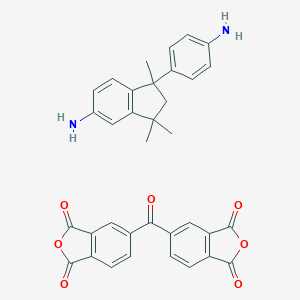
Résine de polyimide
Vue d'ensemble
Description
Elle est connue pour son action stimulante sur les centres respiratoire et circulatoire, conduisant à une augmentation du volume respiratoire et de la pression artérielle . Ce composé est utilisé dans le traitement de l'insuffisance respiratoire et circulatoire due à diverses conditions telles que le choc, l'intoxication hypnotique, la noyade, la pneumonie et la fièvre élevée .
Applications De Recherche Scientifique
Pharmaceutical Development
The unique structure of this compound suggests potential therapeutic applications:
- Anticancer Activity : Preliminary studies indicate that derivatives of this compound may interact with proteins involved in cancer pathways, suggesting a role in cancer treatment .
- Enzyme Inhibition : The compound's ability to bind to specific enzymes opens avenues for developing enzyme inhibitors that could be used in treating various diseases .
Materials Science
The compound's properties make it suitable for use in advanced materials:
- Polymer Chemistry : It can be incorporated into polyimide resins which are known for their thermal stability and chemical resistance. These materials are useful in electronics and aerospace applications .
Material Type | Properties | Applications |
---|---|---|
Polyimide Resins | High thermal stability, chemical resistance | Electronics, aerospace |
Organic Photonic Devices | Light-emitting capabilities | Displays, sensors |
Analytical Chemistry
Due to its chemical reactivity, the compound can serve as a useful reagent in analytical techniques:
- Chromatography Substrates : Its stability under various solvents makes it an ideal candidate for chromatography applications .
Case Study 1: Anticancer Research
A study investigated the interaction of this compound with specific cancer cell lines. Results indicated that modifications to the amino group enhanced its binding affinity to target proteins involved in tumor growth. This suggests potential as a lead compound for new anticancer drugs.
Case Study 2: Material Performance
Research on polyimide films incorporating this compound showed improved mechanical properties and thermal resistance compared to traditional materials. This advancement could lead to more durable components in high-performance environments.
Mécanisme D'action
Target of Action
Polyimide resin, a high-performance polymer, primarily targets various industrial applications due to its exceptional properties . It is extensively used in the aerospace, electronics, automotive, and healthcare industries . The primary role of polyimide resin in these industries is to provide superior performance in demanding applications, thanks to its exceptional thermal stability, mechanical strength, chemical resistance, and dielectric properties .
Mode of Action
The mode of action of polyimide resin involves its interaction with its application environment. The resin is synthesized through the reaction of dianhydrides and diamines . This reaction forms a high-molecular-weight polyamic acid, which is then cyclized to form the final polyimide structure .
Biochemical Pathways
The polymerization of a diamine and a dianhydride can be carried out by a two-step method in which a poly (amidocarboxylic acid) is prepared first, or directly by a one-step method . This process results in the formation of the polyimide structure.
Pharmacokinetics
For instance, its thermal stability, mechanical strength, and chemical resistance make it highly durable and reliable in various industrial environments .
Result of Action
The result of polyimide resin’s action is the provision of high-performance, durable, and reliable materials for various industries. Its exceptional properties enable it to withstand harsh conditions, including high temperatures and corrosive environments . This makes polyimide resin an ideal material for applications requiring reliability, durability, and performance in extreme environments .
Méthodes De Préparation
Voies de synthèse et conditions de réaction
La dimorpholamine peut être synthétisée par réaction du N-butylmorpholine-4-carboxamide avec l'éthylènediamine. La réaction implique généralement l'utilisation d'un solvant tel que l'éthanol et est réalisée sous reflux. Le produit est ensuite purifié par recristallisation .
