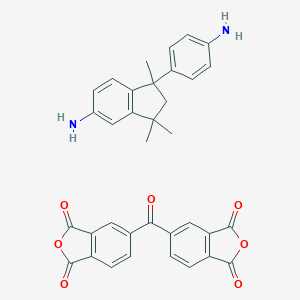
ポリイミド樹脂
概要
説明
科学的研究の応用
Dimorpholamine has a wide range of applications in scientific research:
Chemistry: It is used as a reagent in organic synthesis and as a catalyst in certain chemical reactions.
Biology: Dimorpholamine is used in studies related to respiratory and circulatory functions.
Medicine: It is investigated for its potential therapeutic applications in treating respiratory and circulatory insufficiencies.
Industry: Dimorpholamine is used in the production of pharmaceuticals and other chemical products
作用機序
ジモルホラミンは、脳の呼吸器と循環器の中枢を刺激することで効果を発揮します。これは、呼吸量と血圧の上昇につながります。ジモルホラミンの分子標的は、呼吸器と循環器の中枢にある受容体であり、化合物の結合により活性化されます。 作用機序に関与する正確な経路はまだ調査中です .
類似化合物の比較
類似化合物
- N,N’-ジブチル-N,N’-ジカルボキシモルホリンエチレンジアミン
- N-ブチルモルホリン-4-カルボキサミド
- エチレンジアミン誘導体
ユニークさ
ジモルホラミンは、呼吸器と循環器の中枢の両方に対する強力な刺激作用を持つためユニークです。 他の類似化合物とは異なり、それは二重の効果を持ち、呼吸器と循環器の不全を含む状態の治療に非常に効果的です .
準備方法
合成ルートと反応条件
ジモルホラミンは、N-ブチルモルホリン-4-カルボキサミドとエチレンジアミンとの反応によって合成することができます。この反応は、通常、エタノールなどの溶媒を使用し、還流条件下で行われます。 生成物はその後、再結晶によって精製されます .
工業的製造方法
工業的な環境では、ジモルホラミンの製造は、同様の合成ルートに従いますが、より大規模で行われます。反応条件は、最終生成物の高収率と高純度を確保するために最適化されます。 連続フローリアクターや自動化システムの使用は、反応条件と製品品質の一貫性を維持するのに役立ちます .
化学反応の分析
反応の種類
ジモルホラミンは、次のようなさまざまな化学反応を起こします。
酸化: ジモルホラミンは、対応する酸化物を形成するために酸化することができます。
還元: これは、アミンを形成するために還元することができます。
一般的な試薬と条件
酸化: 一般的な酸化剤には、過マンガン酸カリウムと過酸化水素があります。
還元: 水素化リチウムアルミニウムや水素化ホウ素ナトリウムなどの還元剤が使用されます。
生成される主な生成物
これらの反応から生成される主な生成物には、ジモルホラミンの酸化物、還元されたアミン、置換された化合物などのさまざまなジモルホラミンの誘導体が含まれます .
科学研究への応用
ジモルホラミンは、科学研究で幅広い用途があります。
化学: 有機合成における試薬として、特定の化学反応における触媒として使用されます。
生物学: ジモルホラミンは、呼吸器と循環器の機能に関連する研究に使用されています。
医学: 呼吸器と循環器の不全の治療における潜在的な治療的用途について調査されています。
類似化合物との比較
Similar Compounds
- N,N’-dibutyl-N,N’-dicarboxymorpholine ethylenediamine
- N-butylmorpholine-4-carboxamide
- Ethylenediamine derivatives
Uniqueness
Dimorpholamine is unique due to its potent stimulating action on both respiratory and circulatory centers. Unlike other similar compounds, it has a dual effect, making it highly effective in treating conditions involving respiratory and circulatory insufficiency .
