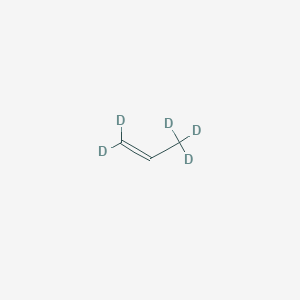
1,1,3,3,3-Pentadeuterioprop-1-ene
Descripción general
Descripción
1,1,3,3,3-Pentadeuterioprop-1-ene: is a deuterated analog of propene, where five hydrogen atoms are replaced by deuterium. Deuterium is a stable isotope of hydrogen, which makes this compound particularly useful in various scientific research applications, especially in the field of spectroscopy and reaction mechanism studies.
Métodos De Preparación
Synthetic Routes and Reaction Conditions: 1,1,3,3,3-Pentadeuterioprop-1-ene can be synthesized through the deuteration of propene. One common method involves the catalytic exchange of hydrogen atoms with deuterium using a deuterium gas atmosphere in the presence of a suitable catalyst such as palladium on carbon (Pd/C).
Industrial Production Methods: Industrial production of deuterated compounds often involves the use of heavy water (D2O) as a source of deuterium. The process typically includes the catalytic deuteration of hydrocarbons under controlled conditions to achieve high levels of deuterium incorporation.
Análisis De Reacciones Químicas
Types of Reactions: 1,1,3,3,3-Pentadeuterioprop-1-ene undergoes similar chemical reactions as its non-deuterated counterpart, propene. These reactions include:
Oxidation: The compound can be oxidized to form deuterated alcohols, aldehydes, or carboxylic acids.
Reduction: It can be reduced to form deuterated alkanes.
Substitution: The compound can undergo substitution reactions where deuterium atoms are replaced by other functional groups.
Common Reagents and Conditions:
Oxidation: Common oxidizing agents include potassium permanganate (KMnO4) and ozone (O3).
Reduction: Catalytic hydrogenation using deuterium gas (D2) and a metal catalyst such as palladium (Pd) or platinum (Pt).
Substitution: Halogenation reactions using halogens like chlorine (Cl2) or bromine (Br2).
Major Products Formed:
Oxidation: Deuterated alcohols, aldehydes, and carboxylic acids.
Reduction: Deuterated alkanes.
Substitution: Deuterated halides.
Aplicaciones Científicas De Investigación
1,1,3,3,3-Pentadeuterioprop-1-ene is widely used in scientific research due to its unique properties:
Chemistry: It is used in kinetic isotope effect studies to understand reaction mechanisms.
Biology: Deuterated compounds are used in metabolic studies to trace biochemical pathways.
Medicine: It is used in the development of deuterated drugs, which often have improved metabolic stability and reduced toxicity.
Industry: Deuterated compounds are used in the production of specialty chemicals and materials with enhanced properties.
Mecanismo De Acción
The mechanism by which 1,1,3,3,3-Pentadeuterioprop-1-ene exerts its effects is primarily through the kinetic isotope effect. The presence of deuterium atoms, which are heavier than hydrogen atoms, results in a lower vibrational frequency and bond dissociation energy. This leads to slower reaction rates for processes involving C-D bonds compared to C-H bonds, allowing researchers to study reaction mechanisms in greater detail.
Comparación Con Compuestos Similares
- 1,1,1,3,3-Pentadeuterio-2-(trideuteriomethoxy)prop-1-ene
- 1,1,1,3,3-Pentafluoropropane
- cis-1,3,3,3-Tetrafluoroprop-1-ene
Comparison: 1,1,3,3,3-Pentadeuterioprop-1-ene is unique due to its specific deuterium substitution pattern, which makes it particularly useful for studying the kinetic isotope effect. Other similar compounds, such as 1,1,1,3,3-Pentafluoropropane and cis-1,3,3,3-Tetrafluoroprop-1-ene, have different substitution patterns and are used in different applications, such as refrigerants and solvents .
Propiedades
IUPAC Name |
1,1,3,3,3-pentadeuterioprop-1-ene | |
---|---|---|
Source | PubChem | |
URL | https://pubchem.ncbi.nlm.nih.gov | |
Description | Data deposited in or computed by PubChem | |
InChI |
InChI=1S/C3H6/c1-3-2/h3H,1H2,2H3/i1D2,2D3 | |
Source | PubChem | |
URL | https://pubchem.ncbi.nlm.nih.gov | |
Description | Data deposited in or computed by PubChem | |
InChI Key |
QQONPFPTGQHPMA-KPAILUHGSA-N | |
Source | PubChem | |
URL | https://pubchem.ncbi.nlm.nih.gov | |
Description | Data deposited in or computed by PubChem | |
Canonical SMILES |
CC=C | |
Source | PubChem | |
URL | https://pubchem.ncbi.nlm.nih.gov | |
Description | Data deposited in or computed by PubChem | |
Isomeric SMILES |
[2H]C(=CC([2H])([2H])[2H])[2H] | |
Source | PubChem | |
URL | https://pubchem.ncbi.nlm.nih.gov | |
Description | Data deposited in or computed by PubChem | |
Molecular Formula |
C3H6 | |
Source | PubChem | |
URL | https://pubchem.ncbi.nlm.nih.gov | |
Description | Data deposited in or computed by PubChem | |
Molecular Weight |
47.11 g/mol | |
Source | PubChem | |
URL | https://pubchem.ncbi.nlm.nih.gov | |
Description | Data deposited in or computed by PubChem | |
Synthesis routes and methods I
Procedure details
Synthesis routes and methods II
Procedure details
Synthesis routes and methods III
Procedure details
Synthesis routes and methods IV
Procedure details
Synthesis routes and methods V
Procedure details
Descargo de responsabilidad e información sobre productos de investigación in vitro
Tenga en cuenta que todos los artículos e información de productos presentados en BenchChem están destinados únicamente con fines informativos. Los productos disponibles para la compra en BenchChem están diseñados específicamente para estudios in vitro, que se realizan fuera de organismos vivos. Los estudios in vitro, derivados del término latino "in vidrio", involucran experimentos realizados en entornos de laboratorio controlados utilizando células o tejidos. Es importante tener en cuenta que estos productos no se clasifican como medicamentos y no han recibido la aprobación de la FDA para la prevención, tratamiento o cura de ninguna condición médica, dolencia o enfermedad. Debemos enfatizar que cualquier forma de introducción corporal de estos productos en humanos o animales está estrictamente prohibida por ley. Es esencial adherirse a estas pautas para garantizar el cumplimiento de los estándares legales y éticos en la investigación y experimentación.