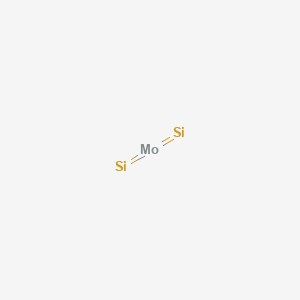
Molybdenum silicide
Overview
Description
Molybdenum silicide is an intermetallic compound composed of molybdenum and silicon, with the chemical formula MoSi₂. It is a refractory ceramic material primarily used in heating elements due to its high melting point of 2030°C and excellent electrical conductivity . This compound forms a protective silicon dioxide layer at high temperatures, which provides oxidation resistance, making it suitable for high-temperature applications .
Mechanism of Action
Target of Action
Molybdenum silicide, also known as molybdenum disilicide, is an intermetallic compound primarily used in heating elements due to its high melting point and excellent oxidation resistance . Its primary targets are high-temperature structural applications, particularly in aircraft gas turbine engines .
Mode of Action
This compound operates by providing a high melting point (2030 °C) material with excellent oxidation resistance . At high temperatures, it forms a passivation layer of silicon dioxide, protecting it from further oxidation . Its low electrical resistance, high thermal stability, electron-migration resistance, and excellent diffusion-barrier characteristics make it important for microelectronic applications .
Biochemical Pathways
Its excellent oxidation resistance and thermal stability make it an ideal material for use in high-temperature furnaces .
Pharmacokinetics
Its physical properties, such as high melting point, excellent oxidation resistance, and moderate density, impact its bioavailability in its primary applications .
Result of Action
The primary result of this compound’s action is its ability to withstand high temperatures and resist oxidation. This makes it an ideal material for use in heating elements in electric furnaces used in laboratory and production environments in the production of glass, steel, electronics, ceramics, and in the heat treatment of materials .
Action Environment
The action of this compound is heavily influenced by environmental factors. Its effectiveness and stability are maximized in high-temperature, oxidizing environments. Its maximum operating temperature must be lowered in atmospheres with low oxygen content due to the breakdown of the passivation layer .
Preparation Methods
Molybdenum silicide can be synthesized through various methods, including:
Sintering: This involves compacting and heating molybdenum and silicon powders to form a dense material.
Plasma Spraying: This technique uses a plasma jet to melt and deposit molybdenum disilicide powder onto a substrate, forming a coating.
Chemical Vapor Deposition (CVD): In this method, gaseous precursors react on a substrate to form a thin film of molybdenum disilicide.
Pack Cementation: This involves embedding the substrate in a powder mixture and heating it to allow the diffusion of silicon into the molybdenum.
Industrial production often employs plasma spraying and CVD due to their ability to produce high-purity and uniform coatings .
Chemical Reactions Analysis
Molybdenum silicide undergoes several types of chemical reactions:
Reduction: This compound can be reduced by hydrogen gas at elevated temperatures to produce molybdenum and silicon.
Substitution: It can react with halogens to form molybdenum halides and silicon halides.
Common reagents used in these reactions include oxygen, hydrogen, and halogens. The major products formed are silicon dioxide, molybdenum, and various molybdenum and silicon halides .
Scientific Research Applications
Molybdenum silicide has a wide range of scientific research applications:
Comparison with Similar Compounds
Molybdenum silicide is often compared with other high-temperature materials such as:
Tungsten disilicide (WSi₂): Similar to molybdenum disilicide, tungsten disilicide has a high melting point and excellent oxidation resistance.
Chromium disilicide (CrSi₂): This compound has lower oxidation resistance and melting point compared to molybdenum disilicide.
Nickel aluminide (Ni₃Al): While nickel aluminide has good oxidation resistance, its melting point is lower than that of molybdenum disilicide.
This compound’s unique combination of high melting point, oxidation resistance, and electrical conductivity makes it particularly suitable for high-temperature applications .
