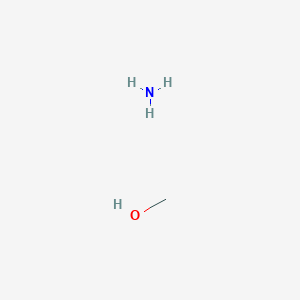
Ammonia methanol
Vue d'ensemble
Description
Ammonia (NH₃) and methanol (CH₃OH) are pivotal industrial chemicals with diverse applications. Ammonia is critical for fertilizer production and emerging as a hydrogen carrier, while methanol serves as a fuel additive, solvent, and precursor for formaldehyde and plastics. Both compounds are integral to decarbonization strategies but differ significantly in properties, production methods, and environmental impacts .
Méthodes De Préparation
Synthetic Routes and Reaction Conditions: Ammonia is typically produced through the Haber-Bosch process, which involves the reaction of nitrogen and hydrogen gases under high pressure and temperature in the presence of a catalyst . Methanol is produced from synthesis gas (a mixture of carbon monoxide, carbon dioxide, and hydrogen) using a catalyst under high pressure and temperature .
Industrial Production Methods: Industrial production of ammonia involves compressing syngas to a high pressure and then reacting it with hydrogen in the presence of a catalyst . Methanol production involves the catalytic conversion of synthesis gas at high pressure and temperature . Both processes are energy-intensive and require significant infrastructure.
Analyse Des Réactions Chimiques
Types of Reactions: Ammonia methanol undergoes various chemical reactions, including oxidation, reduction, and substitution reactions. For example, in combustion reactions, ammonia and methanol can react with oxygen to produce nitrogen, carbon dioxide, and water .
Common Reagents and Conditions: Common reagents used in reactions involving this compound include oxygen, hydrogen, and various catalysts. Reaction conditions typically involve high temperatures and pressures to facilitate the desired chemical transformations .
Major Products Formed: The major products formed from the reactions of this compound include nitrogen, carbon dioxide, and water. In some cases, other products such as nitrogen oxides (NOx) may also be formed, depending on the specific reaction conditions .
Applications De Recherche Scientifique
Combustion and Emission Characteristics
Ammonia-Methanol as a Fuel:
Research indicates that ammonia-methanol blends can significantly enhance combustion efficiency while reducing greenhouse gas emissions. For instance, a study demonstrated that the addition of methanol to ammonia improves the reactivity of the fuel mixture, leading to a reduction in ignition delay time by over 60% when 5% methanol is added . This characteristic is particularly beneficial in spark ignition engines, where the use of ammonia-methanol solutions has shown increased thermal efficiency compared to traditional fuels like gasoline .
Emission Analysis:
While ammonia-methanol blends reduce carbon dioxide emissions, they can lead to increased nitrogen oxides (NOx) emissions. Experimental findings indicate that NOx emissions peak at certain equivalence ratios but can be managed through optimal combustion conditions . The following table summarizes key emission characteristics from various studies:
Study | Fuel Blend | CO2 Emissions | NOx Emissions | Thermal Efficiency |
---|---|---|---|---|
Xu et al. | Ammonia + Methanol (5%) | Decreased | Increased to 12,500 ppm | Higher than gasoline |
Lin et al. | Ammonia + Methanol | Reduced | Similar to methanol alone | Increased by 0.6% |
Co-Production Processes
Methanol and Ammonia Co-Production:
The co-production of methanol and ammonia is gaining traction due to its economic advantages and sustainability benefits. The IMAP™ process developed by Topsoe allows for efficient co-production, with plants like UCC Shchekinoazot producing significant quantities of both chemicals annually . This dual production approach not only optimizes resource use but also enhances overall plant efficiency.
Hydrogen Storage and Carbon Recycling
Hydrogen Carrier:
Methanol serves as an effective hydrogen carrier, facilitating easier storage and transportation compared to gaseous hydrogen. This property is crucial for integrating hydrogen into various industrial applications . The ability to convert carbon dioxide into methanol also supports carbon recycling initiatives, contributing to reduced emissions in chemical manufacturing processes.
Industrial Applications
Chemical Industry Utilization:
Ammonia-methanol blends are being explored for their roles in various chemical processes. Methanol is utilized as a solvent, reactant, or reducing agent in the production of plastics and other chemicals . Additionally, the agricultural sector benefits from methanol's application in pesticides and fertilizers, promoting sustainable farming practices .
Case Studies
Case Study: GNFC Bharuch Plant Upgrade
The Gujarat Narmada Valley Fertilizers & Chemicals (GNFC) plant underwent significant upgrades that enhanced its methanol production capacity from 60 MTPD to 160 MTPD through strategic modifications . These changes included improved gas cooling circuits and synthesis gas generation units, demonstrating the potential for existing facilities to adapt for increased efficiency.