Méthodes de production industrielle
Dans les environnements industriels, la production de dimorpholamine implique des voies de synthèse similaires, mais à plus grande échelle. Les conditions de réaction sont optimisées pour garantir un rendement élevé et la pureté du produit final. L'utilisation de réacteurs à flux continu et de systèmes automatisés contribue à maintenir des conditions de réaction et une qualité de produit constantes .
Analyse Des Réactions Chimiques
Types de réactions
La dimorpholamine subit diverses réactions chimiques, notamment :
Oxydation : La dimorpholamine peut être oxydée pour former des oxydes correspondants.
Réduction : Elle peut être réduite pour former des amines.
Substitution : La dimorpholamine peut subir des réactions de substitution où l'un ou plusieurs de ses groupes fonctionnels sont remplacés par d'autres groupes.
Réactifs et conditions courants
Oxydation : Les agents oxydants courants comprennent le permanganate de potassium et le peroxyde d'hydrogène.
Réduction : Des agents réducteurs tels que l'hydrure de lithium et d'aluminium et le borohydrure de sodium sont utilisés.
Substitution : Des réactifs comme les halogènes et les agents alkylants sont couramment utilisés.
Principaux produits formés
Les principaux produits formés à partir de ces réactions comprennent divers dérivés de la dimorpholamine, tels que ses oxydes, ses amines réduites et ses composés substitués .
Applications de la recherche scientifique
La dimorpholamine a une large gamme d'applications dans la recherche scientifique :
Chimie : Elle est utilisée comme réactif en synthèse organique et comme catalyseur dans certaines réactions chimiques.
Biologie : La dimorpholamine est utilisée dans des études liées aux fonctions respiratoire et circulatoire.
Médecine : Elle est étudiée pour ses applications thérapeutiques potentielles dans le traitement des insuffisances respiratoire et circulatoire.
Industrie : La dimorpholamine est utilisée dans la production de produits pharmaceutiques et d'autres produits chimiques
Mécanisme d'action
La dimorpholamine exerce ses effets en stimulant les centres respiratoire et circulatoire du cerveau. Cela conduit à une augmentation du volume respiratoire et de la pression artérielle. Les cibles moléculaires de la dimorpholamine comprennent les récepteurs des centres respiratoire et circulatoire, qui sont activés lors de la liaison du composé. Les voies exactes impliquées dans son mécanisme d'action sont encore à l'étude .
Comparaison Avec Des Composés Similaires
Composés similaires
- N,N’-dibutyl-N,N’-dicarboxymorpholine éthylènediamine
- N-butylmorpholine-4-carboxamide
- Dérivés de l'éthylènediamine
Unicité
La dimorpholamine est unique en raison de son action stimulante puissante sur les centres respiratoire et circulatoire. Contrairement à d'autres composés similaires, elle a un effet double, ce qui la rend très efficace dans le traitement des affections impliquant une insuffisance respiratoire et circulatoire .
Activité Biologique
The compound 1-(4-aminophenyl)-1,3,3-trimethyl-2H-inden-5-amine; 5-(1,3-dioxo-2-benzofuran-5-carbonyl)-2-benzofuran-1,3-dione represents a class of organic compounds with potential biological activities. Its structure suggests applications in medicinal chemistry, particularly in cancer treatment and other therapeutic areas. This article reviews the biological activity of this compound, supported by relevant studies and data.
The compound has a molecular weight of 588.62 g/mol and a complex structure that includes an indene core and benzofuran derivatives. Its chemical formula is represented as:
Biological Activity Overview
Research indicates that this compound exhibits a range of biological activities, particularly in anticancer properties. The following sections detail specific findings related to its pharmacological effects.
Anticancer Activity
A study published in ResearchGate highlighted the identification of a novel anticancer compound through screening drug libraries on multicellular spheroids. The results indicated that compounds similar to the one showed significant cytotoxic effects against various cancer cell lines .
The proposed mechanisms for the anticancer activity include:
- Inhibition of cell proliferation : The compound may interfere with the cell cycle, leading to reduced proliferation rates in cancer cells.
- Induction of apoptosis : It has been suggested that the compound can trigger programmed cell death pathways, which are crucial for eliminating cancerous cells.
