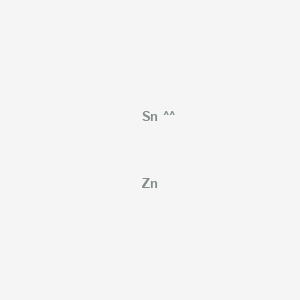
Tin-ZINC
- Cliquez sur DEMANDE RAPIDE pour recevoir un devis de notre équipe d'experts.
- Avec des produits de qualité à un prix COMPÉTITIF, vous pouvez vous concentrer davantage sur votre recherche.
Vue d'ensemble
Description
Zinc oxide (ZnO) is a versatile inorganic compound with the chemical formula ZnO, widely utilized in industries ranging from electronics to pharmaceuticals. It exists in two primary forms: crystalline (hexagonal wurtzite or cubic zinc blende structures) and amorphous. ZnO exhibits unique properties such as a wide bandgap (~3.3 eV), high electron mobility, and strong photocatalytic activity, making it suitable for applications like UV-blocking agents in sunscreens, gas sensors, and photocatalysts for environmental remediation . Recent advancements have focused on its nano-scale form, where ZnO nanoparticles (NPs) demonstrate enhanced surface reactivity and quantum effects compared to bulk ZnO .
Applications De Recherche Scientifique
Soldering Applications
Tin-Zinc Solders:
this compound solders are widely used in soldering applications due to their low melting point (around 390°F or 199°C) and excellent corrosion resistance. These solders are particularly beneficial for joining metals that are sensitive to heat, such as aluminum and copper. They are effective in both electronic component repairs and structural applications where precision is critical .
Key Benefits:
- Lower Operating Temperatures: this compound solders can operate at lower temperatures compared to traditional lead-tin solders, reducing the risk of thermal damage to components.
- Corrosion Resistance: The inherent corrosion resistance of this compound alloys makes them suitable for outdoor and harsh environments .
- High Tensile Strength: These solders provide strong joints, essential for maintaining the integrity of electronic components .
Case Study 1: Electronic Assemblies
A study conducted by Nihon Superior Co., Ltd. highlighted the potential of this compound eutectic alloys as lead-free solder alternatives in electronic assemblies. The research focused on mechanical properties and interfacial characteristics with copper substrates, demonstrating reduced formation of intermetallic compounds compared to other solder types .
Case Study 2: Automotive Industry
In automotive applications, this compound alloys are utilized for coating components exposed to corrosive environments, such as undercarriages and exhaust systems. Their ability to withstand harsh conditions while providing a protective layer has led to increased adoption in this sector .
Health Considerations
Research has also investigated the interactions between dietary tin and zinc in humans, revealing that high levels of dietary tin may inhibit zinc absorption. This aspect is crucial for understanding the broader implications of this compound usage beyond industrial applications .
Analyse Des Réactions Chimiques
Reactivity and Displacement Reactions
Zinc (Zn) displaces tin (Sn) from its compounds due to its higher reactivity, as shown in the tin hedgehog experiment where Zn pellets react with tin(II) chloride (\ceSnCl2
):
\ceSnCl2(aq)+Zn(s)−>ZnCl2(aq)+Sn(s)
This reaction produces dendritic tin crystals ("hedgehog" morphology) and zinc chloride . Concurrently, acidic conditions (\ceHCl
) in the solution generate hydrogen gas:
\ceZn(s)+2HCl(aq)−>H2(g)+ZnCl2(aq) .
Reactivity Series Comparison
Metal | Reactivity Ranking |
---|---|
Zn | Higher |
Sn | Lower |
Oxidation States
-
Tin : Common oxidation states are +2 (\ceSn2+
) and +4 (\ceSn4+
) . -
Zinc : Exhibits a +2 oxidation state (\ceZn2+
) in compounds .