Properties
InChI |
InChI=1S/Mo.2Si | |
---|---|---|
Source | PubChem | |
URL | https://pubchem.ncbi.nlm.nih.gov | |
Description | Data deposited in or computed by PubChem | |
InChI Key |
YXTPWUNVHCYOSP-UHFFFAOYSA-N | |
Source | PubChem | |
URL | https://pubchem.ncbi.nlm.nih.gov | |
Description | Data deposited in or computed by PubChem | |
Canonical SMILES |
[Si]=[Mo]=[Si] | |
Source | PubChem | |
URL | https://pubchem.ncbi.nlm.nih.gov | |
Description | Data deposited in or computed by PubChem | |
Molecular Formula |
MoSi2 | |
Source | PubChem | |
URL | https://pubchem.ncbi.nlm.nih.gov | |
Description | Data deposited in or computed by PubChem | |
Molecular Weight |
152.12 g/mol | |
Source | PubChem | |
URL | https://pubchem.ncbi.nlm.nih.gov | |
Description | Data deposited in or computed by PubChem | |
Physical Description |
Dark gray crystalline powder; Available as cylinders, lumps, granules, powder, or whiskers; [Hawley] Dark grey odorless powder; Insoluble in water; [MSDSonline] | |
Record name | Molybdenum disilicide | |
Source | Haz-Map, Information on Hazardous Chemicals and Occupational Diseases | |
URL | https://haz-map.com/Agents/8283 | |
Description | Haz-Map® is an occupational health database designed for health and safety professionals and for consumers seeking information about the adverse effects of workplace exposures to chemical and biological agents. | |
Explanation | Copyright (c) 2022 Haz-Map(R). All rights reserved. Unless otherwise indicated, all materials from Haz-Map are copyrighted by Haz-Map(R). No part of these materials, either text or image may be used for any purpose other than for personal use. Therefore, reproduction, modification, storage in a retrieval system or retransmission, in any form or by any means, electronic, mechanical or otherwise, for reasons other than personal use, is strictly prohibited without prior written permission. | |
CAS No. |
12136-78-6 | |
Record name | Molybdenum silicide (MoSi2) | |
Source | CAS Common Chemistry | |
URL | https://commonchemistry.cas.org/detail?cas_rn=12136-78-6 | |
Description | CAS Common Chemistry is an open community resource for accessing chemical information. Nearly 500,000 chemical substances from CAS REGISTRY cover areas of community interest, including common and frequently regulated chemicals, and those relevant to high school and undergraduate chemistry classes. This chemical information, curated by our expert scientists, is provided in alignment with our mission as a division of the American Chemical Society. | |
Explanation | The data from CAS Common Chemistry is provided under a CC-BY-NC 4.0 license, unless otherwise stated. | |
Record name | Molybdenum silicide (MoSi2) | |
Source | ChemIDplus | |
URL | https://pubchem.ncbi.nlm.nih.gov/substance/?source=chemidplus&sourceid=0012136786 | |
Description | ChemIDplus is a free, web search system that provides access to the structure and nomenclature authority files used for the identification of chemical substances cited in National Library of Medicine (NLM) databases, including the TOXNET system. | |
Record name | Molybdenum silicide (MoSi2) | |
Source | EPA Chemicals under the TSCA | |
URL | https://www.epa.gov/chemicals-under-tsca | |
Description | EPA Chemicals under the Toxic Substances Control Act (TSCA) collection contains information on chemicals and their regulations under TSCA, including non-confidential content from the TSCA Chemical Substance Inventory and Chemical Data Reporting. | |
Record name | Molybdenum disilicide | |
Source | European Chemicals Agency (ECHA) | |
URL | https://echa.europa.eu/substance-information/-/substanceinfo/100.032.016 | |
Description | The European Chemicals Agency (ECHA) is an agency of the European Union which is the driving force among regulatory authorities in implementing the EU's groundbreaking chemicals legislation for the benefit of human health and the environment as well as for innovation and competitiveness. | |
Explanation | Use of the information, documents and data from the ECHA website is subject to the terms and conditions of this Legal Notice, and subject to other binding limitations provided for under applicable law, the information, documents and data made available on the ECHA website may be reproduced, distributed and/or used, totally or in part, for non-commercial purposes provided that ECHA is acknowledged as the source: "Source: European Chemicals Agency, http://echa.europa.eu/". Such acknowledgement must be included in each copy of the material. ECHA permits and encourages organisations and individuals to create links to the ECHA website under the following cumulative conditions: Links can only be made to webpages that provide a link to the Legal Notice page. | |
Q1: What is the molecular formula and weight of Molybdenum disilicide?