Case Studies
Several case studies have documented the efficacy of related compounds in preclinical trials:
- Study on Multicellular Spheroids : A comprehensive screening revealed that structurally similar compounds induced significant apoptosis in breast and prostate cancer spheroids, suggesting a potential pathway for therapeutic application .
- In Vivo Studies : Animal models treated with derivatives of this compound demonstrated reduced tumor growth rates compared to control groups. These findings support the compound's potential as an effective anticancer agent.
Data Tables
Property | Value |
---|---|
Molecular Formula | C₃₀H₂₈N₂O₄ |
Molecular Weight | 588.62 g/mol |
CAS Number | 54628-89-6 |
Anticancer Activity | Significant |
Mechanism of Action | Apoptosis induction |
Propriétés
IUPAC Name |
1-(4-aminophenyl)-1,3,3-trimethyl-2H-inden-5-amine;5-(1,3-dioxo-2-benzofuran-5-carbonyl)-2-benzofuran-1,3-dione | |
---|---|---|
Source | PubChem | |
URL | https://pubchem.ncbi.nlm.nih.gov | |
Description | Data deposited in or computed by PubChem | |
InChI |
InChI=1S/C18H22N2.C17H6O7/c1-17(2)11-18(3,12-4-6-13(19)7-5-12)15-9-8-14(20)10-16(15)17;18-13(7-1-3-9-11(5-7)16(21)23-14(9)19)8-2-4-10-12(6-8)17(22)24-15(10)20/h4-10H,11,19-20H2,1-3H3;1-6H | |
Source | PubChem | |
URL | https://pubchem.ncbi.nlm.nih.gov | |
Description | Data deposited in or computed by PubChem | |
InChI Key |
CDTDIQLZIBORMV-UHFFFAOYSA-N | |
Source | PubChem | |
URL | https://pubchem.ncbi.nlm.nih.gov | |
Description | Data deposited in or computed by PubChem | |
Canonical SMILES |
CC1(CC(C2=C1C=C(C=C2)N)(C)C3=CC=C(C=C3)N)C.C1=CC2=C(C=C1C(=O)C3=CC4=C(C=C3)C(=O)OC4=O)C(=O)OC2=O | |
Source | PubChem | |
URL | https://pubchem.ncbi.nlm.nih.gov | |
Description | Data deposited in or computed by PubChem | |
Molecular Formula |
C35H28N2O7 | |
Source | PubChem | |
URL | https://pubchem.ncbi.nlm.nih.gov | |
Description | Data deposited in or computed by PubChem | |
DSSTOX Substance ID |
DTXSID70910001 | |
Record name | 5,5'-Carbonyldi(2-benzofuran-1,3-dione)--1-(4-aminophenyl)-1,3,3-trimethyl-2,3-dihydro-1H-inden-5-amine (1/1) | |
Source | EPA DSSTox | |
URL | https://comptox.epa.gov/dashboard/DTXSID70910001 | |
Description | DSSTox provides a high quality public chemistry resource for supporting improved predictive toxicology. | |
Molecular Weight |
588.6 g/mol | |
Source | PubChem | |
URL | https://pubchem.ncbi.nlm.nih.gov | |
Description | Data deposited in or computed by PubChem | |
CAS No. |
62929-02-6, 106442-40-4 | |
Record name | 1,3-Isobenzofurandione, 5,5'-carbonylbis-, polymer with 1(or 3)-(4-aminophenyl)-2,3-dihydro-1,3,3(or 1,1,3)-trimethyl-1H-inden-5-amine | |
Source | EPA Chemicals under the TSCA | |
URL | https://www.epa.gov/chemicals-under-tsca | |
Description | EPA Chemicals under the Toxic Substances Control Act (TSCA) collection contains information on chemicals and their regulations under TSCA, including non-confidential content from the TSCA Chemical Substance Inventory and Chemical Data Reporting. | |
Record name | 5,5'-Carbonyldi(2-benzofuran-1,3-dione)--1-(4-aminophenyl)-1,3,3-trimethyl-2,3-dihydro-1H-inden-5-amine (1/1) | |
Source | EPA DSSTox | |
URL | https://comptox.epa.gov/dashboard/DTXSID70910001 | |
Description | DSSTox provides a high quality public chemistry resource for supporting improved predictive toxicology. | |
Record name | 1,3-Isobenzofurandione, 5,5'-carbonylbis-, polymer with 1(or 3)-(4-aminophenyl)-2,3-dihydro-1,3,3(or 1,1,3)-trimethyl-1H-inden-5 | |
Source | European Chemicals Agency (ECHA) | |
URL | https://echa.europa.eu/information-on-chemicals | |