Redox Reactions
-
\ceSn4+
is reduced to \ceSn2+
by Fe or Al in \ceHCl
:
\ceFe(s)+[SnCl6]2−(aq)−>Fe2+(aq)+[SnCl4]2−(aq)+2Cl−(aq) . -
\ceSn2+
acts as a reducing agent, converting \ceHgCl2
to \ceHg2Cl2
or metallic Hg .
Eutectic Composition
The Sn-Zn eutectic (91.5% Sn, 8.5% Zn) melts at 196.5°C, resembling the Sn-Pb phase diagram . Microalloying with Mn (ppm levels) suppresses Sn dendrite formation and enhances corrosion resistance .
Optimal Alloy Performance
Property | Sn-Zn-Mn Alloy (20–25% Zn) | Pure Sn |
---|---|---|
Corrosion Current | Minimal | Higher |
Intermetallic Layer | ~2.5 µm (Cu substrate) | ~5 µm |
Electrochemical Behavior
In 3% NaCl solution, Sn-Zn alloys (20–25% Zn) exhibit minimal corrosion current (Icorr
) due to passivation .
Accelerated Corrosion Tests
Test | Coating Performance (Hours to Failure) |
---|---|
ASTM B117 (Salt Fog) | 1,200+ |
Prohesion® | 800+ |
Industrial Uses
-
Soldering : Sn-Zn eutectic alloys are Pb-free alternatives with comparable wetting properties to Sn-Pb .
-
Plating : Sn-Zn coatings (20–25% Zn) resist SO₂ corrosion better than pure Zn .
-
Organometallics : Reagent-grade Zn/Sn enable syntheses of organotin (e.g., \ceR4Sn
) and organozinc compounds for pharmaceuticals .
Hazardous Incompatibilities
Material | Reaction with Zn/Sn |
---|---|
Strong acids (HCl) | \ceH2 |
gas release | |
Halogens (Cl₂) | Violent oxidation |
Q & A
Q. What analytical techniques are essential for characterizing the physicochemical properties of Tin-Zinc alloys?
Classification: Basic
Answer: Key techniques include X-ray diffraction (XRD) for crystallographic analysis, scanning electron microscopy with energy-dispersive X-ray spectroscopy (SEM-EDS) for elemental mapping, and electrochemical impedance spectroscopy (EIS) for corrosion behavior. Ensure calibration against standard reference materials and replicate measurements to minimize instrumental errors. For phase identification, pair XRD with differential scanning calorimetry (DSC) to correlate structural and thermal properties .
Q. How should researchers design experiments to evaluate the corrosion resistance of this compound coatings under simulated environmental conditions?
Classification: Advanced
Answer: Use a factorial design to test variables such as pH, humidity, and saline concentration. Include control samples (e.g., pure Tin or Zinc coatings) and replicate experiments ≥3 times. Employ electrochemical methods like potentiodynamic polarization and salt spray testing. Validate results with surface characterization (SEM-EDS) to correlate corrosion rates with microstructural changes .
Q. What computational tools are suitable for modeling the electronic structure of this compound intermetallic compounds?
Classification: Advanced
Answer: Density functional theory (DFT) simulations using software like VASP or Gaussian can predict band structures and bonding interactions. For docking studies, leverage ZINC database (http://zinc.docking.org ) to access 3D compound libraries and AutoDock Vina for binding affinity calculations. Validate computational predictions with experimental XRD and X-ray photoelectron spectroscopy (XPS) data .
Q. How can contradictions in electrochemical data from this compound studies be resolved?
Classification: Advanced
Answer: Conduct sensitivity analyses to identify outlier variables (e.g., electrolyte composition, scan rate). Use meta-analysis frameworks (Cochrane guidelines) to systematically compare datasets. Apply multivariate regression to isolate confounding factors, and verify reproducibility via inter-laboratory collaborations .
Q. What protocols ensure reproducibility in synthesizing this compound nanomaterials?
Classification: Basic
Answer: Standardize precursor ratios (e.g., Sn:Zn molar ratios) and reaction conditions (temperature, pH, stirring rate). Document synthesis steps in detail, including inert atmosphere requirements for oxidation-sensitive alloys. Characterize products with transmission electron microscopy (TEM) and dynamic light scattering (DLS) for size distribution .