Case Study: Conversion of Ammonia Plants
Another study highlighted the conversion of traditional ammonia plants into methanol production facilities. This approach allows for utilizing existing infrastructure while reducing costs associated with new plant construction—estimated at one-third less expensive than building new facilities .
Mécanisme D'action
The mechanism of action of ammonia methanol involves its combustion characteristics. When used as a fuel, this compound undergoes combustion reactions that release energy. The molecular targets and pathways involved in these reactions include the breaking and forming of chemical bonds between nitrogen, hydrogen, carbon, and oxygen atoms . The specific mechanism depends on the reaction conditions and the presence of catalysts .
Comparaison Avec Des Composés Similaires
Physicochemical Properties Comparison
Key physicochemical properties influence their industrial applicability:
Ammonia’s low energy density and toxicity limit its direct use in fuel cells, whereas methanol’s higher volatility and flammability require careful handling .
Environmental Impact and Emissions
- Production Emissions: Traditional ammonia production emits ~0.5 Gt CO₂-eq/year, while methanol contributes ~0.3 Gt CO₂-eq/year. Green ammonia (wind-powered electrolysis) and methanol (CO₂ capture) reduce emissions by 60–70% but require policy support for scalability .
- Combustion Byproducts: Ammonia combustion releases trace N₂O and NOx, undermining its "zero-carbon" claims. Methanol combustion produces CO₂ but fewer particulates than diesel .
Production Methods and Sustainability
- Ammonia :
Dominated by the Haber–Bosch process (natural gas-based). Green routes (e.g., electrolysis) are cost-competitive during energy crises but face scalability challenges . - Methanol: Produced via syngas (CO + H₂). Emerging methods utilize CO₂ hydrogenation, reducing reliance on fossil fuels .
Economic Viability and Market Trends
Q & A
Basic Research Questions
Q. How can ammonia-methanol solvent systems be optimized for chromatographic separations in analytical chemistry?
- Methodological Approach : Use experimental design (e.g., D-optimal design) to evaluate solvent-additive combinations. For example, ammonia-methanol mixtures enhance ionisation efficiency in supercritical fluid chromatography (SFC) by improving desolvation and reducing fragmentation. Key variables include desolvation gas temperature (positive effect) and cone voltage (negative effect) . Adding ammonia to methanol in mobile phases (e.g., 0.1–1% v/v) improves peak resolution in HPTLC by modulating polarity and pH .
Q. What experimental strategies are effective for resolving contradictions in kinetic models for ammonia-methanol-fed microbial cultures?
- Methodological Approach : Compare model predictions (e.g., Haldane kinetics) against experimental data for biomass, PHB, and ammonia concentrations. Weighted regression can prioritize variables with larger magnitudes (e.g., biomass data), but structural model limitations may require alternative formulations. For instance, discrepancies in residual biomass predictions in Protomonas extorquens cultures were resolved by adopting a second fed-batch method with lower δ² values (0.12 vs. 0.89) .
Advanced Research Questions
Q. How do ammonia-methanol mixtures influence auto-ignition kinetics at high pressures and intermediate temperatures?
- Methodological Approach : Conduct shock-tube experiments and kinetic modeling to quantify ignition delay times. Methanol oxidation follows first-order kinetics (activation energy: ~98 kcal/mol at 480–540°C), while ammonia exhibits catalytic behavior (activation energy: ~38 kcal/mol at 640–700°C). Synergistic effects in mixtures require pressure-corrected elementary reaction models to predict formaldehyde formation and hydrogen underprediction .
Q. What computational frameworks reconcile discrepancies in supercritical water oxidation (SCWO) mechanisms for ammonia-methanol waste streams?
- Methodological Approach : Develop isothermal plug flow reactor experiments coupled with density functional theory (DFT) simulations. Methanol’s rate-limiting oxidation to CO₂ correlates with ammonia’s catalytic conversion to N₂. Validate models using high-pressure rate constants and intermediate species detection (e.g., formaldehyde) .
Q. How can soft sensors improve real-time monitoring of ammonia-methanol consumption in bioreactors?
- Methodological Approach : Train artificial neural networks (ANNs) with inputs like CO₂ evolution rate, methanol consumption, and ammonia uptake. For hepatitis B vaccine production, ANNs achieved biomass prediction errors <5% across four fed-batch cycles by correlating metabolic waste dynamics with sensor data .
Q. What role do ammonia-methanol blends play in carbon-neutral fuel synthesis?
- Methodological Approach : Integrate green hydrogen (from water electrolysis) with CO₂ capture for methanol synthesis. Blue ammonia (using CCS) and e-methanol (from renewable H₂) reduce emissions by 60–80% in life-cycle assessments. Optimize bifunctional catalysts (e.g., Cu-ZnO/Al₂O₃) for co-electrolysis of NH₃ and CH₃OH in fuel cells .