特性
IUPAC Name |
1-(4-aminophenyl)-1,3,3-trimethyl-2H-inden-5-amine;5-(1,3-dioxo-2-benzofuran-5-carbonyl)-2-benzofuran-1,3-dione | |
---|---|---|
Source | PubChem | |
URL | https://pubchem.ncbi.nlm.nih.gov | |
Description | Data deposited in or computed by PubChem | |
InChI |
InChI=1S/C18H22N2.C17H6O7/c1-17(2)11-18(3,12-4-6-13(19)7-5-12)15-9-8-14(20)10-16(15)17;18-13(7-1-3-9-11(5-7)16(21)23-14(9)19)8-2-4-10-12(6-8)17(22)24-15(10)20/h4-10H,11,19-20H2,1-3H3;1-6H | |
Source | PubChem | |
URL | https://pubchem.ncbi.nlm.nih.gov | |
Description | Data deposited in or computed by PubChem | |
InChI Key |
CDTDIQLZIBORMV-UHFFFAOYSA-N | |
Source | PubChem | |
URL | https://pubchem.ncbi.nlm.nih.gov | |
Description | Data deposited in or computed by PubChem | |
Canonical SMILES |
CC1(CC(C2=C1C=C(C=C2)N)(C)C3=CC=C(C=C3)N)C.C1=CC2=C(C=C1C(=O)C3=CC4=C(C=C3)C(=O)OC4=O)C(=O)OC2=O | |
Source | PubChem | |
URL | https://pubchem.ncbi.nlm.nih.gov | |
Description | Data deposited in or computed by PubChem | |
Molecular Formula |
C35H28N2O7 | |
Source | PubChem | |
URL | https://pubchem.ncbi.nlm.nih.gov | |
Description | Data deposited in or computed by PubChem | |
DSSTOX Substance ID |
DTXSID70910001 | |
Record name | 5,5'-Carbonyldi(2-benzofuran-1,3-dione)--1-(4-aminophenyl)-1,3,3-trimethyl-2,3-dihydro-1H-inden-5-amine (1/1) | |
Source | EPA DSSTox | |
URL | https://comptox.epa.gov/dashboard/DTXSID70910001 | |
Description | DSSTox provides a high quality public chemistry resource for supporting improved predictive toxicology. | |
Molecular Weight |
588.6 g/mol | |
Source | PubChem | |
URL | https://pubchem.ncbi.nlm.nih.gov | |
Description | Data deposited in or computed by PubChem | |
CAS No. |
62929-02-6, 106442-40-4 | |
Record name | 1,3-Isobenzofurandione, 5,5'-carbonylbis-, polymer with 1(or 3)-(4-aminophenyl)-2,3-dihydro-1,3,3(or 1,1,3)-trimethyl-1H-inden-5-amine | |
Source | EPA Chemicals under the TSCA | |
URL | https://www.epa.gov/chemicals-under-tsca | |
Description | EPA Chemicals under the Toxic Substances Control Act (TSCA) collection contains information on chemicals and their regulations under TSCA, including non-confidential content from the TSCA Chemical Substance Inventory and Chemical Data Reporting. | |
Record name | 5,5'-Carbonyldi(2-benzofuran-1,3-dione)--1-(4-aminophenyl)-1,3,3-trimethyl-2,3-dihydro-1H-inden-5-amine (1/1) | |
Source | EPA DSSTox | |
URL | https://comptox.epa.gov/dashboard/DTXSID70910001 | |
Description | DSSTox provides a high quality public chemistry resource for supporting improved predictive toxicology. | |
Record name | 1,3-Isobenzofurandione, 5,5'-carbonylbis-, polymer with 1(or 3)-(4-aminophenyl)-2,3-dihydro-1,3,3(or 1,1,3)-trimethyl-1H-inden-5 | |
Source | European Chemicals Agency (ECHA) | |
URL | https://echa.europa.eu/information-on-chemicals | |
Description | The European Chemicals Agency (ECHA) is an agency of the European Union which is the driving force among regulatory authorities in implementing the EU's groundbreaking chemicals legislation for the benefit of human health and the environment as well as for innovation and competitiveness. | |
Explanation | Use of the information, documents and data from the ECHA website is subject to the terms and conditions of this Legal Notice, and subject to other binding limitations provided for under applicable law, the information, documents and data made available on the ECHA website may be reproduced, distributed and/or used, totally or in part, for non-commercial purposes provided that ECHA is acknowledged as the source: "Source: European Chemicals Agency, http://echa.europa.eu/". Such acknowledgement must be included in each copy of the material. ECHA permits and encourages organisations and individuals to create links to the ECHA website under the following cumulative conditions: Links can only be made to webpages that provide a link to the Legal Notice page. | |
Synthesis routes and methods I
Procedure details
Synthesis routes and methods II
Procedure details
Synthesis routes and methods III
Procedure details
Synthesis routes and methods IV
Procedure details
Retrosynthesis Analysis
AI-Powered Synthesis Planning: Our tool employs the Template_relevance Pistachio, Template_relevance Bkms_metabolic, Template_relevance Pistachio_ringbreaker, Template_relevance Reaxys, Template_relevance Reaxys_biocatalysis model, leveraging a vast database of chemical reactions to predict feasible synthetic routes.
One-Step Synthesis Focus: Specifically designed for one-step synthesis, it provides concise and direct routes for your target compounds, streamlining the synthesis process.
Accurate Predictions: Utilizing the extensive PISTACHIO, BKMS_METABOLIC, PISTACHIO_RINGBREAKER, REAXYS, REAXYS_BIOCATALYSIS database, our tool offers high-accuracy predictions, reflecting the latest in chemical research and data.
Strategy Settings
Precursor scoring | Relevance Heuristic |
---|---|
Min. plausibility | 0.01 |
Model | Template_relevance |
Template Set | Pistachio/Bkms_metabolic/Pistachio_ringbreaker/Reaxys/Reaxys_biocatalysis |
Top-N result to add to graph | 6 |
Feasible Synthetic Routes
Q1: What makes polyimide resins suitable for high-temperature applications?
