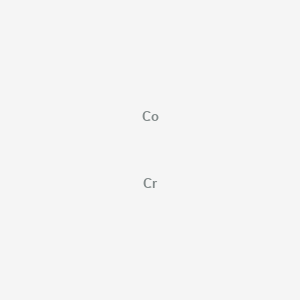
Hastelloy C
- Click on QUICK INQUIRY to receive a quote from our team of experts.
- With the quality product at a COMPETITIVE price, you can focus more on your research.
Overview
Description
Hastelloy C (UNS N10002 / W.Nr . 2.4819) is a nickel-based superalloy renowned for its exceptional resistance to corrosion in oxidizing and moderately reducing environments. Its chemical composition includes 15.0–17.0% chromium, 3.0–4.5% molybdenum, and 4.0–7.0% tungsten, with nickel as the base element . The alloy also contains controlled amounts of iron, carbon, and silicon to minimize the formation of detrimental intermetallic phases (e.g., β-Ni₄Mo) .
This compound exhibits outstanding performance in aggressive media such as hot contaminated mineral acids, chlorine, acetic acid, and seawater . Its yield strength at room temperature is approximately 365 MPa, with a tensile strength of 760 MPa and an elongation of 62% . Applications span chemical processing, pharmaceuticals, pollution control, and energy industries, particularly in equipment exposed to sulfuric, hydrochloric, and phosphoric acids .
Scientific Research Applications
Properties of Hastelloy C
This compound alloys exhibit several key properties that contribute to their widespread use:
- Corrosion Resistance : Excellent resistance to pitting, crevice corrosion, and stress corrosion cracking.
- High-Temperature Stability : Maintains mechanical integrity at elevated temperatures.
- Fabricability : Easily welded and fabricated into complex shapes.
Chemical Processing
This compound is extensively used in the chemical processing industry due to its superior corrosion resistance. It is commonly found in:
- Pressure Vessels : Used for storing corrosive chemicals.
- Heat Exchangers : Effective in transferring heat without degrading.
- Piping Systems : Ensures safe transport of aggressive chemicals.
Application | Description |
---|---|
Pressure Vessels | Designed to withstand high pressure and corrosive environments. |
Heat Exchangers | Facilitates efficient heat transfer while resisting corrosion. |
Piping Systems | Provides safe transport for corrosive substances. |
Aerospace Industry
In aerospace applications, this compound is favored for its lightweight and high-strength characteristics. Common uses include:
- Engine Components : Parts that require high-temperature stability.
- Fasteners and Connectors : Essential for structural integrity under extreme conditions.
Application | Description |
---|---|
Engine Components | Resists oxidation and maintains performance at high temperatures. |
Fasteners | Ensures reliability in critical aerospace structures. |
Nuclear Applications
This compound is also utilized in nuclear facilities due to its ability to resist radiation-induced degradation and corrosion from nuclear fuels.
- Reactor Components : Used in areas exposed to high radiation and corrosive environments.
- Storage Tanks : Safely contains radioactive materials.
Application | Description |
---|---|
Reactor Components | Withstands harsh conditions while ensuring safety. |
Storage Tanks | Provides secure containment for radioactive substances. |
Case Study 1: Chemical Processing Plant
A chemical processing plant utilized this compound for constructing reactors that handle hydrochloric acid. The alloy's resistance to localized corrosion significantly reduced maintenance costs and downtime, leading to increased operational efficiency.
Case Study 2: Aerospace Engine Component
An aerospace manufacturer employed this compound for turbine blades in jet engines. The alloy's ability to withstand high temperatures allowed for improved engine performance and fuel efficiency, demonstrating its critical role in advancing aerospace technology.
Q & A
Basic Research Questions
Q. What are the standard experimental methods for evaluating the corrosion resistance of Hastelloy C in extreme environments?
Methodological Answer:
- Use electrochemical testing (e.g., potentiodynamic polarization, electrochemical impedance spectroscopy) to quantify corrosion rates in simulated environments (e.g., acidic, high-temperature) .
- Pair with metallographic analysis (SEM/EDS) to examine surface degradation mechanisms .
- Key Consideration: Ensure environmental parameters (pH, temperature, pressure) are rigorously controlled to replicate operational conditions .
Q. How does the microstructure of this compound influence its mechanical properties under thermal stress?
Methodological Answer:
- Conduct thermomechanical testing (e.g., creep resistance, tensile strength at elevated temperatures) with controlled heating/cooling rates .
- Combine with microstructural characterization (TEM, XRD) to correlate grain boundary stability and phase transformations with mechanical performance .
- Framework: Apply P-E/I-C-O (Population: this compound; Exposure: Thermal cycling; Outcome: Mechanical degradation) to structure experiments .
Q. What are the validated protocols for synthesizing this compound with controlled alloying element ratios?
Methodological Answer:
- Use vacuum arc remelting (VAR) or powder metallurgy to ensure homogeneity .
