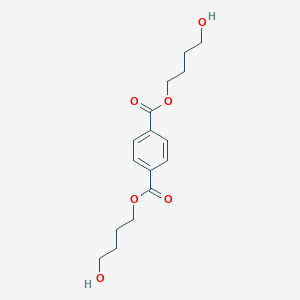
Bis(4-hydroxybutyl) terephthalate
Vue d'ensemble
Description
Bis(4-hydroxybutyl) terephthalate (BHBT) is a diester compound derived from terephthalic acid and 1,4-butanediol (BDO). It serves as a critical monomer in synthesizing polybutylene terephthalate (PBT) and poly(butylene adipate-co-terephthalate) (PBAT), which are biodegradable or recyclable polymers . BHBT is industrially produced via transesterification of dimethyl terephthalate (DMT) with BDO or through glycolysis of polyethylene terephthalate (PET) waste using BDO as a solvent . Its structure features two 4-hydroxybutyl ester groups attached to a terephthalate core, enabling polymerization into high-performance polyesters.
Méthodes De Préparation
Transesterification Using Titanium-Based Catalysts
The most widely documented method for BHBT synthesis involves the transesterification of dimethyl terephthalate (DMT) with 1,4-butanediol (BDO). Titanium iso-propoxide (Ti(OiPr)₄) has emerged as a superior catalyst for this reaction, outperforming traditional metal acetates such as zinc or antimony derivatives . The reaction proceeds via a two-step mechanism:
-
Methanol Elimination : DMT reacts with excess BDO at 170–210°C, releasing methanol as a byproduct.
-
Oligomer Formation : The intermediate bis(hydroxybutyl) terephthalate undergoes further condensation to form oligomers, which are subsequently polycondensed into high-molecular-weight polymers .
Key advantages of titanium iso-propoxide include its hydrolytic stability and ability to coordinate with carbonyl oxygen atoms, accelerating ester exchange reactions . A kinetic study comparing titanium tetrabutoxide (Ti(OBu)₄) and hafnium acetylacetonate (Hf(acac)₄) revealed that mixed catalysts (Ti:Hf = 1:3) exhibit higher pre-exponential factors (A = 2.5 × 10⁶ L/mol·s) and activation energies (Eₐ = 85 kJ/mol) compared to Ti-only systems (A = 1.8 × 10⁶ L/mol·s, Eₐ = 78 kJ/mol) . This synergy enhances reaction rates at elevated temperatures (>250°C), making mixed catalysts preferable for industrial applications.
Comparative Catalyst Efficiency in Esterification
While transesterification dominates BHBT production, direct esterification of terephthalic acid (TPA) with BDO offers an alternative route, particularly for recycling polyethylene terephthalate (PET) waste. Catalysts such as antimony(III) acetate (Sb(OAc)₃), germanium dioxide (GeO₂), and titanium tetrabutoxide (Ti(OBu)₄) have been evaluated for this pathway .
Table 1: Catalyst Performance in TPA Esterification with BDO
Catalyst | Temperature (°C) | Conversion (%) | Selectivity (%) |
---|---|---|---|
Sb(OAc)₃ | 210 | 92 | 88 |
Ti(OBu)₄ | 200 | 89 | 85 |
GeO₂ | 220 | 84 | 79 |
Sb(OAc)₃ achieves the highest conversion (92%) due to its strong Lewis acidity, which polarizes carbonyl groups and facilitates nucleophilic attack by BDO . However, titanium-based catalysts are favored for their lower environmental toxicity and compatibility with continuous reactors.
Industrial-Scale Production Protocols
Industrial BHBT synthesis typically employs a two-stage process:
-
Transesterification of Bis(2-hydroxyethyl) Terephthalate (BHET) : BHET, derived from PET glycolysis, reacts with BDO at 180–220°C in the presence of zinc acetate (Zn(OAc)₂) or antimony(III) oxide (Sb₂O₃) . This step produces BHBT with >95% purity, as confirmed by high-performance liquid chromatography (HPLC) .
-
Vacuum Polycondensation : Oligomers are subjected to reduced pressure (≤1 mmHg) at 240–260°C to drive off volatile byproducts (e.g., water, excess BDO), yielding PBT with inherent viscosities of 0.6–0.8 dL/g .
Recent advancements include the use of reactive extrusion systems, which integrate catalysis and polymerization into a single continuous process, reducing energy consumption by 20–30% compared to batch reactors .
