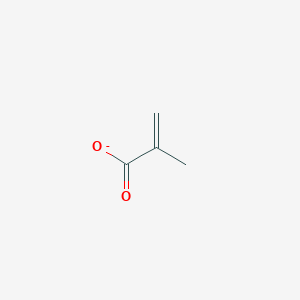
Methacrylate
Übersicht
Beschreibung
Methacrylate refers to esters of methacrylic acid, characterized by the presence of a methyl group (-CH₃) attached to the alpha carbon of the acrylic acid backbone. This structural feature imparts distinct physicochemical properties, such as enhanced rigidity and thermal stability, compared to acrylates . This compound monomers are widely used in polymer chemistry for applications ranging from dental resins (e.g., BisGMA, UDMA, TEGDMA) to coatings and chromatographic monoliths . Their polymerization under UV or thermal initiation enables tailored material properties, including hardness and porosity .
Wissenschaftliche Forschungsanwendungen
Materials Science
- Polymer Production : MMA is primarily used as a monomer for producing various polymers, including acrylic plastics and synthetic rubbers. These polymers are essential in manufacturing products such as paints, adhesives, and coatings .
- Nanocomposites : Recent studies have explored the incorporation of graphene oxide into PMMA to create nanocomposite materials with enhanced mechanical and electrical properties. These materials are being investigated for applications in structural components and electronics .
Healthcare
- Dental Applications : PMMA is extensively used in prosthodontics for fabricating dentures, orthodontic retainers, and artificial teeth due to its favorable properties like low density and aesthetic appeal. Modifications have been made to improve its mechanical strength and thermal properties .
- Bone Cement : MMA is also utilized in orthopedic surgery as bone cement, providing stability and support for implants .
Coatings and Adhesives
- Durable Coatings : MMA-based coatings offer excellent weather resistance and durability, making them suitable for automotive finishes and industrial applications. They protect surfaces from environmental degradation .
- Adhesives : High-performance adhesives formulated with MMA exhibit rapid curing times and strong bonding capabilities across various substrates, including metals and plastics .
Electronics
- Encapsulation : In electronics manufacturing, MMA is used to encapsulate sensitive components, providing insulation against moisture and environmental factors .
Case Study 1: Laser Processing of PMMA
Research conducted on the CO2 continuous laser ablation of PMMA sheets demonstrated that varying laser powers could effectively transform PMMA from solid to liquid states, optimizing processing conditions for industrial applications. The study established a theoretical model that aligns well with experimental results, enhancing the efficiency of laser processing techniques .
Case Study 2: Prosthodontic Advancements
A comprehensive review highlighted the advancements in PMMA formulations for dental applications. Innovations include the incorporation of nanoparticles to enhance the physical properties of PMMA used in dental prosthetics. This research showcases how modifications can lead to better performance in clinical settings .
Comparative Data Table
Application Area | Specific Uses | Benefits |
---|---|---|
Materials Science | Polymer production | Versatile applications in various industries |
Healthcare | Dental prosthetics | Aesthetic appeal; customizable properties |
Bone cement | Provides stability for orthopedic implants | |
Coatings | Automotive coatings | UV stability; weather resistance |
Adhesives | Industrial adhesives | Strong bonding; quick curing |
Electronics | Component encapsulation | Moisture protection; electrical insulation |
Analyse Chemischer Reaktionen
Oxidation Pathways of Methacrylate Derivatives
Density functional theory (DFT) studies reveal two primary oxidation channels for MMA and methylacrylic acid (MAA) with triplet oxygen (O₂) :
Reaction Channel | Activation Energy (kcal/mol) | Dominant Conditions |
---|---|---|
C-H bond oxidation | 5.4 – 7.2 | Room temperature |
C=C bond oxidation | Higher barriers | Elevated temperatures |
The methyl group’s C-H bond exhibits higher reactivity due to hyperconjugative stabilization of transition states. At 25°C, >90% of reactions proceed via C-H oxidation, forming hydroperoxide intermediates . Above 100°C, C=C bond oxidation becomes competitive, generating epoxide derivatives .
