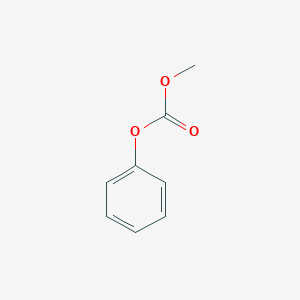
Methyl phenyl carbonate
Vue d'ensemble
Description
Methyl phenyl carbonate (MPC, C₈H₈O₃) is an organic carbonate ester with a phenyl group and a methoxy group attached to a carbonyl center. It serves as a critical intermediate in synthesizing diphenyl carbonate (DPC), a precursor for polycarbonate plastics. MPC is typically synthesized via the transesterification of dimethyl carbonate (DMC) and phenol, catalyzed by heterogeneous catalysts such as TiO₂/SiO₂ .
Key properties of MPC include:
- Standard Molar Combustion Enthalpy: -3,868.6 kJ/mol (experimentally determined via calorimetry) .
- Purity: ≥99.5% achievable through reduced-pressure distillation and sodium hydroxide washing .
- Applications: Primarily used in DPC production, which is vital for manufacturing high-performance polymers like polycarbonates .
Méthodes De Préparation
Synthetic Routes and Reaction Conditions: Methyl phenyl carbonate is typically synthesized through the reaction of methyl formate and phenol under alkaline conditions. The reaction involves mixing methyl formate and phenol, followed by heating the mixture to a temperature range of 100-120°C to facilitate the reaction .
Industrial Production Methods: In industrial settings, the production of this compound often involves the use of catalysts to enhance the reaction efficiency. The process includes steps such as distillation and crystallization to purify the final product .
Analyse Des Réactions Chimiques
Kinetics of the Reaction
The kinetics of the synthesis reaction has been studied extensively. Experiments indicate that the reaction rate is influenced by several factors:
-
Catalyst Concentration: Higher catalyst concentrations lead to increased reaction rates.
-
Temperature: The reaction typically occurs in a temperature range of 160 to 200 °C.
-
Reactant Ratio: The molar ratio of DMC to phenol affects the yield of methyl phenyl carbonate.
A study reported that at optimal conditions, the initial rate of this compound formation can be expressed as:
where is the rate constant, and and are the reaction orders with respect to DMC and phenol, respectively .
Disproportionation Reaction
This compound can undergo a disproportionation reaction to form diphenyl carbonate (DPC) and dimethyl carbonate. This step is crucial for producing high-value industrial chemicals.
Disproportionation Reaction:
This reaction is often facilitated by various catalysts, including lead-based nanocatalysts, which enhance the efficiency and selectivity of DPC formation .
Side Reactions
Side reactions can occur during the synthesis and transformation processes, leading to byproducts such as anisole, which can form from the methylation of phenol. Understanding these side reactions is essential for optimizing yields and purity in industrial applications .
Reaction Conditions and Yields
Catalyst Type | Temperature (°C) | DMC:Phenol Ratio | Yield of MPC (%) | Byproducts |
---|---|---|---|---|
Titanium Tetraphenate | 180 | 1:1 | 85 | Methanol |
Lead Nanocatalyst | 200 | 1:3 | 90 | Anisole |
Stannate Catalyst | 160 | 3:1 | 80 | Diphenyl Carbonate |
Kinetic Parameters
Parameter | Value |
---|---|
Activation Energy (kJ/mol) | 75 |
Rate Constant (k) | Varies with conditions |
Reaction Order w.r.t DMC | 1 |
Reaction Order w.r.t Phenol | 0.5 |
Applications De Recherche Scientifique
Industrial Applications
-
Synthesis of Polycarbonates :
- MPC serves as a precursor for the production of diphenyl carbonate (DPC), which is a key building block for polycarbonate plastics. The transformation of MPC to DPC is facilitated by catalytic processes, which have been optimized to improve yield and efficiency .
- Catalytic Efficiency : Research has shown that specific lead-based nanocatalysts can significantly enhance the conversion rates of MPC to DPC, with various support materials affecting catalytic performance .