- Validate compositions via ICP-OES or XRF and cross-reference with ASTM/ISO standards .
- Data Management: Document batch-specific variations in a structured table (e.g., alloy composition vs. hardness/ductility) .
Advanced Research Questions
Q. How can contradictory data on this compound’s corrosion resistance in mixed-acid environments be resolved?
Methodological Answer:
- Perform multivariate regression analysis to identify confounding variables (e.g., trace impurities, surface finish) across studies .
- Design controlled comparative experiments using standardized test protocols (e.g., ASTM G48 for pitting corrosion) .
- Critical Step: Publish raw datasets with metadata (e.g., environmental controls, instrumentation calibration) to enable replication .
Q. What advanced computational models predict this compound’s fatigue life in cyclic oxidation environments?
Methodological Answer:
- Apply finite element analysis (FEA) coupled with thermodynamic databases (e.g., CALPHAD) to simulate stress-oxidation interactions .
- Validate models against in-situ synchrotron XRD data capturing real-time crack propagation .
- Pitfall Avoidance: Address overfitting by testing models across multiple temperature and stress regimes .
Q. How can additive manufacturing parameters be optimized to minimize defect formation in this compound components?
Methodological Answer:
- Use design of experiments (DoE) to systematically vary parameters (e.g., laser power, scan speed) and assess outcomes (porosity, residual stress) .
- Characterize defects via non-destructive testing (CT scanning, ultrasonic testing) .
- Ethical Consideration: Disclose limitations in reproducibility due to machine-specific variability .
Q. Methodological Frameworks for this compound Research
Q. How to formulate a FINER (Feasible, Interesting, Novel, Ethical, Relevant) research question for this compound?
Guidelines:
- Feasible : Ensure access to specialized equipment (e.g., high-temperature autoclaves) and alloy samples .
- Novel : Investigate understudied areas (e.g., hydrogen embrittlement in subsea applications) .
- Ethical : Adhere to material safety protocols for handling hazardous byproducts (e.g., hexavalent chromium) .
Q. What statistical approaches are suitable for analyzing heterogeneous datasets in this compound studies?
Recommendations:
- Use multivariate ANOVA to account for interactions between variables (e.g., temperature, alloy composition) .
- Apply Bayesian inference for probabilistic modeling of corrosion rate uncertainties .
Q. Data Management and Reproducibility
Q. How to ensure reproducibility of this compound experiments across laboratories?
Best Practices:
- Publish detailed supplementary materials with step-by-step protocols (e.g., heat treatment cycles, surface preparation) .
- Use FAIR data principles (Findable, Accessible, Interoperable, Reusable) for sharing datasets .
Q. What metadata standards are critical for this compound research databases?
Requirements:
Comparison with Similar Compounds
Chemical Composition
The following table compares Hastelloy C with its closest analogues: This compound-276 , C-22 , and C-4 .
Key Observations :
- C-276 and C-22 have higher molybdenum content, enhancing resistance to reducing acids like hydrochloric acid .
- C-22 contains significantly more chromium (20–22.5%) for improved performance in oxidizing conditions, such as wet chlorine .
- C-4 reduces tungsten content compared to this compound, optimizing thermal stability for high-temperature applications .
Mechanical Properties
Property | This compound | C-276 | C-22 | C-4 |
---|---|---|---|---|
Yield Strength (MPa) | 365 | 510* | 415 | 380 |
Tensile Strength (MPa) | 760 | 790 | 800 | 750 |
Elongation (%) | 62 | 50 | 45 | 55 |
*C-276’s yield strength decreases to ~510 MPa after 800°C heat treatment due to microstructural changes .
Key Observations :
- C-276 offers superior as-fabricated strength but is sensitive to thermal processing .
- C-22 balances strength and ductility, making it suitable for welded structures .
- C-4 prioritizes thermal stability over room-temperature strength .
Corrosion Resistance
Acid Environments
- Phosphoric Acid : this compound resists boiling 40% H₃PO₄ at 2 mils/year, outperforming most stainless steels but less stable than C-276 in contaminated acids .
- Sulfuric Acid : C-22’s high Cr content (20–22.5%) provides superior resistance to oxidizing 10% H₂SO₄ at 90°C .
Chloride Environments
Preparation Methods
Alloy Composition and Raw Material Selection
The foundation of Hastelloy C-276’s performance lies in its precise chemical composition, which balances nickel, chromium, molybdenum, and tungsten to achieve resistance to both oxidizing and reducing media. The nominal composition, as specified by industry standards, is detailed in Table 1 .
