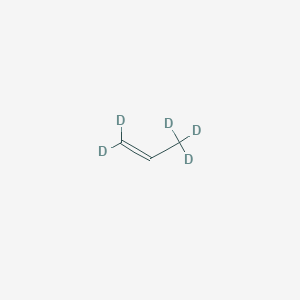
1,1,3,3,3-Pentadeuterioprop-1-ene
Übersicht
Beschreibung
1,1,3,3,3-Pentadeuterioprop-1-ene: is a deuterated analog of propene, where five hydrogen atoms are replaced by deuterium. Deuterium is a stable isotope of hydrogen, which makes this compound particularly useful in various scientific research applications, especially in the field of spectroscopy and reaction mechanism studies.
Vorbereitungsmethoden
Synthetic Routes and Reaction Conditions: 1,1,3,3,3-Pentadeuterioprop-1-ene can be synthesized through the deuteration of propene. One common method involves the catalytic exchange of hydrogen atoms with deuterium using a deuterium gas atmosphere in the presence of a suitable catalyst such as palladium on carbon (Pd/C).
Industrial Production Methods: Industrial production of deuterated compounds often involves the use of heavy water (D2O) as a source of deuterium. The process typically includes the catalytic deuteration of hydrocarbons under controlled conditions to achieve high levels of deuterium incorporation.
Analyse Chemischer Reaktionen
Types of Reactions: 1,1,3,3,3-Pentadeuterioprop-1-ene undergoes similar chemical reactions as its non-deuterated counterpart, propene. These reactions include:
Oxidation: The compound can be oxidized to form deuterated alcohols, aldehydes, or carboxylic acids.
Reduction: It can be reduced to form deuterated alkanes.
Substitution: The compound can undergo substitution reactions where deuterium atoms are replaced by other functional groups.
Common Reagents and Conditions:
Oxidation: Common oxidizing agents include potassium permanganate (KMnO4) and ozone (O3).
Reduction: Catalytic hydrogenation using deuterium gas (D2) and a metal catalyst such as palladium (Pd) or platinum (Pt).
Substitution: Halogenation reactions using halogens like chlorine (Cl2) or bromine (Br2).
Major Products Formed:
Oxidation: Deuterated alcohols, aldehydes, and carboxylic acids.
Reduction: Deuterated alkanes.
Substitution: Deuterated halides.
Wissenschaftliche Forschungsanwendungen
1,1,3,3,3-Pentadeuterioprop-1-ene is widely used in scientific research due to its unique properties:
Chemistry: It is used in kinetic isotope effect studies to understand reaction mechanisms.
Biology: Deuterated compounds are used in metabolic studies to trace biochemical pathways.
Medicine: It is used in the development of deuterated drugs, which often have improved metabolic stability and reduced toxicity.
Industry: Deuterated compounds are used in the production of specialty chemicals and materials with enhanced properties.
Wirkmechanismus
The mechanism by which 1,1,3,3,3-Pentadeuterioprop-1-ene exerts its effects is primarily through the kinetic isotope effect. The presence of deuterium atoms, which are heavier than hydrogen atoms, results in a lower vibrational frequency and bond dissociation energy. This leads to slower reaction rates for processes involving C-D bonds compared to C-H bonds, allowing researchers to study reaction mechanisms in greater detail.
Vergleich Mit ähnlichen Verbindungen
- 1,1,1,3,3-Pentadeuterio-2-(trideuteriomethoxy)prop-1-ene
- 1,1,1,3,3-Pentafluoropropane
- cis-1,3,3,3-Tetrafluoroprop-1-ene
Comparison: 1,1,3,3,3-Pentadeuterioprop-1-ene is unique due to its specific deuterium substitution pattern, which makes it particularly useful for studying the kinetic isotope effect. Other similar compounds, such as 1,1,1,3,3-Pentafluoropropane and cis-1,3,3,3-Tetrafluoroprop-1-ene, have different substitution patterns and are used in different applications, such as refrigerants and solvents .
Eigenschaften
IUPAC Name |
1,1,3,3,3-pentadeuterioprop-1-ene | |
---|---|---|
Source | PubChem | |
URL | https://pubchem.ncbi.nlm.nih.gov | |
Description | Data deposited in or computed by PubChem | |
InChI |
InChI=1S/C3H6/c1-3-2/h3H,1H2,2H3/i1D2,2D3 | |
Source | PubChem | |
URL | https://pubchem.ncbi.nlm.nih.gov | |
Description | Data deposited in or computed by PubChem | |
InChI Key |
QQONPFPTGQHPMA-KPAILUHGSA-N | |
Source | PubChem | |
URL | https://pubchem.ncbi.nlm.nih.gov | |
Description | Data deposited in or computed by PubChem | |
Canonical SMILES |
CC=C | |
Source | PubChem | |
URL | https://pubchem.ncbi.nlm.nih.gov | |
Description | Data deposited in or computed by PubChem | |
Isomeric SMILES |
[2H]C(=CC([2H])([2H])[2H])[2H] | |
Source | PubChem | |
URL | https://pubchem.ncbi.nlm.nih.gov | |
Description | Data deposited in or computed by PubChem | |
Molecular Formula |
C3H6 | |
Source | PubChem | |
URL | https://pubchem.ncbi.nlm.nih.gov | |
Description | Data deposited in or computed by PubChem | |
Molecular Weight |
47.11 g/mol | |
Source | PubChem | |
URL | https://pubchem.ncbi.nlm.nih.gov | |
Description | Data deposited in or computed by PubChem | |
Synthesis routes and methods I
Procedure details
Synthesis routes and methods II
Procedure details
Synthesis routes and methods III
Procedure details
Synthesis routes and methods IV
Procedure details
Synthesis routes and methods V
Procedure details
Haftungsausschluss und Informationen zu In-Vitro-Forschungsprodukten
Bitte beachten Sie, dass alle Artikel und Produktinformationen, die auf BenchChem präsentiert werden, ausschließlich zu Informationszwecken bestimmt sind. Die auf BenchChem zum Kauf angebotenen Produkte sind speziell für In-vitro-Studien konzipiert, die außerhalb lebender Organismen durchgeführt werden. In-vitro-Studien, abgeleitet von dem lateinischen Begriff "in Glas", beinhalten Experimente, die in kontrollierten Laborumgebungen unter Verwendung von Zellen oder Geweben durchgeführt werden. Es ist wichtig zu beachten, dass diese Produkte nicht als Arzneimittel oder Medikamente eingestuft sind und keine Zulassung der FDA für die Vorbeugung, Behandlung oder Heilung von medizinischen Zuständen, Beschwerden oder Krankheiten erhalten haben. Wir müssen betonen, dass jede Form der körperlichen Einführung dieser Produkte in Menschen oder Tiere gesetzlich strikt untersagt ist. Es ist unerlässlich, sich an diese Richtlinien zu halten, um die Einhaltung rechtlicher und ethischer Standards in Forschung und Experiment zu gewährleisten.