- Use in Urethanes and Isocyanates :
- Perfume and Fragrance Industry :
Case Study 1: Catalytic Transformation
A study investigated the use of lead-based catalysts for the disproportionation of this compound to diphenyl carbonate. The results indicated that catalysts supported on magnesium oxide exhibited superior activity due to better metal-support interactions. This research underscores the importance of catalyst selection in maximizing product yield from MPC transformations .
Case Study 2: Perfume Composition Enhancement
Research into the use of this compound in fragrance formulations revealed its ability to impart desirable scent characteristics. Specifically, it was found that blends containing MPC could replicate floral nuances akin to rose and hyacinth, making it a valuable ingredient in high-end perfumery .
Table 1: Catalytic Performance of Different Supports for MPC Transformation
Catalyst Support | Conversion Rate (%) | Selectivity to DPC (%) | Reusability |
---|---|---|---|
MgO | 85 | 90 | High |
ZrO₂ | 80 | 88 | Moderate |
SiO₂ | 75 | 85 | Low |
Al₂O₃ | 70 | 80 | Low |
Table 2: Organoleptic Properties Contributed by this compound
Product Type | Aroma Characteristics |
---|---|
Perfumes | Floral notes (rose, hyacinth) |
Soaps | Fresh fruit undertones |
Detergents | Clean, powdery scents |
Mécanisme D'action
The mechanism of action of methyl phenyl carbonate involves its interaction with various molecular targets. It acts as a nucleophile in substitution reactions, where it donates an electron pair to form new chemical bonds. The pathways involved include nucleophilic substitution and esterification reactions .
Comparaison Avec Des Composés Similaires
Comparison with Similar Compounds
MPC belongs to the organic carbonate family, which includes compounds such as dimethyl carbonate (DMC), diphenyl carbonate (DPC), and ethyl methyl carbonate (EMC). Below is a detailed comparison:
Structural and Physical Properties
Catalytic Behavior and Reactivity
- MPC : Requires Lewis acid sites (e.g., PbO/MgO) for efficient conversion to DPC. Catalyst supports like MgO and ZrO₂ enhance Pb dispersion and stability, achieving MPC conversion rates >80% .
- DMC : Reacts via nucleophilic substitution in transesterifications; less sensitive to catalyst acidity .
- DPC : Forms via MPC disproportionation, requiring precise control of equilibrium (low K₂) and suppression of side reactions like decarboxylation .
Thermodynamic and Kinetic Insights
- MPC vs. DMC : MPC’s phenyl group increases steric hindrance, reducing reactivity compared to DMC in transesterifications .
- Acidity Dependence : MPC conversion to DPC correlates with Lewis acid site density (e.g., PbO/MgO has 0.45 mmol/g acid sites vs. 0.28 mmol/g for PbO/Al₂O₃) .
- Side Reactions : Strong acidic catalysts (e.g., PbO/Al₂O₃) promote MPC decarboxylation to anisole, reducing DPC selectivity .
Key Research Findings
Catalyst Optimization : PbO/MgO and PbO/ZrO₂ exhibit superior recyclability (>3 cycles) due to strong metal-support interactions, minimizing Pb leaching .
Acid Site Engineering : Catalysts with balanced Lewis/Brønsted acid sites (AL/AB ratio ~3.2 for PbO/ZrO₂) maximize DPC yield while minimizing byproducts .
Industrial Scalability : Continuous removal of co-produced DMC shifts equilibrium toward DPC, achieving ~90% MPC conversion in batch reactors .
Activité Biologique
Methyl phenyl carbonate (MPC) is an organic compound that has garnered attention in various fields due to its unique chemical properties and biological activities. This article explores the biological activity of MPC, focusing on its reactivity, catalytic applications, and potential therapeutic uses, supported by data tables and research findings.
MPC is synthesized primarily through the transesterification of phenol with dimethyl carbonate (DMC). This process can be catalyzed by various materials, including metal oxides and triflate catalysts. The synthesis pathway is crucial as it influences the yield and purity of the final product.