Table 1: Nominal Composition of this compound-276 (Weight %)
Element | Minimum | Maximum |
---|---|---|
Nickel | 57 | Balance |
Chromium | 14.5 | 16.5 |
Molybdenum | 15.0 | 17.0 |
Tungsten | 3.0 | 4.5 |
Iron | 4.0 | 7.0 |
Cobalt | - | 2.5 |
Carbon | - | 0.02 |
Raw materials must adhere to stringent purity standards to minimize impurities like sulfur and phosphorus, which can degrade corrosion resistance. Vacuum induction melting (VIM) is the primary method for initial alloy synthesis, ensuring precise control over composition and gas content .
Melting and Casting Processes
The melting phase is critical for homogenizing the alloy and eliminating detrimental inclusions. Industrial practices typically employ a two-step process:
-
Vacuum Induction Melting (VIM):
-
Electroslag Remelting (ESR):
Casting is performed in preheated molds to avoid thermal shock, with cooling rates controlled to prevent microsegregation. Post-casting, ingots undergo ultrasonic testing to detect internal defects .
Forging and Hot Working
Forging transforms cast ingots into semi-finished products (billets, bars) while enhancing mechanical properties through grain refinement. Key parameters include:
Table 2: Forging Temperature Ranges for this compound-276
Process Stage | Temperature Range (°C) | Holding Time (Hours) |
---|---|---|
Pre-forging heating | 980–1020 | 1–1.5 |
Final forging | 1140–1160 | 5–6 |
-
Multi-fire forging is employed, with intermediate reheating to maintain workability. Each "fire" (deformation cycle) reduces grain size by 30–40%, and finish forging temperatures are kept above 1000°C to avoid cracking .
-
Temperature compensation systems on hydraulic presses mitigate heat loss during deformation, extending the effective forging window .
Post-forging, components are air-cooled to prevent residual stress accumulation.
Heat Treatment and Solution Annealing
Solution annealing eliminates intermetallic phases (e.g., μ-phase, carbides) that form during processing. The standard protocol involves:
-
Heating to 1080–1120°C in a controlled atmosphere furnace.
-
Holding for 15–16 hours to ensure complete dissolution of secondary phases .
-
Rapid quenching in water or air to retain a single-phase austenitic structure .
Table 3: Mechanical Properties After Solution Annealing
Condition | Tensile Strength (MPa) | Yield Strength (MPa) | Elongation (%) |
---|---|---|---|
Annealed | 455 | 842 | 40 |
Cold Worked (40%) | 1310 | 1531 | 3.8 |
Cold working further enhances strength but requires careful strain control to avoid embrittlement .
Mechanical Processing: Rolling and Machining
Hot Rolling
-
Conducted at 950–1200°C to produce plates and sheets.
-
Reductions per pass limited to 20–25% to prevent edge cracking .
Cold Rolling
-
Achieves final thicknesses <0.5 mm with intermediate annealing at 1050°C.
-
Surface finish is critical; electrolytic polishing removes oxide layers .
Machining
-
Low cutting speeds (10–20 m/min) and high feed rates minimize work hardening.
-
Carbide-tipped tools are preferred for turning and milling .
Quality Control and Testing
Non-Destructive Testing (NDT):
Metallographic Analysis:
-
Etching with Marble’s reagent (10% HCl, 90% H2O) reveals grain structure.
-
ASTM E112 standards specify acceptable grain size (ASTM No. 5–7) .
Corrosion Testing:
Emerging Trends and Innovations
Recent advancements focus on additive manufacturing (AM) of this compound-276. Laser powder bed fusion (LPBF) enables complex geometries with fine microstructures, though post-build heat treatment at 1150°C is necessary to relieve residual stresses . Hybrid processes combining AM with hot isostatic pressing (HIP) show promise for aerospace components .
Properties
CAS No. |
11114-92-4 |
---|---|
Molecular Formula |
CoCr |
Molecular Weight |
110.929 g/mol |
IUPAC Name |
chromium;cobalt |
InChI |
InChI=1S/Co.Cr |
InChI Key |
WAIPAZQMEIHHTJ-UHFFFAOYSA-N |
SMILES |
[Cr].[Co] |
Canonical SMILES |
[Cr].[Co] |
Key on ui other cas no. |
12052-27-6 |
Origin of Product |
United States |
Disclaimer and Information on In-Vitro Research Products
Please be aware that all articles and product information presented on BenchChem are intended solely for informational purposes. The products available for purchase on BenchChem are specifically designed for in-vitro studies, which are conducted outside of living organisms. In-vitro studies, derived from the Latin term "in glass," involve experiments performed in controlled laboratory settings using cells or tissues. It is important to note that these products are not categorized as medicines or drugs, and they have not received approval from the FDA for the prevention, treatment, or cure of any medical condition, ailment, or disease. We must emphasize that any form of bodily introduction of these products into humans or animals is strictly prohibited by law. It is essential to adhere to these guidelines to ensure compliance with legal and ethical standards in research and experimentation.