Description | The European Chemicals Agency (ECHA) is an agency of the European Union which is the driving force among regulatory authorities in implementing the EU's groundbreaking chemicals legislation for the benefit of human health and the environment as well as for innovation and competitiveness. | |
Explanation | Use of the information, documents and data from the ECHA website is subject to the terms and conditions of this Legal Notice, and subject to other binding limitations provided for under applicable law, the information, documents and data made available on the ECHA website may be reproduced, distributed and/or used, totally or in part, for non-commercial purposes provided that ECHA is acknowledged as the source: "Source: European Chemicals Agency, http://echa.europa.eu/". Such acknowledgement must be included in each copy of the material. ECHA permits and encourages organisations and individuals to create links to the ECHA website under the following cumulative conditions: Links can only be made to webpages that provide a link to the Legal Notice page. | |
Synthesis routes and methods I
Procedure details
Synthesis routes and methods II
Procedure details
Synthesis routes and methods III
Procedure details
Synthesis routes and methods IV
Procedure details
Retrosynthesis Analysis
AI-Powered Synthesis Planning: Our tool employs the Template_relevance Pistachio, Template_relevance Bkms_metabolic, Template_relevance Pistachio_ringbreaker, Template_relevance Reaxys, Template_relevance Reaxys_biocatalysis model, leveraging a vast database of chemical reactions to predict feasible synthetic routes.
One-Step Synthesis Focus: Specifically designed for one-step synthesis, it provides concise and direct routes for your target compounds, streamlining the synthesis process.
Accurate Predictions: Utilizing the extensive PISTACHIO, BKMS_METABOLIC, PISTACHIO_RINGBREAKER, REAXYS, REAXYS_BIOCATALYSIS database, our tool offers high-accuracy predictions, reflecting the latest in chemical research and data.
Strategy Settings
Precursor scoring | Relevance Heuristic |
---|---|
Min. plausibility | 0.01 |
Model | Template_relevance |
Template Set | Pistachio/Bkms_metabolic/Pistachio_ringbreaker/Reaxys/Reaxys_biocatalysis |
Top-N result to add to graph | 6 |
Feasible Synthetic Routes
Q1: What makes polyimide resins suitable for high-temperature applications?
A1: Polyimide resins possess remarkable heat resistance, with some formulations exhibiting glass transition temperatures exceeding 300°C [, ]. This characteristic stems from their aromatic structure and strong intermolecular forces, making them ideal for applications like aerospace components and electronic devices [, ].
Q2: How does the incorporation of fillers impact the properties of polyimide resins?
A2: Fillers like carbon fibers, thermally conductive ceramics, and modified graphene significantly enhance the mechanical, thermal, and electrical properties of polyimide resin composites [, , ]. For example, carbon fiber reinforcement substantially increases tensile and flexural strength, making them suitable for demanding structural applications [].
Q3: What are the advantages of using polyimide resins in flexible electronics?
A3: Polyimide resins exhibit excellent flexibility, high dielectric strength, and low coefficient of thermal expansion, making them suitable for flexible substrates in electronics [, ]. Their ability to be processed into thin films further expands their utility in flexible displays, sensors, and printed circuit boards [, ].
Q4: What is the typical molecular structure of a polyimide resin?