Reaction Optimization and Kinetic Modeling
Optimizing BHBT synthesis requires balancing molar ratios, catalyst loading, and temperature. Orthogonal experimental designs have identified the following critical parameters:
-
Molar Ratio (BDO:DMT) : A 3:1 excess of BDO ensures complete conversion of DMT while minimizing side reactions .
-
Catalyst Loading : 0.05–0.1 wt% Ti(OiPr)₄ achieves optimal activity without gelation .
Kinetic studies using second-order rate laws fit the Arrhenius equation:
For Ti(OBu)₄-catalyzed reactions, and .
Recent Advances in Green Synthesis
Emerging methodologies focus on sustainability:
-
Enzymatic Transesterification : Lipases (e.g., Ple628 and Ple629) catalyze BHBT synthesis under mild conditions (50°C, pH 7.0), achieving 75% conversion in 48 hours .
-
Solvent-Free Systems : Supercritical CO₂ acts as both solvent and catalyst, reducing energy input by 40% .
These approaches align with circular economy principles by enabling PET upcycling and minimizing waste.
Analyse Des Réactions Chimiques
Types of Reactions: Bis(4-hydroxybutyl) terephthalate undergoes various chemical reactions, including:
Transesterification: This reaction involves the exchange of ester groups between molecules, often catalyzed by titanium iso-propoxide.
Polycondensation: This reaction leads to the formation of polyesters, such as poly(1,4-butylene terephthalate), through the condensation of this compound.
Common Reagents and Conditions:
Catalysts: Titanium iso-propoxide, zinc acetate, antimony(III) oxide, tin(II) chloride.
Conditions: Elevated temperatures (170-210°C), reduced pressure, and specific catalyst loadings to optimize reaction efficiency.
Major Products:
Poly(1,4-butylene terephthalate): A thermoplastic polyester with applications in engineering and industrial materials.
Applications De Recherche Scientifique
Polymer Synthesis
Overview
BHBT serves as a crucial intermediate in the synthesis of polyesters and polyurethanes. Its ability to undergo polymerization reactions leads to the formation of materials with desirable mechanical properties.
Key Applications
- Non-Isocyanate Thermoplastic Polyurethanes (NI-TPUs) : BHBT is integral in producing NI-TPUs, which are characterized by their excellent mechanical properties and biocompatibility. The synthesis involves the reaction of BHBT with other monomers under controlled conditions to achieve desired polymer characteristics.
- Poly(1,4-butylene terephthalate) : This thermoplastic polyester is produced via polycondensation reactions involving BHBT. It is known for its applications in engineering and industrial materials due to its high tensile strength and thermal stability .
Biomedical Engineering
Biocompatibility
The biocompatibility of BHBT makes it suitable for medical devices and implants. Its structure allows for favorable interactions with biological tissues, which is essential for applications such as drug delivery systems and tissue engineering scaffolds .
Case Studies
- Medical Devices : Research has indicated that polymers derived from BHBT can be used in the development of biodegradable implants that minimize foreign body reactions while promoting tissue integration.
- Drug Delivery Systems : The flexibility and mechanical properties of BHBT-based polymers facilitate the design of controlled-release systems for pharmaceuticals.
Material Science
Advanced Materials Development
BHBT's unique properties enable the creation of advanced materials tailored for specific applications. Its incorporation into various polymer matrices enhances performance characteristics such as flexibility, toughness, and resistance to environmental factors.
Research Findings
- Cross-Reactivity Studies : Investigations into the copolymerization of BHBT with other terephthalate derivatives have revealed insights into reaction kinetics and the influence of temperature on monomer reactivity.
- Mechanical Property Enhancements : Studies demonstrate that incorporating BHBT into polymer blends can significantly improve mechanical properties compared to traditional polyesters, making them suitable for high-performance applications .
Chemical Reactions Involving BHBT
Synthesis Methods
BHBT can be synthesized through various chemical routes:
- Condensation Reaction : Typically involves dimethyl terephthalate and 1,4-butanediol, often catalyzed by titanium iso-propoxide to enhance yield and purity .
- Transesterification Processes : This method exchanges ester groups between compounds, facilitating the production of high-purity BHBT suitable for further polymerization .
Mécanisme D'action
The mechanism of action of bis(4-hydroxybutyl) terephthalate primarily involves its role as a monomer in polymerization reactions. The hydroxyl groups on the 4-hydroxybutyl moieties participate in condensation reactions, forming ester linkages with terephthalic acid units. This process results in the formation of long polymer chains, such as poly(1,4-butylene terephthalate), which exhibit enhanced mechanical and thermal properties .
