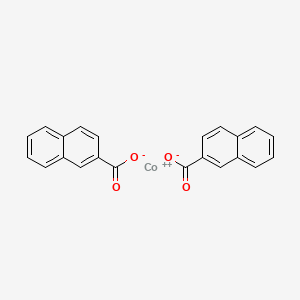
Cobalt naphthenate
- Klicken Sie auf QUICK INQUIRY, um ein Angebot von unserem Expertenteam zu erhalten.
- Mit qualitativ hochwertigen Produkten zu einem WETTBEWERBSFÄHIGEN Preis können Sie sich mehr auf Ihre Forschung konzentrieren.
Übersicht
Beschreibung
Cobalt naphthenate (CAS 61789-51-3) is a coordination compound formed by cobalt(II) ions and naphthenic acid derivatives, typically derived from crude oil refining. It appears as a dark brown liquid or powder, soluble in organic solvents like white spirits, and is commercially available in concentrations ranging from 6% to 10.5% cobalt metal by weight . Its primary applications include:
- Catalysis: Accelerating polymerization reactions (e.g., in 1,4-cis-polybutadiene production) and redox curing of resins .
- Paints and Coatings: Serving as a siccative (drying agent) in alkyd resins, improving hardness and durability .
- Rubber Industry: Enhancing adhesion between rubber compounds and brass-plated steel cords .
Wissenschaftliche Forschungsanwendungen
Introduction to Cobalt Naphthenate
This compound is a coordination complex formed from cobalt(II) and naphthenic acids. It is primarily recognized for its applications as a catalyst and drying agent in various industrial processes. This compound is a mixture of cobalt(II) derivatives, which contributes to its effectiveness in promoting chemical reactions, particularly in the curing of resins and inks.
Catalyst in Polymerization Processes
This compound is extensively used as a catalyst in the polymerization of unsaturated polyester resins and epoxy systems. Its role as an accelerator enhances the curing process, resulting in improved mechanical properties and chemical resistance of the final products.
- Case Study : In a study focusing on the effects of this compound on resin formulations, it was found that incorporating this compound significantly reduced curing times while enhancing the durability of the resins used in coatings and adhesives .
Drying Agent for Paints and Coatings
The compound serves as an effective drying agent in paints, varnishes, and inks. It facilitates the autoxidative crosslinking of drying oils, which is crucial for achieving desired film properties.
- Data Table: Drying Efficiency Comparison
Compound | Drying Time (hours) | Final Film Hardness |
---|---|---|
This compound | 1 | High |
Manganese Naphthenate | 2 | Medium |
Iron Naphthenate | 3 | Low |
This table illustrates that this compound outperforms other metal naphthenates in terms of drying efficiency and film hardness .
Rubber Adhesion Promoter
In the rubber industry, this compound is utilized as an adhesion promoter, particularly in tire manufacturing. It enhances the bonding between rubber and steel components, leading to improved performance characteristics.
- Case Study : A patent describes a preparation method for solid this compound that demonstrates its effectiveness as a rubber adhesion accelerator, meeting industry standards for tire production .
Concrete Additive
Recent research indicates that this compound can be employed as an additive in concrete formulations to mitigate surface erosion and enhance compressive strength. This application is particularly beneficial in structural and decorative construction panels.
- Research Findings : Studies have shown that varying concentrations of this compound positively affect the compressive strength of concrete, making it suitable for high-performance applications .
Pigment Production
This compound is also used in producing pigments for ceramics, glass, and enamels. Its ability to act as a pigment drier contributes to the stability and color retention of these materials.
Safety and Toxicity Considerations
While this compound has numerous industrial applications, it is essential to consider its toxicity. The compound is classified as moderately toxic and has been associated with various health risks, including potential carcinogenic effects upon prolonged exposure. Safety measures must be implemented to minimize contact with skin and eyes during handling .
Analyse Chemischer Reaktionen
Autoxidation and Crosslinking in Drying Oils
Cobalt naphthenate is widely employed as a catalyst for the autoxidative crosslinking of unsaturated drying oils (e.g., linseed oil) and alkyd resins. The mechanism involves:
-
Hydroperoxide Formation : Cobalt(II) promotes the generation of hydroperoxides (ROOH) via radical chain initiation.
-
Radical Decomposition : The cobalt center undergoes redox cycling (Co²⁺ ↔ Co³⁺), decomposing hydroperoxides into alkoxy (RO- ) and peroxy (ROO- ) radicals.