A1: Molybdenum disilicide has the molecular formula MoSi2 and a molecular weight of 152.11 g/mol.
Q2: What is the crystal structure of MoSi2?
A2: MoSi2 primarily exists in two crystal structures: a tetragonal α-MoSi2 phase and a hexagonal β-MoSi2 phase. The α-MoSi2 phase is more thermodynamically stable at lower temperatures. []
Q3: What spectroscopic techniques are used to characterize MoSi2?
A3: Electron energy-loss spectroscopy (EELS) is a valuable tool to analyze the electronic structure of MoSi2 thin films. EELS studies have revealed interband transitions related to metal d bands and Mo(4d)-Si(3p) levels, providing insights into the bonding nature during silicidation. [] X-ray diffraction (XRD) is also commonly employed for phase identification and analysis of MoSi2. [][33]
Q4: What is the significance of the brittle-to-ductile transition temperature in MoSi2?
A4: MoSi2 exhibits a brittle-to-ductile transition around 1000°C. Above this temperature, it demonstrates increased ductility, making it suitable for high-temperature structural applications. []
Q5: How does the addition of aluminum oxide affect the properties of MoSi2?
A5: Combining MoSi2 with aluminum oxide (Al2O3) yields a ceramic composite with enhanced thermal shock resistance and high-temperature strength compared to pure MoSi2. This improvement arises from the synergistic effects of both materials. []
Q6: What is the role of a protective silica layer in the oxidation resistance of MoSi2?
A6: At high temperatures, MoSi2 forms a protective silica (SiO2) layer on its surface upon exposure to oxygen. This layer acts as a barrier, effectively hindering further oxidation and contributing to its remarkable oxidation resistance. [][30][41]
Q7: What are the limitations of using MoSi2 in high-temperature applications?
A7: Despite its high melting point and oxidation resistance, MoSi2 suffers from limitations such as low-temperature brittleness, creep at high temperatures, and susceptibility to "pest" degradation in certain environments. [][36][43]
Q8: How does the addition of tantalum affect the fracture toughness of MoSi2?
A8: Incorporating ductile tantalum (Ta) reinforcements into a MoSi2 matrix via plasma spraying significantly improves its room-temperature fracture toughness. Studies show a 50% increase for unreinforced plasma-sprayed MoSi2 and even greater improvements with Ta additions. The mechanisms behind this enhancement include crack bridging, crack deflection, and crack blunting, leading to R-curve behavior. []
Q9: What are some common methods for producing MoSi2?
A9: MoSi2 can be produced through various techniques, including:
- Direct reaction of molybdenum and silicon: This method involves heating a mixture of molybdenum and silicon powders to high temperatures. []
- Mechanical alloying: This process utilizes high-energy ball milling to synthesize MoSi2 powder from elemental powders. []
- Plasma spraying: This versatile technique deposits MoSi2 coatings or builds near-net-shaped components by feeding MoSi2 powder into a plasma jet. [][10][36][37]
- Reactive vapor infiltration: This method involves diffusing silicon vapor into a porous molybdenum preform at high temperatures, leading to the in-situ formation of MoSi2. [][34]
Q10: How does the particle size of MoSi2 powder affect its properties and applications?
