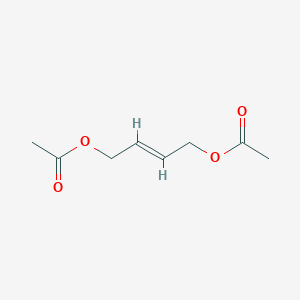
But-2-ene-1,4-diyl diacetate
Overview
Description
It is a colorless to yellow sticky oil or semi-solid that is used in various chemical synthesis processes . This compound is characterized by its two acetate groups attached to a butene backbone, making it a versatile intermediate in organic chemistry.
Mechanism of Action
Target of Action
But-2-ene-1,4-diyl diacetate is a chemical compound with the molecular formula C8H12O4
Action Environment
Environmental factors can significantly influence the action, efficacy, and stability of a compound. For this compound, it is recommended to be stored in a dry environment at a temperature between 2-8°C . .
Preparation Methods
Synthetic Routes and Reaction Conditions: But-2-ene-1,4-diyl diacetate is typically synthesized through the esterification of 1,4-butanediol with acetic anhydride. The reaction is usually carried out under anhydrous conditions with an acid catalyst to facilitate the esterification process . The reaction conditions often involve moderate temperatures to ensure complete conversion of the diol to the diacetate.
Industrial Production Methods: In an industrial setting, the production of this compound follows similar principles but on a larger scale. The process involves the continuous feeding of 1,4-butanediol and acetic anhydride into a reactor, where the reaction is catalyzed by an acid such as sulfuric acid. The product is then purified through distillation to achieve the desired purity levels .
Chemical Reactions Analysis
Types of Reactions: But-2-ene-1,4-diyl diacetate undergoes various chemical reactions, including:
Isomerization: This compound can be isomerized using catalysts such as Grubbs G2 and Hoveyda-Grubbs HG2, leading to rapid isomerization with high yields.
Hydrolysis: The diacetate can be hydrolyzed to yield 1,4-butanediol and acetic acid under acidic or basic conditions.
Common Reagents and Conditions:
Isomerization: Catalysts like Grubbs G2 and Hoveyda-Grubbs HG2 in solvents such as benzotrifluoride (BTF) or dichloromethane (DCM).
Hydrolysis: Acidic or basic aqueous solutions are commonly used for hydrolysis reactions.
Major Products:
Isomerization: The major product is the isomerized form of this compound.
Hydrolysis: The major products are 1,4-butanediol and acetic acid.
Scientific Research Applications
But-2-ene-1,4-diyl diacetate has several applications in scientific research:
Organic Synthesis: It serves as an intermediate in the synthesis of various organic compounds, including polymers and pharmaceuticals.
Polymer Chemistry: It is used in ring-opening metathesis polymerization (ROMP) and other olefin metathesis reactions to produce high molecular weight polymers.
Chemical Research: The compound is utilized in studying reaction mechanisms and developing new catalytic processes.
Comparison with Similar Compounds
1,4-Butanediol diacetate: Similar in structure but lacks the double bond present in but-2-ene-1,4-diyl diacetate.
2-Butene-1,4-diol diacetate: Another isomer with different spatial arrangement of atoms.
Uniqueness: this compound is unique due to its double bond, which imparts distinct reactivity and makes it suitable for specific catalytic processes such as olefin metathesis . This differentiates it from other similar compounds that may not possess the same level of reactivity or versatility in chemical synthesis.
