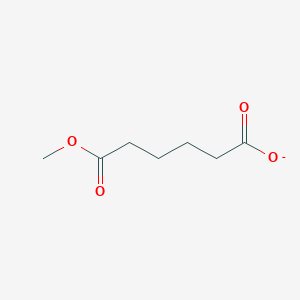
Methyl adipate
- Cliquez sur DEMANDE RAPIDE pour recevoir un devis de notre équipe d'experts.
- Avec des produits de qualité à un prix COMPÉTITIF, vous pouvez vous concentrer davantage sur votre recherche.
Vue d'ensemble
Description
Methyl adipate (CAS 627-91-8), a monoester of adipic acid and methanol, is a fatty acid derivative with the molecular formula C₇H₁₂O₄. It is synthesized via esterification reactions and is naturally identified in plant extracts, such as those from Phyllanthus emblica (Malacca fruit and bark), through GC-MS analysis . Industrially, it serves as an intermediate in plasticizer synthesis (e.g., diisooctyl adipate) and polymer modifications . Its polar nature, due to the single methyl ester group, distinguishes it from diesters like dithis compound.
Méthodes De Préparation
Acid-Catalyzed Batch Esterification
Conventional batch esterification remains a foundational method for methyl adipate synthesis. The process typically involves refluxing adipic acid with excess methanol in the presence of a homogeneous acid catalyst, such as sulfuric acid or hydrochloric acid. A representative protocol from patent CN102351691A demonstrates that sulfuric acid (98% concentration) catalyzes the dehydration of adipic acid at 145–170°C in solvents like trimethylbenzene, achieving a monoester yield of 96–97% after 4–6 hours. While this method simplifies post-reaction separation by generating adipic anhydride intermediates, it requires meticulous control of stoichiometry to minimize diethyl adipate byproducts.
Kinetic studies further elucidate the role of methanol-to-acid molar ratios. Research by Khosravi and Shinde revealed that increasing the methanol/adipic acid ratio from 10:1 to 20:1 enhanced conversion from 78% to 92% at 333 K using Amberlyst 15. However, excessive methanol necessitated energy-intensive recovery, highlighting a trade-off between yield and process efficiency.
Continuous Esterification Processes
Industrial-scale production increasingly adopts continuous esterification to improve throughput and reduce costs. Patent CN102442905A details a tubular reactor system where adipic acid and methanol undergo catalytic esterification at 120–150°C under pressurized conditions. The integration of a rectifying tower enables real-time removal of water, driving the equilibrium toward ester formation. This method achieved a dithis compound purity of >99% with a space velocity of 0.25 h⁻¹, significantly outperforming batch systems in productivity .
A novel vapor-phase approach (CN111320543A ) further optimizes continuous synthesis by introducing methanol vapor into a reaction tower containing adipic acid particles. At 1.08 MPa and 140°C, this method attained a 97.2% adipic acid conversion rate, with dithis compound constituting 37.3% of the product stream. The vapor-phase process minimizes solvent use and accelerates mass transfer, though it demands precise temperature control to prevent thermal degradation.
Solid Acid Catalysts in Esterification
Heterogeneous catalysis addresses environmental and corrosion concerns associated with liquid acids. Amberlyst 15, a macroreticular ion-exchange resin, has emerged as a robust catalyst for this compound synthesis. Khosravi and Shinde reported a 92% conversion at 333 K with a 20:1 methanol/adipic acid ratio and 10% catalyst loading. The pseudo-homogeneous kinetic model fit experimental data well, showing a second-order dependence on adipic acid concentration.
Table 1: Effect of Reaction Parameters on Amberlyst 15 Catalyzed Esterification
Temperature (K) | Methanol/Adipic Acid Ratio | Catalyst Loading (%) | Conversion (%) |
---|---|---|---|
313 | 10:1 | 5 | 65 |
323 | 15:1 | 7 | 78 |
333 | 20:1 | 10 | 92 |
Solid catalysts offer reusability; however, pore blockage and active site leaching after multiple cycles remain challenges.
Advanced Catalytic Systems and Innovations
Recent advancements explore Lewis acid catalysts, such as titanium tetrabutoxide, to enhance reaction rates. Although initially developed for bis-2-ethylhexyl adipate synthesis , titanium-based systems achieved 99% adipic acid conversion by activating carboxylic groups, suggesting adaptability for this compound production. Additionally, enzymatic esterification using lipases presents a green alternative, though industrial adoption is limited by enzyme cost and stability.
Comparative Analysis of Preparation Methods
Table 2: Performance Metrics of this compound Synthesis Methods
*Purity reflects dithis compound content in crude product.