Radical Polymerization Mechanisms
MMA undergoes free-radical polymerization initiated by peroxides, with kinetics influenced by:
Key Factors
Table 2: Secondary Reaction Prevalence in MMA Polymerization
Temperature Range | Depropagation | Backbiting | β-Scission |
---|---|---|---|
<80°C | – | – | – |
80–180°C | + | – | – |
>180°C | ++ | – | – |
Radical chain transfer constants (Cₛ) for MMA: 0.08–0.12, indicating moderate transfer activity compared to acrylates (Cₛ=0.15–0.30) .
Metabolic Transformation Pathways
In biological systems, MMA undergoes sequential transformations :
Reactivity with Radical Species
Pulse radiolysis studies quantify MMA’s radical interactions:
-
Hydroxyl radical (- OH) :
(diffusion-controlled)
Primary site: C=C bond addition (87% probability) -
This compound radicals :
Combination barriers:Radical Pair ΔE‡ (kcal/mol) MMA- + MMA 7.2 MMA- + Acrylate 5.4
Chain transfer to polymer (CTP) becomes significant above 10% conversion, with .
These reaction profiles guide material design in dental composites, adhesives, and biomedical hydrogels requiring controlled polymerization kinetics and degradation resistance.
Q & A
Basic Research Questions
Q. What are the standard experimental protocols for synthesizing methacrylate-based polymers, and how can researchers optimize reaction conditions?
- Methodological Answer : Synthesis typically involves free radical polymerization, where parameters like initiator type (e.g., AIBN), monomer-to-initiator ratio, and temperature are critical. For example, poly(methyl this compound) (PMMA) synthesis via miniemulsion solvent-evaporation requires precise control of surfactant concentration and stirring rates to achieve uniform nanocapsules . Optimization involves iterative DOE (Design of Experiments) to assess variables like crosslinker concentration and reaction time, with characterization via GPC for molecular weight distribution .
Q. How should researchers design experiments to characterize this compound monomer purity and polymer structural integrity?
- Methodological Answer : Use tandem analytical techniques:
- Purity : GC-MS for volatile impurities, HPLC for non-volatile residues .
- Structural Analysis : FTIR to confirm this compound C=O (1720 cm⁻¹) and C-O-C (1150 cm⁻¹) peaks; NMR for tacticity (syndiotactic vs. isotactic PMMA) .
- Thermal Stability : TGA to assess decomposition thresholds (e.g., PMMA degrades at ~300°C) .
Q. What are the best practices for conducting a literature review on this compound applications in biomaterials?
- Methodological Answer :
- Database Selection : Prioritize Scopus and Web of Science for comprehensive coverage, filtering by keywords like "this compound hydrogel" AND "biocompatibility" .
- Inclusion Criteria : Focus on peer-reviewed articles (2015–2025) with in vitro/vivo toxicity data. Exclude patents and industrial reports .
- Gap Analysis : Use tools like VOSviewer to map research trends, identifying understudied areas (e.g., long-term degradation in physiological environments) .
Advanced Research Questions
Q. How can researchers resolve contradictions in reported this compound crosslinking efficiencies across studies?
- Methodological Answer :
- Systematic Review : Follow COSMOS-E guidelines to aggregate data from cohort studies, assessing variables like UV initiator concentration (e.g., 0.1% vs. 1% Irgacure 2959) .
- Statistical Re-evaluation : Apply meta-analysis to reconcile discrepancies, using random-effects models to account for heterogeneity in experimental conditions (e.g., solvent polarity, curing time) .
- Experimental Validation : Reproduce conflicting studies under controlled conditions, isolating variables like oxygen inhibition .
Q. What advanced methodologies enable real-time monitoring of this compound polymerization kinetics?
- Methodological Answer :
- In Situ Techniques : Use Raman spectroscopy to track conversion rates via C=C bond disappearance (1630 cm⁻¹) .