Q. How to systematically review literature on this compound applications in energy storage?
Classification: Advanced
Answer: Use databases like PubMed and Web of Science with Boolean queries (e.g., "(this compound OR Sn-Zn) AND (battery OR supercapacitor)"). Follow PRISMA guidelines for screening and inclusion criteria. Extract data on capacity retention and cycle life, and assess bias using tools like ROBINS-I .
Q. What criteria guide the selection of this compound ratios for optimizing mechanical strength?
Classification: Basic
Answer: Refer to phase diagrams (e.g., Sn-Zn binary system) to identify eutectic points. Test tensile strength and hardness via nanoindentation for varying compositions (e.g., 10–90% Zn). Use finite element analysis (FEA) to simulate stress distribution and validate with experimental fracture toughness data .
Q. How can the ZINC database enhance virtual screening for Zinc-containing compounds?
Classification: Basic
Answer: Filter ZINC by molecular weight (150–500 Da), logP (-2–5), and Lipinski’s Rule of Five compliance. Use substructure searches to identify this compound coordination complexes. Download ready-to-dock 3D structures in .mol2 format and validate with molecular dynamics (MD) simulations .
Q. What spectroscopic methods detect trace impurities in this compound alloys?
Classification: Basic
Answer: Inductively coupled plasma mass spectrometry (ICP-MS) quantifies trace metal contaminants (e.g., Pb, Cu). Pair with glow discharge optical emission spectroscopy (GD-OES) for depth profiling. For organic impurities, use Fourier-transform infrared spectroscopy (FTIR) with attenuated total reflectance (ATR) mode .
Q. How to address ethical considerations in human exposure studies involving this compound nanoparticles?
Classification: Advanced
Answer: Adopt FINER criteria (Feasible, Interesting, Novel, Ethical, Relevant) during study design. Obtain IRB approval for cytotoxicity assays (e.g., MTT on human cell lines). Include data anonymization protocols and disclose conflict of interests in publications. Reference ATSDR guidelines for zinc toxicity thresholds .
Comparaison Avec Des Composés Similaires
Zinc Oxide (ZnO) vs. Titanium Dioxide (TiO₂) Nanoparticles
Property | ZnO Nanoparticles | TiO₂ Nanoparticles |
---|---|---|
Bandgap (eV) | ~3.3 | ~3.2 (anatase), ~3.0 (rutile) |
Photocatalytic Activity | Effective under UV light; limited visible-light response | Broader UV absorption; often doped for visible-light activation |
Applications | Sunscreens, antibacterial coatings, sensors | Paints, self-cleaning surfaces, solar cells |
Toxicity Concerns | Cytotoxic at high concentrations | Lower cytotoxicity but potential environmental persistence |
Research highlights that ZnO NPs exhibit superior antibacterial properties compared to TiO₂, particularly against E. coli and S. aureus, due to reactive oxygen species (ROS) generation . However, TiO₂ NPs are preferred in photovoltaics for their stability and efficiency .
Zinc Oxide vs. Zinc Sulfide (ZnS)
ZnS, another II-VI semiconductor, has a wider bandgap (~3.7 eV) and is renowned for its mechanoluminescence (ML). Doped ZnS (e.g., Mn²⁺ or Cu⁺) emits light under mechanical stress, enabling applications in stress sensors and safety systems . In contrast, ZnO’s piezoelectric properties make it ideal for flexible electronics. Recent studies show ZnS-based materials achieve 550+ charge-discharge cycles in zinc-air batteries, outperforming ZnO in energy density .
