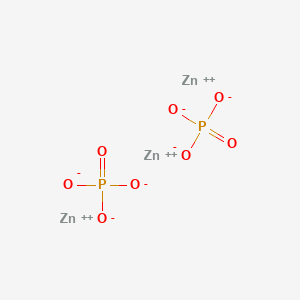
リン酸亜鉛
概要
説明
Zinc phosphate is an inorganic compound with the chemical formula Zn₃(PO₄)₂. It appears as a white, odorless, and tasteless powder. This compound is widely used as a corrosion-resistant coating on metal surfaces, either as part of an electroplating process or applied as a primer pigment. It has largely replaced toxic materials based on lead or chromium and has become the most commonly used corrosion inhibitor .
科学的研究の応用
Chemistry: Zinc phosphate is extensively used as a corrosion inhibitor in the metal industry. It forms a protective layer on metal surfaces, preventing oxidation and corrosion.
Biology and Medicine: In dentistry, zinc phosphate is employed as a dental cement for securing crowns, bridges, and orthodontic appliances. Its biocompatibility and bonding capability make it an effective material for dental applications .
Industry: Zinc phosphate is a common ingredient in paints and coatings due to its anti-corrosion properties. It is also used in the production of fertilizers, flame retardants, and glass manufacturing .
Environmental Applications: Recent studies have explored the use of zinc phosphate-based nanosheets for antibacterial and antioxidant activities, as well as for the sustainable decolorization of textile wastewater .
作用機序
Target of Action
Zinc Phosphate (Zn3(PO4)2) is an inorganic compound that primarily targets metal surfaces, acting as a corrosion-resistant coating . In the field of dentistry, it is used as a cement for permanent metal and zirconium dioxide restorations . It also interacts with various enzymes and transcription factors within biological systems .
Mode of Action
Zinc Phosphate forms a protective layer on metal surfaces, preventing corrosion and enhancing durability . In dentistry, it is mixed with zinc oxide (ZnO) and magnesium oxide (MgO) powders along with a liquid consisting principally of phosphoric acid, water, and buffers to form a cement . On a cellular level, zinc is known to bind to around 3000 proteins in vivo, representing about 10% of the human proteome .
Biochemical Pathways
Zinc Phosphate plays a significant role in various biochemical pathways and cellular functions, such as response to oxidative stress, homeostasis, immune responses, DNA replication, DNA damage repair, cell cycle progression, apoptosis, and aging . It is required for the synthesis of protein and collagen, thus contributing to wound healing and maintaining healthy skin .
Pharmacokinetics
Zinc Phosphate is a white solid that is insoluble in water . This property affects its Absorption, Distribution, Metabolism, and Excretion (ADME) properties, limiting its bioavailability. It is soluble in inorganic acids, ammonia, and ammonium salt solutions .
Result of Action
The molecular and cellular effects of Zinc Phosphate’s action are diverse. It contributes to the corrosion resistance of metal surfaces . In biological systems, it influences numerous physiological processes, including cell cycle progression, immune functions, and many other physiological procedures .
Action Environment
Environmental factors significantly influence the action, efficacy, and stability of Zinc Phosphate. For instance, the solubility of Zinc Phosphate in water decreases with increasing temperature . In biological systems, the availability of other nutrients in the environment influences the homeostasis of zinc within plants . Furthermore, the pH of the environment can affect the availability of zinc, especially in soils of low soluble organic matter .
生化学分析
Biochemical Properties
These enzymes, located on the external layer of the cell membrane, catalyze the hydrolysis of organic phosphate esters present in the extracellular space . Zinc and magnesium are significant co-factors for the biological activity of these enzymes .
Cellular Effects
The effects of Zinc Phosphate on cells are largely mediated through its interaction with ALPs. These enzymes are available in various body tissues and have distinct physiochemical properties . They influence cell function by catalyzing biochemical reactions involving phosphate esters .
Molecular Mechanism
At the molecular level, Zinc Phosphate exerts its effects through its role as a co-factor for ALPs. These enzymes require three metal ions, including two Zinc ions and one Magnesium ion, in their active site for their biological activity .
Metabolic Pathways
Zinc Phosphate is involved in the metabolic pathways related to the function of ALPs. These enzymes can hydrolyze or transphosphorylate a wide variety of phosphated compounds .
Subcellular Localization
The subcellular localization of Zinc Phosphate is likely related to the localization of ALPs, as these enzymes are its primary interaction partners. ALPs are located primarily in the ectoplasm and are anchored to the plasma membrane .
準備方法
Synthetic Routes and Reaction Conditions: Zinc phosphate is typically synthesized by the reaction of zinc oxide (ZnO) with phosphoric acid (H₃PO₄). The reaction occurs in an aqueous medium, producing zinc phosphate and water as byproducts: [ 3ZnO + 2H₃PO₄ \rightarrow Zn₃(PO₄)₂ + 3H₂O ]
Another method involves the reaction of zinc metal with phosphoric acid, which also produces hydrogen gas along with zinc phosphate: [ 3Zn + 2H₃PO₄ \rightarrow Zn₃(PO₄)₂ + 3H₂ ]
Industrial Production Methods: In industrial settings, zinc phosphate is produced by mixing zinc oxide and phosphoric acid under controlled conditions. The mixture is then heated to facilitate the reaction, and the resulting zinc phosphate is filtered, washed, and dried to obtain the final product .
