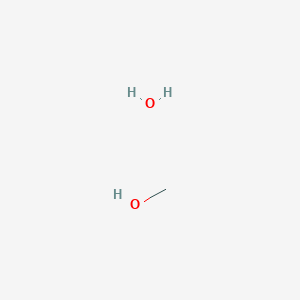
Water methanol
- 専門家チームからの見積もりを受け取るには、QUICK INQUIRYをクリックしてください。
- 品質商品を競争力のある価格で提供し、研究に集中できます。
説明
Water-methanol mixtures are hydroalcoholic solvents widely used in chemical, pharmaceutical, and environmental research due to their tunable polarity and extraction efficiency. Methanol (CH₃OH) is a polar protic solvent with a dielectric constant of 32.7, while water (H₂O) has a dielectric constant of 80.1. Blending these solvents creates a medium with intermediate polarity, making it ideal for extracting moderately polar compounds such as phenolic acids, flavonoids, and alkaloids . For example, 60–80% methanol in water is optimal for phenolic compound extraction, as it matches the polarity of these biomolecules while enhancing solubility and matrix penetration .
化学反応の分析
Decomposition and Secondary Reactions
Methanol decomposition pathways diverge based on water content:
-
Without water : CH₃OH → CO + 2H₂ (ΔH° = +90.7 kJ/mol), producing CO and H₂ .
-
With water : Overoxidation is suppressed, favoring CH₃OH stability. Copper-zinc oxide catalysts exhibit 80% methanol selectivity in aqueous systems versus 30% in anhydrous conditions .
Electric fields (0.35–0.40 V/Å) induce unique methanol-water reactivity, forming:
Catalytic Mechanisms and Kinetics
Density functional theory (DFT) and ab initio molecular dynamics reveal:
-
CO hydrogenation proceeds via formate (HCOO⁻) or methoxide (CH₃O⁻) intermediates on Cu(211) surfaces .
-
Water inhibition : Excess H₂O disrupts H-bond networks, reducing proton conductivity and field-induced reactivity in methanol-rich mixtures .
Thermodynamic and Kinetic Data
Parameter | Value | Source |
---|---|---|
Equilibrium constant (Kp₁, 513 K) | 2.1 × 10⁻⁵ bar⁻² | |
Activation energy (CO hydrogenation) | 75–85 kJ·mol⁻¹ | |
Water activity (50% MeOH) | 0.62 (vs. ideal 0.67) |
Recycling unconverted syngas and in-situ product removal enhance methanol yields by shifting equilibria .
Environmental and Industrial Implications
-
Waste valorization : Plasma-assisted systems convert methane emissions to methanol with 93% selectivity, mitigating CO₂ byproducts .
-
Catalyst design : Bimetallic Cu/ZnO interfaces optimize H₂ spillover and CO/CO₂ adsorption, critical for large-scale methanol plants .
This synthesis underscores the interplay between water content, catalytic architecture, and reaction conditions in methanol chemistry.
Q & A
Basic Research Questions
Q. What experimental design methodologies are recommended for optimizing methanol synthesis parameters?
Utilize a Design of Experiment (DoE) approach with factorial studies to evaluate variables such as molar ratios, synthesis methods, and solvents. For example, a 3-factor, 2-level full factorial design can identify optimal conditions for cocrystal formation or catalytic activity . Statistical software (e.g., Minitab) aids in generating randomized experimental runs and analyzing interactions between variables.
Q. How are vapor-liquid equilibrium (VLE) data validated for methanol-containing systems?
Apply thermodynamic consistency tests using UNIFAC model parameters. For methanol-ethylene carbonate systems, isobaric VLE measurements at 101.325 kPa are compared with model predictions to ensure deviations remain within acceptable limits. This method confirms reliability for reactor and distillation column design .
Q. What analytical techniques are critical for quantifying methanol in reaction products?
Gas chromatography (GC) with flame ionization detection (FID) is standard for species-specific quantification. For residual solvent analysis (e.g., methanol at 3000 ppm), calibrate standards using Karl Fischer titration or GC-headspace methods, ensuring alignment with pharmacopeial guidelines .
Advanced Research Questions
Q. How can kinetic contradictions between experimental and modeled reactor data be resolved?
Calibrate plug-flow reactor models using experimental datasets spanning industrial-relevant conditions (e.g., 3–7 MPa pressure, 7,000–13,000 h⁻¹ GHSV). For Cu/Zn/Al/Zr catalysts, validate kinetic parameters (e.g., Graaf’s rate expressions) by ensuring model deviations remain below 10% for product species flow rates .