Table 1: Synthesis Conditions for this compound
Catalyst | Temperature (°C) | Reaction Time (h) | Yield (%) |
---|---|---|---|
AlSBA-15 (Si/Al = 10) | 100 | 3 | 71 |
TiO2/SiO2 | 80 | 5 | 65 |
Sc(OTf)3 | 363 | 2 | 85 |
La(OTf)3 | 363 | 2 | 78 |
Catalytic Applications
MPC has been extensively studied for its catalytic properties, particularly in carbomethoxylation reactions. It acts as a carbomethoxylating agent for aromatic amines, demonstrating significant reactivity under mild conditions. The effectiveness of MPC in these reactions is influenced by the choice of catalyst and reaction parameters.
Case Study: Carbamation of Aromatic Amines
In a study utilizing Sc(OTf)3 as a catalyst, MPC was found to selectively react with aniline and other aromatic diamines, achieving high yields. The selectivity was significantly better than that observed with DMC, indicating MPC's superior performance in these reactions .
Table 2: Reactivity of this compound with Aromatic Amines
Amines | Catalyst | Temperature (K) | Yield (%) |
---|---|---|---|
Aniline | Sc(OTf)3 | 363 | 90 |
4,4-Methylenedianiline | La(OTf)3 | 363 | 85 |
2,4-Diaminotoluene | Sc(OTf)3 | 363 | 88 |
Toxicological Studies
While MPC shows promise in various catalytic applications, its biological safety profile is essential for potential therapeutic use. Preliminary studies indicate low toxicity levels in vitro, making it a candidate for further exploration in drug development.
Case Study: In Vitro Toxicity Assessment
A toxicity assessment conducted on human cell lines showed that MPC exhibited minimal cytotoxic effects at concentrations up to 100 µM. The compound's IC50 value was determined to be significantly higher than that of many conventional solvents, suggesting a favorable safety profile .
Q & A
Q. Basic Research: What experimental methods are critical for characterizing catalysts in MPC-to-DPC transformations?
Answer:
Catalyst characterization requires a multi-technique approach to assess structural, textural, and acidic properties:
- X-ray diffraction (XRD) identifies crystalline phases and Pb dispersion on supports like MgO or ZrO₂ .
- NH₃-TPD and Py-IR quantify acid site strength/distribution (weak, medium, strong) and differentiate Lewis vs. Brønsted acidity. For example, PbO/MgO exhibits strong Lewis acidity, correlating with high DPC selectivity .
- TEM and XPS evaluate Pb nanoparticle size (e.g., <5 nm on MgO) and oxidation states, which influence catalytic activity .
- H₂-TPR measures metal-support interactions; stronger interactions in PbO/MgO/ZrO₂ enhance recyclability .
Key Data:
Catalyst | Total Acid Sites (μmol/g) | Lewis Acid Dominance (AL/AB Ratio) |
---|---|---|
PbO/MgO | 450 | 8.2 |
PbO/ZrO₂ | 320 | 5.6 |
PbO/Al₂O₃ | 280 | N/A (Lewis-only) |
Q. Advanced Research: How do support materials influence Pb catalyst stability and Pb leaching in MPC disproportionation?
Answer:
Support materials dictate Pb dispersion and metal-support bonding:
- MgO and ZrO₂ exhibit strong Pb-O interactions, minimizing Pb leaching (<1% loss after 3 cycles) due to high Pb dispersion and stable anchoring .
- SiO₂, Al₂O₃, TiO₂ show weaker interactions, leading to Pb leaching (up to 15% loss) and activity decline .
- XRD post-reaction confirms retained amorphous Pb phases on MgO/ZrO₂, while Al₂O₃-supported catalysts form Pb aggregates .
Methodological Insight:
- Use ICP-OES to quantify Pb loss during recycling.
- Optimize calcination temperature to enhance metal-support bonding without sintering Pb nanoparticles .
