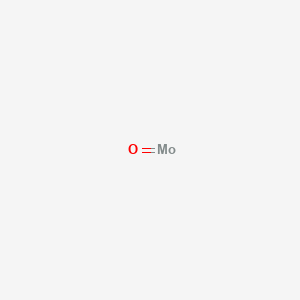
MOLYBDENUM OXIDE
Übersicht
Beschreibung
Molybdenum oxide (MoO₃) is a transition metal oxide with a layered orthorhombic crystal structure, enabling ion intercalation and diverse stoichiometries (e.g., MoO₂, MoO₃, and mixed-valence oxides) . Its oxidation states range from +2 to +7, granting tunable electronic, optical, and catalytic properties. MoO₃ exhibits high thermal stability (decomposes at ~800°C) and is widely used in electrochromic devices, gas sensors, catalysis, and energy storage systems . The material’s oxygen vacancy concentration and non-stoichiometry significantly influence its conductivity and surface reactivity, making it adaptable for advanced applications .
Vorbereitungsmethoden
Synthetic Routes and Reaction Conditions
MOLYBDENUM OXIDE compounds can be synthesized through various methods. One common approach involves the reaction of molybdenum trioxide with organic ligands in the presence of a solvent. For example, the synthesis of binuclear oxomolybdenum (V) xanthate complexes involves the reaction of molybdenum trioxide with xanthate ligands under controlled conditions .
Industrial Production Methods
Industrial production of oxomolybdenum compounds often involves high-temperature methods. For instance, molybdenum carbides can be prepared by reacting molybdenum or this compound with elemental carbon in an atmosphere of hydrogen or hydrocarbon gases at temperatures ranging from 1200 to 2000°C .
Analyse Chemischer Reaktionen
Types of Reactions
MOLYBDENUM OXIDE compounds undergo various types of chemical reactions, including:
Oxidation: this compound compounds are well-known oxidation catalysts.
Reduction: These compounds can also participate in reduction reactions, often involving the transfer of oxygen atoms.
Substitution: Ligand substitution reactions are common, where ligands attached to the molybdenum center are replaced by other ligands.
Common Reagents and Conditions
Common reagents used in reactions with oxomolybdenum compounds include hydrogen peroxide, tert-butyl hydroperoxide, and various organic ligands. Reaction conditions typically involve controlled temperatures and solvents to facilitate the desired transformations.
Major Products
The major products formed from reactions involving oxomolybdenum compounds depend on the specific reaction type. For example, oxidation reactions often yield oxidized organic compounds, while reduction reactions can produce reduced organic or inorganic species.
Wissenschaftliche Forschungsanwendungen
Catalysis
Molybdenum oxide serves as a catalyst in various chemical reactions due to its ability to facilitate oxidation and reduction processes.
- Methane Oxidation : this compound has been explored for its catalytic activity in the selective oxidation of methane to valuable products like formaldehyde. Research indicates that this compound catalysts can achieve high selectivity for these reactions when properly supported on materials like silica .
- Hydrogen Evolution Reaction : Molybdenum oxides are also investigated for their potential in hydrogen production via electrolysis, acting as efficient catalysts that enhance the reaction kinetics .
Energy Storage and Conversion
Molybdenum oxides are utilized in energy storage devices, particularly lithium-ion batteries and supercapacitors.
- Lithium-Ion Batteries : this compound nanostructures demonstrate significant promise in improving the performance of lithium-ion batteries by enhancing charge capacity and cycling stability .
- Supercapacitors : The structural properties of molybdenum oxides contribute to their effectiveness in supercapacitors, providing high capacitance values and excellent cyclic behavior .
Electronics
The electrical properties of molybdenum oxides make them suitable for applications in electronic devices.
- Photodetectors : Molybdenum oxides have been integrated into photodetectors due to their favorable bandgap properties and sensitivity to light .
- Solar Cells : Research has focused on using this compound as a hole transport layer in solar cells, enhancing efficiency through improved charge carrier mobility .
Antimicrobial Applications
Recent studies have highlighted the antimicrobial properties of this compound against various bacteria, including Escherichia coli and Bacillus subtilis. This characteristic opens avenues for its use in coatings and materials designed to prevent microbial growth .
Case Studies
Future Prospects
The future applications of this compound are promising due to ongoing research that aims to enhance its functionalities through nanostructuring and composite formation. Innovations may lead to advancements in areas such as:
- Environmental Monitoring : this compound sensors for detecting toxic gases could play a critical role in industrial safety.