- Photocalorimetry : Measure heat flow during UV-initiated polymerization to calculate kinetic parameters (e.g., activation energy) .
- Machine Learning : Train models on historical kinetic data to predict gelation points under novel conditions (e.g., high humidity) .
Q. How can researchers assess the environmental impact of this compound degradation byproducts?
- Methodological Answer :
- Degradation Studies : Accelerate aging via UV/heat exposure, analyzing leachates via LC-QTOF-MS to identify toxic fragments (e.g., methacrylic acid) .
- Ecotoxicity Assays : Use Daphnia magna or algal models to quantify LC50 values for degradation products .
- Life Cycle Analysis (LCA) : Model cradle-to-grave impacts, emphasizing energy-intensive steps like monomer purification .
Q. What strategies improve reproducibility in this compound-based 3D printing formulations?
- Methodological Answer :
- Standardization : Adopt ASTM F42 guidelines for resin preparation, documenting viscosity (via rheometry) and photoinitiator half-life .
- Interlab Comparisons : Share datasets via platforms like Zenodo, ensuring transparency in post-curing protocols (e.g., 405 nm wavelength, 10 mW/cm² intensity) .
- Error Tracking : Use failure mode analysis (FMA) to catalog defects (e.g., layer delamination) and link to process variables .
Q. Methodological Guidance Tables
Research Stage | Key Tools/Methods | References |
---|---|---|
Synthesis Optimization | DOE, GPC, Miniemulsion solvent-evaporation | |
Contradiction Resolution | Meta-analysis, COSMOS-E guidelines | |
Environmental Impact | LC-QTOF-MS, Ecotoxicity assays |
Common Pitfalls | Solutions |
---|---|
Inconsistent crosslinker dispersion | Pre-mix monomers via sonication (40 kHz, 30 min) |
Overlooking oxygen inhibition | Use inert gas purging (N₂/Ar) during curing |
Q. Ethical & Reporting Standards
Vergleich Mit ähnlichen Verbindungen
Comparison with Similar Compounds
Methacrylate vs. Acrylate
The primary distinction lies in the presence of the alpha-methyl group in methacrylates, which acrylates lack. This structural difference leads to:
- Enhanced Rigidity : this compound-based polymers exhibit greater hardness due to restricted chain mobility. For example, epoxy-methacrylate formulations show superior hardness compared to acrylate counterparts .
- Higher Glass Transition Temperature (Tg) : Methacrylates like methyl this compound (MMA) have higher Tg values (e.g., ~105°C for PMMA) than polyacrylates (e.g., ~40°C for polyethyl acrylate) due to steric hindrance .
- Slower Polymerization Kinetics : The methyl group reduces the propagation rate coefficient ($kp$) during radical polymerization. For instance, $kp$ for MMA is ~2.5 × 10³ L·mol⁻¹·s⁻¹, whereas acrylates like butyl acrylate (BA) exhibit $k_p$ ~3.8 × 10⁴ L·mol⁻¹·s⁻¹ .
Table 1: Key Properties of this compound vs. Acrylate Polymers
Property | This compound (e.g., PMMA) | Acrylate (e.g., PBA) |
---|---|---|
Tg (°C) | ~105 | ~40 |
Hardness (Shore D) | 85–90 | 50–60 |
$k_p$ (L·mol⁻¹·s⁻¹) | 2.5 × 10³ | 3.8 × 10⁴ |
Volatility | Low | High |
Variations Within this compound Monomers
Methacrylates differ based on their ester substituents, influencing properties and applications:
Methyl this compound (MMA) vs. Butyl this compound (BMA)
- Thermal Properties : BMA’s longer alkyl chain reduces Tg (e.g., ~20°C for PBMA vs. ~105°C for PMMA) but improves flexibility .
- Applications : PMMA is used in rigid optics and automotive components, while PBMA is employed in flexible coatings .
Functional Methacrylates (e.g., HEMA, EDMA)
- Hydroxyethyl this compound (HEMA) : Contains a hydroxyl group, enhancing hydrophilicity but increasing cytotoxicity in dental resins .