Q. Basic Research: What thermodynamic challenges limit MPC-to-DPC conversion efficiency?
Answer:
The equilibrium constant (K) for MPC disproportionation is small (~10⁻³–10⁻⁴), favoring reverse reactions. Strategies to shift equilibrium include:
- Excess MPC (molar ratio >2:1) to drive forward reaction .
- Reactive distillation to remove DPC and byproducts (e.g., dimethyl carbonate) .
- Low-temperature operation (e.g., 180–200°C) to minimize side reactions like MPC decarboxylation to anisole .
Key Finding:
- At 200°C, PbO/MgO achieves 92% MPC conversion vs. 65% for PbO/Al₂O₃ due to optimized acid site strength .
Q. Advanced Research: Why does excessive Lewis acidity reduce DPC selectivity despite enhancing MPC conversion?
Answer:
Strong Lewis acidity (e.g., PbO/MgO) accelerates MPC activation but also promotes decarboxylation to anisole:
- NH₃-TPD shows PbO/MgO has 70% strong acid sites vs. 40% for PbO/ZrO₂, correlating with higher anisole yields (15% vs. 5%) .
- Py-IR confirms Lewis acid dominance (AL/AB >5) in high-activity catalysts, but moderate acid strength (e.g., ZrO₂) balances conversion and selectivity .
Methodological Recommendation:
Q. Basic Research: How are acid site distributions quantified in MPC disproportionation catalysts?
Answer:
- NH₃-TPD : Measures total acid sites by ammonia desorption peaks:
- Py-IR : Differentiates Lewis (1440–1450 cm⁻¹) and Brønsted (1540–1550 cm⁻¹) sites. PbO/ZrO₂ has both types, whereas PbO/Al₂O₃ is Lewis-only .
Application Example:
- For PbO/TiO₂, NH₃-TPD reveals weak-medium acidity (total 210 μmol/g), explaining its low activity .
Q. Advanced Research: What causes activity loss in PbO/SiO₂ catalysts during MPC recycling?
Answer:
- Pb leaching : ICP-OES shows 12% Pb loss after 3 cycles due to weak Pb-SiO₂ interactions .
- Structural degradation : TEM reveals Pb nanoparticle agglomeration (from 4 nm to 15 nm) on SiO₂, reducing active surface area .
- Mitigation : Pre-treat SiO₂ with chelating agents (e.g., EDTA) to enhance Pb anchoring .
Q. Basic Research: What spectroscopic techniques validate MPC purity and reaction intermediates?
Answer:
- GC-MS : Identifies DPC (retention time: 12.3 min) and anisole (8.5 min) in product mixtures .
- ¹H NMR : Confirms MPC structure via aromatic proton signals (δ 7.3–7.5 ppm) and methyl carbonate (δ 3.8 ppm) .
- FT-IR : Detects carbonyl stretching (C=O) at 1740–1760 cm⁻¹ for MPC and DPC .
Q. Advanced Research: How do solvent systems impact MPC reaction kinetics and byproduct formation?
Answer:
- Polar aprotic solvents (e.g., DMF) stabilize transition states, increasing reaction rates but risking side reactions (e.g., hydrolysis) .
- Solvent-free systems at 200°C maximize DPC yield (88%) by minimizing dilution effects .
- Kinetic analysis : Pseudo-first-order models fit MPC conversion data (rate constant k = 0.015 min⁻¹ for PbO/MgO) .