- Biocompatible Materials : The antimicrobial properties could be harnessed for medical devices and surfaces that require sterility.
Wirkmechanismus
The mechanism of action of oxomolybdenum compounds often involves the transfer of oxygen atoms. For example, in oxidation reactions, the molybdenum center facilitates the transfer of oxygen from the compound to the substrate, resulting in the oxidation of the substrate . The molecular targets and pathways involved depend on the specific application and reaction type.
Vergleich Mit ähnlichen Verbindungen
Comparison with Similar Compounds
Molybdenum Oxide vs. Tungsten Oxide (WO₃)
Structural and Functional Similarities :
- Both MoO₃ and WO₃ are layered transition metal oxides with electrochromic properties, used in smart windows and displays .
- They share synthesis methods, such as chemical vapor deposition (CVD) and sputtering .
Key Differences :
This compound vs. Silver Oxide (AgO)
Catalytic Performance in Formaldehyde Production :
Catalyst Type | Conversion Rate | Lifespan (months) | Porosity |
---|---|---|---|
This compound | 99% | 12–18 | 0.7 |
Silver Oxide | 85% | 3–8 | 0.5 |
Advantages of MoO₃ :
- Higher conversion efficiency and durability due to robust oxidative stability.
- Cost-effective compared to silver-based catalysts .
This compound vs. Molybdenum Carbide (Mo₂C)
Functional Contrasts :
Property | MoO₃ | Mo₂C |
---|---|---|
Conductivity | Semiconducting | Metallic |
Applications | Gas sensing, electrochromics | Hydrogen evolution reaction (HER), abrasion-resistant coatings |
Mixed Molybdenum-Tungsten Oxides (Mo-W Oxides)
Synergistic Properties :
Q & A
Basic Research Questions
Q. What are the most reliable methods for synthesizing high-purity molybdenum oxide (MoO₃) nanoparticles for catalytic applications?
- Methodological Answer : Sol-gel synthesis (e.g., using ammonium heptamolybdate precursors) and hydrothermal methods (e.g., autoclave reactions at 150–200°C) are widely used. For phase purity, annealing in controlled atmospheres (e.g., O₂ for MoO₃) is critical. Characterization via XRD (to confirm α-MoO₃ orthorhombic phase) and TEM (for nanoparticle size distribution) is essential. Cross-referencing with Raman spectroscopy ensures structural integrity .
Q. How can researchers characterize the crystallographic phases and oxidation states of this compound compounds?
- Methodological Answer : Combine XRD for crystallographic phase identification (e.g., distinguishing α-MoO₃ from metastable phases) with XPS to determine oxidation states (e.g., Mo⁶⁺ in MoO₃ vs. mixed Mo⁵⁺/Mo⁶⁺ in oxygen-deficient MoO₃₋ₓ). For surface-sensitive analysis, Auger electron spectroscopy (AES) complements bulk techniques. Always calibrate instruments using reference standards (e.g., MoO₃ powder) to minimize systematic errors .
Q. What are the key considerations for designing electrochemical experiments to evaluate this compound’s charge-storage mechanisms?
- Methodological Answer : Use cyclic voltammetry (CV) at varying scan rates (e.g., 5–100 mV/s) to distinguish capacitive (surface-controlled) and diffusion-limited processes. Pair with galvanostatic charge-discharge (GCD) to calculate specific capacitance. Electrolyte choice (e.g., H₂SO₄ for acidic conditions) must align with the oxide’s stability window. Include control experiments with inert electrodes (e.g., Pt) to isolate Faradaic contributions .
Advanced Research Questions
Q. How do oxygen vacancies in this compound influence its electronic structure and catalytic activity for CO₂ reduction?
- Methodological Answer : Oxygen vacancies can be introduced via H₂ reduction or plasma treatment. Use electron paramagnetic resonance (EPR) to quantify vacancy density and DFT calculations to model band structure changes. Catalytic activity correlates with vacancy concentration; validate via in-situ FTIR to track intermediate species (e.g., *COOH) during CO₂ reduction. Compare Tafel slopes to assess rate-limiting steps .
Q. What experimental strategies can resolve contradictions in reported catalytic activities of this compound-based materials for oxidative dehydrogenation (ODH) reactions?