Batch methods excel in simplicity but suffer from high energy use and byproduct formation. Continuous systems optimize productivity but require capital-intensive infrastructure. Solid catalysts balance environmental and economic factors, albeit with moderate activity.
Industrial-Scale Production Considerations
Scaling this compound synthesis necessitates addressing methanol recovery, waste management, and catalyst longevity. Patent CN102442905A highlights the use of multi-stage distillation to reclaim methanol, reducing raw material costs by 30%. Furthermore, process intensification via reactive distillation columns integrates reaction and separation, cutting operational expenses by 20% compared to conventional setups .
Analyse Des Réactions Chimiques
Hydrolysis
DMA undergoes hydrolysis under acidic or basic conditions to yield adipic acid and methanol. This reaction is pivotal in recycling processes and environmental degradation studies.
Reagents/Conditions:
Industrial Example:
A patent (CN111320543A) describes hydrolysis during esterification at 120°C under methanol-saturated vapor pressure, achieving >97% adipic acid conversion .
Condition | Acidic (H₂SO₄) | Basic (NaOH) |
---|---|---|
Temperature (°C) | 90–100 | 70–100 |
Reaction Time (h) | 1–4 | 2–6 |
Conversion (%) | >95 | >97 |
Oxidation
DMA oxidizes to adipic acid under strong oxidizing conditions, a pathway relevant to nylon precursor synthesis.
Reagents/Conditions:
Key Data:
Ammonolysis
Reaction with concentrated ammonia produces adipamide, a polymer intermediate.
Reagents/Conditions:
Reaction:
(CH2)4(COOCH3)2+2NH3→(CH2)4(CONH2)2+2CH3OH
Hydrogenation
Catalytic hydrogenation converts DMA to 1,6-hexanediol (1,6-HDO), a key monomer for polyesters and polyurethanes.
Reagents/Conditions:
Performance Data:
Catalyst | 1,6-HDO Yield (%) | Byproducts |
---|---|---|
Rh-Sn/α-Al₂O₃ | 70–80 | 6-Hydroxyhexyl this compound (intermediate) |
Ru-Sn/TiO₂ | 60–70 | Cyclic ethers |
Mechanism:
Ester-Exchange Reactions
DMA participates in transesterification with alcohols or diols, enabling tailored ester synthesis.
Example:
-
Reaction with 1,6-HDO under hydrogenation conditions forms mixed esters (e.g., 6-hydroxyhexyl this compound) .
Enzymatic Reactions
Lipases catalyze DMA synthesis and degradation, offering green chemistry pathways.
Key Study:
Applications De Recherche Scientifique
Methyl adipate is widely used in scientific research due to its versatility :
Chemistry: It serves as a building block in organic synthesis and is used to create more complex molecules.
Biology: It is used in the study of metabolic pathways and enzyme reactions.
Medicine: Research into its potential therapeutic effects and its role in drug synthesis is ongoing.
Mécanisme D'action
The mechanism of action of Methyl adipate involves its interaction with various molecular targets and pathways. It can act as a substrate for enzymes, participating in metabolic reactions that lead to the formation of different products. The exact pathways and targets depend on the specific application and conditions .
Comparaison Avec Des Composés Similaires
Structural and Functional Differences
Table 1: Structural Comparison of Adipate Esters
Key Findings :
- Methyl vs. Dithis compound: this compound’s monoester structure (C₇H₁₂O₄) provides higher polarity compared to dithis compound (C₈H₁₄O₄), making it less volatile but more reactive in ester-exchange reactions . Dithis compound is a key precursor in DOA synthesis, where titanium adipate catalysts optimize yields .
- Plasticizer Performance: Butyl phenoxyethyl adipate exhibits superior thermal stability (glass-transition temperature reduction of 132.2°C vs. PVC) compared to dioctyl phthalate (DOP) and DOA . Butoxyethyl adipates (e.g., butyl butoxyethyl adipate) show comparable melt fluidity to DOA in PVC composites, enhancing processing efficiency .
- Biodegradability: Poly(butylene adipate)-based copolymers are enzymatically degradable due to their ester backbone, unlike non-adipate polyesters like PLA .
Thermal and Physical Properties
Table 2: Thermal and Functional Properties
Key Findings :
- Thermal Stability: Branched adipates like butyl phenoxyethyl adipate outperform linear esters (e.g., DOA) in thermal resistance, critical for high-temperature PVC processing .
- Polymer Modifications : Incorporating methyl glycolate into poly(butylene adipate/terephthalate) (PBAT) increases tensile strength (25 mol% GA units) and crystallization temperature .
Environmental and Industrial Relevance
- Sustainability: Bulk synthesis of poly(butylene adipate)-co-(dilinoleic adipate) (PBA-DLA) reduces reliance on diphenyl ether, lowering environmental impact .