Zinc Oxide vs. Zinc Aluminate (ZnAl₂O₄)
ZnAl₂O₄, a spinel-structured material, offers high thermal stability (>1000°C) and catalytic efficiency. While ZnO is used in gas sensing, ZnAl₂O₄ excels in catalytic oxidation reactions, such as converting methane to syngas. Cr³⁺-doped ZnAl₂O₄ exhibits tunable ML properties, with a 0.70 V overpotential gap in oxygen evolution reactions (OER), surpassing ZnO’s performance in electrocatalysis .
Zinc Oxide vs. Zinc Carbonate (ZnCO₃)
Zinc carbonate and its derivatives (e.g., hydrozincite) are critical in corrosion inhibition and as precursors for ZnO synthesis. ZnCO₃ decomposes at ~300°C to yield ZnO, making it a cost-effective raw material. However, ZnCO₃ lacks ZnO’s semiconductor properties, limiting its use in electronics .
Zinc Oxide vs. Zinc Dicyanimide (Zn[C₂N₃]₂)
Zinc dicyanimide (CAS 18622-28-1) is a coordination polymer with applications in energy storage. Its unique structure ([Zn⁺²] linked by dicyanimide ligands) enables high ionic conductivity, though it lacks the photocatalytic activity of ZnO.
Méthodes De Préparation
Solution-Based Synthesis of Tin-Zinc Oxides
Aqueous Chemical Growth (ACG) for Nanostructures
Aqueous chemical growth (ACG) enables the fabrication of tin oxide (SnO₂) and zinc oxide (ZnO) nanostructures, such as nanowires and microrods, through controlled hydrolysis and condensation reactions. A representative protocol involves dissolving tin tetrachloride pentahydrate (SnCl₄·5H₂O) and urea (NH₂CONH₂) in MilliQ water, followed by hydrochloric acid addition to adjust pH . Substrates like Si/SiO₂ wafers are immersed in the solution and heated at 95°C for 5–9 hours, yielding nanowires with diameters of 10–20 nm . The growth rate approximates 1 µm per hour, with post-synthesis annealing at 800°C enhancing crystallinity .
Reaction Mechanism
Hydrolysis of tin precursors proceeds via:
SnCl4+4H2O→Sn(OH)4+4HCl
Urea decomposition facilitates gradual pH increase, promoting condensation:
NH2CONH2+H2O→2NH3+CO2
Ammonia generation drives hydroxylation, forming SnO₂ nuclei that elongate into nanowires under hydrothermal conditions .
Sol-Gel Synthesis of Heterometallic Oxides
Sol-gel methods produce homogeneous Zn-Sn-O films for solar cell applications. Zinc methoxy-ethoxide (Zn(moe)₂) and tin tert-butoxide (Sn(OtBu)₄) are reacted in toluene to form a heterometallic alkoxide precursor . Spin-coating the solution onto substrates, followed by annealing in humidified argon, yields films with reduced carbon impurities, as confirmed by thermogravimetric analysis (TGA) . X-ray diffraction (XRD) reveals coexisting ZnO and Zn₂SnO₄ phases, critical for electron transport in photovoltaic devices .
Condensation Pathways
Olation and oxolation govern gel formation:
M-OH+M-OR→M-O-M+ROH(Olation)
M-OH+M-OH→M-O-M+H2O(Oxolation)
Polymeric gels dominate when hydrolysis outpaces condensation, whereas particulate gels form under rapid condensation .
Electrodeposition of this compound Alloys
Cyanide-Free Alkaline Baths
Electrodeposition utilizing stannate-zincate electrolytes produces Sn-Zn alloys with compositions tunable via current density and pH. A rotating-cathode cell with a stainless steel cathode (40.32 cm²) and Sn-Zn alloy anode (78% Sn, 22% Zn) operates at 0.3–2.0 A/dm² . Bath compositions and resulting alloy properties are summarized below:
Current Density (A/dm²) | Sn in Deposit (%) | Zn in Deposit (%) | Deposit Appearance |
---|---|---|---|
0.745 | 22 | 78 | Whitish |
1.244 | 72 | 28 | Greyish white |
2.488 | 60 | 40 | Whitish |
4.900 | 58 | 42 | Whitish |
Data adapted from Syama et al. (1945) .