- Ethylene Dithis compound (EDMA): A crosslinker that creates rigid networks in chromatographic monoliths due to its bifunctional structure .
Table 2: Comparison of this compound Derivatives
This compound vs. Methacrylamide
Methacrylamide derivatives, such as those used in cartilage matrix biomaterials, exhibit distinct behavior:
- Stability : Methacrylamides resist hydrolysis better than methacrylates, enhancing durability in aqueous environments .
- Quantification : Methacrylamide content is indirectly measured due to overlapping NMR signals with this compound .
Bio-Based Methacrylates (e.g., Isosorbide this compound)
Isosorbide methacrylates, derived from renewable resources, offer:
Eigenschaften
CAS-Nummer |
18358-13-9 |
---|---|
Molekularformel |
C4H5O2- |
Molekulargewicht |
85.08 g/mol |
IUPAC-Name |
2-methylprop-2-enoate |
InChI |
InChI=1S/C4H6O2/c1-3(2)4(5)6/h1H2,2H3,(H,5,6)/p-1 |
InChI-Schlüssel |
CERQOIWHTDAKMF-UHFFFAOYSA-M |
SMILES |
CC(=C)C(=O)[O-] |
Kanonische SMILES |
CC(=C)C(=O)[O-] |
Synonyme |
Methacrylic acidanion |
Herkunft des Produkts |
United States |
Synthesis routes and methods I
Procedure details
Synthesis routes and methods II
Procedure details
Synthesis routes and methods III
Procedure details
Synthesis routes and methods IV
Procedure details
Retrosynthesis Analysis
AI-Powered Synthesis Planning: Our tool employs the Template_relevance Pistachio, Template_relevance Bkms_metabolic, Template_relevance Pistachio_ringbreaker, Template_relevance Reaxys, Template_relevance Reaxys_biocatalysis model, leveraging a vast database of chemical reactions to predict feasible synthetic routes.
One-Step Synthesis Focus: Specifically designed for one-step synthesis, it provides concise and direct routes for your target compounds, streamlining the synthesis process.
Accurate Predictions: Utilizing the extensive PISTACHIO, BKMS_METABOLIC, PISTACHIO_RINGBREAKER, REAXYS, REAXYS_BIOCATALYSIS database, our tool offers high-accuracy predictions, reflecting the latest in chemical research and data.
Strategy Settings
Precursor scoring | Relevance Heuristic |
---|---|
Min. plausibility | 0.01 |
Model | Template_relevance |
Template Set | Pistachio/Bkms_metabolic/Pistachio_ringbreaker/Reaxys/Reaxys_biocatalysis |
Top-N result to add to graph | 6 |
Feasible Synthetic Routes
Haftungsausschluss und Informationen zu In-Vitro-Forschungsprodukten
Bitte beachten Sie, dass alle Artikel und Produktinformationen, die auf BenchChem präsentiert werden, ausschließlich zu Informationszwecken bestimmt sind. Die auf BenchChem zum Kauf angebotenen Produkte sind speziell für In-vitro-Studien konzipiert, die außerhalb lebender Organismen durchgeführt werden. In-vitro-Studien, abgeleitet von dem lateinischen Begriff "in Glas", beinhalten Experimente, die in kontrollierten Laborumgebungen unter Verwendung von Zellen oder Geweben durchgeführt werden. Es ist wichtig zu beachten, dass diese Produkte nicht als Arzneimittel oder Medikamente eingestuft sind und keine Zulassung der FDA für die Vorbeugung, Behandlung oder Heilung von medizinischen Zuständen, Beschwerden oder Krankheiten erhalten haben. Wir müssen betonen, dass jede Form der körperlichen Einführung dieser Produkte in Menschen oder Tiere gesetzlich strikt untersagt ist. Es ist unerlässlich, sich an diese Richtlinien zu halten, um die Einhaltung rechtlicher und ethischer Standards in Forschung und Experiment zu gewährleisten.