Properties
IUPAC Name |
[(E)-4-acetyloxybut-2-enyl] acetate | |
---|---|---|
Source | PubChem | |
URL | https://pubchem.ncbi.nlm.nih.gov | |
Description | Data deposited in or computed by PubChem | |
InChI |
InChI=1S/C8H12O4/c1-7(9)11-5-3-4-6-12-8(2)10/h3-4H,5-6H2,1-2H3/b4-3+ | |
Source | PubChem | |
URL | https://pubchem.ncbi.nlm.nih.gov | |
Description | Data deposited in or computed by PubChem | |
InChI Key |
VZUAUHWZIKOMFC-ONEGZZNKSA-N | |
Source | PubChem | |
URL | https://pubchem.ncbi.nlm.nih.gov | |
Description | Data deposited in or computed by PubChem | |
Canonical SMILES |
CC(=O)OCC=CCOC(=O)C | |
Source | PubChem | |
URL | https://pubchem.ncbi.nlm.nih.gov | |
Description | Data deposited in or computed by PubChem | |
Isomeric SMILES |
CC(=O)OC/C=C/COC(=O)C | |
Source | PubChem | |
URL | https://pubchem.ncbi.nlm.nih.gov | |
Description | Data deposited in or computed by PubChem | |
Molecular Formula |
C8H12O4 | |
Source | PubChem | |
URL | https://pubchem.ncbi.nlm.nih.gov | |
Description | Data deposited in or computed by PubChem | |
Molecular Weight |
172.18 g/mol | |
Source | PubChem | |
URL | https://pubchem.ncbi.nlm.nih.gov | |
Description | Data deposited in or computed by PubChem | |
CAS No. |
18621-75-5 | |
Record name | 1,4-Diacetoxy-2-butene | |
Source | ChemIDplus | |
URL | https://pubchem.ncbi.nlm.nih.gov/substance/?source=chemidplus&sourceid=0018621755 | |
Description | ChemIDplus is a free, web search system that provides access to the structure and nomenclature authority files used for the identification of chemical substances cited in National Library of Medicine (NLM) databases, including the TOXNET system. | |
Record name | 2-Butene-1,4-diol, 1,4-diacetate | |
Source | European Chemicals Agency (ECHA) | |
URL | https://echa.europa.eu/information-on-chemicals | |
Description | The European Chemicals Agency (ECHA) is an agency of the European Union which is the driving force among regulatory authorities in implementing the EU's groundbreaking chemicals legislation for the benefit of human health and the environment as well as for innovation and competitiveness. | |
Explanation | Use of the information, documents and data from the ECHA website is subject to the terms and conditions of this Legal Notice, and subject to other binding limitations provided for under applicable law, the information, documents and data made available on the ECHA website may be reproduced, distributed and/or used, totally or in part, for non-commercial purposes provided that ECHA is acknowledged as the source: "Source: European Chemicals Agency, http://echa.europa.eu/". Such acknowledgement must be included in each copy of the material. ECHA permits and encourages organisations and individuals to create links to the ECHA website under the following cumulative conditions: Links can only be made to webpages that provide a link to the Legal Notice page. | |
Synthesis routes and methods I
Procedure details
Synthesis routes and methods II
Procedure details
Synthesis routes and methods III
Procedure details
Synthesis routes and methods IV
Procedure details
Q1: What is the significance of But-2-ene-1,4-diyl diacetate in olefin metathesis reactions?
A1: this compound serves as a model substrate for studying isomerization reactions catalyzed by Grubbs' catalysts, specifically the second-generation (G2) and Hoveyda-Grubbs (HG2) catalysts []. These reactions are crucial in organic synthesis for rearranging double bonds within a molecule.
Q2: How does Benzotrifluoride (BTF) compare to Dichloromethane (DCM) as a solvent for isomerization reactions involving this compound?
A2: Research indicates that Benzotrifluoride (BTF) is a viable and potentially advantageous alternative to Dichloromethane (DCM) for isomerization reactions of this compound catalyzed by G2 and HG2 catalysts []. The study showed that reactions performed in BTF exhibited significantly faster initial rates compared to DCM, achieving high yields within shorter reaction times []. This finding highlights the potential of BTF as a more environmentally friendly solvent option for olefin metathesis reactions.
Disclaimer and Information on In-Vitro Research Products
Please be aware that all articles and product information presented on BenchChem are intended solely for informational purposes. The products available for purchase on BenchChem are specifically designed for in-vitro studies, which are conducted outside of living organisms. In-vitro studies, derived from the Latin term "in glass," involve experiments performed in controlled laboratory settings using cells or tissues. It is important to note that these products are not categorized as medicines or drugs, and they have not received approval from the FDA for the prevention, treatment, or cure of any medical condition, ailment, or disease. We must emphasize that any form of bodily introduction of these products into humans or animals is strictly prohibited by law. It is essential to adhere to these guidelines to ensure compliance with legal and ethical standards in research and experimentation.