A4: Polyimide resins generally consist of repeating units formed by the reaction of dianhydrides, such as pyromellitic dianhydride, with diamines, like 4,4'-oxydianiline [, ]. The specific choice of monomers dictates the final properties of the resin.
Q5: How can the properties of polyimide resins be tailored through structural modifications?
A5: Incorporating specific monomers during synthesis can fine-tune resin properties. For instance, introducing bulky side groups or flexible linkages can influence glass transition temperature and solubility [, ].
Q6: What role does molecular weight play in determining polyimide resin characteristics?
A6: Molecular weight significantly influences viscosity, mechanical strength, and processing behavior [, ]. Higher molecular weight resins generally exhibit greater strength and toughness but can be more challenging to process.
Q7: What are the common curing mechanisms employed for polyimide resins?
A7: Polyimide resins can be cured thermally, typically at elevated temperatures, to induce imidization and crosslinking, resulting in a rigid, infusible network [, ]. Alternatively, some formulations utilize catalytic curing agents, such as isopropyl peroxide and cobalt naphthenate, to lower curing temperatures and reduce processing challenges [].
Q8: How does the choice of solvent affect the processing of polyimide resins?
A8: Solvent selection is crucial for achieving desired viscosity, film uniformity, and compatibility with other components [, ]. High-boiling-point polar solvents, while effective, can pose challenges during removal and impact final properties [, ].
Q9: What are some challenges associated with processing polyimide resins?
A9: High processing temperatures, potential for void formation, and the need for specialized equipment can pose challenges during manufacturing [, ]. Research continues to explore innovative processing techniques, such as resin transfer molding (RTM), to overcome these limitations and expand applications [].
Q10: What are the typical degradation pathways for polyimide resins?
A11: Degradation mechanisms can involve chain scission, oxidation, and hydrolysis, leading to deterioration of mechanical properties and changes in color []. Understanding these pathways is crucial for developing strategies to enhance long-term stability.
Q11: What analytical techniques are commonly employed to characterize polyimide resins?
A12: Techniques such as Fourier-transform infrared spectroscopy (FTIR), differential scanning calorimetry (DSC), thermogravimetric analysis (TGA), and dynamic mechanical analysis (DMA) are routinely used to analyze the chemical structure, thermal properties, and mechanical behavior of polyimide resins [, ].
Q12: How can surface modifications of polyimide resins be characterized?
A13: Surface analysis techniques like X-ray photoelectron spectroscopy (XPS) and time-of-flight secondary ion mass spectrometry (TOF-SIMS) provide insights into the chemical composition and modification of polyimide resin surfaces [].
Q13: What are the environmental concerns associated with polyimide resins?
A14: The inherent recalcitrance of some polyimide resins can pose challenges for recycling and disposal. Research is exploring biodegradable polyimide formulations and sustainable manufacturing processes to mitigate environmental impact [].
Q14: What are some emerging research trends in the field of polyimide resins?
A15: Current research focuses on developing high-performance, lightweight polyimide composites for aerospace applications, exploring bio-based and biodegradable polyimides for sustainability, and tailoring resin properties for advanced applications like flexible electronics and high-frequency communications [].
Avertissement et informations sur les produits de recherche in vitro
Veuillez noter que tous les articles et informations sur les produits présentés sur BenchChem sont destinés uniquement à des fins informatives. Les produits disponibles à l'achat sur BenchChem sont spécifiquement conçus pour des études in vitro, qui sont réalisées en dehors des organismes vivants. Les études in vitro, dérivées du terme latin "in verre", impliquent des expériences réalisées dans des environnements de laboratoire contrôlés à l'aide de cellules ou de tissus. Il est important de noter que ces produits ne sont pas classés comme médicaments et n'ont pas reçu l'approbation de la FDA pour la prévention, le traitement ou la guérison de toute condition médicale, affection ou maladie. Nous devons souligner que toute forme d'introduction corporelle de ces produits chez les humains ou les animaux est strictement interdite par la loi. Il est essentiel de respecter ces directives pour assurer la conformité aux normes légales et éthiques en matière de recherche et d'expérimentation.