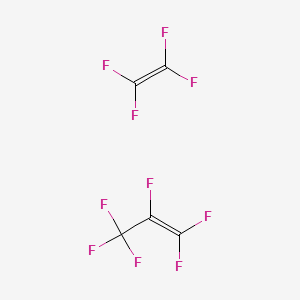
Hfp tfe
Vue d'ensemble
Description
Hfp tfe is a useful research compound. Its molecular formula is C5F10 and its molecular weight is 250.04 g/mol. The purity is usually 95%.
BenchChem offers high-quality this compound suitable for many research applications. Different packaging options are available to accommodate customers' requirements. Please inquire for more information about this compound including the price, delivery time, and more detailed information at info@benchchem.com.
Propriétés
Numéro CAS |
25067-11-2 |
---|---|
Formule moléculaire |
C5F10 |
Poids moléculaire |
250.04 g/mol |
Nom IUPAC |
1,1,2,3,3,3-hexafluoroprop-1-ene;1,1,2,2-tetrafluoroethene |
InChI |
InChI=1S/C3F6.C2F4/c4-1(2(5)6)3(7,8)9;3-1(4)2(5)6 |
Clé InChI |
PEVRKKOYEFPFMN-UHFFFAOYSA-N |
SMILES canonique |
C(=C(F)F)(C(F)(F)F)F.C(=C(F)F)(F)F |
Numéros CAS associés |
25067-11-2 |
Origine du produit |
United States |
Synthesis routes and methods I
Procedure details
Synthesis routes and methods II
Procedure details
Synthesis routes and methods III
Procedure details
Synthesis routes and methods IV
Procedure details
Avertissement et informations sur les produits de recherche in vitro
Veuillez noter que tous les articles et informations sur les produits présentés sur BenchChem sont destinés uniquement à des fins informatives. Les produits disponibles à l'achat sur BenchChem sont spécifiquement conçus pour des études in vitro, qui sont réalisées en dehors des organismes vivants. Les études in vitro, dérivées du terme latin "in verre", impliquent des expériences réalisées dans des environnements de laboratoire contrôlés à l'aide de cellules ou de tissus. Il est important de noter que ces produits ne sont pas classés comme médicaments et n'ont pas reçu l'approbation de la FDA pour la prévention, le traitement ou la guérison de toute condition médicale, affection ou maladie. Nous devons souligner que toute forme d'introduction corporelle de ces produits chez les humains ou les animaux est strictement interdite par la loi. Il est essentiel de respecter ces directives pour assurer la conformité aux normes légales et éthiques en matière de recherche et d'expérimentation.