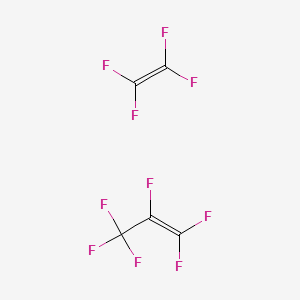
Hfp tfe
Übersicht
Beschreibung
Hfp tfe is a useful research compound. Its molecular formula is C5F10 and its molecular weight is 250.04 g/mol. The purity is usually 95%.
BenchChem offers high-quality this compound suitable for many research applications. Different packaging options are available to accommodate customers' requirements. Please inquire for more information about this compound including the price, delivery time, and more detailed information at info@benchchem.com.
Eigenschaften
CAS-Nummer |
25067-11-2 |
---|---|
Molekularformel |
C5F10 |
Molekulargewicht |
250.04 g/mol |
IUPAC-Name |
1,1,2,3,3,3-hexafluoroprop-1-ene;1,1,2,2-tetrafluoroethene |
InChI |
InChI=1S/C3F6.C2F4/c4-1(2(5)6)3(7,8)9;3-1(4)2(5)6 |
InChI-Schlüssel |
PEVRKKOYEFPFMN-UHFFFAOYSA-N |
Kanonische SMILES |
C(=C(F)F)(C(F)(F)F)F.C(=C(F)F)(F)F |
Verwandte CAS-Nummern |
25067-11-2 |
Herkunft des Produkts |
United States |
Synthesis routes and methods I
Procedure details
Synthesis routes and methods II
Procedure details
Synthesis routes and methods III
Procedure details
Synthesis routes and methods IV
Procedure details
Haftungsausschluss und Informationen zu In-Vitro-Forschungsprodukten
Bitte beachten Sie, dass alle Artikel und Produktinformationen, die auf BenchChem präsentiert werden, ausschließlich zu Informationszwecken bestimmt sind. Die auf BenchChem zum Kauf angebotenen Produkte sind speziell für In-vitro-Studien konzipiert, die außerhalb lebender Organismen durchgeführt werden. In-vitro-Studien, abgeleitet von dem lateinischen Begriff "in Glas", beinhalten Experimente, die in kontrollierten Laborumgebungen unter Verwendung von Zellen oder Geweben durchgeführt werden. Es ist wichtig zu beachten, dass diese Produkte nicht als Arzneimittel oder Medikamente eingestuft sind und keine Zulassung der FDA für die Vorbeugung, Behandlung oder Heilung von medizinischen Zuständen, Beschwerden oder Krankheiten erhalten haben. Wir müssen betonen, dass jede Form der körperlichen Einführung dieser Produkte in Menschen oder Tiere gesetzlich strikt untersagt ist. Es ist unerlässlich, sich an diese Richtlinien zu halten, um die Einhaltung rechtlicher und ethischer Standards in Forschung und Experiment zu gewährleisten.