Q. What strategies improve CO₂-to-methanol catalyst performance under varying CO/CO₂ ratios?
Test catalysts across stoichiometric number ratios (H₂/CO₂ = 3–6) and CO co-feeds. Use isothermal fixed-bed reactors (e.g., 9.1 mm diameter, 0.5 g catalyst loading) to assess activity. Calibrated models must account for reverse water-gas shift (RWGS) reactions to predict methanol yield accurately .
Q. How do adsorption-enhanced processes boost methanol and DME synthesis efficiency?
Integrate zeolitic membranes (e.g., LTA 3A) for in situ water removal, shifting equilibrium toward methanol. For sorption-enhanced DME synthesis, optimize cycle designs (e.g., pressure swing) to achieve >99% CO₂ conversion and 82% DME yield .
Q. What nonthermal plasma configurations enhance direct methane-to-methanol conversion?
Use pulsed discharge reactors (e.g., metal tubular reactors) with peak voltages ≥25 kV. Combine with V₂O₅-SiO₂ catalysts to increase methanol selectivity (~38%) and CH₄ conversion (~2%). Optimize power transfer efficiency (>50%) by adjusting circuit inductance and capacitance .
Q. How are hexagonal In₂O₃ nanocatalysts rationally designed for high methanol selectivity?
Employ density functional theory (DFT) to predict catalytic activity of exposed facets (e.g., hexagonal In₂O₃(104)). Synthesize phase-pure nanomaterials and validate via stability tests under industrial conditions (e.g., 250–300°C, 50 bar). Experimental methanol selectivity should exceed 90% .
Q. What methods address SAPO-34 catalyst deactivation in methanol-to-olefins (MTO) processes?
Characterize pore structure and acidity using NH₃-TPD and XRD. Adjust synthesis parameters (e.g., SiO₂/Al₂O₃ ratio, templating agents) to balance Brønsted acid sites and mitigate coking. In situ regeneration via oxidative treatments restores >80% initial activity .
Q. How are multi-scale models developed for techno-economic assessment (TEA) of methanol processes?
Integrate lab-scale kinetic data (e.g., from fixed-bed reactors) into Aspen Plus simulations. Compare state-of-the-art (SOT) and conventional two-step processes, evaluating metrics like carbon efficiency (~60% for SOT) and levelized cost of methanol (LCOM) .
類似化合物との比較
Comparison with Similar Compounds/Solvents
Water-Methanol vs. Water-Ethanol
Both hydroalcoholic mixtures are effective for extracting bioactive compounds, but key differences exist:
Research Findings :
- Methanol-water extracts showed 20–30% higher total phenolic content than ethanol-water in Rosa canina and Astragalus caprinus .
- Ethanol-water outperformed methanol-water in extracting caffeine and non-polar volatiles from tea and coffee wastes .
Water-Methanol vs. Pure Methanol or Water
Key Studies :
- Methanol-water (70%) extracted 3× more flavonoids from Retama sphaerocarpa than pure methanol or water .
- Pure methanol denatured antiplatelet compounds in Ardisia elliptica, whereas methanol-water preserved bioactivity .
Water-Methanol vs. Subcritical Water
Subcritical water (100–374°C under pressure) mimics organic solvents like methanol by reducing dielectric constants (ε < 30).
Data :
- Subcritical water achieved 90% of methanol-water’s polyphenol yield from Orostachys japonicus but degraded 15% of flavonoids .
準備方法
Distillation and Separation Techniques in Industrial Methanol Production
Fundamentals of Methanol-Water Distillation
Methanol and water form an azeotropic mixture, making their separation challenging due to their high mutual solubility and close boiling points (methanol: 64.7°C, water: 100°C). Industrial facilities employ fractional distillation columns to achieve high-purity methanol (>99.85%). The Ampco methanol plant, for instance, uses a multi-stage distillation process where the mixture is heated under controlled pressure to separate methanol vapor from residual water . The vapor is condensed, with a portion refluxed to enhance purity, while wastewater is treated for disposal .
Key Parameters in Industrial Distillation
Parameter | Value/Description | Source |
---|---|---|
Daily water consumption | 3,000 metric tons | |
Column height | >30 meters (to accommodate reflux stages) | |
Energy input | Steam-intensive process (~8 MW power demand) |
Advanced Distillation in eMethanol Synthesis
Liquid Wind’s eMethanol production integrates carbon capture with renewable hydrogen, followed by catalytic synthesis and distillation. The exothermic reaction (CO₂ + 3H₂ → CH₃OH + H₂O) generates heat that is repurposed to drive distillation, improving energy efficiency . The final mixture undergoes vacuum distillation to remove water, achieving fuel-grade methanol .