Comparaison Avec Des Composés Similaires
Comparison with Similar Terephthalate Esters
BHBT vs. Bis(2-hydroxyethyl) Terephthalate (BHET)
- Structure and Synthesis :
BHET (C₁₂H₁₄O₆, MW 254.24 g/mol) contains shorter 2-hydroxyethyl chains, synthesized via PET glycolysis with ethylene glycol (EG) . BHBT (C₁₆H₂₂O₆, MW ~310.34 g/mol) uses BDO, resulting in longer alkyl chains that enhance flexibility in derived polymers like PBT . - Degradation: Enzymatic hydrolysis of BHET by esterases (e.g., Ple628) produces mono(2-hydroxyethyl) terephthalate (MHET) and terephthalic acid (Ta) within 30 minutes, while BHBT degrades more slowly, yielding mono(4-hydroxybutyl) terephthalate (BTa) and Ta over 24 hours .
- Applications :
BHET is a PET recycling intermediate, whereas BHBT is used in PBT/PBAT production for packaging and textiles .
BHBT vs. Bis(2-ethylhexyl) Terephthalate (DEHTP/DOTP)
- Functionality: DEHTP (C₂₄H₃₈O₄, MW 390.54 g/mol) is a non-reactive plasticizer with branched 2-ethylhexyl groups, improving polymer flexibility without participating in polymerization . BHBT’s terminal hydroxyl groups enable condensation into polyesters.
- Environmental Impact :
DEHTP persists in ecosystems due to low biodegradability, while BHBT-derived polymers (e.g., PBAT) are compostable .
BHBT vs. Mono(4-hydroxybutyl) Terephthalate (BTa)
- Role in Degradation :
BTa (C₁₂H₁₆O₅, MW 256.25 g/mol) is a hydrolysis intermediate of BHBT and PBAT, detected in rumen microbial assays . BHBT’s dimer structure slows degradation compared to BTa, which is rapidly metabolized into Ta . - Thermal Properties :
BHBT’s higher molecular weight and dual hydroxyl groups contribute to a lower melting point (~80–90°C estimated) compared to BHET (Tm = 106–109°C) , enhancing processability in polymer melts.
Key Data Tables
Table 1: Structural and Functional Comparison of Terephthalate Esters
Research Findings and Implications
- Enzymatic Degradation : BHBT’s slower hydrolysis compared to BHET suggests PBAT’s environmental persistence is intermediate between PET (fast degradation) and conventional plastics .
- Catalytic Efficiency : Metal-free catalysts (e.g., SiO₂-DCD) prevent THF formation during BHBT synthesis, addressing a key challenge in BDO-based glycolysis .
- Industrial Relevance: BHBT’s production from recycled PET aligns with circular economy goals, reducing reliance on virgin DMT .
Activité Biologique
Bis(4-hydroxybutyl) terephthalate (BHBT), with the molecular formula CHO, is an organic compound that serves as a diester derived from terephthalic acid. It features two 4-hydroxybutyl groups attached to a terephthalate core. BHBT is primarily utilized in the synthesis of polyesters and polyurethanes, which are essential in various industrial and biomedical applications due to their mechanical properties and biocompatibility.
The synthesis of BHBT typically involves the condensation reaction of dimethyl terephthalate with an excess of 1,4-butanediol, often catalyzed by titanium iso-propoxide. This method yields high-purity BHBT suitable for subsequent polymerization processes. The compound's structure contributes to its favorable properties for both material science and biomedical engineering applications.
Biological Activity
BHBT's biological activity is primarily associated with its biocompatibility , making it a suitable candidate for use in medical devices and implants. Its ability to interact favorably with biological tissues is crucial for applications in biomedical engineering.
- Target of Action : BHBT is used in synthesizing non-isocyanate thermoplastic polyurethanes (NI-TPUs), which are known for their excellent mechanical properties.
- Mode of Action : The polymerization process involves the reaction of BHBT with other compounds to form NI-TPUs, which exhibit desirable characteristics for various applications.
- Biochemical Pathways : The polymerization reaction pathway is influenced by environmental conditions such as temperature and pressure, which are critical for the successful formation of polymers.