Q. Data Contradiction Analysis
Q. Why do kinetic models for ammonia inhibition in methanol-fed cultures fail to predict PHB accumulation?
- Resolution Strategy : Re-examine substrate inhibition terms in Haldane models. In Protomonas extorquens, nitrogen mass flow rate (Fₙ) and methanol-specific consumption rate (K₂) were misparameterized, leading to δ² > 0.8. Calibrate models using fed-batch phase data instead of batch-phase assumptions .
Q. How to address conflicting reports on ammonia-methanol solvent stability in long-term chromatographic storage?
- Resolution Strategy : Perform robustness testing via full factorial design. Variables like ammonia concentration (0.1–1% in methanol) and storage temperature (4–25°C) significantly impact shelf life. For LC-MS, LabReady™ blends with 0.1% NH₃ showed <2% degradation over 6 months .
Tables for Key Experimental Parameters
Propriétés
IUPAC Name |
azane;methanol | |
---|---|---|
Details | Computed by LexiChem 2.6.6 (PubChem release 2019.06.18) | |
Source | PubChem | |
URL | https://pubchem.ncbi.nlm.nih.gov | |
Description | Data deposited in or computed by PubChem | |
InChI |
InChI=1S/CH4O.H3N/c1-2;/h2H,1H3;1H3 | |
Details | Computed by InChI 1.0.5 (PubChem release 2019.06.18) | |
Source | PubChem | |
URL | https://pubchem.ncbi.nlm.nih.gov | |
Description | Data deposited in or computed by PubChem | |
InChI Key |
CBHOOMGKXCMKIR-UHFFFAOYSA-N | |
Details | Computed by InChI 1.0.5 (PubChem release 2019.06.18) | |
Source | PubChem | |
URL | https://pubchem.ncbi.nlm.nih.gov | |
Description | Data deposited in or computed by PubChem | |
Canonical SMILES |
CO.N | |
Details | Computed by OEChem 2.1.5 (PubChem release 2019.06.18) | |
Source | PubChem | |
URL | https://pubchem.ncbi.nlm.nih.gov | |
Description | Data deposited in or computed by PubChem | |
Molecular Formula |
CH7NO | |
Details | Computed by PubChem 2.1 (PubChem release 2019.06.18) | |
Source | PubChem | |
URL | https://pubchem.ncbi.nlm.nih.gov | |
Description | Data deposited in or computed by PubChem | |
Molecular Weight |
49.073 g/mol | |
Details | Computed by PubChem 2.1 (PubChem release 2021.05.07) | |
Source | PubChem | |
URL | https://pubchem.ncbi.nlm.nih.gov | |
Description | Data deposited in or computed by PubChem | |
Synthesis routes and methods I
Procedure details
Synthesis routes and methods II
Procedure details
Synthesis routes and methods III
Procedure details
Synthesis routes and methods IV
Procedure details
Synthesis routes and methods V
Procedure details
Retrosynthesis Analysis
AI-Powered Synthesis Planning: Our tool employs the Template_relevance Pistachio, Template_relevance Bkms_metabolic, Template_relevance Pistachio_ringbreaker, Template_relevance Reaxys, Template_relevance Reaxys_biocatalysis model, leveraging a vast database of chemical reactions to predict feasible synthetic routes.
One-Step Synthesis Focus: Specifically designed for one-step synthesis, it provides concise and direct routes for your target compounds, streamlining the synthesis process.
Accurate Predictions: Utilizing the extensive PISTACHIO, BKMS_METABOLIC, PISTACHIO_RINGBREAKER, REAXYS, REAXYS_BIOCATALYSIS database, our tool offers high-accuracy predictions, reflecting the latest in chemical research and data.
Strategy Settings
Precursor scoring | Relevance Heuristic |
---|---|
Min. plausibility | 0.01 |
Model | Template_relevance |
Template Set | Pistachio/Bkms_metabolic/Pistachio_ringbreaker/Reaxys/Reaxys_biocatalysis |
Top-N result to add to graph | 6 |
Feasible Synthetic Routes
Avertissement et informations sur les produits de recherche in vitro
Veuillez noter que tous les articles et informations sur les produits présentés sur BenchChem sont destinés uniquement à des fins informatives. Les produits disponibles à l'achat sur BenchChem sont spécifiquement conçus pour des études in vitro, qui sont réalisées en dehors des organismes vivants. Les études in vitro, dérivées du terme latin "in verre", impliquent des expériences réalisées dans des environnements de laboratoire contrôlés à l'aide de cellules ou de tissus. Il est important de noter que ces produits ne sont pas classés comme médicaments et n'ont pas reçu l'approbation de la FDA pour la prévention, le traitement ou la guérison de toute condition médicale, affection ou maladie. Nous devons souligner que toute forme d'introduction corporelle de ces produits chez les humains ou les animaux est strictement interdite par la loi. Il est essentiel de respecter ces directives pour assurer la conformité aux normes légales et éthiques en matière de recherche et d'expérimentation.