Q & A
Basic Research Questions
Q. How can methyl adipate be reliably quantified in complex environmental or biological matrices?
- Methodological Answer : Use liquid/liquid or liquid/solid extraction followed by gas chromatography-mass spectrometry (GC-MS) or liquid chromatography-tandem mass spectrometry (LC-MS/MS). For environmental samples, EPA Method 506 provides a validated protocol for adipate ester analysis, with detection limits of ~0.1–1 µg/mL depending on the matrix . In lipidomics studies, untargeted LC-MS with multivariate analysis (e.g., PCA) can resolve this compound from co-eluting lipids . GC-MS parameters optimized for methyl esters (e.g., column: DB-5MS; ionization: EI at 70 eV) yield reproducible quantification, as demonstrated in fungal metabolite studies .
Q. What spectroscopic techniques are most effective for structural confirmation of this compound and its derivatives?
- Methodological Answer : Combine ¹H NMR and ¹³C NMR to identify ester carbonyl signals (δ ~170–175 ppm) and methyl ester protons (δ ~3.6 ppm). For isomers (e.g., dimethyl 3,4-di(p-anisyl)adipate), 2D NMR techniques like HETCOR are critical to differentiate substitution patterns . Infrared spectroscopy (IR) can corroborate ester C=O stretches (~1740 cm⁻¹) and methyl C-H bending (~1450 cm⁻¹) .
Advanced Research Questions
Q. How can researchers resolve isomeric impurities in synthetic this compound derivatives?
- Methodological Answer : Employ silica-gel column chromatography with gradient elution (e.g., hexane/ethyl acetate) to separate diastereomers or regioisomers, as shown in cathodic reduction products of methyl cinnamate derivatives . Confirm purity via high-resolution mass spectrometry (HRMS) and 2D NMR. For epoxy-functionalized analogs (e.g., bis(3,4-epoxycyclohexylmethyl) adipate), monitor reaction progress using thin-layer chromatography (TLC) with iodine staining .
Q. What experimental designs are optimal for studying this compound’s role in polymer biodegradation?
- Methodological Answer : Use soil or marine sediment microcosms spiked with isotopically labeled this compound (e.g., ¹³C-labeled) to track mineralization rates via respirometry. For poly(butylene adipate-co-terephthalate) (PBAT) blends, monitor esterase activity and matrix degradation using gel permeation chromatography (GPC) and Fourier-transform infrared spectroscopy (FTIR) . Include negative controls with non-biodegradable polymers (e.g., polyethylene) to validate specificity.
Q. How do conflicting toxicological data for adipate esters inform risk assessment frameworks?
- Methodological Answer : Address contradictions by replicating carcinogenicity studies under standardized protocols. For example, di(2-ethylhexyl) adipate (DEHA) induced liver tumors in mice but not rats, suggesting species-specific metabolic activation . Use in vitro models (e.g., human hepatocyte cultures) to compare cytochrome P450-mediated oxidation pathways. Prioritize dose-response studies with endpoints like oxidative stress biomarkers (e.g., glutathione depletion) .
Propriétés
Formule moléculaire |
C7H11O4- |
---|---|
Poids moléculaire |
159.16 g/mol |
Nom IUPAC |
6-methoxy-6-oxohexanoate |
InChI |
InChI=1S/C7H12O4/c1-11-7(10)5-3-2-4-6(8)9/h2-5H2,1H3,(H,8,9)/p-1 |
Clé InChI |
UOBSVARXACCLLH-UHFFFAOYSA-M |
SMILES canonique |
COC(=O)CCCCC(=O)[O-] |
Origine du produit |
United States |
Avertissement et informations sur les produits de recherche in vitro
Veuillez noter que tous les articles et informations sur les produits présentés sur BenchChem sont destinés uniquement à des fins informatives. Les produits disponibles à l'achat sur BenchChem sont spécifiquement conçus pour des études in vitro, qui sont réalisées en dehors des organismes vivants. Les études in vitro, dérivées du terme latin "in verre", impliquent des expériences réalisées dans des environnements de laboratoire contrôlés à l'aide de cellules ou de tissus. Il est important de noter que ces produits ne sont pas classés comme médicaments et n'ont pas reçu l'approbation de la FDA pour la prévention, le traitement ou la guérison de toute condition médicale, affection ou maladie. Nous devons souligner que toute forme d'introduction corporelle de ces produits chez les humains ou les animaux est strictement interdite par la loi. Il est essentiel de respecter ces directives pour assurer la conformité aux normes légales et éthiques en matière de recherche et d'expérimentation.