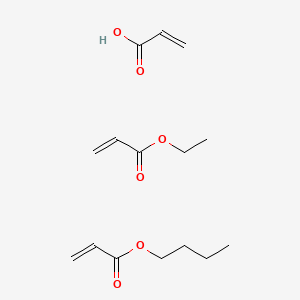
Butylacrylate ethylacrylate acrylic acid
Descripción general
Descripción
Butylacrylate ethylacrylate acrylic acid is a useful research compound. Its molecular formula is C15H24O6 and its molecular weight is 300.35 g/mol. The purity is usually 95%.
BenchChem offers high-quality this compound suitable for many research applications. Different packaging options are available to accommodate customers' requirements. Please inquire for more information about this compound including the price, delivery time, and more detailed information at info@benchchem.com.
Propiedades
Fórmula molecular |
C15H24O6 |
---|---|
Peso molecular |
300.35 g/mol |
Nombre IUPAC |
butyl prop-2-enoate;ethyl prop-2-enoate;prop-2-enoic acid |
InChI |
InChI=1S/C7H12O2.C5H8O2.C3H4O2/c1-3-5-6-9-7(8)4-2;1-3-5(6)7-4-2;1-2-3(4)5/h4H,2-3,5-6H2,1H3;3H,1,4H2,2H3;2H,1H2,(H,4,5) |
Clave InChI |
FEGVAAWSWJUUPF-UHFFFAOYSA-N |
SMILES canónico |
CCCCOC(=O)C=C.CCOC(=O)C=C.C=CC(=O)O |
Números CAS relacionados |
27322-15-2 |
Origen del producto |
United States |
Synthesis routes and methods I
Procedure details
Synthesis routes and methods II
Procedure details
Synthesis routes and methods III
Procedure details
Synthesis routes and methods IV
Procedure details
Synthesis routes and methods V
Procedure details
Descargo de responsabilidad e información sobre productos de investigación in vitro
Tenga en cuenta que todos los artículos e información de productos presentados en BenchChem están destinados únicamente con fines informativos. Los productos disponibles para la compra en BenchChem están diseñados específicamente para estudios in vitro, que se realizan fuera de organismos vivos. Los estudios in vitro, derivados del término latino "in vidrio", involucran experimentos realizados en entornos de laboratorio controlados utilizando células o tejidos. Es importante tener en cuenta que estos productos no se clasifican como medicamentos y no han recibido la aprobación de la FDA para la prevención, tratamiento o cura de ninguna condición médica, dolencia o enfermedad. Debemos enfatizar que cualquier forma de introducción corporal de estos productos en humanos o animales está estrictamente prohibida por ley. Es esencial adherirse a estas pautas para garantizar el cumplimiento de los estándares legales y éticos en la investigación y experimentación.