-
Crosslinking : These radicals abstract hydrogen atoms from adjacent unsaturated fatty acid chains, forming covalent crosslinks and solid polymer networks .
Key Data :
Property | Value/Effect | Source |
---|---|---|
Optimal Co concentration | 0.005–0.02% (w/w) in oil | |
Drying time reduction | 50–70% compared to uncatalyzed systems |
Hydrosilylation of Alkenes
This compound acts as a catalyst for the hydrosilylation of alkenes with diphenylsilane (Ph₂SiH₂), enabling the synthesis of organosilanes. A study using N,P-ligands (e.g., L1 ) demonstrated enhanced catalytic efficiency :
Experimental Conditions and Results :
Ligand | Reaction Time (h) | Temperature (°C) | 1-Octene Conversion (%) |
---|---|---|---|
None | 3 | 50 | <5 |
L1 | 3 | 50 | 99.9 |
L5 | 3 | 50 | 96.4 |
Key Findings :
-
Ligand L1 (sodium 2-(diphenylphosphino)methyl-2-ethylaminopropanoate) maximized activity due to strong electron-donating properties .
-
Additives like KOBu reduced reaction time to 0.5 hours at room temperature by activating silane reagents .
Catalytic Oxidation in Hydrocarbon Processing
This compound accelerates low-temperature oxidation (LTO) of hydrocarbons, critical for enhanced oil recovery. In Changqing tight oil, it:
-
Reduced activation energy (Eₐ) of LTO by 15–30% across saturates, aromatics, and resins .
-
Promoted hydroxyl-containing oxide and CO₂ formation while inhibiting ether production .
Activation Energy Comparison :
Fraction | Eₐ (kJ/mol) Without Co | Eₐ (kJ/mol) With Co |
---|---|---|
Saturates | 72.3 | 61.5 |
Aromatics | 85.1 | 72.8 |
Resins | 94.6 | 68.4 |
Polymerization and Curing of Resins
In polymer chemistry, this compound initiates free-radical polymerization and accelerates curing:
-
Unsaturated Polyesters : Acts as a co-catalyst with peroxides (e.g., MEKP), reducing gelation time by 40–60% .
-
Flame-Retardant Polymers : Promotes crosslinking in halogenated resins, improving thermal stability .
Typical Formulation :
Component | Role | Concentration (wt%) |
---|---|---|
This compound | Catalyst | 0.1–0.5 |
Methyl ethyl ketone peroxide (MEKP) | Initiator | 1–2 |
Q & A
Basic Research Questions
Q. What are the standard laboratory methods for synthesizing cobalt naphthenate, and how can purity be ensured?
- Methodology : Synthesis typically involves reacting cobalt salts (e.g., cobalt chloride) with naphthenic acid in a solvent like toluene or xylene under controlled pH and temperature. Purification steps include solvent evaporation, filtration, and vacuum drying. Purity is assessed via elemental analysis (e.g., inductively coupled plasma mass spectrometry for cobalt content) and Fourier-transform infrared spectroscopy (FTIR) to confirm ligand coordination .
- Key Considerations : Ensure anhydrous conditions to prevent hydrolysis, and validate stoichiometric ratios using gravimetric analysis. Cross-reference protocols from peer-reviewed studies to minimize variability .
Q. How can researchers characterize the structural and physicochemical properties of this compound?
- Methodology :
- Structural analysis : Use nuclear magnetic resonance (NMR) for ligand structure confirmation and X-ray photoelectron spectroscopy (XPS) to determine cobalt oxidation states.
- Physicochemical properties : Measure solubility in organic solvents (e.g., via UV-Vis spectroscopy) and thermal stability using thermogravimetric analysis (TGA) .
Q. What safety protocols are critical when handling this compound in laboratory settings?
- Guidelines :
- Use fume hoods to avoid inhalation of powdered forms, which are flammable and may release toxic fumes upon decomposition.
- Wear nitrile gloves and lab coats to prevent dermal exposure, as cobalt compounds are potential skin irritants .
Advanced Research Questions
Q. What experimental designs are optimal for studying the catalytic mechanisms of this compound in oxidation reactions?
- Approach :
- Kinetic studies : Monitor reaction rates using gas chromatography (GC) or in-situ FTIR to track intermediate species.
- Mechanistic probes : Introduce radical scavengers (e.g., TEMPO) to identify reaction pathways. Compare activity with cobalt carboxylate analogs to isolate ligand effects .