Types of Reactions:
Oxidation and Reduction: Zinc phosphate itself is relatively stable and does not undergo significant oxidation or reduction under normal conditions.
Substitution Reactions: Zinc phosphate can participate in substitution reactions where the phosphate group is replaced by other anions or ligands.
Common Reagents and Conditions:
Phosphoric Acid: Used in the synthesis of zinc phosphate.
Zinc Oxide: A common starting material for the preparation of zinc phosphate.
Major Products Formed:
Zinc Phosphate: The primary product formed from the reaction of zinc oxide and phosphoric acid.
Water and Hydrogen Gas: Byproducts formed during the synthesis process.
類似化合物との比較
Hopeite (Zn₃(PO₄)₂·4H₂O): A natural hydrous form of zinc phosphate.
Parahopeite (Zn₃(PO₄)₂·4H₂O): Another natural hydrous form of zinc phosphate.
Tarbuttite (Zn₂(PO₄)(OH)): A natural hydrous zinc phosphate known from oxidation zones of zinc ore beds.
Uniqueness: Zinc phosphate is unique in its widespread use as a corrosion inhibitor, particularly in replacing toxic materials like lead and chromium. Its stability, biocompatibility, and versatility in various applications make it a valuable compound in multiple fields .
特性
CAS番号 |
7779-90-0 |
---|---|
分子式 |
H3O4PZn |
分子量 |
163.4 g/mol |
IUPAC名 |
phosphoric acid;zinc |
InChI |
InChI=1S/H3O4P.Zn/c1-5(2,3)4;/h(H3,1,2,3,4); |
InChIキー |
OXHXATNDTXVKAU-UHFFFAOYSA-N |
SMILES |
[O-]P(=O)([O-])[O-].[O-]P(=O)([O-])[O-].[Zn+2].[Zn+2].[Zn+2] |
正規SMILES |
OP(=O)(O)O.[Zn] |
Key on ui other cas no. |
13847-22-8 14332-60-6 7779-90-0 |
物理的記述 |
DryPowder; Liquid; OtherSolid, Liquid; WetSolid |
ピクトグラム |
Environmental Hazard |
同義語 |
PHOSPHORIC ACID ZINC SALT; ZINC PHOSPHATE TRIBASIC; ZINC PHOSPHATE (ORTHO); ZINC PHOSPHATE; ZINC ORTHOPHOSPHATE; bonderite40; bonderite880; c.i.77964 |
製品の起源 |
United States |
Synthesis routes and methods I
Procedure details
Synthesis routes and methods II
Procedure details
Synthesis routes and methods III
Procedure details
Synthesis routes and methods IV
Procedure details
Synthesis routes and methods V
Procedure details
Retrosynthesis Analysis
AI-Powered Synthesis Planning: Our tool employs the Template_relevance Pistachio, Template_relevance Bkms_metabolic, Template_relevance Pistachio_ringbreaker, Template_relevance Reaxys, Template_relevance Reaxys_biocatalysis model, leveraging a vast database of chemical reactions to predict feasible synthetic routes.
One-Step Synthesis Focus: Specifically designed for one-step synthesis, it provides concise and direct routes for your target compounds, streamlining the synthesis process.
Accurate Predictions: Utilizing the extensive PISTACHIO, BKMS_METABOLIC, PISTACHIO_RINGBREAKER, REAXYS, REAXYS_BIOCATALYSIS database, our tool offers high-accuracy predictions, reflecting the latest in chemical research and data.
Strategy Settings
Precursor scoring | Relevance Heuristic |
---|---|
Min. plausibility | 0.01 |
Model | Template_relevance |
Template Set | Pistachio/Bkms_metabolic/Pistachio_ringbreaker/Reaxys/Reaxys_biocatalysis |
Top-N result to add to graph | 6 |
Feasible Synthetic Routes
Q1: What is the molecular formula and weight of the most common form of zinc phosphate found in these studies?
A1: The most commonly encountered form of zinc phosphate in these studies is zinc phosphate tetrahydrate, with the molecular formula Zn₃(PO₄)₂·4H₂O [, , ]. Its molecular weight is 458.14 g/mol.
Q2: What spectroscopic techniques were used to characterize zinc phosphate in these studies?
A2: Several spectroscopic techniques were employed to characterize zinc phosphate, including: * X-ray diffraction (XRD) to determine crystal structure and phase identification [, , , , ].* Infrared (IR) spectroscopy to analyze chemical bonds and identify functional groups []. * Raman spectroscopy to identify and quantify components and study surface structure [].* Energy-dispersive X-ray spectroscopy (EDS) to determine elemental composition [, ]. * X-ray photoelectron spectroscopy (XPS) to analyze elemental composition and chemical states of elements [].* Scanning electron microscopy (SEM) to visualize surface morphology and microstructure [, , , , , , ].