Polarization of tin anodes ensures stannate (SnO₃²⁻) formation, while zinc dissolves as zincate (Zn(OH)₄²⁻) . Higher current densities favor zinc deposition due to its lower reduction potential .
Acidic Chloride Electrolytes
Alternative baths using SnCl₂ and ZnCl₂ in hydrochloric acid achieve 85–92% Sn alloys. Additives like gelatin suppress dendritic growth, enabling smooth coatings for corrosion protection . Cathodic efficiency exceeds 90% at pH 1.5–2.5, with deposition potentials ranging from -0.65 to -0.85 V vs. SCE .
Solution-Liquid-Solid (SLS) Synthesis of Zinc Tin Phosphide
Zinc tin phosphide (ZnSnP₂) nanowires, a promising solar absorber, are synthesized via SLS using metallic Zn and Sn in trioctylphosphine (TOP) . At 345°C, TOP decomposition releases phosphorus, reacting with molten Zn-Sn droplets to form nanowires . Post-synthesis annealing eliminates binary phosphides (e.g., Zn₃P₂), while nitric acid etching removes residual Sn . Diffuse reflectance spectroscopy confirms a direct bandgap of 1.24 eV, ideal for photoelectrochemical applications .
Thermal Processing of this compound Alloys
Sweating Furnace Techniques
Secondary zinc recovery employs sweating furnaces to separate Zn-Sn alloys from scrap. Heating to 364°C melts zinc (melting point: 419.5°C), leaving higher-melting-point contaminants (e.g., Fe, Cu) as residue . The molten zinc is cast into slabs, achieving 95–98% purity after flux refining .
Powder Metallurgy
Pre-alloyed Sn-Zn powders (e.g., 91% Sn, 9% Zn) are compacted and sintered at 197°C to produce bearings and radiation shields . Homogenization at 250°C for 2 hours ensures uniform microstructure, with density measurements confirming 7.27 g/cm³ .
Comparative Analysis of Methods
Method | Advantages | Limitations | Typical Applications |
---|---|---|---|
ACG | Low-temperature, scalable | Limited to oxide forms | Gas sensors, photovoltaics |
Electrodeposition | Composition control, high throughput | Cyanide baths require waste management | Corrosion-resistant coatings |
SLS | Phase-pure nanowires | High phosphorus toxicity | Solar cells |
Thermal Processing | High purity, industrial scalability | Energy-intensive | Alloy production |
Propriétés
Numéro CAS |
51184-11-3 |
---|---|
Formule moléculaire |
SnZn |
Poids moléculaire |
184.1 g/mol |
Nom IUPAC |
tin;zinc |
InChI |
InChI=1S/Sn.Zn |
Clé InChI |
GZCWPZJOEIAXRU-UHFFFAOYSA-N |
SMILES canonique |
[Zn].[Sn] |
Origine du produit |
United States |
Avertissement et informations sur les produits de recherche in vitro
Veuillez noter que tous les articles et informations sur les produits présentés sur BenchChem sont destinés uniquement à des fins informatives. Les produits disponibles à l'achat sur BenchChem sont spécifiquement conçus pour des études in vitro, qui sont réalisées en dehors des organismes vivants. Les études in vitro, dérivées du terme latin "in verre", impliquent des expériences réalisées dans des environnements de laboratoire contrôlés à l'aide de cellules ou de tissus. Il est important de noter que ces produits ne sont pas classés comme médicaments et n'ont pas reçu l'approbation de la FDA pour la prévention, le traitement ou la guérison de toute condition médicale, affection ou maladie. Nous devons souligner que toute forme d'introduction corporelle de ces produits chez les humains ou les animaux est strictement interdite par la loi. Il est essentiel de respecter ces directives pour assurer la conformité aux normes légales et éthiques en matière de recherche et d'expérimentation.