Analytical Standard Preparation for Methanol Quantification
EPA Method 308: Dilution-Based Standards
The U.S. Environmental Protection Agency (EPA) mandates precise preparation of methanol standards for emissions testing. A stock solution (1,000 µg/mL) is diluted to 10 µg/mL using deionized water, with strict control over volumetric glassware and temperature . Calibration curves are validated using spike recovery tests (85–115% acceptable range) .
NCASI GC/FID Protocol for Industrial Wastewater
The NCASI DI/MEOH-94.03 method specifies gas chromatography with flame ionization detection (GC/FID) for methanol analysis in pulp/paper mill effluents. Samples are diluted with water to fit a 0.5–100 mg/L linear range, then injected into a capillary column (e.g., DB-WAX) with temperature programming . Methanol is identified via retention time matching and confirmed with a second column .
Analytical Method Comparison
Method | Sensitivity (MML) | Applicability | Key Challenge |
---|---|---|---|
EPA 308 | 10 µg/mL | Stack gas emissions | Matrix interference |
NCASI DI/MEOH | 0.5 mg/L | Industrial wastewater | Co-eluting organics |
Catalytic Reforming and Synthesis Methods
Base-Free Aqueous Methanol Reforming
Recent advances in homogeneous catalysis enable hydrogen production via methanol-water reforming without base additives. An acridine-ruthenium pincer complex (e.g., Ru-1 ) achieves a turnover number (TON) of 130,000 H₂ when augmented with hexanethiol, which stabilizes the active thiolate intermediate (Ru-3 ) . The mechanism involves outer-sphere dehydrogenation, bypassing energy-intensive inner-sphere pathways .
Catalytic Performance Metrics
Catalyst System | TON (H₂) | TOF (h⁻¹) | Stability |
---|---|---|---|
Ru-1 + hexanethiol | 130,000 | 464 | >3 weeks at 150°C |
Ni/α-MoC heterogenous | 6× Pt/Al₂O₃ | N/A | >100 hours |
Heterogeneous Catalysis for Large-Scale Production
Atomically dispersed nickel on α-MoC substrates enhances methanol reforming efficiency, achieving hydrogen production rates sixfold higher than Pt/Al₂O₃. The Ni₁-Cₓ motif stabilizes active sites, enabling sustained activity in aqueous conditions .
Industrial-Scale Utilities and Water Management
Water Purification Requirements
Methanol plants require ultra-pure water (conductivity <1 µS/cm) to prevent catalyst poisoning. AMPCO’s facility uses reverse osmosis and ion exchange to treat 3,000 metric tons/day of feedwater, with wastewater treated via anaerobic digestion post-distillation .
Energy Integration in Modern Plants
Exothermic methanol synthesis (ΔH = −49 kJ/mol) provides 40–60% of the thermal energy needed for distillation, reducing reliance on external utilities . Liquid Wind’s design recovers 85% of reaction heat for water-methanol separation .
Emerging Technologies and Innovations
Membrane-Based Separation
Pervaporation membranes (e.g., polyvinyl alcohol composites) show promise for reducing distillation energy costs. Pilot studies report 90% methanol selectivity with flux rates of 2.5 kg/m²·h, though durability remains a challenge .
Plasma-Assisted Methanol Synthesis
Non-thermal plasma reactors enable low-temperature (50–100°C) methanol synthesis from CO₂/H₂ mixtures, achieving 12% conversion efficiency. Water is co-produced and removed via in-situ adsorption .
特性
CAS番号 |
151900-28-6 |
---|---|
分子式 |
CH6O2 |
分子量 |
50.057 g/mol |
IUPAC名 |
methanol;hydrate |
InChI |
InChI=1S/CH4O.H2O/c1-2;/h2H,1H3;1H2 |
InChIキー |
GBMDVOWEEQVZKZ-UHFFFAOYSA-N |
正規SMILES |
CO.O |
製品の起源 |
United States |
試験管内研究製品の免責事項と情報
BenchChemで提示されるすべての記事および製品情報は、情報提供を目的としています。BenchChemで購入可能な製品は、生体外研究のために特別に設計されています。生体外研究は、ラテン語の "in glass" に由来し、生物体の外で行われる実験を指します。これらの製品は医薬品または薬として分類されておらず、FDAから任何の医療状態、病気、または疾患の予防、治療、または治癒のために承認されていません。これらの製品を人間または動物に体内に導入する形態は、法律により厳格に禁止されています。これらのガイドラインに従うことは、研究と実験において法的および倫理的な基準の遵守を確実にするために重要です。