Propriétés
IUPAC Name |
methyl phenyl carbonate | |
---|---|---|
Source | PubChem | |
URL | https://pubchem.ncbi.nlm.nih.gov | |
Description | Data deposited in or computed by PubChem | |
InChI |
InChI=1S/C8H8O3/c1-10-8(9)11-7-5-3-2-4-6-7/h2-6H,1H3 | |
Source | PubChem | |
URL | https://pubchem.ncbi.nlm.nih.gov | |
Description | Data deposited in or computed by PubChem | |
InChI Key |
XTBFPVLHGVYOQH-UHFFFAOYSA-N | |
Source | PubChem | |
URL | https://pubchem.ncbi.nlm.nih.gov | |
Description | Data deposited in or computed by PubChem | |
Canonical SMILES |
COC(=O)OC1=CC=CC=C1 | |
Source | PubChem | |
URL | https://pubchem.ncbi.nlm.nih.gov | |
Description | Data deposited in or computed by PubChem | |
Molecular Formula |
C8H8O3 | |
Source | PubChem | |
URL | https://pubchem.ncbi.nlm.nih.gov | |
Description | Data deposited in or computed by PubChem | |
DSSTOX Substance ID |
DTXSID80159247 | |
Record name | Carbonic acid, methyl phenyl ester | |
Source | EPA DSSTox | |
URL | https://comptox.epa.gov/dashboard/DTXSID80159247 | |
Description | DSSTox provides a high quality public chemistry resource for supporting improved predictive toxicology. | |
Molecular Weight |
152.15 g/mol | |
Source | PubChem | |
URL | https://pubchem.ncbi.nlm.nih.gov | |
Description | Data deposited in or computed by PubChem | |
CAS No. |
13509-27-8 | |
Record name | Carbonic acid, methyl phenyl ester | |
Source | ChemIDplus | |
URL | https://pubchem.ncbi.nlm.nih.gov/substance/?source=chemidplus&sourceid=0013509278 | |
Description | ChemIDplus is a free, web search system that provides access to the structure and nomenclature authority files used for the identification of chemical substances cited in National Library of Medicine (NLM) databases, including the TOXNET system. | |
Record name | Carbonic acid, methyl phenyl ester | |
Source | EPA DSSTox | |
URL | https://comptox.epa.gov/dashboard/DTXSID80159247 | |
Description | DSSTox provides a high quality public chemistry resource for supporting improved predictive toxicology. | |
Synthesis routes and methods I
Procedure details
Synthesis routes and methods II
Procedure details
Synthesis routes and methods III
Procedure details
Synthesis routes and methods IV
Procedure details
Retrosynthesis Analysis
AI-Powered Synthesis Planning: Our tool employs the Template_relevance Pistachio, Template_relevance Bkms_metabolic, Template_relevance Pistachio_ringbreaker, Template_relevance Reaxys, Template_relevance Reaxys_biocatalysis model, leveraging a vast database of chemical reactions to predict feasible synthetic routes.
One-Step Synthesis Focus: Specifically designed for one-step synthesis, it provides concise and direct routes for your target compounds, streamlining the synthesis process.
Accurate Predictions: Utilizing the extensive PISTACHIO, BKMS_METABOLIC, PISTACHIO_RINGBREAKER, REAXYS, REAXYS_BIOCATALYSIS database, our tool offers high-accuracy predictions, reflecting the latest in chemical research and data.
Strategy Settings
Precursor scoring | Relevance Heuristic |
---|---|
Min. plausibility | 0.01 |
Model | Template_relevance |
Template Set | Pistachio/Bkms_metabolic/Pistachio_ringbreaker/Reaxys/Reaxys_biocatalysis |
Top-N result to add to graph | 6 |
Feasible Synthetic Routes
Avertissement et informations sur les produits de recherche in vitro
Veuillez noter que tous les articles et informations sur les produits présentés sur BenchChem sont destinés uniquement à des fins informatives. Les produits disponibles à l'achat sur BenchChem sont spécifiquement conçus pour des études in vitro, qui sont réalisées en dehors des organismes vivants. Les études in vitro, dérivées du terme latin "in verre", impliquent des expériences réalisées dans des environnements de laboratoire contrôlés à l'aide de cellules ou de tissus. Il est important de noter que ces produits ne sont pas classés comme médicaments et n'ont pas reçu l'approbation de la FDA pour la prévention, le traitement ou la guérison de toute condition médicale, affection ou maladie. Nous devons souligner que toute forme d'introduction corporelle de ces produits chez les humains ou les animaux est strictement interdite par la loi. Il est essentiel de respecter ces directives pour assurer la conformité aux normes légales et éthiques en matière de recherche et d'expérimentation.