Research Findings
Recent studies have investigated the kinetics of polycondensation reactions involving BHBT, revealing insights into its reactivity and potential applications in material science. For instance, research has shown that BHBT can effectively participate in copolycondensation reactions, leading to the formation of advanced polymeric materials with enhanced properties.
Case Studies
- Polymer Synthesis : A study demonstrated that BHBT could be utilized to create polyesters with improved mechanical properties, suitable for high-performance applications.
- Biomedical Applications : Research highlighted the use of BHBT-based materials in developing medical implants, showcasing their compatibility with human tissues and low toxicity levels.
Data Tables
The following table summarizes key properties and findings related to BHBT:
Property/Study Aspect | Description/Findings |
---|---|
Molecular Formula | CHO |
Primary Use | Synthesis of polyesters and polyurethanes |
Biocompatibility | Suitable for medical devices and implants |
Reaction Conditions | Catalyzed by titanium iso-propoxide; optimal temperatures vary |
Kinetics of Reaction | Investigated using proton nuclear magnetic resonance (NMR) |
Environmental Impact | Potentially biodegradable alternatives under study |
Q & A
Basic Research Questions
Q. What are the established methodologies for synthesizing Bis(4-hydroxybutyl) terephthalate, and how can reaction conditions be optimized for high purity?
- Methodology : Synthesis typically involves esterification between terephthalic acid and 1,4-butanediol. Optimization can employ factorial design (e.g., varying molar ratios, catalysts like p-toluenesulfonic acid, and reaction temperatures). Orthogonal experimental designs are recommended for multi-factor optimization, enabling identification of critical parameters (e.g., temperature > catalyst concentration) .
- Characterization : Confirm purity via HPLC (>85% threshold as per regulatory standards ), FTIR (C=O ester peaks at ~1715 cm⁻¹), and NMR (δ 4.1–4.3 ppm for -OCH₂ groups) .
Q. How can researchers assess the acute toxicity profile of this compound in preliminary studies?
- Protocol : Use OECD Guideline 423 for acute oral toxicity in rodent models. Monitor mortality, histopathology, and biochemical markers (e.g., liver enzymes). Classify toxicity per GHS criteria (e.g., LD₅₀ thresholds) .
- Data Interpretation : Compare results with structurally analogous esters (e.g., Bis(2-hydroxyethyl) terephthalate) to identify trends in hydroxyl group positioning and toxicity .
Q. What analytical techniques are critical for quantifying this compound degradation products under environmental conditions?
- Methods : Accelerated degradation studies using UV irradiation or hydrolytic conditions (pH 4–10). Analyze products via LC-MS/MS and GC-MS to detect intermediates like terephthalic acid and 4-hydroxybutanol .
- Validation : Cross-reference with PET oligomer degradation pathways, noting similarities in ester bond cleavage mechanisms .
Advanced Research Questions
Q. How can computational modeling (e.g., DFT, MD simulations) predict the thermal stability and polymer compatibility of this compound?
- Framework : Density Functional Theory (DFT) calculates bond dissociation energies (BDEs) for ester linkages. Molecular Dynamics (MD) simulates interactions with polymer matrices (e.g., PBT) to assess plasticization efficiency .
- Validation : Compare predicted degradation temperatures (TGA) and glass transition temperatures (DSC) with experimental data .
Q. What experimental design strategies resolve contradictions in reported ecotoxicity data for this compound?
- Approach : Conduct a systematic review (PRISMA flowchart) to aggregate disparate studies. Apply meta-analysis to identify confounding variables (e.g., test organism sensitivity, exposure duration) .
- Case Study : Replicate conflicting Daphnia magna toxicity assays under controlled conditions (ISO 6341), adjusting parameters like dissolved oxygen and organic carbon content .
Q. How can multi-factorial optimization improve the scalability of this compound synthesis while minimizing byproduct formation?
- Design : Use Response Surface Methodology (RSM) with central composite design. Variables include reaction time, solvent polarity, and catalyst loading. Optimize for yield (>90%) and byproduct suppression (e.g., <5% oligomers) .
- Outcome : Derive a predictive model to balance cost-efficiency and purity, validated via pilot-scale trials .
Q. What mechanistic insights link this compound’s structural features to its endocrine disruption potential?
- Hypothesis : Hydroxyl and ester groups may interact with nuclear receptors (e.g., estrogen receptor-α). Validate via in vitro reporter gene assays (e.g., ER-CALUX) and molecular docking simulations .
- Data Integration : Cross-correlate with QSAR models for phthalate analogs to identify structural alerts .