Q. How can contradictions in toxicity data for this compound across studies be resolved?
- Analytical strategies :
- Meta-analysis : Aggregate data from toxicological databases (e.g., ATSDR reports) and apply statistical tools (ANOVA, regression) to identify confounding variables like exposure duration or solvent carriers .
- In vitro/In vivo correlation : Conduct parallel assays using human cell lines (e.g., HepG2) and rodent models to assess interspecies variability .
Q. What methodologies are effective for tracking environmental degradation pathways of this compound?
- Field and lab integration :
- Environmental sampling : Use liquid-liquid extraction followed by GC-MS to detect degradation products in soil or water.
- Simulation studies : Apply quantitative structure-activity relationship (QSAR) models to predict biodegradation rates under varying pH and microbial activity .
Q. Data and Reproducibility
Q. How can researchers ensure reproducibility in this compound studies?
- Best practices :
Vergleich Mit ähnlichen Verbindungen
Comparison with Similar Cobalt Compounds
Alkyd Resin Driers (Cobalt Soaps)
Cobalt naphthenate is part of a broader class of cobalt carboxylates ("cobalt soaps") used as drying catalysts. Key competitors include cobalt(II) 2-ethylhexanoate (Co-2-EH) and cobalt neodecanoate.
Key Findings :
- All three compounds function effectively at similar cobalt concentrations, but isomer differences may influence solubility and compatibility with resin formulations .
- This compound and neodecanoate are preferred for formulations requiring enhanced stability in hydrophobic matrices due to their organic acid backbones .
Adhesion Promoters in Rubber-Brass Composites
In rubber compounds, cobalt salts enhance adhesion to brass-plated steel cords. Comparative studies highlight performance variations:
Key Findings :
- Cobalt boroacylate outperforms naphthenate in aging resistance due to balanced copper sulfide formation and crosslink density enhancement .
- High this compound levels (>0.16 phr) degrade adhesion after aging, likely due to excessive sulfide layer growth .
Catalytic Activity in Polymerization
This compound is compared with nickel naphthenate and cobalt octanoate in catalytic applications:
Key Findings :
- Cobalt octanoate is preferred in 1,4-cis-polybutadiene production due to optimal Lewis acidity when paired with aluminum co-catalysts .
- Nickel naphthenate shows unique activity in silazane dehydrocoupling but lacks broad industrial adoption .
Key Findings :
- All cobalt compounds share similar carcinogenicity classifications, but bioavailability varies significantly .
Vorbereitungsmethoden
Acid-Base Neutralization with Rosin Dispersion
Reactant Composition and Ratios
The primary method involves neutralizing naphthenic acid with cobalt hydroxide in the presence of rosin and xylene. Key reactant ratios include:
-
Naphthenic acid : 65–75 parts (acid number: 190–210 mg KOH/g)
-
Cobalt hydroxide : 15–17 parts
-
Rosin : 15–25 parts (acts as a dispersant and solid-phase stabilizer)
Rosin’s inclusion prevents agglomeration during solidification, ensuring uniform particle distribution in the final product .
Reaction and Distillation Process
The synthesis occurs in four stages:
-
Mixing and Neutralization : Naphthenic acid, rosin, and xylene are stirred at 150–250 rpm while cobalt hydroxide is gradually added under vacuum.
-
Low-Temperature Distillation : Heating to 85–95°C removes xylene-water azeotrope, eliminating byproduct water .
-
High-Temperature Vacuum Distillation : Temperature is raised to 165–175°C, and vacuum pressure is reduced from -0.01 MPa to -0.09 MPa over 120 minutes to isolate solid this compound .
-
Pelletization : The product is granulated at 25–35°C using a rotary-belt condenser, enhancing handling and solubility in rubber matrices .
Table 1: Performance of this compound from Acid-Base Neutralization
Parameter | Value | Source |
---|---|---|
Cobalt Content | 8–10% (w/w) | |
Decomposition Temperature | >200°C | |
Solubility in Xylene | Complete |
Purified Naphthenic Acid Reaction with Cobaltous Carbonate
Naphthenic Acid Purification
This method prioritizes pre-reaction purification to enhance cobalt content:
-
Solvent Extraction : Naphthenic acid is dissolved in polar solvents (chloroform, iso-amyl butyrate) at a 60:30–35 solvent-to-acid ratio to remove unsaponifiable impurities .