- Methodological Answer : Conduct comparative studies under standardized conditions (e.g., 400–500°C, fixed gas hourly space velocity). Control for surface area differences by normalizing activity to BET surface area. Use isotopic labeling (e.g., ¹⁸O₂) to track oxygen exchange kinetics. Advanced techniques like operando XAS (X-ray absorption spectroscopy) can reveal dynamic structural changes during catalysis .
Q. How can computational modeling (e.g., DFT) be integrated with experimental data to elucidate reaction mechanisms involving this compound surfaces?
- Methodological Answer : Use DFT to model adsorption energies of reactants (e.g., propane on MoO₃(010)) and activation barriers for ODH. Validate with temperature-programmed desorption (TPD) and kinetic isotope effects (KIE). For hybrid studies, correlate simulated density of states (DOS) with experimental UV-Vis spectra to confirm electronic transitions. Ensure computational parameters (e.g., exchange-correlation functionals) match experimental conditions (e.g., temperature, pressure) .
Q. What methodologies are effective in analyzing the stability and degradation pathways of this compound photocatalysts under UV irradiation?
- Methodological Answer : Perform accelerated aging tests with prolonged UV exposure (e.g., 100 h) and monitor phase changes via in-situ XRD. Use XPS depth profiling to identify surface oxidation or reduction. Quantify photocorrosion by ICP-MS analysis of dissolved Mo ions in solution. Compare with control experiments in inert atmospheres to isolate photoinduced vs. thermal effects .
Q. Data Analysis & Contradiction Resolution
Q. How should researchers address discrepancies in reported bandgap values of this compound thin films?
- Methodological Answer : Bandgap variations often arise from differences in film thickness, crystallinity, or measurement techniques. Use Tauc plots from UV-Vis spectra for direct/indirect bandgap estimation. Cross-validate with ellipsometry for thin films. Report deposition parameters (e.g., sputtering power, substrate temperature) to contextualize results. Statistical meta-analysis of literature data can identify outliers .
Q. What statistical approaches are recommended for error analysis in this compound-based sensor response data?
- Methodological Answer : Apply Gaussian error propagation to sensor signals (e.g., resistance changes ± SEM). Use ANOVA to compare response variances across multiple sensors. For non-linear responses (e.g., MoO₃ gas sensors), employ bootstrap resampling to estimate confidence intervals. Report detection limits (LoD) using IUPAC guidelines (3σ/method slope) .
Q. Ethical & Reproducibility Considerations
Q. How can researchers ensure reproducibility when reporting this compound synthesis protocols?
- Methodological Answer : Provide detailed Supplementary Information (SI) with step-by-step procedures, including precursor concentrations, stirring rates, and aging times. Use CIF files for crystallographic data. Adhere to the Beilstein Journal’s guidelines for experimental rigor: report triplicate experiments with standard deviations and include raw data in appendices .
Eigenschaften
Molekularformel |
MoO |
---|---|
Molekulargewicht |
111.95 g/mol |
IUPAC-Name |
oxomolybdenum |
InChI |
InChI=1S/Mo.O |
InChI-Schlüssel |
PQQKPALAQIIWST-UHFFFAOYSA-N |
Kanonische SMILES |
O=[Mo] |
Herkunft des Produkts |
United States |
Synthesis routes and methods I
Procedure details
Synthesis routes and methods II
Procedure details
Synthesis routes and methods III
Procedure details
Haftungsausschluss und Informationen zu In-Vitro-Forschungsprodukten
Bitte beachten Sie, dass alle Artikel und Produktinformationen, die auf BenchChem präsentiert werden, ausschließlich zu Informationszwecken bestimmt sind. Die auf BenchChem zum Kauf angebotenen Produkte sind speziell für In-vitro-Studien konzipiert, die außerhalb lebender Organismen durchgeführt werden. In-vitro-Studien, abgeleitet von dem lateinischen Begriff "in Glas", beinhalten Experimente, die in kontrollierten Laborumgebungen unter Verwendung von Zellen oder Geweben durchgeführt werden. Es ist wichtig zu beachten, dass diese Produkte nicht als Arzneimittel oder Medikamente eingestuft sind und keine Zulassung der FDA für die Vorbeugung, Behandlung oder Heilung von medizinischen Zuständen, Beschwerden oder Krankheiten erhalten haben. Wir müssen betonen, dass jede Form der körperlichen Einführung dieser Produkte in Menschen oder Tiere gesetzlich strikt untersagt ist. Es ist unerlässlich, sich an diese Richtlinien zu halten, um die Einhaltung rechtlicher und ethischer Standards in Forschung und Experiment zu gewährleisten.