Q. Methodological Notes
- Literature Review : Follow evidence-based strategies (PRISMA) for comprehensive coverage of PET-related oligomers, including gray literature and backward/forward citation tracking .
- Theoretical Frameworks : Anchor studies in polymer chemistry principles (e.g., Flory-Huggins theory for solubility parameters) and toxicokinetic models .
Propriétés
IUPAC Name |
bis(4-hydroxybutyl) benzene-1,4-dicarboxylate | |
---|---|---|
Source | PubChem | |
URL | https://pubchem.ncbi.nlm.nih.gov | |
Description | Data deposited in or computed by PubChem | |
InChI |
InChI=1S/C16H22O6/c17-9-1-3-11-21-15(19)13-5-7-14(8-6-13)16(20)22-12-4-2-10-18/h5-8,17-18H,1-4,9-12H2 | |
Source | PubChem | |
URL | https://pubchem.ncbi.nlm.nih.gov | |
Description | Data deposited in or computed by PubChem | |
InChI Key |
MRLFFZIIRRKXBJ-UHFFFAOYSA-N | |
Source | PubChem | |
URL | https://pubchem.ncbi.nlm.nih.gov | |
Description | Data deposited in or computed by PubChem | |
Canonical SMILES |
C1=CC(=CC=C1C(=O)OCCCCO)C(=O)OCCCCO | |
Source | PubChem | |
URL | https://pubchem.ncbi.nlm.nih.gov | |
Description | Data deposited in or computed by PubChem | |
Molecular Formula |
C16H22O6 | |
Source | PubChem | |
URL | https://pubchem.ncbi.nlm.nih.gov | |
Description | Data deposited in or computed by PubChem | |
DSSTOX Substance ID |
DTXSID80451455 | |
Record name | bis(hydroxybutyl) terephthalate | |
Source | EPA DSSTox | |
URL | https://comptox.epa.gov/dashboard/DTXSID80451455 | |
Description | DSSTox provides a high quality public chemistry resource for supporting improved predictive toxicology. | |
Molecular Weight |
310.34 g/mol | |
Source | PubChem | |
URL | https://pubchem.ncbi.nlm.nih.gov | |
Description | Data deposited in or computed by PubChem | |
CAS No. |
23358-95-4 | |
Record name | bis(hydroxybutyl) terephthalate | |
Source | EPA DSSTox | |
URL | https://comptox.epa.gov/dashboard/DTXSID80451455 | |
Description | DSSTox provides a high quality public chemistry resource for supporting improved predictive toxicology. | |
Record name | Bis(4-hydroxybutyl) terephthalate | |
Source | FDA Global Substance Registration System (GSRS) | |
URL | https://gsrs.ncats.nih.gov/ginas/app/beta/substances/LEN57P2BTT | |
Description | The FDA Global Substance Registration System (GSRS) enables the efficient and accurate exchange of information on what substances are in regulated products. Instead of relying on names, which vary across regulatory domains, countries, and regions, the GSRS knowledge base makes it possible for substances to be defined by standardized, scientific descriptions. | |
Explanation | Unless otherwise noted, the contents of the FDA website (www.fda.gov), both text and graphics, are not copyrighted. They are in the public domain and may be republished, reprinted and otherwise used freely by anyone without the need to obtain permission from FDA. Credit to the U.S. Food and Drug Administration as the source is appreciated but not required. | |
Synthesis routes and methods I
Procedure details
Synthesis routes and methods II
Procedure details
Synthesis routes and methods III
Procedure details
Avertissement et informations sur les produits de recherche in vitro
Veuillez noter que tous les articles et informations sur les produits présentés sur BenchChem sont destinés uniquement à des fins informatives. Les produits disponibles à l'achat sur BenchChem sont spécifiquement conçus pour des études in vitro, qui sont réalisées en dehors des organismes vivants. Les études in vitro, dérivées du terme latin "in verre", impliquent des expériences réalisées dans des environnements de laboratoire contrôlés à l'aide de cellules ou de tissus. Il est important de noter que ces produits ne sont pas classés comme médicaments et n'ont pas reçu l'approbation de la FDA pour la prévention, le traitement ou la guérison de toute condition médicale, affection ou maladie. Nous devons souligner que toute forme d'introduction corporelle de ces produits chez les humains ou les animaux est strictement interdite par la loi. Il est essentiel de respecter ces directives pour assurer la conformité aux normes légales et éthiques en matière de recherche et d'expérimentation.