-
Distillation : The extract is distilled at 130–150°C with a reflux ratio <3, recovering 85–90% of the solvent .
-
Vacuum Rectification : Under -0.07 to -0.09 MPa, middle distillates (140–150°C) are collected, yielding naphthenic acid with ≥220 mg KOH/g acid number and ≤2% unsaponifiable matter .
Synthesis with Cobaltous Carbonate
Purified naphthenic acid reacts with wet cobaltous carbonate (CoCO₃·Co(OH)₂·H₂O) under reflux:
-
Stoichiometric Ratios : 4 moles of naphthenic acid per mole of cobaltous carbonate .
-
Stepwise Addition : 40% of naphthenic acid is added at 40°C, followed by the remainder at 60–80°C to control exothermicity .
-
Dehydration and Solvent Removal :
Table 2: Performance of Purified-Method this compound
Parameter | Value | Source |
---|---|---|
Cobalt Content | 12–14% (w/w) | |
Reaction Time Reduction | 1.5–2 hours vs. conventional | |
Solvent Consumption | Reduced by 15% |
Comparative Analysis of Synthesis Methods
Efficiency and Product Quality
-
Acid-Base Neutralization : Faster (total time: 4–6 hours) but yields lower cobalt content (8–10%) .
-
Purified Naphthenate Method : Longer purification (16–22 hours) but achieves higher cobalt content (12–14%) and better thermal stability .
Industrial Applicability
-
Rubber Industry : Acid-base neutralization is preferred for its simplicity and granular product form, which integrates seamlessly into rubber compounding .
-
High-Purity Applications : The purified method suits coatings and resins requiring minimal impurities .
Challenges and Optimization Strategies
Byproduct Management
-
Water Removal : Incomplete dehydration during reflux causes hydrolysis, reducing cobalt content. Solutions include azeotropic distillation with xylene .
-
Solvent Recovery : Vacuum distillation at -0.09 MPa recovers >95% of xylene, critical for cost-effectiveness .
Temperature Control
Exceeding 215°C in the purified method degrades naphthenate complexes. Automated temperature feedback systems are recommended .
Eigenschaften
CAS-Nummer |
157583-32-9 |
---|---|
Molekularformel |
C22H14CoO4 |
Molekulargewicht |
401.3 g/mol |
IUPAC-Name |
cobalt(2+);naphthalene-2-carboxylate |
InChI |
InChI=1S/2C11H8O2.Co/c2*12-11(13)10-6-5-8-3-1-2-4-9(8)7-10;/h2*1-7H,(H,12,13);/q;;+2/p-2 |
InChI-Schlüssel |
IFSWBZCGMGEHLE-UHFFFAOYSA-L |
Kanonische SMILES |
C1=CC=C2C=C(C=CC2=C1)C(=O)[O-].C1=CC=C2C=C(C=CC2=C1)C(=O)[O-].[Co+2] |
Dichte |
0.9 g/cm³ |
melting_point |
140 °C |
Physikalische Beschreibung |
Brown or blush-red solid; [ICSC] Insoluble in water; [MSDSonline] BROWN AMORPHOUS OR BLUISH-RED SOLID. |
Löslichkeit |
Solubility in water: none |
Herkunft des Produkts |
United States |
Haftungsausschluss und Informationen zu In-Vitro-Forschungsprodukten
Bitte beachten Sie, dass alle Artikel und Produktinformationen, die auf BenchChem präsentiert werden, ausschließlich zu Informationszwecken bestimmt sind. Die auf BenchChem zum Kauf angebotenen Produkte sind speziell für In-vitro-Studien konzipiert, die außerhalb lebender Organismen durchgeführt werden. In-vitro-Studien, abgeleitet von dem lateinischen Begriff "in Glas", beinhalten Experimente, die in kontrollierten Laborumgebungen unter Verwendung von Zellen oder Geweben durchgeführt werden. Es ist wichtig zu beachten, dass diese Produkte nicht als Arzneimittel oder Medikamente eingestuft sind und keine Zulassung der FDA für die Vorbeugung, Behandlung oder Heilung von medizinischen Zuständen, Beschwerden oder Krankheiten erhalten haben. Wir müssen betonen, dass jede Form der körperlichen Einführung dieser Produkte in Menschen oder Tiere gesetzlich strikt untersagt ist. Es ist unerlässlich, sich an diese Richtlinien zu halten, um die Einhaltung rechtlicher und ethischer Standards in Forschung und Experiment zu gewährleisten.