Q3: How does the microstructure of zinc phosphate cement change with the addition of zinc oxide nanoparticles?
A3: The addition of zinc oxide nanoparticles to zinc phosphate cement leads to a denser microstructure with reduced cracks and a more homogeneous distribution of the nanoparticles []. This improvement in microstructure contributes to enhanced hardness and compressive strength of the cement.
Q4: How does the presence of iron impurities affect amorphous zinc phosphate?
A4: Iron impurities significantly inhibit the recrystallization of amorphous zinc phosphate []. During ball-milling, iron gets oxidized and incorporated into the zinc phosphate structure, replacing some zinc ions and creating zinc vacancies. These vacancies, coupled with Fe³⁺, bind water molecules more strongly, reducing water mobility and hindering recrystallization.
Q5: How do the anti-alkaline properties of zinc phosphate crystal films change with varying manganese content?
A5: As the manganese content in zinc phosphate crystal films increases, their resistance to alkaline solutions improves, particularly in highly alkaline environments (pH 13) []. This enhancement is attributed to the modification of the chemical structure of the zinc phosphate crystal films by manganese ions.
Q6: Does the addition of stannous fluoride to zinc phosphate cement affect its physical properties?
A6: While previous studies suggested minimal impact on setting time and compressive strength when replacing water with stannous fluoride solution [], further research is needed to assess the effects of higher fluoride concentrations on other properties like consistency, film thickness, solubility, and disintegration [].
Q7: What factors affect the quality of zinc phosphate coatings on steel in the automotive industry?
A7: The quality of zinc phosphate coatings on steel is significantly influenced by the surface characteristics of the steel substrate []. For example, the presence of residual zinc on one-side electrogalvanized steel can lead to less phosphorus incorporation in the coating, affecting its adhesion and anti-corrosion properties.
Q8: What are the advantages of using zinc phosphate as a pigment in waterborne epoxy paints for steel protection?
A8: Zinc phosphate pigments in waterborne epoxy paints provide efficient steel protection due to both barrier effects and the formation of a stable ferric phosphate layer []. This dual action effectively inhibits corrosion, even under damaged coating areas.
Q9: What are the potential applications of zinc phosphate cement in biomedical fields?
A9: Research suggests that zinc phosphate cement exhibits biocompatibility with human osteoblast-like cells [, ]. This finding suggests potential applications in bone contact applications, although further in vivo studies are needed to confirm its suitability.
Q10: How does zinc phosphate interact with stainless steel in dental applications?
A10: Zinc phosphate cement exhibits varying bond strengths with different dental materials []. For example, it shows lower bond strength to stainless steel compared to glass ionomer cement and polycarboxylate cement.
Q11: What is the impact of incorporating Bioglass® powder into zinc phosphate cement?
A11: The incorporation of Bioglass® powder into zinc phosphate cement enhances its bioactivity, promoting the formation of a Ca-P layer on its surface in simulated body fluid []. This modification improves cell attachment and activity without significantly impacting the cement's mechanical or physicochemical properties.
Q12: Can temporary cement cleaning methods impact the retention of crowns cemented with zinc phosphate cement?
A12: The use of temporary cement and its cleaning methods can affect the retention of permanently cemented crowns []. While air-abrasion after temporary cement removal improves the retention of crowns cemented with zinc phosphate cement, using temporary cement generally reduces the retention of crowns cemented with resin-modified glass ionomer cement.
Q13: How does the micro-osmosis of Mineral Trioxide Aggregate (MTA) compare to zinc phosphate cement when used as a cement for casting dowel pins?
A13: MTA exhibits significantly lower micro-osmosis compared to zinc phosphate cement when used as a cement for casting dowel pins []. This superior performance suggests that MTA might be a better choice for minimizing microleakage and potential bacterial contamination in dental applications.
Q14: What are the environmental concerns related to traditional zinc phosphate treatments, and what are the alternatives?
A15: Traditional zinc phosphate treatments often generate sludge, raising environmental concerns. To address this, researchers are exploring alternative zinc phosphate treating solutions that are sludge-free and environmentally friendly []. These solutions typically involve specific molar ratios of zinc, phosphoric acid, and nitric acid, along with additives to control the reaction and prevent sludge formation.
試験管内研究製品の免責事項と情報
BenchChemで提示されるすべての記事および製品情報は、情報提供を目的としています。BenchChemで購入可能な製品は、生体外研究のために特別に設計されています。生体外研究は、ラテン語の "in glass" に由来し、生物体の外で行われる実験を指します。これらの製品は医薬品または薬として分類されておらず、FDAから任何の医療状態、病気、または疾患の予防、治療、または治癒のために承認されていません。これらの製品を人間または動物に体内に導入する形態は、法律により厳格に禁止されています。これらのガイドラインに従うことは、研究と実験において法的および倫理的な基準の遵守を確実にするために重要です。