A1: Polyimide resins possess remarkable heat resistance, with some formulations exhibiting glass transition temperatures exceeding 300°C [, ]. This characteristic stems from their aromatic structure and strong intermolecular forces, making them ideal for applications like aerospace components and electronic devices [, ].
Q2: How does the incorporation of fillers impact the properties of polyimide resins?
A2: Fillers like carbon fibers, thermally conductive ceramics, and modified graphene significantly enhance the mechanical, thermal, and electrical properties of polyimide resin composites [, , ]. For example, carbon fiber reinforcement substantially increases tensile and flexural strength, making them suitable for demanding structural applications [].
Q3: What are the advantages of using polyimide resins in flexible electronics?
A3: Polyimide resins exhibit excellent flexibility, high dielectric strength, and low coefficient of thermal expansion, making them suitable for flexible substrates in electronics [, ]. Their ability to be processed into thin films further expands their utility in flexible displays, sensors, and printed circuit boards [, ].
Q4: What is the typical molecular structure of a polyimide resin?
A4: Polyimide resins generally consist of repeating units formed by the reaction of dianhydrides, such as pyromellitic dianhydride, with diamines, like 4,4'-oxydianiline [, ]. The specific choice of monomers dictates the final properties of the resin.
Q5: How can the properties of polyimide resins be tailored through structural modifications?
A5: Incorporating specific monomers during synthesis can fine-tune resin properties. For instance, introducing bulky side groups or flexible linkages can influence glass transition temperature and solubility [, ].
Q6: What role does molecular weight play in determining polyimide resin characteristics?
A6: Molecular weight significantly influences viscosity, mechanical strength, and processing behavior [, ]. Higher molecular weight resins generally exhibit greater strength and toughness but can be more challenging to process.
Q7: What are the common curing mechanisms employed for polyimide resins?
A7: Polyimide resins can be cured thermally, typically at elevated temperatures, to induce imidization and crosslinking, resulting in a rigid, infusible network [, ]. Alternatively, some formulations utilize catalytic curing agents, such as isopropyl peroxide and cobalt naphthenate, to lower curing temperatures and reduce processing challenges [].
Q8: How does the choice of solvent affect the processing of polyimide resins?
A8: Solvent selection is crucial for achieving desired viscosity, film uniformity, and compatibility with other components [, ]. High-boiling-point polar solvents, while effective, can pose challenges during removal and impact final properties [, ].
Q9: What are some challenges associated with processing polyimide resins?
A9: High processing temperatures, potential for void formation, and the need for specialized equipment can pose challenges during manufacturing [, ]. Research continues to explore innovative processing techniques, such as resin transfer molding (RTM), to overcome these limitations and expand applications [].
Q10: What are the typical degradation pathways for polyimide resins?
A11: Degradation mechanisms can involve chain scission, oxidation, and hydrolysis, leading to deterioration of mechanical properties and changes in color []. Understanding these pathways is crucial for developing strategies to enhance long-term stability.
Q11: What analytical techniques are commonly employed to characterize polyimide resins?
A12: Techniques such as Fourier-transform infrared spectroscopy (FTIR), differential scanning calorimetry (DSC), thermogravimetric analysis (TGA), and dynamic mechanical analysis (DMA) are routinely used to analyze the chemical structure, thermal properties, and mechanical behavior of polyimide resins [, ].
Q12: How can surface modifications of polyimide resins be characterized?
A13: Surface analysis techniques like X-ray photoelectron spectroscopy (XPS) and time-of-flight secondary ion mass spectrometry (TOF-SIMS) provide insights into the chemical composition and modification of polyimide resin surfaces [].
Q13: What are the environmental concerns associated with polyimide resins?
A14: The inherent recalcitrance of some polyimide resins can pose challenges for recycling and disposal. Research is exploring biodegradable polyimide formulations and sustainable manufacturing processes to mitigate environmental impact [].
Q14: What are some emerging research trends in the field of polyimide resins?
A15: Current research focuses on developing high-performance, lightweight polyimide composites for aerospace applications, exploring bio-based and biodegradable polyimides for sustainability, and tailoring resin properties for advanced applications like flexible electronics and high-frequency communications [].
試験管内研究製品の免責事項と情報
BenchChemで提示されるすべての記事および製品情報は、情報提供を目的としています。BenchChemで購入可能な製品は、生体外研究のために特別に設計されています。生体外研究は、ラテン語の "in glass" に由来し、生物体の外で行われる実験を指します。これらの製品は医薬品または薬として分類されておらず、FDAから任何の医療状態、病気、または疾患の予防、治療、または治癒のために承認されていません。これらの製品を人間または動物に体内に導入する形態は、法律により厳格に禁止されています。これらのガイドラインに従うことは、研究と実験において法的および倫理的な基準の遵守を確実にするために重要です。