A10: The particle size of MoSi2 powder significantly impacts its sintering behavior, affecting the final density and microstructure of sintered parts. Fine MoSi2 powders are desirable for applications requiring high density and fine-grained microstructures, such as heating elements. []
Q11: What are the applications of MoSi2 as a coating material?
A11: MoSi2 coatings offer exceptional oxidation and wear resistance at high temperatures, making them suitable for protecting various substrates, such as:
- High-temperature furnace components: MoSi2 coatings safeguard heating elements, furnace linings, and other components from oxidation and corrosion. []
- Turbine blades: MoSi2 coatings shield turbine blades from extreme temperatures and oxidative environments encountered in gas turbines and aerospace applications. [][36]
- Metal cutting tools: MoSi2 coatings enhance the wear resistance and lifespan of cutting tools used in machining operations involving high temperatures and abrasive materials. []
Q12: How does the presence of silicon nitride impact the pest resistance of MoSi2 materials?
A12: Incorporating silicon nitride (Si3N4) into MoSi2 compositions enhances their resistance to "pest" degradation, a phenomenon causing catastrophic disintegration at intermediate temperatures (400-800 °C) in specific environments. This improvement allows MoSi2 to be used in a wider range of high-temperature structural applications. []
Q13: How does the addition of reinforcements like SiC and ZrO2 affect the mechanical properties of MoSi2?
A13: Reinforcing MoSi2 with ceramic particles such as silicon carbide (SiC) and zirconia (ZrO2) improves its high-temperature strength, creep resistance, and fracture toughness. These reinforcements hinder crack propagation and enhance load transfer capabilities. [][8][23][28][33]
Q14: What are the benefits of using plasma spraying to produce MoSi2 composites?
A14: Plasma spraying offers several advantages for manufacturing MoSi2 composites, including:
- Flexibility in composition and microstructure: Plasma spraying allows for tailoring the composite's properties by controlling the type, size, and distribution of reinforcement phases. []
- Near-net-shape fabrication: This technique enables the production of complex-shaped components with minimal post-processing requirements. []
- Improved bonding: The high-energy plasma jet promotes strong interfacial bonding between the MoSi2 matrix and reinforcement phases. []
Q15: Can MoSi2 be used to reinforce other ceramic matrices?
A15: Yes, MoSi2 can act as a reinforcement phase in other ceramic matrices, such as mullite. Studies on mullite-matrix composites reinforced with MoSi2 particles show promising results, including improved strength and toughness compared to monolithic mullite. This enhancement is attributed to the reinforcing effect of MoSi2 and its ability to promote self-healing during oxidation. []
Q16: What are the challenges in processing MoSi2 composites?
A16: Processing MoSi2 composites presents challenges, including:
- Controlling interfacial reactions: At high processing temperatures, unwanted reactions can occur between the MoSi2 matrix and reinforcement phases, degrading the composite's properties. []
- Achieving uniform reinforcement distribution: Ensuring a homogeneous distribution of reinforcement phases throughout the MoSi2 matrix is crucial for optimizing mechanical properties. []
- Mitigating residual stresses: Processing-induced residual stresses can negatively impact the composite's performance and need careful management. []
Disclaimer and Information on In-Vitro Research Products
Please be aware that all articles and product information presented on BenchChem are intended solely for informational purposes. The products available for purchase on BenchChem are specifically designed for in-vitro studies, which are conducted outside of living organisms. In-vitro studies, derived from the Latin term "in glass," involve experiments performed in controlled laboratory settings using cells or tissues. It is important to note that these products are not categorized as medicines or drugs, and they have not received approval from the FDA for the prevention, treatment, or cure of any medical condition, ailment, or disease. We must emphasize that any form of bodily introduction of these products into humans or animals is strictly prohibited by law. It is essential to adhere to these guidelines to ensure compliance with legal and ethical standards in research and experimentation.