation occurs under vacuum (7–15 kPa absolute pressure), with the following critical parameters:
Parameter | Range | Optimal Value |
---|---|---|
Molar ratio (H₂O₂:PA) | 0.1–1 | 0.2–0.6 |
Mass ratio (light component:PA) | 0.1–10 | 0.25–4 |
Catalyst:Phosphate ester | 1:0.1–100 | 1:2–4 |
Operating pressure | 1–101.3 kPa | 7–15 kPa |
The light component (e.g., ethyl propionate) forms an azeotrope with water, enabling continuous removal of reaction water while recycling unreacted reagents .
Catalyst Separation and Recycling
Phosphate esters act as phase-separation agents, reducing catalyst content in the final product to <100 ppm. In Example 5, using 1-hydroxyethylidene-1,1-diphosphonic acid (di-2-ethylhexyl ester) lowered residual catalyst to 30 ppm while maintaining 96.4% selectivity . The system achieves 94–98% yield in subsequent caprolactone synthesis, with byproducts reduced from 20% to 2–7% compared to conventional methods .
Batch Synthesis with Homogeneous Acid Catalysts
Kinetic Profile and Reaction Optimization
A kinetic study using sulfuric acid catalyst determined rate constants () and activation energy () for PPA formation :
Optimal conditions were identified through parametric analysis:
Condition | Effect on PPA Yield |
---|---|
Molar ratio (PA:H₂O₂) = 2.05 | Maximizes H₂O₂ conversion (98%) |
Temperature = 30°C | Balances reaction rate and decomposition |
Catalyst concentration = 0.5 M | Prevents excessive side reactions |
The study revealed first-order dependence on hydrogen peroxide concentration and zero-order dependence on propionic acid at excess ratios .
Limitations of Batch Methods
While achieving 85–90% selectivity, batch processes face challenges in catalyst recovery and scale-up. Sulfuric acid residues necessitate neutralization steps, increasing production costs and waste generation .
Comparative Analysis of Preparation Methods
Energy Efficiency and Scalability
Reactive distillation reduces energy consumption by 30–40% compared to batch reactors, utilizing reaction heat for simultaneous separation . The continuous system’s modular design allows throughput scaling to 10,000 tonnes/year with consistent product quality .
Product Purity and Applications
Continuous methods produce PPA solutions containing 26–28.5% active oxygen, <50 ppm water, and <100 ppm catalyst residuals, meeting pharmaceutical-grade specifications . Batch-derived PPA typically contains 200–500 ppm sulfate impurities, limiting use to industrial oxidations .
Properties
CAS No. |
4212-43-5 |
---|---|
Molecular Formula |
C3H6O3 |
Molecular Weight |
90.08 g/mol |
IUPAC Name |
propaneperoxoic acid |
InChI |
InChI=1S/C3H6O3/c1-2-3(4)6-5/h5H,2H2,1H3 |
InChI Key |
CZPZWMPYEINMCF-UHFFFAOYSA-N |
SMILES |
CCC(=O)OO |
Canonical SMILES |
CCC(=O)OO |
Key on ui other cas no. |
4212-43-5 |
Synonyms |
perpropionic acid propaneperoxoic acid |
Origin of Product |
United States |
Synthesis routes and methods
Procedure details
Disclaimer and Information on In-Vitro Research Products
Please be aware that all articles and product information presented on BenchChem are intended solely for informational purposes. The products available for purchase on BenchChem are specifically designed for in-vitro studies, which are conducted outside of living organisms. In-vitro studies, derived from the Latin term "in glass," involve experiments performed in controlled laboratory settings using cells or tissues. It is important to note that these products are not categorized as medicines or drugs, and they have not received approval from the FDA for the prevention, treatment, or cure of any medical condition, ailment, or disease. We must emphasize that any form of bodily introduction of these products into humans or animals is strictly prohibited by law. It is essential to adhere to these guidelines to ensure compliance with legal and ethical standards in research and experimentation.